- お役立ち記事
- “Unveiling the Secret Weapon of Japanese Manufacturing: The Total Cost Model”
“Unveiling the Secret Weapon of Japanese Manufacturing: The Total Cost Model”
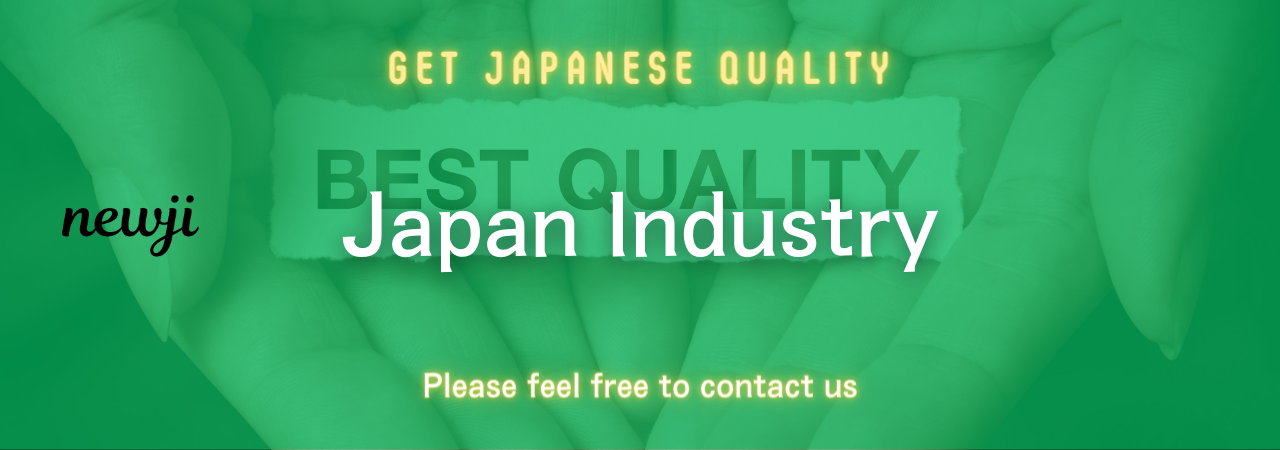
目次
Introduction
The Japanese manufacturing sector is renowned for its efficiency and high-quality output.
Central to this success is the implementation of the Total Cost Model.
This model goes beyond traditional cost-cutting measures by considering all aspects of the manufacturing process.
Understanding and applying the Total Cost Model can provide significant advantages in procurement and purchasing.
In this article, we will explore the intricacies of the Total Cost Model, its advantages and disadvantages, negotiation techniques with suppliers, current market conditions, and best practices for successful implementation.
Understanding the Total Cost Model
What is the Total Cost Model?
The Total Cost Model is a comprehensive approach to cost management in manufacturing.
Unlike traditional models that focus solely on the purchase price of goods or services.
It takes into account all associated costs throughout the entire lifecycle of a product or service.
These costs include acquisition costs, transportation, storage, maintenance, and disposal.
By considering the total cost, companies can make more informed decisions that enhance overall efficiency and profitability.
Importance in Japanese Manufacturing
Japanese manufacturers have long embraced the Total Cost Model as a cornerstone of their production strategies.
This approach aligns with the principles of lean manufacturing and continuous improvement, or Kaizen.
By focusing on total costs, Japanese companies can identify and eliminate waste in their processes.
This leads to higher quality products, reduced lead times, and increased customer satisfaction.
Moreover, the Total Cost Model fosters a collaborative relationship between manufacturers and suppliers, promoting long-term partnerships.
Advantages of the Total Cost Model
Cost Efficiency
One of the primary advantages of the Total Cost Model is enhanced cost efficiency.
By considering all cost factors, companies can identify areas where expenses can be reduced without compromising quality.
This holistic view helps in avoiding hidden costs that might arise from short-term savings.
For example, selecting a supplier with a slightly higher unit price but lower transportation costs can lead to overall savings.
Enhanced Quality Control
The Total Cost Model emphasizes quality throughout the production process.
Higher quality standards reduce the likelihood of defects and returns, leading to cost savings in the long run.
Japanese manufacturers often implement rigorous quality control measures as part of their total cost analysis.
This commitment to quality ensures that products meet or exceed customer expectations, fostering brand loyalty.
Improved Supplier Relationships
Adopting the Total Cost Model encourages transparent and collaborative relationships with suppliers.
Instead of focusing solely on price negotiations, companies work with suppliers to optimize the entire supply chain.
This partnership approach can lead to innovations, improved delivery times, and better responsiveness to market changes.
Long-term relationships based on trust and mutual benefit are a hallmark of Japanese procurement practices.
Risk Mitigation
The Total Cost Model helps in identifying and mitigating various risks associated with the supply chain.
By analyzing all cost components, companies can anticipate potential disruptions and develop contingency plans.
This proactive approach reduces the impact of unforeseen events, such as supplier bankruptcy or transportation delays.
Effective risk management ensures business continuity and stability.
Disadvantages of the Total Cost Model
Complexity in Implementation
Implementing the Total Cost Model can be complex and time-consuming.
It requires detailed data collection and analysis across multiple departments and processes.
Organizations may need to invest in advanced software and training to effectively manage the model.
The initial setup can be resource-intensive, which may be a barrier for smaller companies.
Data Accuracy and Availability
The effectiveness of the Total Cost Model depends on the accuracy and availability of data.
Incomplete or inaccurate data can lead to flawed cost analyses and suboptimal decision-making.
Gathering comprehensive data from all stages of the supply chain is challenging and requires robust information systems.
Ensuring data integrity is essential for the model to deliver reliable insights.
Resistance to Change
Transitioning to the Total Cost Model may face resistance from employees and stakeholders accustomed to traditional methods.
Change management strategies are necessary to address concerns and facilitate smooth adoption.
Employees need to be educated on the benefits of the model and trained in new processes.
Overcoming resistance is crucial for the successful implementation of the Total Cost Model.
Higher Short-term Costs
While the Total Cost Model can lead to long-term savings, it may involve higher short-term costs.
Investments in new technologies, training, and process improvements require upfront expenditures.
Companies must balance the immediate financial impact with the anticipated future benefits.
Strategic planning and budgeting are essential to manage short-term financial challenges.
Supplier Negotiation Techniques
Building Long-term Relationships
Successful supplier negotiations in the context of the Total Cost Model focus on building long-term relationships.
By fostering trust and mutual respect, companies can collaborate with suppliers to achieve shared goals.
Long-term partnerships enable better coordination, innovation, and flexibility in responding to market demands.
Investing in relationship-building activities, such as regular meetings and joint planning sessions, is essential.
Transparency and Communication
Transparency in communication is vital for effective negotiations under the Total Cost Model.
Companies should openly share their cost analysis and expectations with suppliers.
Clear communication helps in aligning objectives and identifying areas for cost optimization.
Regular updates and honest discussions prevent misunderstandings and facilitate problem-solving.
Value-based Negotiation
Value-based negotiation focuses on the overall value delivered rather than just the price.
This approach considers factors such as quality, reliability, and service levels in addition to cost.
By emphasizing value, companies can negotiate terms that benefit both parties and enhance the total cost effectiveness.
Value-based negotiations lead to more sustainable and equitable agreements.
Collaborative Problem-solving
Adopting a collaborative problem-solving approach during negotiations can yield better results.
Instead of viewing negotiations as adversarial, companies and suppliers work together to overcome challenges.
Jointly exploring solutions to reduce costs and improve efficiency strengthens the partnership.
Collaborative efforts often lead to innovative strategies that benefit both sides.
Current Market Conditions
Global Supply Chain Dynamics
The global supply chain landscape is continually evolving, influenced by factors such as geopolitical tensions, natural disasters, and pandemics.
Japanese manufacturers must navigate these dynamics to maintain cost efficiency and reliability.
Understanding global trends and adapting supply chain strategies accordingly is crucial for success.
Diversification of suppliers and investment in resilient logistics are strategies to mitigate supply chain disruptions.
Technological Advancements
Advancements in technology are transforming procurement and purchasing practices.
Automation, artificial intelligence, and data analytics enhance the ability to manage the Total Cost Model effectively.
Japanese companies are at the forefront of integrating these technologies into their manufacturing processes.
Leveraging technology improves accuracy in cost analysis and enables real-time decision-making.
Sustainability and Environmental Considerations
Sustainability has become a significant factor in procurement decisions.
Japanese manufacturers are increasingly adopting environmentally friendly practices to reduce their total cost impact.
Incorporating sustainability into the Total Cost Model includes evaluating the environmental costs associated with production, transportation, and disposal.
Sustainable procurement not only lowers costs but also enhances corporate reputation and compliance with regulations.
Market Competition
Intense competition in the global market requires Japanese manufacturers to continuously optimize their cost structures.
The Total Cost Model provides a strategic advantage by enabling companies to offer high-quality products at competitive prices.
Staying ahead of competitors involves ongoing assessment and refinement of cost management practices.
Innovation and efficiency are key drivers in maintaining a competitive edge.
Best Practices in Implementing the Total Cost Model
Comprehensive Cost Analysis
A thorough cost analysis is the foundation of the Total Cost Model.
Companies should evaluate all cost components, including direct and indirect costs, to gain a complete understanding of their financial landscape.
This includes not only the purchase price but also costs related to transportation, storage, maintenance, and disposal.
Accurate cost analysis enables informed decision-making and effective cost management.
Integration with Supply Chain Management
Integrating the Total Cost Model with supply chain management ensures that cost considerations are embedded in every aspect of the supply chain.
This holistic approach facilitates coordination between procurement, logistics, production, and quality control.
Effective integration minimizes redundancies and optimizes resource utilization.
Cross-departmental collaboration is essential for seamless implementation.
Leveraging Technology and Data Analytics
Utilizing advanced technologies and data analytics enhances the effectiveness of the Total Cost Model.
Automation tools streamline data collection and processing, reducing the likelihood of errors.
Data analytics provides deeper insights into cost drivers and trends, enabling proactive management.
Investing in technology solutions supports the continuous improvement of cost management practices.
Continuous Improvement and Kaizen
Embracing the philosophy of continuous improvement, or Kaizen, aligns with the principles of the Total Cost Model.
Regularly reviewing and refining cost management processes leads to sustained efficiency gains.
Encouraging employee involvement in identifying cost-saving opportunities fosters a culture of innovation.
Continuous improvement ensures that the Total Cost Model remains effective in a dynamic business environment.
Training and Development
Providing training and development for procurement and purchasing teams is crucial for successful implementation.
Employees should be equipped with the skills and knowledge to perform comprehensive cost analyses and manage supplier relationships effectively.
Ongoing education ensures that teams are up-to-date with the latest best practices and technological advancements.
Investing in human capital enhances the overall effectiveness of the Total Cost Model.
Conclusion
The Total Cost Model is a powerful tool that has significantly contributed to the success of Japanese manufacturing.
By adopting a holistic approach to cost management, companies can achieve greater efficiency, higher quality, and stronger supplier relationships.
While implementing the model presents challenges, such as complexity and the need for accurate data, the long-term benefits far outweigh the initial hurdles.
Effective supplier negotiation techniques, an understanding of current market conditions, and adherence to best practices are essential for maximizing the advantages of the Total Cost Model.
Japanese manufacturers demonstrate that with strategic planning and a commitment to continuous improvement, the Total Cost Model can be a secret weapon in achieving manufacturing excellence and sustained competitive advantage.
資料ダウンロード
QCD調達購買管理クラウド「newji」は、調達購買部門で必要なQCD管理全てを備えた、現場特化型兼クラウド型の今世紀最高の購買管理システムとなります。
ユーザー登録
調達購買業務の効率化だけでなく、システムを導入することで、コスト削減や製品・資材のステータス可視化のほか、属人化していた購買情報の共有化による内部不正防止や統制にも役立ちます。
NEWJI DX
製造業に特化したデジタルトランスフォーメーション(DX)の実現を目指す請負開発型のコンサルティングサービスです。AI、iPaaS、および先端の技術を駆使して、製造プロセスの効率化、業務効率化、チームワーク強化、コスト削減、品質向上を実現します。このサービスは、製造業の課題を深く理解し、それに対する最適なデジタルソリューションを提供することで、企業が持続的な成長とイノベーションを達成できるようサポートします。
オンライン講座
製造業、主に購買・調達部門にお勤めの方々に向けた情報を配信しております。
新任の方やベテランの方、管理職を対象とした幅広いコンテンツをご用意しております。
お問い合わせ
コストダウンが利益に直結する術だと理解していても、なかなか前に進めることができない状況。そんな時は、newjiのコストダウン自動化機能で大きく利益貢献しよう!
(Β版非公開)