- お役立ち記事
- A must-see for new employees in the production management department! Basics of 5S activities and continuous improvement approach
A must-see for new employees in the production management department! Basics of 5S activities and continuous improvement approach
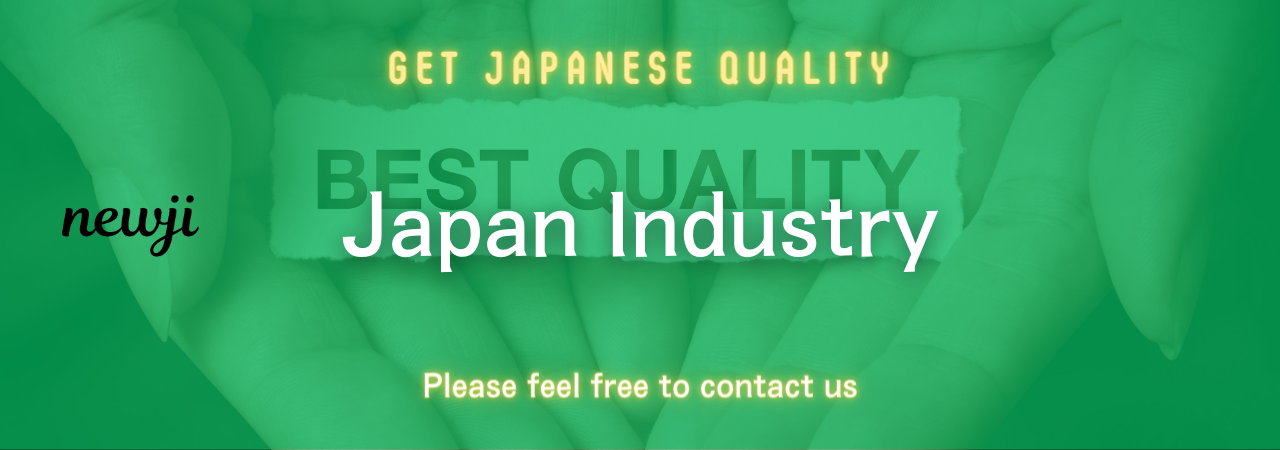
目次
Understanding 5S Activities
For new employees in the production management department, grasping the fundamentals of 5S activities is essential.
5S is a system derived from five Japanese words that describe various steps of the organizational process.
These are seiri (sort), seiton (set in order), seiso (shine), seiketsu (standardize), and shitsuke (sustain).
The goal of 5S is to create and maintain an organized, clean, and efficient workplace.
This not only improves productivity but also enhances safety and employee morale.
By implementing 5S, companies can significantly reduce waste, streamline operations, and maintain high standards of quality and efficiency.
Seiri: Sorting for Success
The first step in 5S activities is seiri, which translates to “sort” in English.
During this stage, employees should go through all tools, equipment, and materials in the workplace and identify which are essential to daily operations.
Unnecessary items should be removed, and necessary items should be stored in a way that makes them easily accessible.
Sorting helps eliminate clutter and ensures that essential tools and materials are readily available when needed.
This step lays the foundation for all the following steps by creating a more organized work environment.
Seiton: Set in Order
After sorting comes seiton, or “set in order.”
This step involves organizing the remaining items in the workplace so they are easy to find and use.
Tools and materials should be arranged in a logical manner, with frequently used items placed where they can be reached quickly.
Seiton helps reduce the amount of time spent searching for tools and materials, leading to increased productivity.
Additionally, an orderly workplace reduces the risk of accidents and errors, contributing to a safer and more efficient work environment.
Seiso: Shine and Clean
The seiso, or “shine” step, emphasizes cleanliness and maintenance.
Employees should routinely clean their workspaces and equipment, keeping them in good condition.
Regular cleaning helps prevent the buildup of dirt and debris, which can lead to equipment malfunctions and workplace hazards.
A clean workplace not only promotes safety but also improves morale.
When employees take pride in their workspace, it leads to a more positive and productive atmosphere.
Seiketsu: Standardize Practices
The fourth step, seiketsu, means “standardize.”
This involves creating consistent methods and procedures for maintaining organization and cleanliness across the workplace.
Clearly defined processes ensure that everyone follows the same standards, reducing confusion and inconsistency.
By standardizing practices, companies can create a culture of efficiency and uniformity, making it easier to train new employees and maintain high standards over time.
Shitsuke: Sustain Improvements
The final step in 5S activities is shitsuke, or “sustain.”
This step focuses on maintaining the improvements achieved through the 5S process.
It requires ongoing training, communication, and reinforcement to ensure that employees continue to follow established procedures.
Sustaining 5S activities is crucial for long-term success.
Regular audits and reviews can help identify areas where improvements are needed and reinforce the importance of these practices.
The Continuous Improvement Approach
Alongside 5S activities, the concept of continuous improvement, often referred to as kaizen, plays a vital role in production management.
Kaizen is a Japanese term meaning “change for better,” and it emphasizes the ongoing effort to improve processes, products, and services.
Continuous improvement involves everyone in the organization, from top management to frontline employees, in the pursuit of incremental changes that enhance efficiency and quality.
The Principles of Kaizen
Kaizen is based on several key principles.
First, it focuses on small, incremental changes rather than large-scale transformations.
This approach makes it easier to implement and sustain improvements over time.
Second, kaizen encourages the involvement of all employees.
By valuing the input and insights of every team member, organizations can identify unique opportunities for improvement.
Finally, kaizen promotes a mindset of continuous learning and adaptation.
By regularly evaluating processes and seeking new ways to enhance performance, companies can stay competitive and responsive to changing market demands.
Implementing Kaizen in the Workplace
To successfully implement kaizen, organizations should establish a structured framework for identifying and addressing improvement opportunities.
This often involves forming cross-functional teams to analyze current processes and brainstorm solutions.
Regular training and communication are essential to fostering a culture of continuous improvement.
Employees should understand the goals and benefits of kaizen and be encouraged to contribute their ideas.
Additionally, setting measurable objectives and tracking progress is crucial for sustaining momentum and demonstrating the impact of kaizen initiatives.
Benefits of 5S and Kaizen
By integrating 5S activities and the continuous improvement approach, production management departments can achieve significant benefits.
These include increased efficiency, reduced waste, improved safety, and higher quality products and services.
Moreover, a focus on organization and improvement can lead to greater employee engagement and satisfaction.
When employees feel supported and empowered to contribute ideas, they are more likely to take ownership of their work and seek out opportunities for growth.
In conclusion, mastering 5S activities and embracing a continuous improvement mindset are essential for new employees in the production management department.
These practices help create a strong foundation for operational excellence, fostering an environment where both the company and its employees can thrive.
資料ダウンロード
QCD調達購買管理クラウド「newji」は、調達購買部門で必要なQCD管理全てを備えた、現場特化型兼クラウド型の今世紀最高の購買管理システムとなります。
ユーザー登録
調達購買業務の効率化だけでなく、システムを導入することで、コスト削減や製品・資材のステータス可視化のほか、属人化していた購買情報の共有化による内部不正防止や統制にも役立ちます。
NEWJI DX
製造業に特化したデジタルトランスフォーメーション(DX)の実現を目指す請負開発型のコンサルティングサービスです。AI、iPaaS、および先端の技術を駆使して、製造プロセスの効率化、業務効率化、チームワーク強化、コスト削減、品質向上を実現します。このサービスは、製造業の課題を深く理解し、それに対する最適なデジタルソリューションを提供することで、企業が持続的な成長とイノベーションを達成できるようサポートします。
オンライン講座
製造業、主に購買・調達部門にお勤めの方々に向けた情報を配信しております。
新任の方やベテランの方、管理職を対象とした幅広いコンテンツをご用意しております。
お問い合わせ
コストダウンが利益に直結する術だと理解していても、なかなか前に進めることができない状況。そんな時は、newjiのコストダウン自動化機能で大きく利益貢献しよう!
(Β版非公開)