- お役立ち記事
- Unlocking Precision: The Role of Traceability in Japanese Manufacturing Excellence
Unlocking Precision: The Role of Traceability in Japanese Manufacturing Excellence
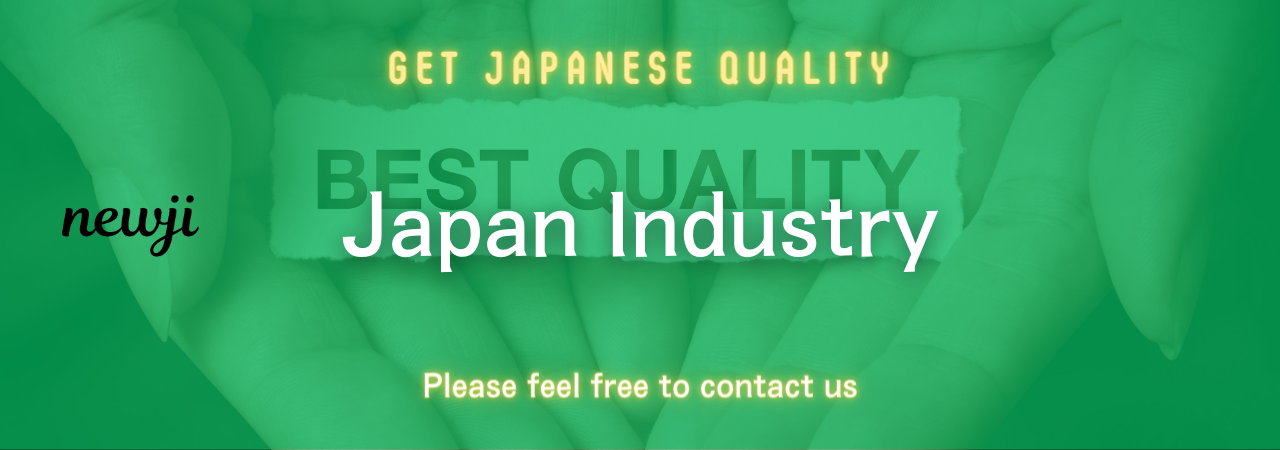
目次
Introduction to Traceability in Japanese Manufacturing
Traceability has become a cornerstone of Japanese manufacturing excellence. It refers to the ability to track and trace the history, application, and location of products and their components throughout the supply chain. Japanese manufacturers have long recognized the importance of detailed traceability systems in ensuring high quality, enhancing efficiency, and maintaining their competitive edge in the global market.
The Importance of Traceability in Procurement and Purchasing
In the realm of procurement and purchasing, traceability plays a critical role in ensuring that materials and components meet stringent quality standards. By implementing robust traceability systems, companies can monitor the origin of materials, verify supplier compliance, and mitigate risks associated with supply chain disruptions.
Enhancing Quality Control
Traceability allows procurement teams to maintain detailed records of each component’s journey from the supplier to the final product. This level of detail facilitates rigorous quality control checks at every stage of the manufacturing process. In the event of a defect or quality issue, traceability enables swift identification of the root cause, allowing for effective corrective actions and minimizing the impact on the final product.
Supplier Verification and Compliance
Japanese manufacturers often work with a network of suppliers that meet strict quality and ethical standards. Traceability systems help verify that suppliers adhere to these standards by providing transparent information about their processes and materials. This verification is essential for maintaining the integrity of the supply chain and ensuring compliance with industry regulations and certifications.
Advantages of Traceability in Japanese Manufacturing
Implementing traceability in manufacturing offers numerous advantages that contribute to the overall excellence of Japanese companies.
Improved Efficiency and Productivity
With traceability, manufacturers can streamline their operations by having real-time access to data on materials and processes. This information enables more efficient inventory management, reduces waste, and minimizes downtime caused by unexpected supply chain issues.
Enhanced Customer Confidence
Customers increasingly demand transparency and accountability from manufacturers. Traceability provides clear evidence of a product’s journey, from raw materials to the finished item, thereby building trust and confidence in the brand. This transparency is particularly important in industries where safety and reliability are paramount.
Risk Mitigation
Traceability systems help identify potential risks and bottlenecks in the supply chain. By having comprehensive visibility into each stage of production, companies can proactively address issues before they escalate, reducing the likelihood of costly recalls or disruptions.
Challenges and Disadvantages of Implementing Traceability
While traceability offers significant benefits, there are also challenges and disadvantages associated with its implementation.
High Initial Investment
Setting up a robust traceability system requires substantial investment in technology, training, and process redesign. For some companies, particularly smaller manufacturers, the upfront costs can be a barrier to adoption.
Complexity and Integration Issues
Integrating traceability systems with existing manufacturing processes and technologies can be complex. Ensuring seamless data flow across different departments and stages of production requires careful planning and coordination.
Data Management and Privacy Concerns
Managing the vast amounts of data generated by traceability systems poses significant challenges. Companies must implement effective data management strategies to handle information securely and comply with privacy regulations.
Supplier Negotiation Techniques in a Traceable Supply Chain
Effective supplier negotiation is essential for maintaining a traceable and efficient supply chain. Japanese manufacturers employ several techniques to ensure strong collaboration and compliance with traceability requirements.
Building Long-Term Relationships
Japanese business culture emphasizes long-term relationships and mutual trust with suppliers. By fostering strong partnerships, manufacturers can encourage suppliers to adhere to traceability standards and continuously improve their processes.
Clear Communication of Requirements
Clear and precise communication of traceability requirements is crucial during negotiations. Manufacturers must articulate their expectations regarding data sharing, quality standards, and reporting protocols to ensure suppliers understand and commit to the necessary traceability practices.
Incentivizing Compliance
Offering incentives for suppliers who consistently meet traceability standards can motivate adherence and improvement. These incentives may include preferred supplier status, long-term contracts, or financial rewards for exceptional performance.
Market Conditions Influencing Traceability Practices
Market conditions play a significant role in shaping traceability practices within Japanese manufacturing.
Globalization and Supply Chain Complexity
As supply chains become more global and complex, the need for effective traceability systems increases. Japanese manufacturers must navigate diverse regulatory environments and manage relationships with a broader range of suppliers, making traceability essential for maintaining control and quality.
Regulatory Requirements
Regulatory standards around the world are evolving to demand greater transparency and traceability in manufacturing. Compliance with these regulations is mandatory for accessing certain markets and avoiding legal penalties, driving Japanese manufacturers to prioritize traceability.
Consumer Demand for Transparency
Modern consumers are more informed and concerned about the origins and manufacturing processes of the products they purchase. This demand for transparency compels manufacturers to implement traceability systems that provide detailed information about their products.
Best Practices for Implementing Traceability in Japanese Manufacturing
Adopting best practices can significantly enhance the effectiveness of traceability systems in Japanese manufacturing.
Investing in Advanced Technology
Leveraging advanced technologies such as RFID, IoT, and blockchain can enhance traceability by providing real-time data and ensuring data integrity. These technologies enable seamless tracking of materials and products throughout the supply chain.
Standardizing Processes and Data Formats
Standardizing traceability processes and data formats across the organization and among suppliers facilitates easier data integration and analysis. Consistency in data collection and reporting ensures that traceability information is reliable and actionable.
Training and Empowering Employees
Comprehensive training programs are essential to ensure that employees at all levels understand the importance of traceability and are proficient in using traceability systems. Empowering employees to take ownership of traceability processes fosters a culture of accountability and continuous improvement.
Continuous Monitoring and Improvement
Traceability is not a one-time implementation but requires ongoing monitoring and improvement. Regularly reviewing traceability data, seeking feedback from stakeholders, and staying updated with technological advancements help maintain and enhance traceability systems over time.
Case Studies: Successful Implementation of Traceability in Japanese Manufacturing
Examining real-world examples of successful traceability implementation provides valuable insights into best practices and strategies.
Toyota’s Just-In-Time (JIT) System
Toyota’s JIT manufacturing system relies heavily on traceability to ensure that materials arrive exactly when needed, reducing inventory costs and waste. By meticulously tracking each component’s status and location, Toyota maintains high efficiency and responsiveness to production demands.
Panasonic’s Quality Management
Panasonic has implemented comprehensive traceability systems across its manufacturing operations to maintain stringent quality standards. By tracking each product’s lifecycle, Panasonic ensures that defects are quickly identified and addressed, enhancing overall product reliability.
Sony’s Supply Chain Transparency
Sony has embraced traceability to enhance supply chain transparency, allowing customers to access detailed information about the sourcing and manufacturing processes of their products. This transparency has strengthened customer trust and loyalty, contributing to Sony’s market success.
The Future of Traceability in Japanese Manufacturing
Looking ahead, traceability is poised to become even more integral to Japanese manufacturing excellence.
Integration with Artificial Intelligence and Machine Learning
The integration of AI and machine learning with traceability systems will enable manufacturers to analyze vast amounts of data more efficiently. Predictive analytics can identify trends and potential issues, allowing for proactive decision-making and further optimization of the supply chain.
Blockchain for Enhanced Security and Transparency
Blockchain technology offers unmatched security and transparency for traceability systems. By providing immutable records of each transaction and process, blockchain can enhance trust among supply chain partners and ensure the integrity of traceability data.
Sustainability and Ethical Manufacturing
As sustainability and ethical manufacturing practices gain prominence, traceability will play a crucial role in verifying the responsible sourcing of materials and ensuring environmentally friendly production processes. Japanese manufacturers will continue to leverage traceability to meet these growing demands and uphold their reputation for excellence.
Conclusion
Traceability is a fundamental element of Japanese manufacturing excellence, influencing every aspect of procurement and purchasing. By implementing robust traceability systems, Japanese manufacturers ensure high quality, enhance efficiency, and maintain strong supplier relationships. Despite the challenges associated with traceability, the advantages it offers in risk mitigation, customer confidence, and operational efficiency make it indispensable. As technology advances and market demands evolve, traceability will continue to be a key driver of innovation and sustainability in Japanese manufacturing, securing its position as a leader in the global market.
資料ダウンロード
QCD調達購買管理クラウド「newji」は、調達購買部門で必要なQCD管理全てを備えた、現場特化型兼クラウド型の今世紀最高の購買管理システムとなります。
ユーザー登録
調達購買業務の効率化だけでなく、システムを導入することで、コスト削減や製品・資材のステータス可視化のほか、属人化していた購買情報の共有化による内部不正防止や統制にも役立ちます。
NEWJI DX
製造業に特化したデジタルトランスフォーメーション(DX)の実現を目指す請負開発型のコンサルティングサービスです。AI、iPaaS、および先端の技術を駆使して、製造プロセスの効率化、業務効率化、チームワーク強化、コスト削減、品質向上を実現します。このサービスは、製造業の課題を深く理解し、それに対する最適なデジタルソリューションを提供することで、企業が持続的な成長とイノベーションを達成できるようサポートします。
オンライン講座
製造業、主に購買・調達部門にお勤めの方々に向けた情報を配信しております。
新任の方やベテランの方、管理職を対象とした幅広いコンテンツをご用意しております。
お問い合わせ
コストダウンが利益に直結する術だと理解していても、なかなか前に進めることができない状況。そんな時は、newjiのコストダウン自動化機能で大きく利益貢献しよう!
(Β版非公開)