- お役立ち記事
- Basics of TPM activities and equipment maintenance approaches that new leaders of equipment technology departments should learn
Basics of TPM activities and equipment maintenance approaches that new leaders of equipment technology departments should learn
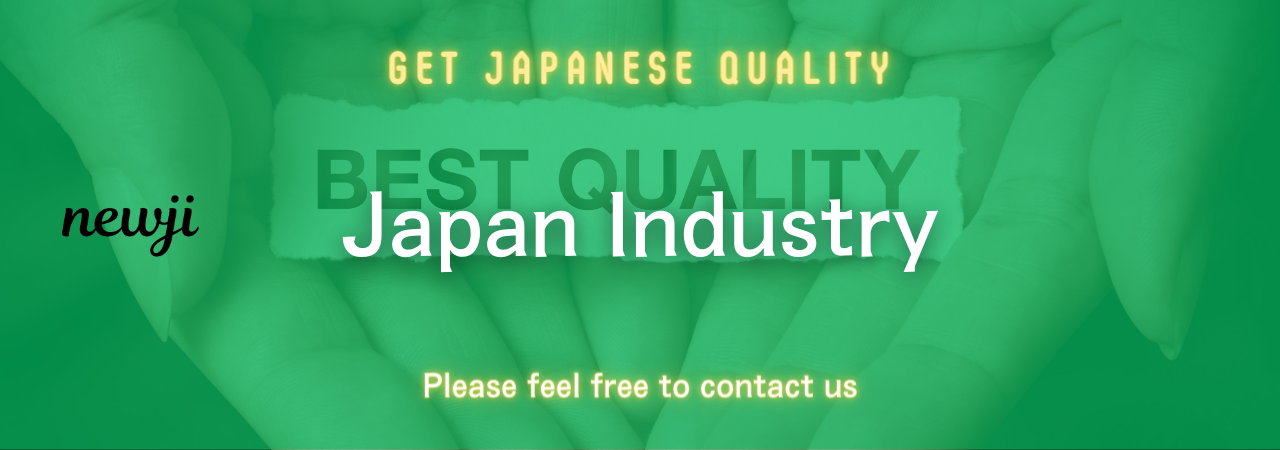
目次
Understanding TPM Activities
Total Productive Maintenance, commonly known as TPM, is a comprehensive approach designed to improve productivity and equipment efficiency in manufacturing sectors.
TPM focuses on proactively maintaining equipment to reduce unexpected breakdowns and promote a more efficient work environment.
The core idea behind TPM is to engage all employees, from operators to managers, in maintenance activities.
This inclusive approach ensures that everyone contributes to maintaining equipment and avoids placing the entire responsibility on maintenance personnel alone.
TPM activities are built around eight pillars, each aiming to achieve optimal equipment functionality and efficiency.
By addressing these key areas, organizations can significantly reduce downtime and improve productivity.
The Eight Pillars of TPM
1. **Autonomous Maintenance**: Operators are trained to perform routine maintenance tasks, such as cleaning, lubrication, and inspections.
This empowers operators to identify potential issues early and promotes ownership of the equipment.
2. **Planned Maintenance**: Scheduling preventive maintenance activities in advance to avoid unexpected breakdowns.
It involves regular inspections and servicing, ensuring machines operate smoothly without interruptions.
3. **Quality Maintenance**: Emphasizes producing defect-free products by identifying and addressing equipment-related quality issues.
This pillar works closely with quality control departments to ensure consistency in production quality.
4. **Focused Improvement**: Uses small, targeted projects to improve specific areas of productivity and equipment effectiveness.
Teams work collaboratively to identify areas where improvements can be made, implementing solutions that enhance overall operations.
5. **Early Equipment Management**: Involves designing systems with maintenance in mind from the outset.
By incorporating maintenance considerations in the design phase, companies can ensure easier upkeep and minimize long-term costs.
6. **Training and Education**: Aims to develop a highly skilled workforce by providing specialized training and knowledge development opportunities.
Educating employees on maintenance best practices ensures they are equipped to handle any challenges that arise.
7. **Safety, Health, and Environment**: Prioritizes creating a safe working environment and reducing environmental impact.
This pillar ensures that all maintenance activities comply with safety and environmental regulations.
8. **Administrative and Office TPM**: Extends TPM principles to administrative functions, focusing on improving efficiency and reducing waste in office environments.
This holistic approach ensures that every aspect of the organization is optimized.
The Importance of Equipment Maintenance
Equipment maintenance is crucial for sustaining productivity and preventing costly downtime in any organization.
Neglecting maintenance can lead to unexpected breakdowns, resulting in lost production time and increased operational costs.
By implementing effective maintenance strategies, companies can ensure their equipment operates at peak efficiency.
Several key benefits highlight the importance of proper equipment maintenance:
Increased Equipment Lifespan
Regular maintenance ensures that machines and equipment continue to function optimally for longer periods, thus extending their lifespan.
By addressing wear and tear issues before they escalate, companies can avoid premature equipment replacement, leading to substantial cost savings.
Enhanced Safety
Well-maintained equipment is inherently safer to operate.
Routine maintenance helps identify potential safety hazards, reducing the risk of accidents and injuries.
Prioritizing safety in maintenance activities not only protects employees but also minimizes liability for the organization.
Cost Efficiency
Proactive maintenance reduces the likelihood of unexpected breakdowns and costly repairs.
By investing in regular upkeep, companies can prevent larger issues from developing, ultimately reducing overall maintenance expenses.
Improved Productivity
Efficiently functioning equipment contributes to smoother operations and higher production rates.
Regular maintenance minimizes downtimes, allowing manufacturing processes to proceed without interruption, thereby maximizing productivity.
Approaches to Equipment Maintenance
Adopting the right maintenance approach is essential for ensuring equipment reliability and efficiency.
Different maintenance strategies can be used depending on the organization’s needs and the nature of the equipment.
Preventive Maintenance
Preventive maintenance involves regularly scheduled inspections and servicing to identify potential issues early.
By conducting maintenance before problems occur, companies can avoid unexpected breakdowns and keep equipment running smoothly.
This approach is particularly effective for machinery with known wear-and-tear patterns.
Predictive Maintenance
Predictive maintenance uses data and technology to predict when equipment might fail or require maintenance.
By analyzing data gathered from sensors and monitoring systems, companies can schedule maintenance activities based on actual equipment conditions.
This data-driven approach allows for optimized maintenance schedules and minimizes unnecessary interventions.
Condition-Based Maintenance
Condition-based maintenance focuses on monitoring the actual condition of equipment and performing maintenance only when necessary.
Regular assessments help identify any deviations from standard operating conditions, prompting timely maintenance.
This strategy helps allocate resources more efficiently by prioritizing equipment in need of immediate attention.
Corrective Maintenance
Corrective maintenance, also known as reactive maintenance, occurs after equipment fails or malfunctions.
While it’s important to address issues as they arise, relying solely on corrective maintenance can be costly and result in significant downtime.
It’s generally used as a supplementary approach alongside preventive or predictive maintenance strategies.
Implementing Effective TPM and Maintenance Practices
For new leaders in equipment technology departments, implementing TPM activities and effective maintenance approaches can be daunting.
However, following a systematic approach can ease the process and ensure successful implementation.
Engage and Educate Employees
Start by involving employees at all levels in TPM activities.
Conduct training sessions to educate them about the importance of maintenance and how they can contribute to improving equipment reliability.
Encourage open communication and feedback to foster a collaborative maintenance culture.
Set Clear Objectives
Define clear objectives for TPM and maintenance initiatives.
Establish measurable goals, such as reducing downtime or extending equipment lifespans, and monitor progress regularly.
Having well-defined objectives helps align efforts and ensures that everyone works towards common goals.
Use Data-Driven Insights
Leverage data and technology to enhance maintenance practices.
Implement predictive and condition-based maintenance strategies by utilizing data analytics and monitoring systems.
Rely on these insights to make informed decisions regarding maintenance schedules and resource allocation.
Continuous Improvement
Promote a culture of continuous improvement within the organization.
Regularly review TPM activities and maintenance strategies to identify areas for enhancement.
Encourage teams to share best practices and innovative ideas to further optimize processes and achieve better results.
By understanding the principles of TPM and implementing effective maintenance approaches, new leaders in equipment technology departments can significantly improve operational efficiency in their organizations.
A proactive approach to equipment maintenance not only enhances productivity but also contributes to a safer and more sustainable work environment.
資料ダウンロード
QCD調達購買管理クラウド「newji」は、調達購買部門で必要なQCD管理全てを備えた、現場特化型兼クラウド型の今世紀最高の購買管理システムとなります。
ユーザー登録
調達購買業務の効率化だけでなく、システムを導入することで、コスト削減や製品・資材のステータス可視化のほか、属人化していた購買情報の共有化による内部不正防止や統制にも役立ちます。
NEWJI DX
製造業に特化したデジタルトランスフォーメーション(DX)の実現を目指す請負開発型のコンサルティングサービスです。AI、iPaaS、および先端の技術を駆使して、製造プロセスの効率化、業務効率化、チームワーク強化、コスト削減、品質向上を実現します。このサービスは、製造業の課題を深く理解し、それに対する最適なデジタルソリューションを提供することで、企業が持続的な成長とイノベーションを達成できるようサポートします。
オンライン講座
製造業、主に購買・調達部門にお勤めの方々に向けた情報を配信しております。
新任の方やベテランの方、管理職を対象とした幅広いコンテンツをご用意しております。
お問い合わせ
コストダウンが利益に直結する術だと理解していても、なかなか前に進めることができない状況。そんな時は、newjiのコストダウン自動化機能で大きく利益貢献しよう!
(Β版非公開)