- お役立ち記事
- For new employees in the equipment technology department! Fundamentals of reliability engineering and practice of equipment testing
For new employees in the equipment technology department! Fundamentals of reliability engineering and practice of equipment testing
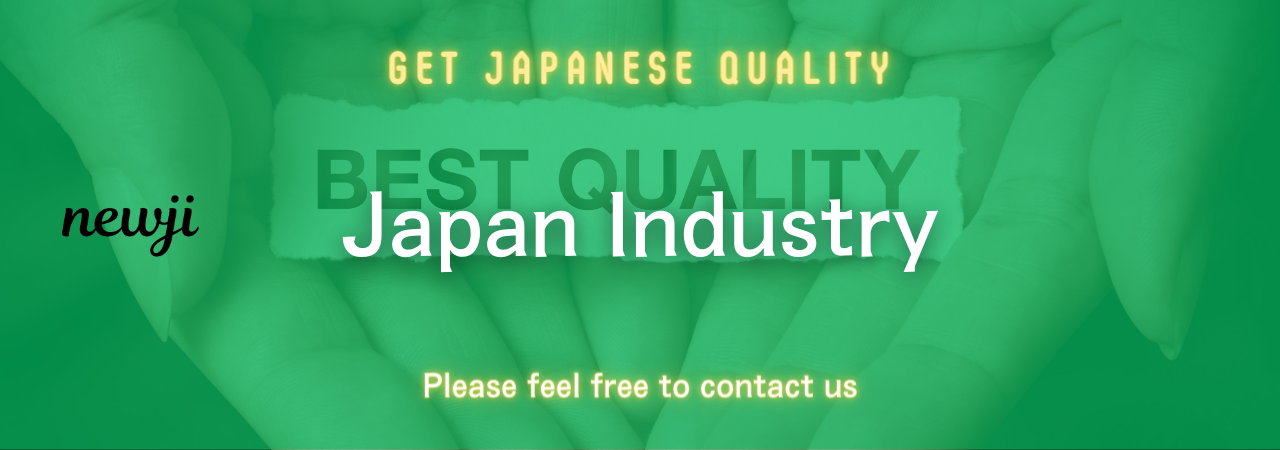
目次
Understanding Reliability Engineering
When you step into the equipment technology department, you are greeted by the fascinating world of reliability engineering.
This field plays a vital role in ensuring that machinery and equipment are dependable and function as expected over time.
But what is reliability engineering, and why is it important?
In essence, reliability engineering is a discipline focused on making products, systems, and processes durable, efficient, and less prone to failure.
Reliability ensures that equipment performs its intended function without interruption within a specific time frame.
This involves analyzing several factors, such as the equipment’s design, materials used, manufacturing process, and environment.
The ultimate goal is to prevent costly downtimes, improve safety, and foster customer confidence.
The Core Principles of Reliability Engineering
Let’s delve deeper into the core principles that underpin reliability engineering.
1. Reliability Prediction
Reliability prediction involves estimating the likelihood that equipment will perform its function without failure within a specific time frame.
By analyzing design specifications, historical data, and statistical models, engineers can forecast potential failure points and take preventive measures.
2. Reliability Testing
Testing is critical to validate the reliability of equipment.
It simulates real-world conditions to ensure that the machinery can withstand various stresses and strains.
By conducting tests, engineers can identify weak points and areas for improvement before the equipment reaches the market.
3. Failure Modes and Effects Analysis (FMEA)
FMEA is a systematic approach to identifying potential failure modes in a product or process.
By analyzing possible effects and prioritizing them based on severity, engineers can mitigate risks and enhance reliability.
This proactive approach helps in designing robust equipment that stands the test of time.
4. Root Cause Analysis
In the unfortunate event of equipment failure, it is vital to understand the underlying causes.
Root cause analysis digs deep into the factors that led to a malfunction.
This helps engineers to implement corrective actions and prevent recurrence, thus enhancing reliability.
5. Maintenance Strategies
Proactive maintenance strategies are indispensable in reliability engineering.
By conducting regular inspections, servicing, and timely repairs, the lifespan of equipment can be significantly extended.
Predictive maintenance, using data analytics and sensor technology, can identify wear and tear before it leads to failure.
Practical Aspects of Equipment Testing
Now that you are familiar with the principles of reliability engineering, let’s explore the practical side of equipment testing.
Types of Testing
Various types of equipment testing are employed in reliability engineering.
These tests ensure that the machinery meets quality standards and performs optimally.
1. Functional Testing
Functional testing assesses if the equipment performs its intended tasks under normal operating conditions.
This involves running the machinery and evaluating its performance against predefined criteria.
2. Environmental Testing
Environmental testing simulates harsh conditions such as extreme temperatures, humidity, and vibrations.
It evaluates how the equipment withstands various environmental factors, ensuring reliability in diverse settings.
3. Accelerated Life Testing
Accelerated life testing subjects equipment to extreme stressors to estimate its lifespan in a shorter time frame.
This helps predict potential weaknesses and rectify them before large-scale deployment.
4. Stress Testing
Stress testing pushes equipment to its operational limits to evaluate performance under duress.
This helps identify the equipment’s capacity to endure high demand and its potential points of failure.
5. Load Testing
Load testing involves applying varying levels of load to assess if the equipment maintains functionality and performance.
It ensures that machines can handle maximum capacity without malfunctioning.
Bringing It All Together
For new employees in the equipment technology department, grasping the fundamentals of reliability engineering is crucial.
A solid understanding of principles like reliability prediction, testing, FMEA, root cause analysis, and maintenance strategies will empower you to evaluate and enhance equipment reliability effectively.
Engaging in practical equipment testing will provide firsthand experience and knowledge, paving the way for improvements and innovation.
Remember, the quest for reliability is constant and requires dedication, observation, and a proactive mindset.
As you embark on this journey, continual learning and collaboration with experienced professionals will sharpen your skills and solidify your contribution to creating reliable and efficient equipment in the industry.
Your role in ensuring reliability will not only prevent failures but also uphold safety and strengthen customer trust.
With a blend of theoretical understanding and hands-on practice, you will become a valuable asset in the ever-evolving field of equipment technology.
資料ダウンロード
QCD調達購買管理クラウド「newji」は、調達購買部門で必要なQCD管理全てを備えた、現場特化型兼クラウド型の今世紀最高の購買管理システムとなります。
ユーザー登録
調達購買業務の効率化だけでなく、システムを導入することで、コスト削減や製品・資材のステータス可視化のほか、属人化していた購買情報の共有化による内部不正防止や統制にも役立ちます。
NEWJI DX
製造業に特化したデジタルトランスフォーメーション(DX)の実現を目指す請負開発型のコンサルティングサービスです。AI、iPaaS、および先端の技術を駆使して、製造プロセスの効率化、業務効率化、チームワーク強化、コスト削減、品質向上を実現します。このサービスは、製造業の課題を深く理解し、それに対する最適なデジタルソリューションを提供することで、企業が持続的な成長とイノベーションを達成できるようサポートします。
オンライン講座
製造業、主に購買・調達部門にお勤めの方々に向けた情報を配信しております。
新任の方やベテランの方、管理職を対象とした幅広いコンテンツをご用意しております。
お問い合わせ
コストダウンが利益に直結する術だと理解していても、なかなか前に進めることができない状況。そんな時は、newjiのコストダウン自動化機能で大きく利益貢献しよう!
(Β版非公開)