- お役立ち記事
- For mid-level employees in the equipment technology department! Safety design method and checklist for risk reduction
For mid-level employees in the equipment technology department! Safety design method and checklist for risk reduction
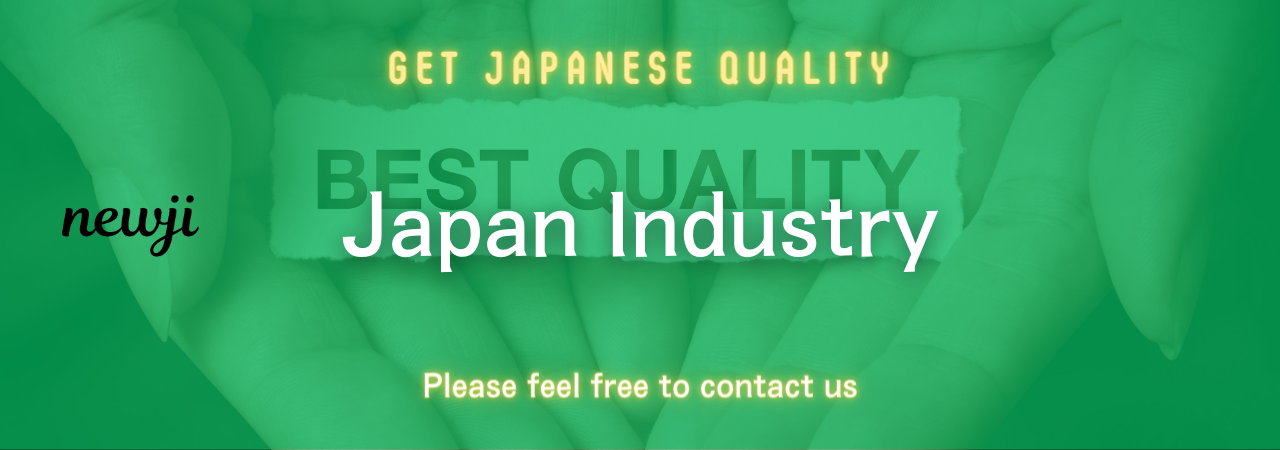
目次
Understanding Safety in Equipment Technology
Safety is a critical aspect in the field of equipment technology, especially for those at the mid-level of their careers.
The responsibility of ensuring that equipment is safe for use falls heavily on the shoulders of mid-level employees.
Implementing a robust safety design can significantly minimize risks, ensuring a safer working environment for everyone involved.
The approach to safety should be integral from the design phase, which is why understanding safety design methods and having a comprehensive checklist is essential for reducing risks.
The Importance of Safety Design
Safety design is fundamentally about predicting what could go wrong and taking proactive steps to prevent any issues from arising.
It requires detailed analysis and understanding of the equipment’s functionality, its environment, and the people interacting with it.
A safe design not only protects employees and extends equipment lifespan but also complies with legal and regulatory standards, which can potentially save on costs related to potential litigation or fines from non-compliance.
Key Safety Design Methods
Several methods can be employed to ensure safety in equipment technology.
Understanding and implementing these methods will make a significant difference in managing risk effectively.
1. Hazard Identification and Risk Assessment (HIRA)
HIRA is a fundamental method where potential hazards are identified, and the risks associated with these hazards are assessed.
This involves thoroughly analyzing the equipment’s design and operation.
Assessment helps in understanding where, when, and how safety might be compromised.
2. Failure Mode and Effects Analysis (FMEA)
FMEA is a structured approach that examines possible failure modes within a system.
By studying the consequences of these failures, mid-level employees can prioritize actions to mitigate risks.
The goal of FMEA is to prevent failures before they occur, thereby improving overall reliability and safety.
3. Safety Integrity Level (SIL)
SIL is a measurement of performance required for a safety instrumented function.
Understanding SIL can help determine the level of risk reduction necessary to meet safety requirements.
By applying SIL, companies can ensure that they have the right measures in place to protect against safety incidents.
4. Design For Safety (DFS)
Design for Safety involves integrating safety principles into the design process right from the start.
This approach ensures that safety is not an afterthought but a primary consideration throughout the design and development stages.
DFS encourages designers to think about how their designs could potentially pose risks and how to mitigate these risks effectively.
Creating a Safety Checklist
A well-structured safety checklist can serve as a useful tool to ensure that nothing is overlooked in the safety design and assessment processes.
1. Identify Hazards
Start by identifying all potential hazards associated with the equipment.
Consider various scenarios and operations where risks might be present.
2. Risk Evaluation
Evaluate the potential impact and likelihood of each identified hazard.
Determine the severity of potential failures and prioritize them for mitigation.
3. Implement Controls
Develop and implement control measures to mitigate identified risks.
Controls could include safety features, training, personal protective equipment, or operational procedures.
4. Regularly Review and Update
Safety is not a one-time activity but requires continuous attention.
Regularly review and update the safety design and checklist as new risks are identified or as further improvements in safety measures are developed.
Promoting a Culture of Safety
Promoting a culture of safety within the organization is as crucial as having technical safety measures in place.
1. Training and Education
Regular training sessions and workshops can help keep employees up-to-date on safety protocols and best practices.
This continuous education fosters an environment where safety is a priority.
2. Encouraging Reporting
Encourage a workplace culture where employees feel comfortable reporting potential risks without fear of reprisal.
Creating a non-punitive reporting system can lead to the early identification of risks.
3. Leadership Commitment
Commitment from leadership is essential in promoting safety culture.
When leaders prioritize safety, it sends a strong message throughout the organization about its importance.
Conclusion
Mid-level employees play a pivotal role in ensuring equipment safety through effective safety design methods and comprehensive checklists.
By understanding and applying safety design principles and fostering a culture committed to risk reduction, equipment technology departments can help ensure safer and more compliant operations.
Regular updates and training, tied to a strong management commitment, will ensure ongoing improvements in safety.
By taking these steps, mid-level employees can create a safer, more efficient work environment that protects everyone involved.
資料ダウンロード
QCD調達購買管理クラウド「newji」は、調達購買部門で必要なQCD管理全てを備えた、現場特化型兼クラウド型の今世紀最高の購買管理システムとなります。
ユーザー登録
調達購買業務の効率化だけでなく、システムを導入することで、コスト削減や製品・資材のステータス可視化のほか、属人化していた購買情報の共有化による内部不正防止や統制にも役立ちます。
NEWJI DX
製造業に特化したデジタルトランスフォーメーション(DX)の実現を目指す請負開発型のコンサルティングサービスです。AI、iPaaS、および先端の技術を駆使して、製造プロセスの効率化、業務効率化、チームワーク強化、コスト削減、品質向上を実現します。このサービスは、製造業の課題を深く理解し、それに対する最適なデジタルソリューションを提供することで、企業が持続的な成長とイノベーションを達成できるようサポートします。
オンライン講座
製造業、主に購買・調達部門にお勤めの方々に向けた情報を配信しております。
新任の方やベテランの方、管理職を対象とした幅広いコンテンツをご用意しております。
お問い合わせ
コストダウンが利益に直結する術だと理解していても、なかなか前に進めることができない状況。そんな時は、newjiのコストダウン自動化機能で大きく利益貢献しよう!
(Β版非公開)