- お役立ち記事
- Successful examples of TQM implementation and quality improvement that quality assurance department leaders should keep in mind
Successful examples of TQM implementation and quality improvement that quality assurance department leaders should keep in mind
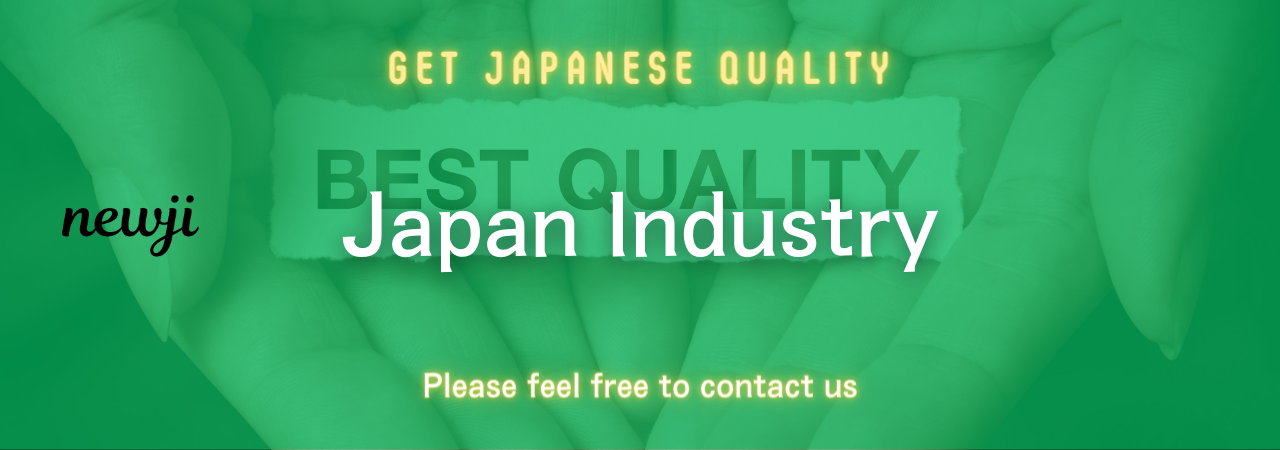
Total Quality Management (TQM) is a strategic approach focused on improving quality across an organization through a collective effort, which involves everyone, from the top executives to frontline staff.
This holistic approach emphasizes customer satisfaction, performance improvement, and a commitment to excellence.
To help understand how TQM can be effectively implemented, we’ll look at successful examples of quality management that leaders in quality assurance departments can learn from.
目次
Understanding Total Quality Management (TQM)
TQM revolves around the concept that long-term success can be achieved through customer satisfaction, and that company processes should revolve around this goal.
It involves the involvement of all members of an organization in improving processes, products, and services to ensure overall efficiency and quality.
Key practices typically include leadership involvement, employee empowerment, a focus on process analysis, customer feedback, and continuous improvement.
Leaders should work to create a quality-oriented culture where everyone is responsible for contributing to the company’s success.
Case Study: Toyota Production System (TPS)
One of the most famous examples of TQM in action is the Toyota Production System (TPS).
TPS emphasizes high-quality production through effective workplace practices and lean manufacturing principles.
This approach has not only enhanced Toyota’s product quality but has also revolutionized manufacturing globally.
The system is built on the principles of “just-in-time” production—producing only what is needed, when it is needed—and “jidoka,” or automation with a human touch, ensuring machines halt automatically when issues are detected.
TPS showcases the significance of reducing waste, optimizing processes, and making quality the responsibility of everyone in the company.
Key Takeaways for Quality Leaders
– **Employee Empowerment**: Involve all employees in quality initiatives, providing training and responsibilities to ensure they feel a part of the improvement process.
– **Continuous Improvement**: Regularly review and refine processes, encouraging small, consistent improvements rather than sporadic major changes.
– **Customer Focus**: Maintain a strong focus on fulfilling customer needs and feedback to guide quality improvements.
Case Study: Philips’ Quality Transformation
Philips, a leader in many electronic sectors, has successfully leveraged TQM to transform its quality approach.
By integrating TQM into its culture, Philips focused on reducing defects and enhancing product reliability.
This was achieved by streamlining processes to achieve global production consistency while still allowing for local adaptations where necessary.
They implemented a stringent focus on quality standards, ensuring products met or exceeded customer expectations.
Through a global quality transformation program, Philips has managed to significantly lower failure rates across its product lines and improve customer satisfaction.
Key Takeaways for Quality Leaders
– **Standardized Processes**: Develop standardized yet adaptive processes to maintain quality across different geographical regions.
– **Training**: Invest in comprehensive training and development for employees to understand and apply quality control measures effectively.
– **Data-Driven Decisions**: Use data analytics to monitor quality metrics and identify areas for improvement.
Case Study: Motorola’s Six Sigma Initiative
Motorola is credited with developing the Six Sigma methodology, which has been widely adopted by numerous industries for quality improvement.
This strategy is a data-driven approach that seeks to eliminate defects in processes and ensure product quality is maintained.
Motorola’s implementation of Six Sigma helped improve process efficiency, product quality, and employee involvement by prioritizing statistical analysis and performance metrics.
The success of this methodology lies in its structured approach to problem-solving and its focus on reducing variability and defects.
Key Takeaways for Quality Leaders
– **Structured Problem-Solving**: Implement structured problem-solving approaches like DMAIC (Define, Measure, Analyze, Improve, Control) to address issues systematically.
– **Performance Metrics**: Establish clear performance metrics to measure progress and drive improvement.
– **Cultural Adoption**: Ensure that quality improvement philosophies, such as Six Sigma, are ingrained in the company culture to sustain changes.
Key Principles for Successful TQM Implementation
The case studies provide valuable insights into successfully implementing TQM.
Here are some key principles that quality assurance department leaders should consider:
Leadership Commitment
Successful TQM starts with leadership.
Leaders must commit to a quality-centric approach, demonstrating this commitment through actions and resource allocation.
When leaders exemplify quality management principles, it inspires employees to follow suit.
Customer Centricity
Ensuring customer satisfaction is at the heart of TQM.
Processes should be evaluated and adjusted based on feedback from customers to meet or exceed their expectations.
This focus not only improves quality but also builds long-term customer loyalty.
Continuous Improvement
TQM is not a one-time initiative.
It requires ongoing effort to improve all aspects of the business continuously.
By fostering an environment where employees are encouraged to seek out and suggest improvements, companies can consistently achieve higher quality levels.
Collaboration and Communication
Effective collaboration among departments and open communication channels are critical for TQM success.
Aligning goals, sharing knowledge, and discussing problems collectively can lead to better quality outcomes.
Conclusion
By looking at successful examples of TQM implementation, it becomes clear that with the right approach, significant improvements in quality and efficiency can be achieved.
Quality assurance department leaders play a crucial role in fostering an environment where quality is the shared responsibility of all, leading to better products, processes, and ultimately, satisfied customers.
The key to successful TQM lies in commitment, empowerment, and the continuous pursuit of excellence.
資料ダウンロード
QCD調達購買管理クラウド「newji」は、調達購買部門で必要なQCD管理全てを備えた、現場特化型兼クラウド型の今世紀最高の購買管理システムとなります。
ユーザー登録
調達購買業務の効率化だけでなく、システムを導入することで、コスト削減や製品・資材のステータス可視化のほか、属人化していた購買情報の共有化による内部不正防止や統制にも役立ちます。
NEWJI DX
製造業に特化したデジタルトランスフォーメーション(DX)の実現を目指す請負開発型のコンサルティングサービスです。AI、iPaaS、および先端の技術を駆使して、製造プロセスの効率化、業務効率化、チームワーク強化、コスト削減、品質向上を実現します。このサービスは、製造業の課題を深く理解し、それに対する最適なデジタルソリューションを提供することで、企業が持続的な成長とイノベーションを達成できるようサポートします。
オンライン講座
製造業、主に購買・調達部門にお勤めの方々に向けた情報を配信しております。
新任の方やベテランの方、管理職を対象とした幅広いコンテンツをご用意しております。
お問い合わせ
コストダウンが利益に直結する術だと理解していても、なかなか前に進めることができない状況。そんな時は、newjiのコストダウン自動化機能で大きく利益貢献しよう!
(Β版非公開)