- お役立ち記事
- A new approach to HAZOP analysis and safety design that equipment maintenance departments should know about
A new approach to HAZOP analysis and safety design that equipment maintenance departments should know about
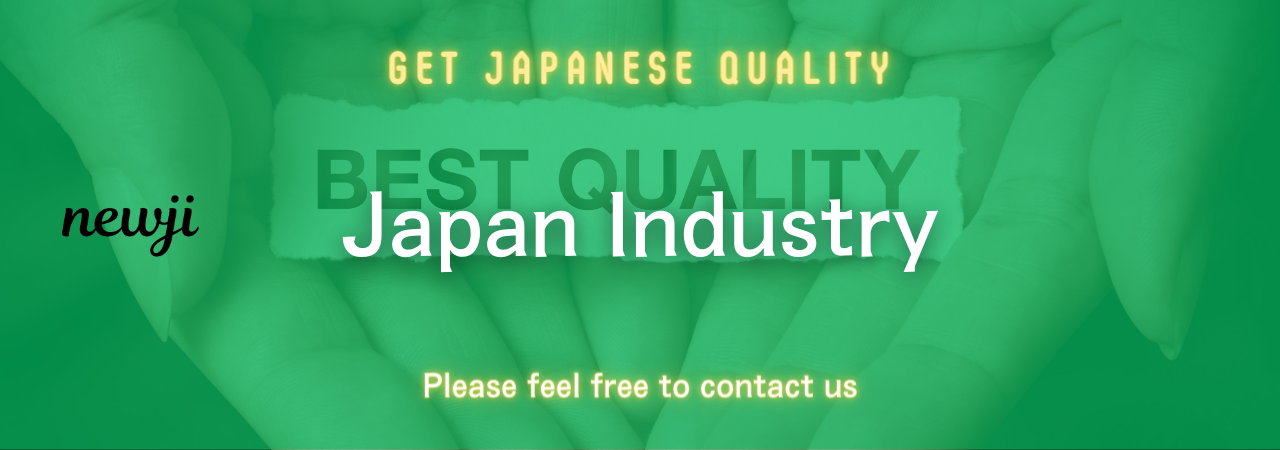
目次
Understanding HAZOP: A Fundamental Overview
HAZOP, short for Hazard and Operability Study, is a systematic and structured method that identifies potential hazards and operability issues in process systems.
Originating from the chemical industry, it has become a standard tool in various sectors for managing safety and operational risks.
For equipment maintenance departments, comprehending HAZOP is crucial to ensure that machinery and processes are not only efficient but also safe.
A HAZOP analysis involves a multidisciplinary team reviewing a process design or existing processes.
Through brainstorming sessions, team members explore possible deviations from normal operations that could lead to hazardous events.
Such deviations might result from incorrect equipment design, human error, or operational inefficiencies.
By identifying these deviations, teams can devise strategies to mitigate risks.
The Importance of HAZOP in Safety Design
Safety design plays a pivotal role in maintaining operational integrity and protecting both people and assets.
Incorporating HAZOP in safety design adds an additional layer of scrutiny, identifying potential fault lines that might otherwise go unnoticed.
A robust safety design anticipates and mitigates risks, regardless of whether they stem from mechanical failure, environmental conditions, or human factors.
For equipment maintenance departments, this means having a robust protocol for regular inspections and proactive maintenance.
A HAZOP analysis can pinpoint critical safety features that require constant monitoring and upkeep.
Addressing these findings can help prevent accidents, reduce downtime, and ensure compliance with industry regulations.
The New Approach: Integrating Technology with HAZOP
Technological advances have revolutionized how industries conduct HAZOP analyses.
Traditional methods relied heavily on manual checks and team brainstorming sessions.
Today, digital tools and software can automate parts of the process, enhancing accuracy and efficiency.
For instance, simulation software can model potential hazards based on historical data.
These simulations provide visual and analytical insights into how different scenarios might unfold, offering a dynamic tool for HAZOP teams.
By integrating real-time data and predictive analytics, maintenance departments can anticipate failures before they occur and schedule necessary maintenance more effectively.
Furthermore, technology paves the way for remote collaboration among team members across different locations.
This accessibility ensures that the necessary expertise is always at hand, facilitating timely and informed decision-making.
Key Benefits of Using Technology in HAZOP
1. **Enhanced Precision:** Digital tools allow for more precise data collection and analysis than manual methods, reducing the risk of human error in the HAZOP process.
2. **Time-Efficiency:** Automation reduces the time required to gather information and assess potential risks, enabling quicker implementation of safety measures.
3. **Improved Communication:** Remote collaboration tools make it easier for team members from different departments or sites to work together, promoting a more cohesive safety strategy.
4. **Predictive Maintenance:** Leveraging data analytics to predict equipment issues aids in scheduling maintenance activities proactively, minimizing unexpected breakdowns.
The Role of Equipment Maintenance Departments
Equipment maintenance departments serve a crucial function in the ongoing success of HAZOP activities.
Their frontline expertise provides vital input into the HAZOP process, ensuring that designs and operational practices are based on real-world conditions and limitations.
To maximize the benefits of HAZOP, maintenance teams need to be thoroughly familiar with the systems and equipment they service.
They must maintain meticulous records of past maintenance activities, issues encountered, and any design or operational changes made to equipment.
These records are instrumental in identifying recurring problems or trends that could lead to potential hazards.
Regular training and updates for maintenance personnel on the latest safety standards and technologies are also essential.
This knowledge ensures that they can actively contribute to HAZOP analyses and implement suggested safety improvements effectively.
Best Practices for Maintenance Departments in HAZOP
1. **Maintain Detailed Logs:** Keep comprehensive records of all maintenance activities and equipment histories to provide valuable data for HAZOP analysis.
2. **Engage in Continuous Training:** Ensure that staff are regularly trained on new safety technologies and industry standards to stay current with best practices.
3. **Foster Collaboration:** Work closely with other departments to share insights and observations that could enhance overall safety and equipment performance.
4. **Implement Feedback Loops:** Incorporate feedback from HAZOP findings into maintenance schedules and procedures to continually improve safety mechanisms.
Combining HAZOP with Other Safety Techniques
While HAZOP is a powerful tool, it is not the only safety analysis technique available.
Combining it with other methods like Failure Mode and Effects Analysis (FMEA) or Layer of Protection Analysis (LOPA) can provide a more detailed overview of potential risks.
These complementary methodologies offer different perspectives on safety design, bolstering the robustness of overall risk management strategies.
For equipment maintenance departments, integrating various safety techniques can lead to a more comprehensive understanding of how equipment functions under different scenarios and what measures can enhance safety.
Maintenance teams should be open to adopting new tools and techniques to gain a more holistic view of their systems.
This proactive approach can lead to safer environments, more efficient operations, and greater confidence in the integrity of safety designs.
Conclusion
The evolving approach to HAZOP analysis and safety design presents numerous opportunities for equipment maintenance departments.
Through integrating new technologies, embracing collaboration, and adopting best practices, maintenance teams can play a critical role in enhancing safety and operational integrity.
Understanding and implementing HAZOP is not merely a regulatory requirement—it’s an essential part of safeguarding personnel and maintaining efficient production processes.
By committing to continuous improvement and adopting a proactive stance toward potential hazards, maintenance departments can make significant contributions to both workplace safety and operational excellence.
資料ダウンロード
QCD調達購買管理クラウド「newji」は、調達購買部門で必要なQCD管理全てを備えた、現場特化型兼クラウド型の今世紀最高の購買管理システムとなります。
ユーザー登録
調達購買業務の効率化だけでなく、システムを導入することで、コスト削減や製品・資材のステータス可視化のほか、属人化していた購買情報の共有化による内部不正防止や統制にも役立ちます。
NEWJI DX
製造業に特化したデジタルトランスフォーメーション(DX)の実現を目指す請負開発型のコンサルティングサービスです。AI、iPaaS、および先端の技術を駆使して、製造プロセスの効率化、業務効率化、チームワーク強化、コスト削減、品質向上を実現します。このサービスは、製造業の課題を深く理解し、それに対する最適なデジタルソリューションを提供することで、企業が持続的な成長とイノベーションを達成できるようサポートします。
オンライン講座
製造業、主に購買・調達部門にお勤めの方々に向けた情報を配信しております。
新任の方やベテランの方、管理職を対象とした幅広いコンテンツをご用意しております。
お問い合わせ
コストダウンが利益に直結する術だと理解していても、なかなか前に進めることができない状況。そんな時は、newjiのコストダウン自動化機能で大きく利益貢献しよう!
(Β版非公開)