- お役立ち記事
- Unlocking the Secrets of Japanese Manufacturing: Revolutionize Your Business with Production Efficiency Improvement
Unlocking the Secrets of Japanese Manufacturing: Revolutionize Your Business with Production Efficiency Improvement
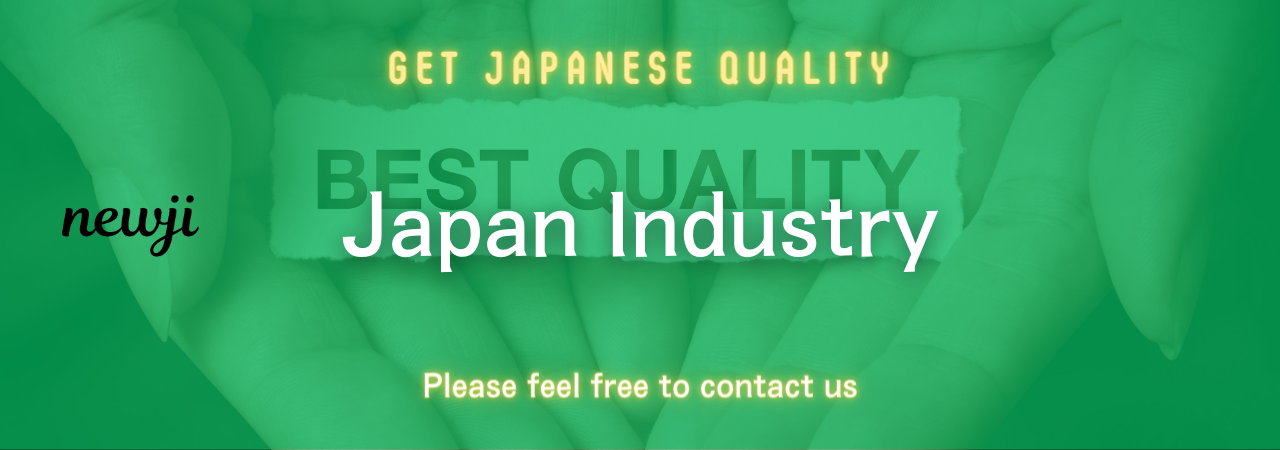
目次
Understanding Japanese Manufacturing Excellence
Japanese manufacturing has long been synonymous with quality, precision, and efficiency. Companies worldwide seek to emulate the success of Japanese firms, known for their ability to produce high-quality products while maintaining cost-effectiveness. This article explores the secrets behind Japanese manufacturing efficiency and how businesses can leverage these practices to revolutionize their operations.
The Pillars of Japanese Manufacturing
Japanese manufacturing excellence is built upon several key principles that foster continuous improvement and operational efficiency. Understanding these pillars is essential for any business aiming to adopt similar strategies.
Kaizen: Continuous Improvement
Kaizen, meaning “change for better,” is a cornerstone of Japanese manufacturing. It emphasizes continuous, incremental improvements in all aspects of a business. By encouraging every employee to contribute ideas for improving processes, products, and services, companies can achieve significant enhancements over time.
Just-In-Time (JIT) Production
JIT is a strategy that aligns raw material orders with production schedules. This minimizes inventory costs and reduces waste by ensuring that materials arrive exactly when needed in the production process. Implementing JIT requires precise demand forecasting and a reliable supply chain.
Respect for People
Japanese manufacturing places a strong emphasis on valuing employees and fostering a collaborative work environment. By investing in employee training and encouraging teamwork, companies can enhance productivity and innovation.
The Role of Procurement and Purchasing in Japanese Manufacturing
Effective procurement and purchasing strategies are vital to maintaining the high standards of Japanese manufacturing. These functions ensure that the right materials are acquired at the right time and cost, contributing to overall production efficiency.
Strategic Supplier Partnerships
Japanese companies often build long-term relationships with suppliers, fostering trust and collaboration. These strategic partnerships enable better communication, flexibility, and mutual support, which are crucial for maintaining quality and efficiency.
Supplier Development Programs
To ensure that suppliers meet their high standards, Japanese manufacturers implement supplier development programs. These programs provide training, resources, and feedback to help suppliers improve their processes and products, aligning them with the company’s quality expectations.
Advantages of Sourcing from Japanese Suppliers
Partnering with Japanese suppliers offers numerous benefits that can significantly enhance a company’s manufacturing capabilities.
High-Quality Standards
Japanese suppliers are renowned for their commitment to quality. By sourcing from these suppliers, companies can ensure that their products meet stringent quality criteria, reducing defects and enhancing customer satisfaction.
Advanced Technology and Innovation
Japan is a leader in technological innovation. Suppliers from Japan often employ the latest technologies and innovative practices, enabling companies to gain access to cutting-edge solutions that can improve their production processes.
Reliability and Consistency
Japanese suppliers are known for their reliability and consistency in delivering materials on time and in the required quantities. This dependability helps companies maintain smooth production schedules and minimize downtime.
Disadvantages of Sourcing from Japanese Suppliers
While there are many advantages, sourcing from Japanese suppliers also presents certain challenges that businesses must navigate.
Higher Costs
Japanese suppliers often charge premium prices due to their high-quality standards and advanced technologies. These higher costs can impact the overall budget, especially for companies with tight margins.
Language and Cultural Barriers
Effective communication is essential for successful partnerships. Language differences and cultural nuances can pose challenges in negotiations and day-to-day interactions, potentially hindering collaboration.
Longer Lead Times
Depending on the location of the supplier and shipping logistics, lead times can be longer compared to local suppliers. This can affect inventory management and the ability to respond quickly to market changes.
Supplier Negotiation Techniques
Negotiating with Japanese suppliers requires a nuanced approach that respects cultural practices and fosters mutual benefit.
Building Relationships
In Japanese business culture, building strong personal relationships is crucial. Taking the time to establish trust and rapport can lead to more favorable negotiations and long-term partnerships.
Understanding Cultural Norms
Being aware of Japanese cultural norms, such as the importance of hierarchy and indirect communication, can enhance negotiation effectiveness. Showing respect and patience during discussions reflects positively on the negotiating party.
Focus on Mutual Benefits
Japanese negotiations often emphasize win-win outcomes. Presenting proposals that offer mutual benefits can lead to more successful agreements and strengthen the supplier relationship.
Market Conditions Affecting Japanese Procurement
Several market conditions influence the procurement landscape in Japan, impacting how companies approach sourcing strategies.
Economic Stability
Japan’s stable economy provides a reliable environment for procurement activities. However, global economic fluctuations can still affect currency exchange rates and international trade dynamics.
Technological Advancements
Rapid technological changes in Japan drive innovation in manufacturing processes. Staying abreast of these advancements is essential for companies looking to incorporate the latest technologies into their operations.
Supply Chain Resilience
Natural disasters and geopolitical issues can disrupt supply chains. Japanese companies often implement robust contingency plans to ensure continuity, which can be a valuable practice for procurement strategies.
Best Practices in International Procurement from Japan
Adopting best practices from Japanese procurement can enhance efficiency and effectiveness in purchasing operations.
Demand Forecasting
Accurate demand forecasting is essential for aligning procurement with production needs. Utilizing advanced forecasting tools and collaborating closely with suppliers can improve accuracy and reduce excess inventory.
Lean Inventory Management
Implementing lean inventory principles, such as JIT, helps minimize waste and reduce storage costs. This approach requires precise coordination with suppliers to ensure timely delivery of materials.
Performance Metrics and Monitoring
Establishing clear performance metrics allows companies to monitor supplier performance effectively. Regular assessments help identify areas for improvement and ensure that suppliers meet quality and delivery standards.
Challenges and Solutions in Adopting Japanese Practices
Integrating Japanese manufacturing principles into a business can present challenges that require strategic solutions.
Cultural Integration
Adapting to Japanese practices often involves significant cultural shifts within a company. Providing cultural training and promoting an open-minded organizational culture can facilitate smoother integration.
Technology Implementation
Adopting advanced manufacturing technologies can be resource-intensive. Investing in training and phased implementation plans can mitigate risks and ensure successful technology integration.
Maintaining Supplier Relationships
Building and maintaining strong supplier relationships require ongoing effort and communication. Establishing regular touchpoints and fostering a collaborative environment can sustain these partnerships long-term.
Case Studies: Successful Implementation of Japanese Manufacturing Techniques
Examining real-world examples can provide valuable insights into the successful application of Japanese manufacturing principles.
Toyota Production System
Toyota’s Production System (TPS) exemplifies the successful implementation of Kaizen and JIT. By continuously improving processes and eliminating waste, Toyota has maintained its position as a leader in the automotive industry.
Panasonic’s Supplier Integration
Panasonic has effectively integrated its suppliers into its production process through strategic partnerships and supplier development programs. This approach has enhanced product quality and production efficiency.
Future Trends in Japanese Manufacturing and Procurement
Staying ahead of emerging trends is crucial for companies aiming to leverage Japanese manufacturing practices for future success.
Automation and Industry 4.0
The rise of automation and Industry 4.0 technologies is transforming Japanese manufacturing. Embracing these advancements can lead to increased productivity and reduced operational costs.
Sustainability and Green Manufacturing
Japanese manufacturers are increasingly focusing on sustainability and eco-friendly practices. Incorporating green manufacturing principles can not only improve environmental impact but also meet growing consumer demand for sustainable products.
Global Supply Chain Optimization
Optimizing global supply chains for resilience and efficiency is becoming a priority. Leveraging Japanese expertise in supply chain management can help companies navigate complexities and enhance overall performance.
Conclusion
Unlocking the secrets of Japanese manufacturing offers a pathway to significant improvements in production efficiency and overall business performance. By embracing principles such as continuous improvement, strategic supplier partnerships, and advanced technology, companies can revolutionize their operations. While challenges exist, adopting best practices and learning from successful case studies can pave the way for sustainable growth and competitive advantage in the global market.
資料ダウンロード
QCD調達購買管理クラウド「newji」は、調達購買部門で必要なQCD管理全てを備えた、現場特化型兼クラウド型の今世紀最高の購買管理システムとなります。
ユーザー登録
調達購買業務の効率化だけでなく、システムを導入することで、コスト削減や製品・資材のステータス可視化のほか、属人化していた購買情報の共有化による内部不正防止や統制にも役立ちます。
NEWJI DX
製造業に特化したデジタルトランスフォーメーション(DX)の実現を目指す請負開発型のコンサルティングサービスです。AI、iPaaS、および先端の技術を駆使して、製造プロセスの効率化、業務効率化、チームワーク強化、コスト削減、品質向上を実現します。このサービスは、製造業の課題を深く理解し、それに対する最適なデジタルソリューションを提供することで、企業が持続的な成長とイノベーションを達成できるようサポートします。
オンライン講座
製造業、主に購買・調達部門にお勤めの方々に向けた情報を配信しております。
新任の方やベテランの方、管理職を対象とした幅広いコンテンツをご用意しております。
お問い合わせ
コストダウンが利益に直結する術だと理解していても、なかなか前に進めることができない状況。そんな時は、newjiのコストダウン自動化機能で大きく利益貢献しよう!
(Β版非公開)