- お役立ち記事
- The basics of creating and operating QC process charts that new employees in the manufacturing operations department should know.
月間76,176名の
製造業ご担当者様が閲覧しています*
*2025年3月31日現在のGoogle Analyticsのデータより
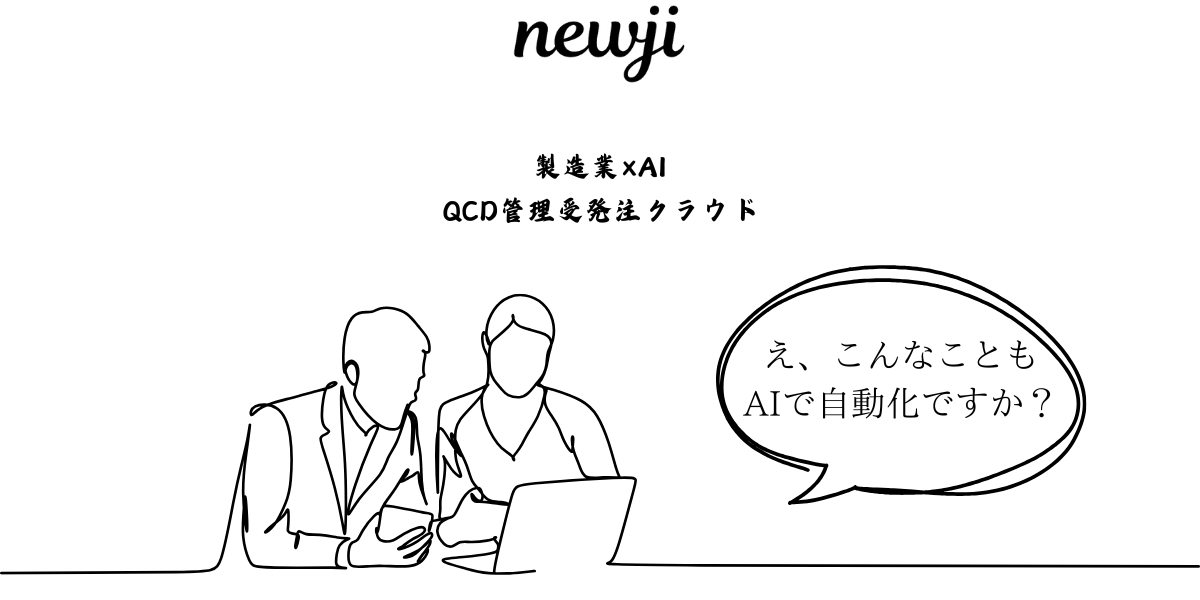
The basics of creating and operating QC process charts that new employees in the manufacturing operations department should know.
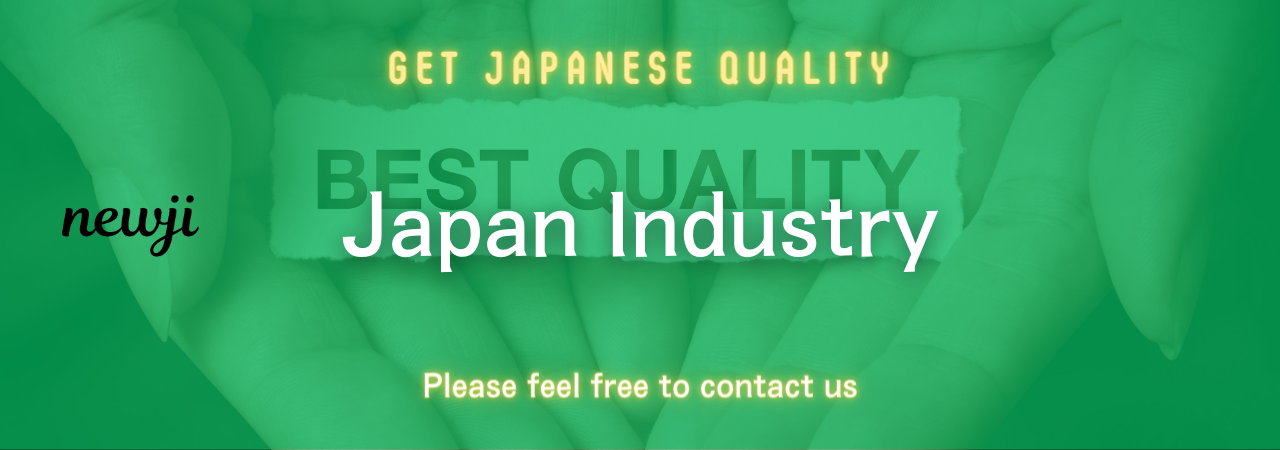
目次
Understanding QC Process Charts
Quality Control (QC) process charts are vital tools in the manufacturing industry.
They help monitor, control, and improve quality control processes.
For new employees in the manufacturing operations department, grasping the fundamentals of QC process charts is essential.
These charts ensure that products meet required standards and help identify any variations in the manufacturing process.
QC process charts work by plotting data over time.
They give insights into the performance of the production process and highlight any inconsistencies.
Familiarity with these charts is crucial to maintaining the quality of products, reducing waste, and increasing productivity.
Let’s delve into the basics of creating and operating QC process charts.
Types of QC Process Charts
There are several types of QC process charts, each serving different purposes.
The common ones include:
1. **Control Charts**: These charts track the performance of processes over time by displaying data points.
Control charts can help identify trends, shifts, or cycles, allowing for timely corrective actions.
2. **Histogram**: This is a graphical representation showing the distribution of data points.
It helps understand the frequency of different values within a dataset, making it easier to see patterns.
3. **Pareto Chart**: This chart is used to identify the most significant factors in a dataset.
It prioritizes issues so that teams can address the most critical ones first, fostering effective problem-solving.
4. **Scatter Diagram**: This type of chart displays the relationship between two variables.
It helps determine whether changes in one variable correlate with changes in another, thus identifying cause-and-effect relationships.
Steps to Create QC Process Charts
Creating a QC process chart involves several essential steps.
Step 1: Define the Objective
Before creating a QC process chart, it’s important to define its purpose.
Clearly understanding what you intend to achieve, whether it’s monitoring process stability, identifying variation, or improving product quality, will guide the entire process.
Step 2: Collect Data
Data collection is a critical step in creating an effective QC process chart.
Gather accurate and reliable data, ensuring that it represents the process under normal operating conditions.
The data could be from observations, measurements, or various checkpoints within the production process.
Step 3: Choose the Right Chart
Selecting the appropriate chart depends on the specific purpose and type of data available.
For instance, if you need to observe the process over time, a control chart is ideal.
If you want to analyze the distribution of data or prioritize problems, a histogram or Pareto chart would be more suitable.
Step 4: Plot the Data
With data in hand and the appropriate chart type chosen, it’s time to plot the data points on the chart.
Ensure accuracy in plotting to reflect the true nature of the dataset.
This visual representation will help identify trends or outliers and allow for immediate analysis.
Step 5: Analyze the Chart
Interpreting the information displayed on the QC process chart is critical.
Look for any patterns, trends, or deviations from expected norms.
Analysis should involve identifying whether the process is stable and within control limits or if any corrective actions are needed.
Step 6: Take Corrective Action
Once analysis has revealed any issues or areas for improvement, the next step is to take corrective actions.
This could involve adjusting the process, recalibrating equipment, or retraining staff to ensure quality standards are met.
Tips for Effective Operation of QC Process Charts
To maximize the benefits of QC process charts, keep the following tips in mind:
Regular Monitoring
Regularly update and monitor the QC process charts to capture any significant variations or trends.
Consistent monitoring will allow for timely interventions and continuous process improvements.
Continuous Improvement
Encourage a culture of continuous improvement where feedback from the QC process charts is utilized to enhance production processes.
This proactive approach can lead to increased efficiency and improved product quality.
Collaboration and Communication
Facilitate open communication and collaboration among team members when analyzing QC process charts.
Sharing insights and discussing potential solutions can lead to more effective decision-making and improved outcomes.
Conclusion
QC process charts are indispensable tools in maintaining and improving quality in the manufacturing industry.
For new employees in the manufacturing operations department, understanding these charts is crucial for ensuring the production of top-quality products.
By learning to create, analyze, and act on insights from QC process charts, they can contribute significantly to their organization’s success.
Armed with this knowledge, they are well-prepared to tackle quality control challenges and drive process improvements.
Remember, regular monitoring, collaboration, and a commitment to continuous improvement are key to leveraging the full potential of QC process charts.
資料ダウンロード
QCD管理受発注クラウド「newji」は、受発注部門で必要なQCD管理全てを備えた、現場特化型兼クラウド型の今世紀最高の受発注管理システムとなります。
ユーザー登録
受発注業務の効率化だけでなく、システムを導入することで、コスト削減や製品・資材のステータス可視化のほか、属人化していた受発注情報の共有化による内部不正防止や統制にも役立ちます。
NEWJI DX
製造業に特化したデジタルトランスフォーメーション(DX)の実現を目指す請負開発型のコンサルティングサービスです。AI、iPaaS、および先端の技術を駆使して、製造プロセスの効率化、業務効率化、チームワーク強化、コスト削減、品質向上を実現します。このサービスは、製造業の課題を深く理解し、それに対する最適なデジタルソリューションを提供することで、企業が持続的な成長とイノベーションを達成できるようサポートします。
製造業ニュース解説
製造業、主に購買・調達部門にお勤めの方々に向けた情報を配信しております。
新任の方やベテランの方、管理職を対象とした幅広いコンテンツをご用意しております。
お問い合わせ
コストダウンが利益に直結する術だと理解していても、なかなか前に進めることができない状況。そんな時は、newjiのコストダウン自動化機能で大きく利益貢献しよう!
(β版非公開)