- お役立ち記事
- Unlocking the Secrets of Japanese Bath Additive OEM: Revolutionize Your Wellness Experience
Unlocking the Secrets of Japanese Bath Additive OEM: Revolutionize Your Wellness Experience
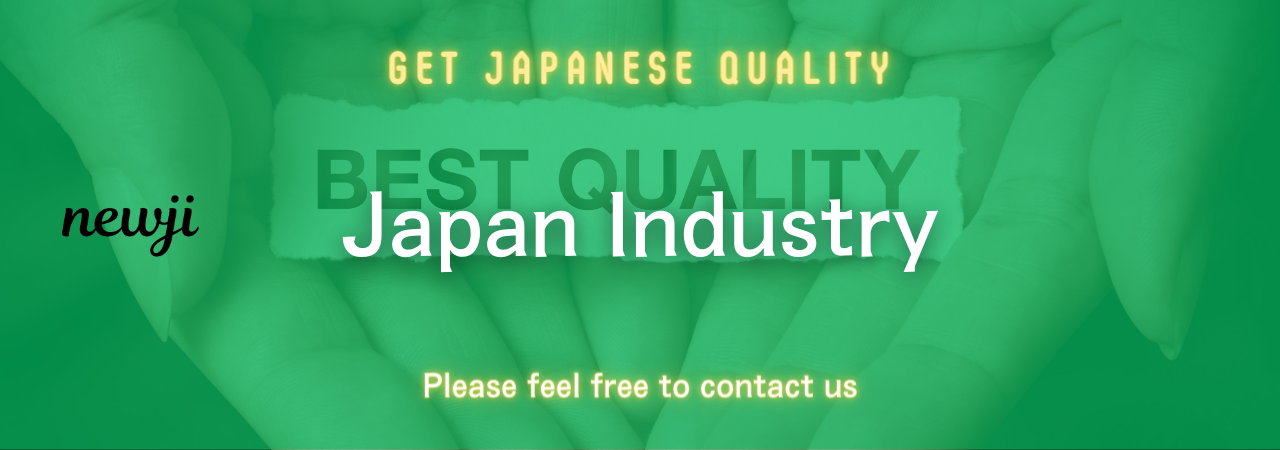
目次
Understanding OEM in Japanese Bath Additives
Japanese Original Equipment Manufacturers (OEMs) in the bath additive industry have garnered a reputation for excellence and innovation. OEM partnerships involve collaborating with Japanese manufacturers to produce bath additives that meet specific requirements and standards. This collaboration allows companies to leverage Japan’s advanced technology and expertise in creating high-quality wellness products.
What is OEM?
OEM stands for Original Equipment Manufacturer. In this context, it refers to a company that produces bath additives based on the specifications and branding of another company. This partnership enables businesses to offer customized products without investing heavily in manufacturing facilities and research.
The Japanese Advantage
Japan’s manufacturing sector is known for its precision, quality, and efficiency. These attributes make Japanese OEMs highly sought after in the global market, particularly in the wellness and personal care industries. Their commitment to excellence ensures that the final products meet rigorous quality standards, providing consumers with reliable and effective bath additives.
Advantages of Partnering with Japanese Manufacturers
Collaborating with Japanese OEMs offers numerous benefits that can significantly enhance a company’s product offerings and market position.
Superior Quality
Japanese manufacturers adhere to stringent quality control measures, ensuring that bath additives are free from defects and meet high standards. This commitment to quality translates into consistent product performance and customer satisfaction.
Innovative Technology
Japan is at the forefront of technological advancements in manufacturing. By partnering with Japanese OEMs, companies can access cutting-edge technologies that enhance product efficacy and introduce unique features in bath additives.
Customization and Flexibility
Japanese OEMs offer a high degree of customization, allowing companies to tailor products to specific market needs. From ingredient selection to packaging design, manufacturers work closely with partners to create bespoke solutions that align with brand identity and consumer preferences.
Reliable Supply Chain
Japan’s well-established logistics infrastructure ensures timely and reliable delivery of products. This reliability minimizes supply chain disruptions and ensures that businesses can maintain consistent inventory levels to meet consumer demand.
Disadvantages and Challenges
While there are significant advantages to partnering with Japanese OEMs, businesses may also encounter certain challenges.
High Production Costs
Japanese manufacturing is often associated with higher production costs due to superior quality and advanced technology. These costs can translate into higher product prices, which may impact competitiveness in price-sensitive markets.
Cultural and Language Barriers
Effective communication is crucial for successful OEM partnerships. Cultural differences and language barriers can pose challenges in negotiations, project management, and day-to-day operations, potentially leading to misunderstandings and delays.
Long Lead Times
Japanese manufacturers may have longer lead times due to meticulous quality control processes. While this ensures high-quality products, it may not align with businesses that require rapid turnaround times for product launches or seasonal demand.
Minimum Order Quantities
OEM partners often require minimum order quantities, which can be a barrier for smaller companies or those testing new markets. This requirement necessitates careful planning and inventory management to avoid excess stock and associated costs.
Supplier Negotiation Techniques
Successful negotiations with Japanese OEMs require a strategic approach that respects cultural nuances and emphasizes mutual benefits.
Building Trust and Relationships
In Japanese business culture, building a strong relationship is fundamental. Investing time in establishing trust through regular communication, respect, and understanding can lead to more favorable negotiation outcomes and long-term partnerships.
Clear Communication of Requirements
Clearly articulating product specifications, quality standards, and expectations is essential. Providing detailed documentation and being transparent about business objectives helps prevent misunderstandings and aligns both parties towards common goals.
Flexibility and Compromise
Demonstrating flexibility and a willingness to compromise can facilitate smoother negotiations. Understanding the manufacturer’s constraints and being open to alternative solutions can lead to mutually beneficial agreements.
Long-Term Partnership Perspective
Approaching negotiations with a long-term partnership mindset encourages collaboration and reduces the focus on short-term gains. Highlighting the potential for ongoing business and mutual growth can strengthen the negotiation position.
Market Conditions for Japanese Bath Additives
Understanding the current market conditions is crucial for businesses looking to source bath additives from Japanese OEMs.
Growing Demand for Wellness Products
The global wellness industry is experiencing significant growth, with consumers increasingly seeking high-quality, effective bath additives. This trend presents opportunities for companies to introduce innovative products that cater to health-conscious consumers.
Competitive Landscape
The market is competitive, with numerous brands vying for consumer attention. Differentiating products through unique formulations, advanced technology, and effective branding is essential for success.
Regulatory Environment
Compliance with international regulations and standards is critical when importing bath additives. Japanese manufacturers are well-versed in navigating these regulations, ensuring that products meet the necessary legal requirements for various markets.
Economic Factors
Economic stability in Japan supports reliable manufacturing and supply chains. However, fluctuations in exchange rates and global economic conditions can impact pricing and profitability, necessitating strategic financial planning.
Best Practices in Procurement and Purchasing
Adopting best practices in procurement and purchasing can enhance the efficiency and effectiveness of partnerships with Japanese OEMs.
Due Diligence in Supplier Selection
Conducting thorough due diligence when selecting suppliers ensures that partners are reputable, financially stable, and capable of meeting quality and delivery requirements. Evaluating past performance, certifications, and references is essential in this process.
Establishing Clear Contracts
Detailed contracts that outline all aspects of the partnership, including specifications, pricing, delivery schedules, and quality standards, are crucial. Clear contractual agreements minimize the risk of disputes and provide a framework for resolving issues.
Implementing Effective Communication Channels
Maintaining open and effective communication with suppliers fosters collaboration and prompt resolution of any issues. Utilizing various communication tools and establishing regular updates help keep all parties aligned and informed.
Monitoring and Evaluating Performance
Regularly monitoring supplier performance through key performance indicators (KPIs) ensures that standards are maintained. Evaluating factors such as quality, delivery times, and responsiveness helps identify areas for improvement and reinforces accountability.
Quality Control and Assurance
Ensuring the highest quality of bath additives is paramount for success in the wellness market.
Establishing Quality Standards
Defining clear quality standards and ensuring that Japanese OEMs understand and adhere to them is essential. These standards should cover all aspects of the product, including ingredients, formulation, packaging, and labeling.
Regular Audits and Inspections
Conducting regular audits and inspections of manufacturing facilities helps verify compliance with quality standards. These evaluations provide insights into production processes and identify opportunities for enhancing quality control measures.
Collaborative Quality Improvement
Working collaboratively with suppliers to continuously improve quality processes fosters a culture of excellence. Sharing feedback, conducting joint training sessions, and implementing best practices contribute to sustained quality enhancements.
Logistics and Supply Chain Management
Efficient logistics and supply chain management are critical for maintaining product availability and minimizing costs.
Optimizing Transportation Routes
Strategically planning transportation routes can reduce lead times and lower shipping costs. Collaborating with experienced logistics partners ensures that products are delivered efficiently and reliably.
Inventory Management
Implementing effective inventory management practices, such as just-in-time (JIT) inventory, helps balance supply and demand while minimizing carrying costs. Accurate forecasting and real-time tracking systems enhance inventory accuracy and responsiveness.
Addressing Supply Chain Risks
Identifying and mitigating supply chain risks, such as delays, disruptions, or quality issues, is essential. Developing contingency plans and diversifying supplier sources can enhance supply chain resilience.
Case Studies and Examples
Examining real-world examples of successful OEM partnerships provides valuable insights and lessons.
Case Study 1: Brand X’s Success with Japanese OEMs
Brand X partnered with a leading Japanese OEM to develop a line of premium bath additives. By leveraging the manufacturer’s expertise in natural ingredients and advanced formulation techniques, Brand X introduced a product line that quickly gained market traction. The collaboration emphasized quality and innovation, resulting in increased brand loyalty and market share.
Case Study 2: Overcoming Challenges in Supplier Negotiations
Company Y faced challenges in negotiating terms with a Japanese OEM due to cultural differences. By investing in cross-cultural training and engaging a local intermediary, Company Y successfully established effective communication channels. This approach facilitated more favorable negotiation outcomes and strengthened the long-term partnership.
Case Study 3: Enhancing Quality Control through Collaboration
A startup brand sought to enter the wellness market with high-quality bath additives. Partnering with a Japanese OEM, they implemented joint quality control measures and regular audits. This collaboration ensured product consistency and compliance with international standards, enabling the startup to build a reputable brand presence.
Conclusion
Partnering with Japanese OEMs for bath additives offers a pathway to high-quality, innovative wellness products that can transform consumer experiences. While challenges such as higher production costs and cultural barriers exist, the advantages of superior quality, technological expertise, and reliable supply chains make Japanese manufacturers valuable partners. By adopting best practices in procurement, fostering strong relationships, and focusing on continuous quality improvement, businesses can effectively leverage Japanese OEM capabilities to revolutionize their wellness offerings and achieve sustained market success.
資料ダウンロード
QCD調達購買管理クラウド「newji」は、調達購買部門で必要なQCD管理全てを備えた、現場特化型兼クラウド型の今世紀最高の購買管理システムとなります。
ユーザー登録
調達購買業務の効率化だけでなく、システムを導入することで、コスト削減や製品・資材のステータス可視化のほか、属人化していた購買情報の共有化による内部不正防止や統制にも役立ちます。
NEWJI DX
製造業に特化したデジタルトランスフォーメーション(DX)の実現を目指す請負開発型のコンサルティングサービスです。AI、iPaaS、および先端の技術を駆使して、製造プロセスの効率化、業務効率化、チームワーク強化、コスト削減、品質向上を実現します。このサービスは、製造業の課題を深く理解し、それに対する最適なデジタルソリューションを提供することで、企業が持続的な成長とイノベーションを達成できるようサポートします。
オンライン講座
製造業、主に購買・調達部門にお勤めの方々に向けた情報を配信しております。
新任の方やベテランの方、管理職を対象とした幅広いコンテンツをご用意しております。
お問い合わせ
コストダウンが利益に直結する術だと理解していても、なかなか前に進めることができない状況。そんな時は、newjiのコストダウン自動化機能で大きく利益貢献しよう!
(Β版非公開)