- お役立ち記事
- New leaders of product quality control departments should learn how to effectively conduct why-why analysis.
New leaders of product quality control departments should learn how to effectively conduct why-why analysis.
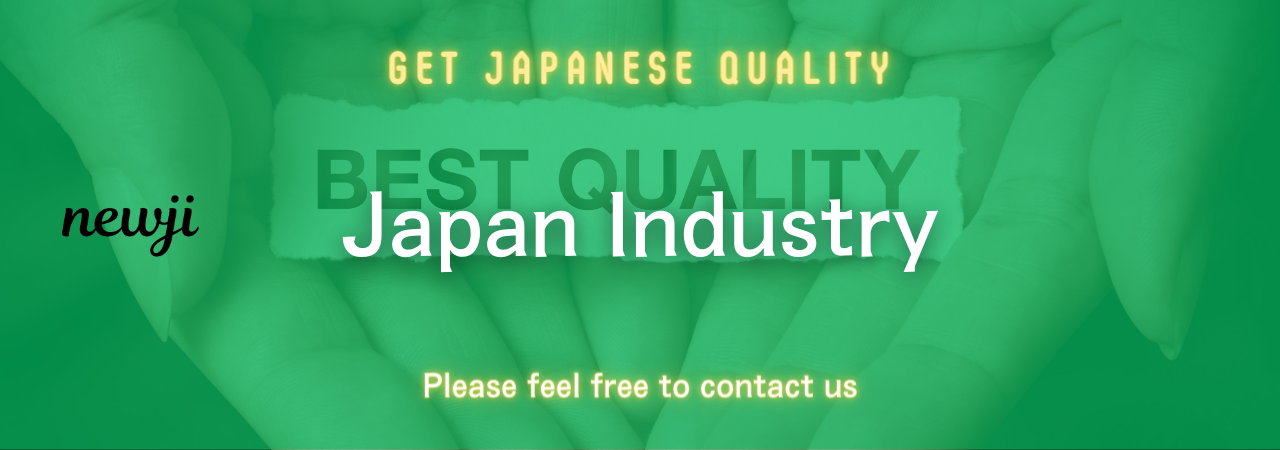
目次
Understanding the Why-Why Analysis
The Why-Why Analysis is a systematic approach to uncover the root cause of a problem.
It involves asking a series of “why” questions to peel back the layers of symptoms and reach the core issue.
New leaders in product quality control departments will find this method invaluable, as it helps identify the underlying reasons for failures or deviations in product quality.
It ensures that solutions are directed at the source of the problem rather than its manifestations, leading to more effective problem resolution and prevention.
Importance of Why-Why Analysis for Quality Control
In quality control, identifying the root cause of issues is critical to maintaining high standards.
By understanding what causes defects or failures, leaders can implement corrective actions that not only solve the current problem but also prevent future occurrences.
This approach leads to continuous improvement, enhancing product reliability and increasing customer satisfaction.
The Why-Why Analysis fosters a culture of inquiry and learning within the department, encouraging team members to critically evaluate processes and their outcomes.
The Five Whys Technique
A popular form of Why-Why Analysis is the Five Whys technique.
This method involves asking “why” up to five times or until the root cause is identified.
The number five isn’t rigid; it serves as a guideline to ensure in-depth exploration of the problem.
By repeatedly questioning why a problem occurs, teams can move beyond surface-level explanations and discover deeper, systemic issues.
Benefits of Using Why-Why Analysis
The Why-Why Analysis offers several benefits to new leaders in quality control departments.
Firstly, it promotes a structured way of thinking that enhances problem-solving skills.
Secondly, it allows for thorough investigations without requiring specialized tools, making it accessible and easy to implement.
Lastly, it builds a collaborative environment where team members can contribute to identifying and resolving issues.
Steps to Conduct an Effective Why-Why Analysis
Conducting a successful Why-Why Analysis involves several steps.
Let’s explore these steps to ensure new leaders can effectively implement this method in their departments.
Step 1: Define the Problem
Clearly articulate the problem or issue at hand.
This step is crucial because a well-defined problem lays the foundation for fruitful inquiry.
The problem statement should be specific and measurable, providing a clear target for the analysis.
Step 2: Assemble the Team
Bring together a diverse team with different perspectives and expertise related to the problem.
Involving multiple viewpoints can lead to more comprehensive insights and innovative solutions.
Encourage open communication and active participation among team members.
Step 3: Ask the First “Why”
Identify the immediate reason for the problem by asking, “Why did this happen?”
Document the response and ensure everyone in the team agrees on this answer.
It’s essential to dig deep and avoid settling on superficial responses.
Step 4: Continue Asking “Why”
For each subsequent answer, ask another “why” to delve deeper into the issue.
Continue this process until you uncover the root cause.
Remember, reaching the root cause may take fewer or more than five “whys.”
Step 5: Validate the Findings
Once the root cause is identified, validate your findings.
This involves checking if the root cause, if addressed, would prevent the problem from occurring again.
Engage the team to ensure the conclusions are logical and evidence-based.
Step 6: Develop a Corrective Action Plan
Based on the validated root cause, devise a corrective action plan.
Ensure the plan addresses the root cause thoroughly and includes measures to prevent future occurrences.
Clearly assign responsibilities and timelines for implementing the solution.
Step 7: Implement and Monitor the Solution
Put the corrective action plan into action.
Monitor its effectiveness by evaluating if the problem has been resolved and if processes have improved.
Make adjustments as necessary to ensure the solution’s success and sustainability.
Challenges and Tips for New Leaders
While the Why-Why Analysis is a powerful tool, new leaders may face challenges in its implementation.
Awareness of these challenges and employing strategic tips can help overcome obstacles.
Challenge: Jumping to Conclusions
A common challenge is the tendency to jump to conclusions without thorough investigation.
Encourage your team to resist assumptions and focus on evidence-based analysis.
Facilitate discussions that promote deeper inquiry and reflection.
Challenge: Ineffective Communication
Ineffective communication can hinder the analysis process.
Ensure clear communication by setting guidelines for discussions and encouraging active listening.
Document findings and decisions to provide a reference point and maintain team alignment.
Tip: Foster a Culture of Continuous Improvement
Cultivate a culture that values continuous improvement and problem-solving.
Encourage your team to regularly use Why-Why Analysis to understand issues and drive improvements.
Recognize and celebrate successes to motivate further innovations.
Tip: Provide Training and Resources
Ensure your team members are trained in the Why-Why Analysis method.
Provide resources and tools that facilitate effective analysis.
Encourage learning and development to enhance problem-solving capabilities.
Conclusion
For new leaders in product quality control departments, mastering the Why-Why Analysis is essential for effective problem-solving.
By understanding and addressing root causes, leaders can drive continuous improvement, enhance product reliability, and increase customer satisfaction.
Although challenges may arise, fostering a culture of inquiry, providing necessary training, and encouraging collaboration will enable successful implementation of this method.
Investing time and effort into Why-Why Analysis not only strengthens the department’s operations but also contributes to the overall success of the organization.
資料ダウンロード
QCD調達購買管理クラウド「newji」は、調達購買部門で必要なQCD管理全てを備えた、現場特化型兼クラウド型の今世紀最高の購買管理システムとなります。
ユーザー登録
調達購買業務の効率化だけでなく、システムを導入することで、コスト削減や製品・資材のステータス可視化のほか、属人化していた購買情報の共有化による内部不正防止や統制にも役立ちます。
NEWJI DX
製造業に特化したデジタルトランスフォーメーション(DX)の実現を目指す請負開発型のコンサルティングサービスです。AI、iPaaS、および先端の技術を駆使して、製造プロセスの効率化、業務効率化、チームワーク強化、コスト削減、品質向上を実現します。このサービスは、製造業の課題を深く理解し、それに対する最適なデジタルソリューションを提供することで、企業が持続的な成長とイノベーションを達成できるようサポートします。
オンライン講座
製造業、主に購買・調達部門にお勤めの方々に向けた情報を配信しております。
新任の方やベテランの方、管理職を対象とした幅広いコンテンツをご用意しております。
お問い合わせ
コストダウンが利益に直結する術だと理解していても、なかなか前に進めることができない状況。そんな時は、newjiのコストダウン自動化機能で大きく利益貢献しよう!
(Β版非公開)