- お役立ち記事
- A must-see for equipment maintenance department managers! How to extend the life of your equipment with reliability testing
A must-see for equipment maintenance department managers! How to extend the life of your equipment with reliability testing
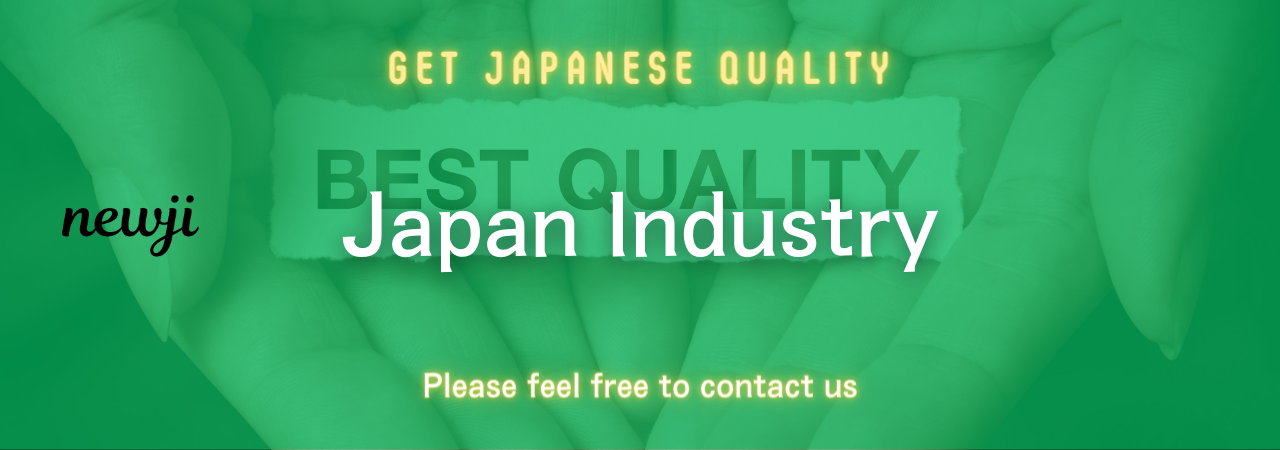
目次
Understanding Reliability Testing
Reliability testing is an essential part of equipment maintenance that helps ensure the durability and longevity of machinery and tools used in various industries.
This type of testing evaluates how a piece of equipment performs under different conditions over time.
By doing so, it helps predict the lifespan of the equipment and identifies potential issues before they become critical failures.
Understanding the importance and application of reliability testing can significantly benefit equipment maintenance department managers by enhancing the efficiency and performance of their assets.
Why Reliability Testing Matters
Reliability testing is fundamental to maintaining the ongoing performance and efficiency of equipment.
When done properly, this testing can save costs by reducing the frequency of repairs and replacements.
It provides insights into how equipment responds to stress and different operational environments.
With these insights, maintenance teams can make informed decisions about the timing of repairs and necessary upgrades.
Moreover, reliability testing contributes to safety by identifying potential weak points in equipment that could lead to accidents or failures.
Key Components of Reliability Testing
Reliability testing is not a one-size-fits-all process; it comprises various components tailored to specific equipment and industry needs.
These components include environmental testing, life testing, and stress testing.
Each plays a crucial role in determining the reliability and expected lifespan of equipment.
Understanding these components helps ensure the testing is effective and comprehensive.
Environmental Testing
Environmental testing examines how equipment responds to various environmental conditions.
This could include extreme temperatures, humidity, dust, and vibration.
By simulating these environmental conditions, maintenance managers can understand how the equipment will perform under real-world conditions.
This type of testing helps in predicting failure modes and preventing premature wear and tear.
For instance, equipment that operates in a hot and dusty environment may have different maintenance needs than equipment used in a clean, climate-controlled setting.
Life Testing
Life testing involves operating equipment until it fails to determine its lifespan.
This testing helps identify how long equipment can perform its function under normal conditions before it begins to break down.
Understanding the lifespan helps maintenance managers schedule replacements or overhauls before critical failures occur.
Life testing offers valuable data on the longevity of components and materials, assisting in choosing better materials and designs for future purchases.
Stress Testing
Stress testing evaluates how equipment performs under extreme conditions beyond normal operational limits.
This testing identifies the breaking points of equipment and provides insights into durability and robustness.
By understanding these limits, maintenance managers can develop strategies to avoid pushing equipment beyond its capabilities, reducing the risk of failure.
Stress testing is also valuable for refining equipment specifications and improving design features to enhance performance and reliability.
Implementing Reliability Testing in Your Maintenance Strategy
Incorporating reliability testing into your maintenance strategy is a proactive approach to extending the life of equipment.
It allows maintenance teams to move from reactive to preventive and predictive maintenance.
This shift is crucial for maximizing operational efficiency and minimizing downtime.
Creating a Test Plan
Developing a comprehensive test plan is the first step in successful reliability testing.
This plan should outline the types of tests, the conditions for testing, and the metrics used for evaluation.
Define clear objectives for each test, such as identifying the most common failure modes or establishing a baseline for future evaluations.
Involving cross-functional teams in the planning phase ensures that all operational perspectives are considered.
Data Analysis and Interpretation
The ability to collect and analyze data is crucial in reliability testing.
Data collected during tests must be meticulously recorded and analyzed to draw meaningful conclusions.
Utilize statistical tools and software to identify patterns and correlations in the data.
Interpretation of results should involve collaboration with engineers and field technicians to ensure all angles are examined.
Reliable data analysis can help pinpoint specific areas for improvement and optimize maintenance schedules.
Continuous Improvement
Reliability testing is not a one-time activity but a continuous process.
As new data become available and as equipment evolves, the testing strategies should be updated and refined.
Promote a culture of continuous improvement within the maintenance department to ensure that insights gained from testing lead to actionable changes.
This proactive approach not only extends the life of equipment but also enhances safety and efficiency across operations.
The Impact of Reliability Testing on Equipment Life
The implementation of reliability testing can significantly extend the life of equipment.
By identifying potential issues early, it prevents unexpected breakdowns and extends operating intervals.
Reduced downtime translates into cost savings and increased productivity.
In addition, improved reliability enhances customer satisfaction, as they experience fewer disruptions and improved performance.
Incorporating reliability testing into the maintenance strategy demonstrates a commitment to quality and operational excellence.
Conclusion
Reliability testing is an invaluable tool for equipment maintenance department managers seeking to maximize the lifespan and efficiency of their assets.
By understanding and implementing key components such as environmental, life, and stress testing, maintenance managers can anticipate issues and make informed decisions.
As part of a comprehensive maintenance strategy, reliability testing fosters a proactive approach that enhances safety, reduces costs, and ensures equipment longevity.
Embrace reliability testing as a fundamental part of your maintenance practice to achieve sustainable operational success.
資料ダウンロード
QCD調達購買管理クラウド「newji」は、調達購買部門で必要なQCD管理全てを備えた、現場特化型兼クラウド型の今世紀最高の購買管理システムとなります。
ユーザー登録
調達購買業務の効率化だけでなく、システムを導入することで、コスト削減や製品・資材のステータス可視化のほか、属人化していた購買情報の共有化による内部不正防止や統制にも役立ちます。
NEWJI DX
製造業に特化したデジタルトランスフォーメーション(DX)の実現を目指す請負開発型のコンサルティングサービスです。AI、iPaaS、および先端の技術を駆使して、製造プロセスの効率化、業務効率化、チームワーク強化、コスト削減、品質向上を実現します。このサービスは、製造業の課題を深く理解し、それに対する最適なデジタルソリューションを提供することで、企業が持続的な成長とイノベーションを達成できるようサポートします。
オンライン講座
製造業、主に購買・調達部門にお勤めの方々に向けた情報を配信しております。
新任の方やベテランの方、管理職を対象とした幅広いコンテンツをご用意しております。
お問い合わせ
コストダウンが利益に直結する術だと理解していても、なかなか前に進めることができない状況。そんな時は、newjiのコストダウン自動化機能で大きく利益貢献しよう!
(Β版非公開)