- お役立ち記事
- New surface treatment technologies that the metal materials technology department should work on and their benefits
New surface treatment technologies that the metal materials technology department should work on and their benefits
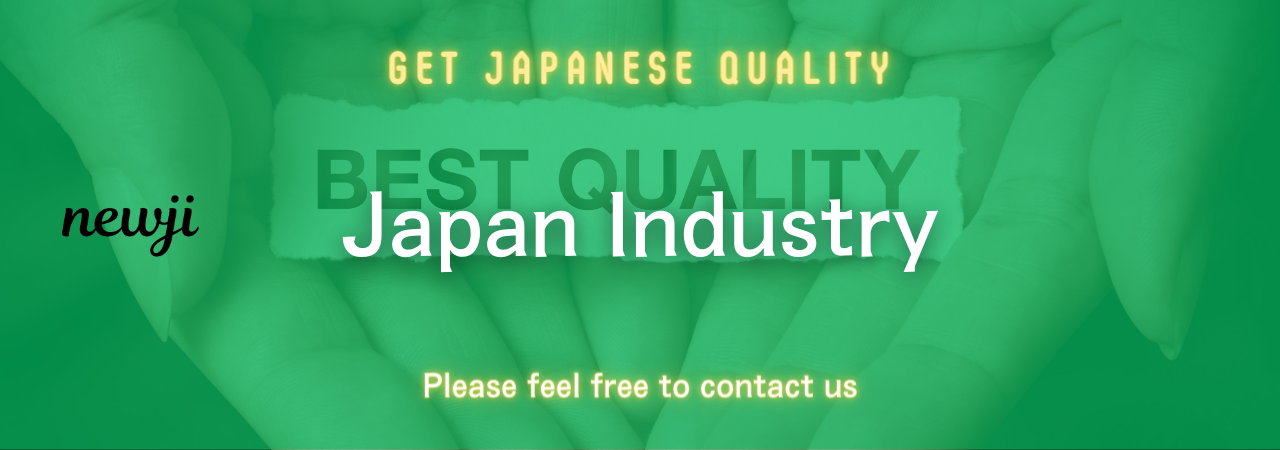
目次
Introduction to Surface Treatment Technologies
Surface treatment technologies play a significant role in enhancing the properties of metal materials, such as their resistance to corrosion, wear, and environmental effects.
These technologies offer an array of benefits, including improved durability, aesthetic appeal, and functionality.
For departments focused on metal materials technology, understanding and adopting new surface treatment technologies is essential.
In this article, we will explore some emerging surface treatment technologies that are worth considering and discuss the benefits they can provide.
Nanostructured Coatings
Nanostructured coatings represent a cutting-edge approach in surface treatment, offering enhanced performance due to their unique properties.
These coatings involve the application of materials with nanoscale structures onto the surface of metals.
One major advantage of nanostructured coatings is their ability to drastically improve the hardness and wear resistance of metal surfaces.
The nanoscale features increase the surface area and improve the bond between the coating and the substrate, resulting in enhanced durability.
Additionally, nanostructured coatings can impart unique properties such as self-cleaning or anti-bacterial effects.
This makes them ideal for applications in various industries, including medical devices, consumer electronics, and automotive components.
Thermal Spray Coatings
Thermal spray coatings involve the application of a coating material onto a substrate through the use of high-temperature processes.
This technique is highly versatile and can be used to apply a wide range of materials, from metals and ceramics to alloys and composites.
Thermal spray coatings offer excellent adhesion and can be applied quickly, which makes them suitable for large-scale industrial applications.
One of the primary benefits of thermal spray coatings is their ability to protect metal surfaces from corrosion and wear.
By applying a corrosion-resistant layer, these coatings can extend the lifespan of metal components, reducing the need for frequent replacements.
In industries where equipment operates under harsh conditions, thermal spray coatings can prove to be highly cost-effective and efficient.
Applications and Benefits
Thermal spray coatings are commonly used in the aerospace, automotive, and oil and gas industries.
They protect against environmental factors, harsh chemicals, and mechanical abrasion.
By improving resistance to extreme conditions, thermal spray coatings enhance the performance and reliability of components like turbine blades, pistons, and pipelines.
Physical Vapor Deposition (PVD)
Physical Vapor Deposition, or PVD, is a vacuum-based process that deposits thin films onto metal substrates.
This technology offers a range of advantages, including the ability to create coatings with precise thickness control and homogenous distribution.
PVD coatings are known for their excellent adhesion and robustness, which makes them highly desirable for applications requiring high wear resistance and thermal stability.
PVD coatings can significantly improve the functionality and appearance of metal surfaces.
They can be engineered to provide specific colors and finishes, adding value to consumer products like watches, jewelry, and electronic devices.
Moreover, PVD coatings offer excellent resistance to corrosion and oxidation, making them suitable for both decorative and protective purposes.
Chemical Vapor Deposition (CVD)
Chemical Vapor Deposition, or CVD, involves depositing a solid material onto a substrate from a gaseous state.
This surface treatment method is widely used to apply coatings that require high precision and uniform thickness.
CVD coatings are renowned for their ability to enhance thermal and chemical stability, making them ideal for applications in high-temperature environments.
One significant benefit of CVD is its capability to produce coatings with outstanding hardness and wear resistance.
Tools and components used in the mining and machining industries often benefit greatly from CVD coatings, as they help extend the operational life of tools and reduce maintenance costs.
Advantages for Various Industries
CVD coatings are particularly beneficial in the semiconductor industry, where they are used to fabricate microelectronics and integrated circuits.
The technology enables the creation of thin films with exceptional purity, essential for maintaining the performance and efficiency of electronic devices.
Anodizing
Anodizing is an electrochemical surface treatment process that increases the natural oxide layer on metal surfaces, typically aluminum.
This process enhances resistance to wear and corrosion while providing a decorative finish that can be dyed in various colors.
Anodizing is particularly valued for its ability to strengthen surfaces without adding significant weight.
The anodizing process is used extensively in the aerospace and architectural industries.
For instance, anodized aluminum parts in aircraft can withstand adverse environmental conditions, including exposure to temperature extremes and humidity.
Furthermore, in architectural applications, anodizing provides aesthetically pleasing finishes and long-lasting color stability, reducing maintenance costs.
Plasma Electrolytic Oxidation (PEO)
Plasma Electrolytic Oxidation, also known as micro-arc oxidation, is an advanced surface treatment that converts the substrate’s surface into a ceramic oxide layer.
This process creates a coating with exceptional hardness, wear resistance, and environmental protection.
PEO is often used to treat lightweight metals like aluminum, magnesium, and titanium, which are prevalent in automotive and aerospace industries.
One notable advantage of PEO is its ability to create multi-functional coatings, offering properties like electrical insulation, thermal barrier protection, and increased fatigue resistance.
Components coated with PEO experience an extended service life and reduced environmental impact due to less frequent replacements and repairs.
Conclusion
Incorporating new surface treatment technologies presents substantial opportunities for enhancing the properties and longevity of metal materials in various industries.
Whether it’s achieving superior wear resistance through nanostructured coatings or improving corrosion protection with thermal spray coatings, these technologies offer measurable benefits.
By adopting these advanced surface treatments, the metal materials technology department can lead the way in producing components that stand the test of time, performing reliably under diverse conditions.
Each technology offers unique advantages and applications, underscoring the importance of selecting the right surface treatment in alignment with specific requirements and industry standards.
As innovations continue to emerge in the field of surface treatments, staying informed and adaptable will ensure continued success and innovation in metal materials technology.
資料ダウンロード
QCD調達購買管理クラウド「newji」は、調達購買部門で必要なQCD管理全てを備えた、現場特化型兼クラウド型の今世紀最高の購買管理システムとなります。
ユーザー登録
調達購買業務の効率化だけでなく、システムを導入することで、コスト削減や製品・資材のステータス可視化のほか、属人化していた購買情報の共有化による内部不正防止や統制にも役立ちます。
NEWJI DX
製造業に特化したデジタルトランスフォーメーション(DX)の実現を目指す請負開発型のコンサルティングサービスです。AI、iPaaS、および先端の技術を駆使して、製造プロセスの効率化、業務効率化、チームワーク強化、コスト削減、品質向上を実現します。このサービスは、製造業の課題を深く理解し、それに対する最適なデジタルソリューションを提供することで、企業が持続的な成長とイノベーションを達成できるようサポートします。
オンライン講座
製造業、主に購買・調達部門にお勤めの方々に向けた情報を配信しております。
新任の方やベテランの方、管理職を対象とした幅広いコンテンツをご用意しております。
お問い合わせ
コストダウンが利益に直結する術だと理解していても、なかなか前に進めることができない状況。そんな時は、newjiのコストダウン自動化機能で大きく利益貢献しよう!
(Β版非公開)