- お役立ち記事
- Supply chain risk assessment and countermeasures that new employees in the purchasing management department should know
Supply chain risk assessment and countermeasures that new employees in the purchasing management department should know
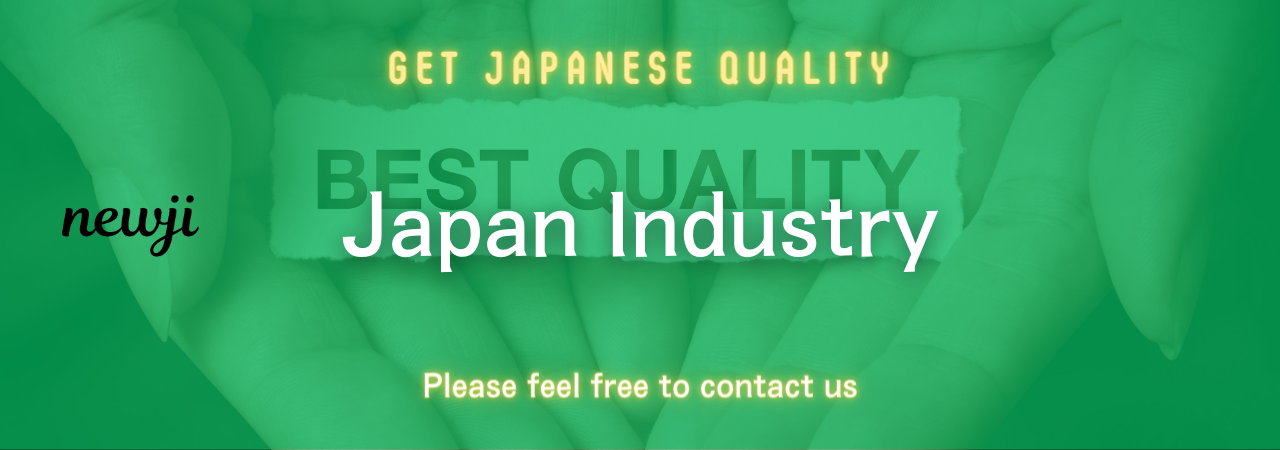
目次
Understanding the Basics of Supply Chain Risk
When you join the purchasing management department, you’ll quickly realize that managing a supply chain is not just about making sure materials are available when needed.
It’s also about identifying and mitigating potential risks that could disrupt the flow of goods and services.
Supply chain risk assessment involves evaluating the vulnerabilities within the supply chain, from supplier operations to transportation logistics.
These risks can stem from various sources, including natural disasters, supplier failures, political instability, and even cyber-attacks.
New employees need to understand that every link in the supply chain is interconnected, and a disruption in one area can have a domino effect on the entire process.
Thus, a comprehensive risk assessment is key to maintaining a smooth and efficient supply chain.
Types of Supply Chain Risks
Operational Risks
Operational risks are related to the everyday functioning of the supply chain.
These include delays in production, machinery breakdowns, and human errors.
For instance, if a key component of a product is damaged during transit, it can delay the entire production schedule.
Understanding these risks helps in finding reliable suppliers and creating contingency plans.
Financial Risks
Financial risks involve changes in market conditions such as currency fluctuations, changes in interest rates, or economic downturns that can impact the cost of goods.
Purchasing managers need to stay updated with global economic trends and work closely with financial analysts to mitigate these risks through hedging strategies or flexible contracts.
Environmental and Natural Disasters
Natural disasters like earthquakes, floods, or hurricanes can severely disrupt supply chains, especially for companies reliant on specific geographic regions.
Environmental risks also include compliance with environmental regulations and sustainability practices.
It’s crucial for new employees to be aware of climate-related risks and to work on sourcing strategies that diversify supplier locations.
Cybersecurity Risks
In today’s digital age, supply chains are heavily dependent on information technology for operations.
This dependence makes them vulnerable to cyber-attacks that can compromise sensitive data and disrupt operations.
New employees should understand the importance of data protection measures and work with IT specialists to ensure systems are robust and secure.
Conducting a Supply Chain Risk Assessment
Performing a thorough supply chain risk assessment is essential for identifying potential vulnerabilities.
Here are the steps new employees in the purchasing management department should follow:
Identify Potential Risks
Start by mapping out each step of the supply chain process, from raw material acquisition to product delivery.
Identify where risks may arise and classify them according to their nature—operational, financial, environmental, or cybersecurity.
Evaluate Risk Impact
Once risks are identified, analyze the impact each risk could have on the supply chain.
Consider factors such as the financial cost of a disruption, the potential for damage to reputation, and the time it would take to recover.
Determine Risk Likelihood
Assess the likelihood of each risk occurring.
This includes considering historical data, current market conditions, and potential future changes in the business environment.
This step involves a fair amount of prediction, but it provides a clear picture of which risks require immediate attention.
Prioritize Risks
Based on the impact and likelihood of each risk, prioritize them to focus attention and resources on managing the most critical threats first.
This step ensures efficient use of time and resources in mitigating supply chain risks.
Countermeasures to Mitigate Supply Chain Risks
Once risks have been assessed and prioritized, the next step is to implement countermeasures.
Develop Strong Supplier Relationships
Cultivating close relationships with suppliers can provide early warning of potential disruptions and create opportunities to negotiate better terms.
It also fosters trust, making it easier to resolve issues quickly when they arise.
Diversify Suppliers and Resources
Relying on a single supplier or geographic location exposes the supply chain to significant risk.
By diversifying suppliers and sourcing locations, companies can better withstand disruptions in one area.
Implement Technology Solutions
Leverage technology to improve visibility and control over the supply chain.
For example, using advanced analytics can provide real-time insights into supply chain operations, while automated systems can enhance efficiency and reduce human error.
Build a Responsive Supply Chain
Creating a responsive supply chain involves planning for rapid adjustments to supply chain processes in response to unforeseen events.
This includes maintaining a level of flexibility in contracts and inventory management practices to adapt quickly.
Emergency Planning and Training
Regularly conduct emergency drills and training for your team to ensure they know the procedures to follow in case of a disruption.
Having a well-prepared response team can minimize downtime and losses during supply chain disruptions.
Conclusion
For new employees in the purchasing management department, understanding supply chain risk assessment and countermeasures is crucial.
By identifying potential risks, evaluating their impact and likelihood, and implementing effective countermeasures, you can contribute to a resilient and efficient supply chain.
This proactive approach ensures that your company is prepared to face any challenges that may arise, safeguarding its operations and enhancing its competitive edge.
資料ダウンロード
QCD調達購買管理クラウド「newji」は、調達購買部門で必要なQCD管理全てを備えた、現場特化型兼クラウド型の今世紀最高の購買管理システムとなります。
ユーザー登録
調達購買業務の効率化だけでなく、システムを導入することで、コスト削減や製品・資材のステータス可視化のほか、属人化していた購買情報の共有化による内部不正防止や統制にも役立ちます。
NEWJI DX
製造業に特化したデジタルトランスフォーメーション(DX)の実現を目指す請負開発型のコンサルティングサービスです。AI、iPaaS、および先端の技術を駆使して、製造プロセスの効率化、業務効率化、チームワーク強化、コスト削減、品質向上を実現します。このサービスは、製造業の課題を深く理解し、それに対する最適なデジタルソリューションを提供することで、企業が持続的な成長とイノベーションを達成できるようサポートします。
オンライン講座
製造業、主に購買・調達部門にお勤めの方々に向けた情報を配信しております。
新任の方やベテランの方、管理職を対象とした幅広いコンテンツをご用意しております。
お問い合わせ
コストダウンが利益に直結する術だと理解していても、なかなか前に進めることができない状況。そんな時は、newjiのコストダウン自動化機能で大きく利益貢献しよう!
(Β版非公開)