- お役立ち記事
- How to create and operate a QC process chart that new employees in the quality control department should know
How to create and operate a QC process chart that new employees in the quality control department should know
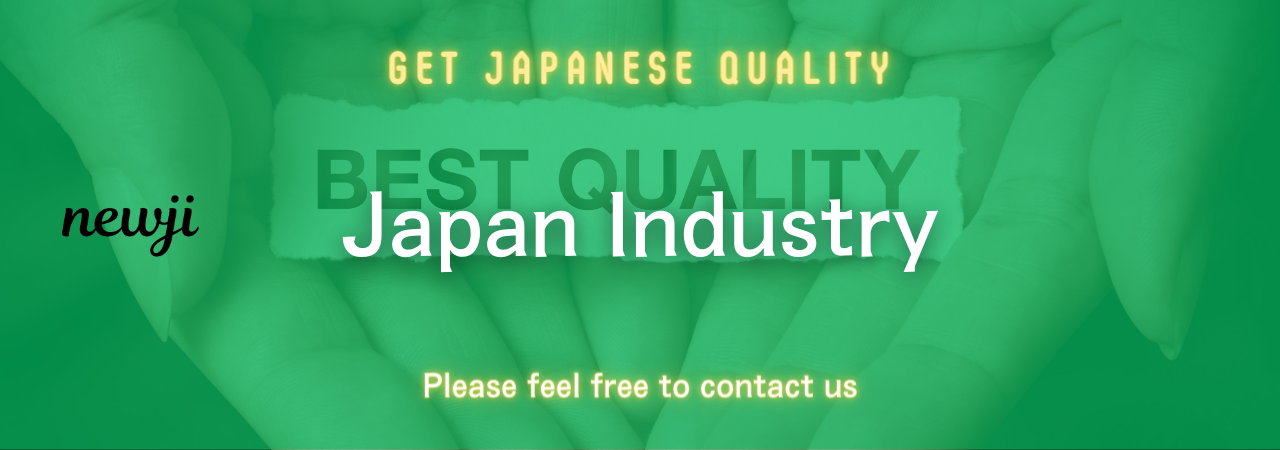
目次
Understanding the QC Process Chart
A QC process chart is an invaluable tool in the quality control department as it visually represents the workflow and ensures consistently high standards in production or service delivery.
New employees, especially in the quality control department, should familiarize themselves with it to understand the sequence of operations and checks that lead to quality assurance.
The QC process chart not only helps in maintaining efficiency but also aids in spotting issues that might otherwise go unnoticed during production phases.
By mapping out each stage of the quality control process, individuals can quickly identify potential bottlenecks and areas for improvement.
The Basics of QC Process Charts
Before diving into creating a QC process chart, it’s crucial to understand its basic components.
A QC process chart typically includes several key elements like process steps, decision points, inputs, outputs, and checkpoints.
These elements are depicted through standard symbols such as rectangles for process steps, diamonds for decision points, and arrows to indicate the flow of the process.
New employees should get acquainted with these symbols to effectively read and interpret QC process charts.
Steps to Create a QC Process Chart
Creating a QC process chart is a systematic and straightforward task if approached methodically.
Here are the steps to guide new employees through the process:
1. Identify the Process to be Charted
The first step involves clearly defining the process that needs to be documented on the QC chart.
Whether it’s the manufacturing of a product or providing a service, every detailed step should be identified to ensure nothing important is left out.
2. Gather Necessary Information
Consult with your team or review existing documentation to gather all pertinent information about the steps involved in your quality control process.
Understanding who is responsible for each task and the necessary inputs and outputs will be crucial in this phase.
3. Determine Key Quality Control Points
Determine the critical checkpoints within the process where quality must be assessed.
This ensures that any defects or issues are caught at the earliest possible stage, reducing rework or failures later on.
4. Use a Flowchart Tool
Using a flowchart tool or software can be immensely helpful for creating your QC process chart.
There’s a variety of software available ranging from basic programs like Microsoft Office to more specialized tools like Lucidchart or Visio that offer intuitive interfaces for designing complex flowcharts.
5. Design the Chart
Start placing your process steps, decision points, and checkpoints in chronological order on the chart, using the standard flowchart symbols.
Be sure to draw lines and arrows to connect these elements, showing the direction of the process flow.
6. Validate with Team Members
Before finalizing, share the draft QC process chart with your team members.
They can provide insights or spot any oversight, ensuring the chart accurately represents the actual process.
7. Implement and Update
Once validated, implement the QC process chart within your operations.
Keep track of any changes in the process, as the chart will need to be updated regularly to remain relevant and effective.
Operating the QC Process Chart
After creating a QC process chart, it’s equally essential to operate it effectively.
Here’s how new employees can manage it:
Ensuring Comprehensive Training
Employees should receive comprehensive training on how to effectively utilize the QC process chart as part of their standard operating procedures.
This training will ensure that everyone understands their role, responsibilities, and the expected quality standards.
Regular Monitoring and Evaluation
Routine monitoring and evaluation using the QC process chart help in identifying areas that need improvement.
Encourage employees to provide feedback and suggestions based on their experience during the quality control process.
Documentation and Reporting
Ensure accurate documentation and reporting of all QC activities as outlined in the process chart.
This helps in maintaining transparency and can be crucial for troubleshooting any quality issues that arise.
Continuous Improvement
The QC process chart should be used not only as a guide but also as a tool for continuous improvement.
Encourage innovation and improvements in the quality control processes by routinely revisiting and revising the QC charts to enhance efficiency and effectiveness.
Conclusion
A well-crafted QC process chart serves as the backbone of any quality control department.
For new employees, understanding and effectively using these charts will streamline processes and ensure a high standard of quality is maintained.
By following the steps for creation and operation of a QC process chart, you will not only enhance your department’s efficiency but also contribute meaningfully towards organizational excellence.
Regular updates and training are essential to adapt the QC process to any changes and to keep quality at the forefront of your operations.
資料ダウンロード
QCD調達購買管理クラウド「newji」は、調達購買部門で必要なQCD管理全てを備えた、現場特化型兼クラウド型の今世紀最高の購買管理システムとなります。
ユーザー登録
調達購買業務の効率化だけでなく、システムを導入することで、コスト削減や製品・資材のステータス可視化のほか、属人化していた購買情報の共有化による内部不正防止や統制にも役立ちます。
NEWJI DX
製造業に特化したデジタルトランスフォーメーション(DX)の実現を目指す請負開発型のコンサルティングサービスです。AI、iPaaS、および先端の技術を駆使して、製造プロセスの効率化、業務効率化、チームワーク強化、コスト削減、品質向上を実現します。このサービスは、製造業の課題を深く理解し、それに対する最適なデジタルソリューションを提供することで、企業が持続的な成長とイノベーションを達成できるようサポートします。
オンライン講座
製造業、主に購買・調達部門にお勤めの方々に向けた情報を配信しております。
新任の方やベテランの方、管理職を対象とした幅広いコンテンツをご用意しております。
お問い合わせ
コストダウンが利益に直結する術だと理解していても、なかなか前に進めることができない状況。そんな時は、newjiのコストダウン自動化機能で大きく利益貢献しよう!
(Β版非公開)