- お役立ち記事
- For production management department leaders! Strategy to shorten lead time by incorporating LEAN production method
For production management department leaders! Strategy to shorten lead time by incorporating LEAN production method
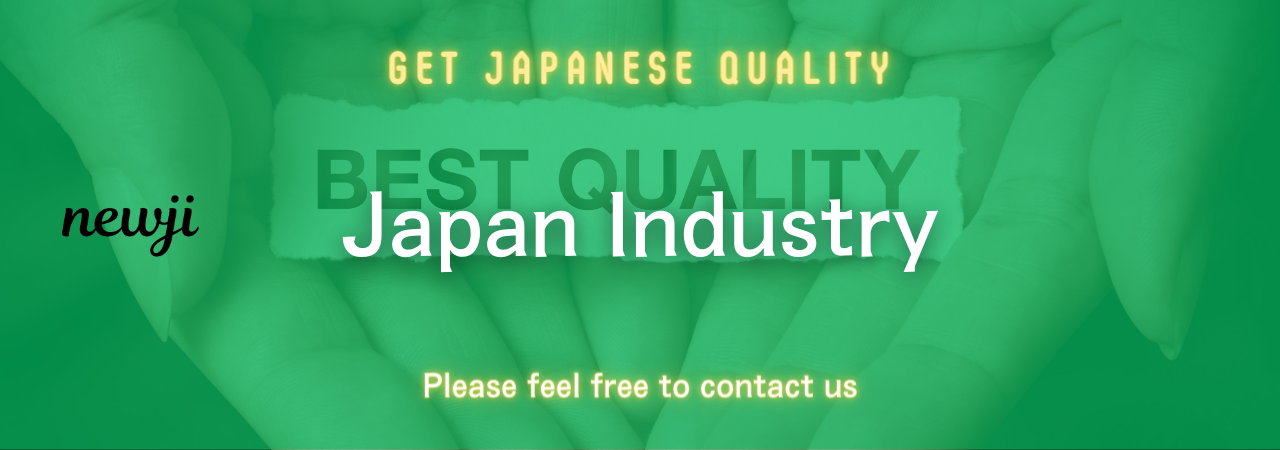
目次
Understanding Lead Time and Its Importance
Lead time is a critical component of the production process that refers to the total time it takes from the initiation of a production order to the delivery of the finished product to the customer.
In today’s fast-paced and competitive market, minimizing lead time is essential for gaining a competitive edge, improving customer satisfaction, and maximizing efficiency in the supply chain.
Production management department leaders play a crucial role in optimizing lead time by implementing effective strategies and practices.
Introducing the LEAN Production Method
The LEAN production method, also known as Lean Manufacturing, is a systematic approach to streamlining production processes by eliminating waste, improving quality, and increasing efficiency.
Developed by Toyota in the 20th century, LEAN methodology focuses on continuously enhancing the production process by identifying and removing non-value-adding activities, thereby shortening lead time and improving overall performance.
By incorporating LEAN principles, production management leaders can create an agile and responsive production environment.
Key Principles of LEAN Production
Before integrating LEAN methodology into production processes, it’s essential to understand its core principles:
1. **Value Identification**: Determine what the customer perceives as value and focus on delivering it.
2. **Value Stream Mapping**: Analyze the entire production process to identify areas of waste and inefficiency.
3. **Flow Creation**: Ensure a smooth and uninterrupted flow of materials and information across the production line.
4. **Pull System Implementation**: Produce only in response to customer demand to avoid overproduction and excess inventory.
5. **Continuous Improvement (Kaizen)**: Encourage ongoing evaluation and refinement of production processes to enhance performance.
Strategies to Shorten Lead Time Using LEAN
To effectively reduce lead time, production management leaders should integrate the following LEAN strategies:
1. Eliminate Waste
Waste reduction is the cornerstone of the LEAN production method.
By identifying and eliminating waste in the production process, you can significantly shorten lead time. Waste can manifest in several forms, including excess inventory, waiting times, overproduction, defective products, and inefficient transportation.
Start by conducting a thorough analysis of the current processes to pinpoint areas of waste and implement corrective actions to streamline operations.
2. Standardize Work Processes
Standardizing work processes ensures a consistent and efficient production environment.
By implementing standardized procedures, you can reduce variability and improve process control, ultimately minimizing lead time.
Standardized processes help employees understand their roles, improve communication, and reduce the likelihood of errors.
Encourage feedback from team members to refine and enhance standardized procedures continually.
3. Optimize Inventory Management
Efficient inventory management is crucial for reducing lead time.
Implementing a just-in-time (JIT) inventory system aligns production schedules with customer demand, minimizing excess inventory and associated holding costs.
By maintaining optimal inventory levels, you can reduce the time needed to process and fulfill orders, leading to shorter lead times and increased customer satisfaction.
4. Implement a Pull System
A pull system is a critical component of LEAN methodology that ensures production is driven by actual customer demand rather than forecasts.
By implementing a pull system, you can minimize overproduction, reduce inventory levels, and optimize resource allocation.
This system allows for a quick response to changes in customer demand and helps maintain a smooth production flow.
5. Enhance Workforce Training and Engagement
A skilled and engaged workforce is vital for successfully implementing LEAN strategies.
Invest in regular training and development programs to equip employees with the necessary skills and knowledge to execute their tasks efficiently.
Encourage a culture of continuous improvement where employees actively contribute ideas and suggestions to optimize processes and reduce lead time.
Recognize and reward team members for their contributions to fostering a positive and innovative work environment.
6. Foster Strong Supplier Relationships
Effective supplier management is essential for reducing lead time.
Develop strong relationships with suppliers to ensure timely delivery of materials and components.
Collaborate with suppliers to identify and resolve potential bottlenecks, and seek opportunities to streamline the supply chain.
By maintaining open lines of communication with suppliers, you can enhance the overall efficiency of the production process.
Measuring the Impact of LEAN on Lead Time
To determine the success of LEAN implementation in reducing lead time, it’s essential to measure and analyze key performance indicators (KPIs).
Monitor metrics such as production cycle time, order fulfillment speed, on-time delivery rate, and overall equipment effectiveness (OEE).
Regularly review these KPIs to assess the impact of LEAN strategies and identify areas for further improvement.
By tracking progress and making data-driven decisions, production management leaders can continuously refine their approach to achieving optimal lead time.
Conclusion
Incorporating the LEAN production method is a proven strategy for production management department leaders seeking to shorten lead time and enhance operational efficiency.
By focusing on waste reduction, standardizing work processes, optimizing inventory management, and fostering a culture of continuous improvement, organizations can achieve significant improvements in lead time and overall performance.
As markets continue to evolve, the ability to respond quickly and efficiently to customer demands will remain a critical competitive advantage, and LEAN methodology provides the tools necessary to succeed in this dynamic environment.
資料ダウンロード
QCD調達購買管理クラウド「newji」は、調達購買部門で必要なQCD管理全てを備えた、現場特化型兼クラウド型の今世紀最高の購買管理システムとなります。
ユーザー登録
調達購買業務の効率化だけでなく、システムを導入することで、コスト削減や製品・資材のステータス可視化のほか、属人化していた購買情報の共有化による内部不正防止や統制にも役立ちます。
NEWJI DX
製造業に特化したデジタルトランスフォーメーション(DX)の実現を目指す請負開発型のコンサルティングサービスです。AI、iPaaS、および先端の技術を駆使して、製造プロセスの効率化、業務効率化、チームワーク強化、コスト削減、品質向上を実現します。このサービスは、製造業の課題を深く理解し、それに対する最適なデジタルソリューションを提供することで、企業が持続的な成長とイノベーションを達成できるようサポートします。
オンライン講座
製造業、主に購買・調達部門にお勤めの方々に向けた情報を配信しております。
新任の方やベテランの方、管理職を対象とした幅広いコンテンツをご用意しております。
お問い合わせ
コストダウンが利益に直結する術だと理解していても、なかなか前に進めることができない状況。そんな時は、newjiのコストダウン自動化機能で大きく利益貢献しよう!
(Β版非公開)