- お役立ち記事
- Mastering Precision: How Japanese Manufacturing Excels in Compliance with Global Standards
Mastering Precision: How Japanese Manufacturing Excels in Compliance with Global Standards
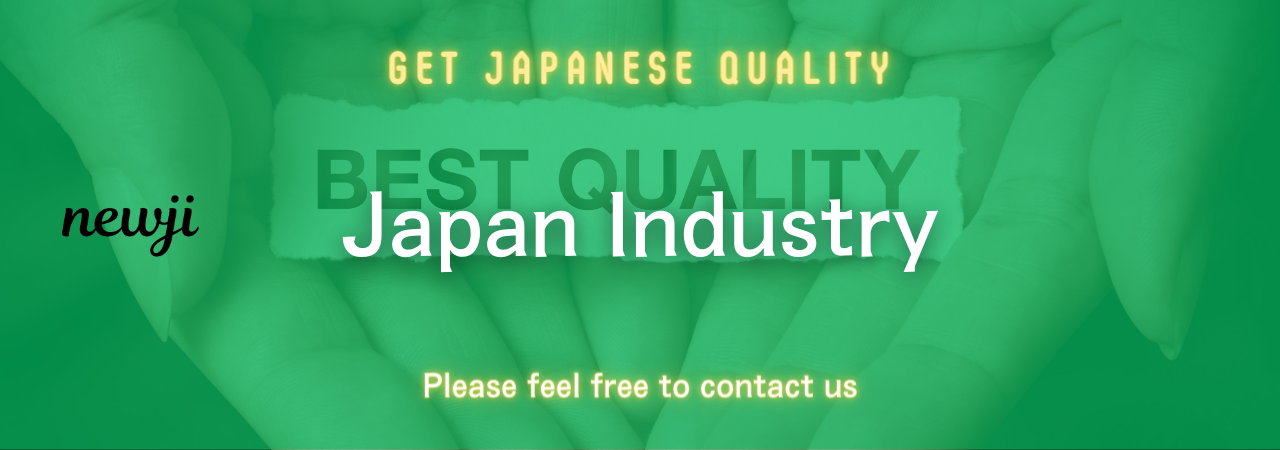
目次
Understanding Global Standards in Manufacturing
What are Global Standards?
Global standards in manufacturing refer to internationally recognized guidelines and specifications that ensure products and services are safe, reliable, and of good quality.
These standards are established by organizations such as the International Organization for Standardization (ISO) and the International Electrotechnical Commission (IEC).
They cover various aspects of manufacturing, including quality management, environmental impact, and product safety.
Importance of Compliance
Compliance with global standards is crucial for manufacturers aiming to compete in international markets.
Adhering to these standards facilitates easier market access and builds trust with consumers and business partners.
It also helps in minimizing risks related to product defects, legal liabilities, and reputational damage.
The Japanese Manufacturing Philosophy
Kaizen – Continuous Improvement
Kaizen is a Japanese philosophy that emphasizes continuous, incremental improvement in all aspects of manufacturing.
It involves every employee, from top management to the shop floor, in the process of identifying and implementing improvements.
This approach leads to higher efficiency, reduced waste, and enhanced product quality.
Lean Manufacturing
Lean manufacturing focuses on minimizing waste without compromising productivity.
By streamlining processes and eliminating non-value-added activities, Japanese manufacturers achieve higher efficiency and lower costs.
This methodology also contributes to faster production cycles and improved responsiveness to market changes.
Quality Control Systems
Japanese manufacturers implement rigorous quality control systems such as Six Sigma and Total Quality Management (TQM).
These systems use data-driven methods to identify and eliminate defects, ensuring consistent product quality.
Quality control is integrated into every stage of the manufacturing process, from design to final inspection.
Procurement and Purchasing Strategies in Japanese Manufacturing
Supplier Relationships
Japanese manufacturers prioritize long-term relationships with suppliers.
They engage in mutually beneficial partnerships, fostering collaboration and trust.
This approach ensures a reliable supply chain and enables continuous quality improvement through joint initiatives.
Just-In-Time (JIT) Inventory
The JIT inventory system minimizes inventory levels by ensuring that materials and components arrive exactly when needed.
This reduces storage costs and minimizes waste, as excess inventory is avoided.
JIT requires precise coordination with suppliers and streamlined internal processes to maintain efficiency.
Strategic Sourcing
Strategic sourcing involves selecting suppliers based on their ability to provide high-quality materials at competitive prices.
Japanese manufacturers evaluate suppliers on various criteria, including reliability, quality standards, and innovation capabilities.
This strategy ensures that manufacturers have access to the best resources for their production needs.
Advantages of Japanese Manufacturing Compliance
High Quality and Reliability
Compliance with global standards ensures that Japanese products meet stringent quality requirements.
This results in higher reliability and durability, enhancing customer satisfaction and brand reputation.
High-quality products are less likely to fail, reducing returns and warranty claims.
Enhanced Efficiency and Productivity
Adhering to established standards streamlines manufacturing processes, leading to increased efficiency.
Standardization reduces variability, allowing for more predictable and manageable production cycles.
This heightened productivity enables Japanese manufacturers to meet market demands swiftly.
Strong Global Reputation
Japanese manufacturing’s commitment to global standards has built a strong international reputation for excellence.
This reputation attracts customers and partners from around the world, facilitating business growth and expansion.
A trusted brand can command premium pricing and secure long-term business relationships.
Challenges and Disadvantages
High Initial Investment
Achieving compliance with global standards often requires significant initial investments in technology, training, and process redesign.
This can be a barrier for smaller manufacturers with limited financial resources.
However, the long-term benefits of compliance typically outweigh the initial costs.
Cultural Barriers in International Business
Japanese manufacturers may face cultural differences when dealing with international partners and customers.
Understanding and adapting to diverse business practices and communication styles is essential for successful global operations.
Cultural barriers can sometimes lead to misunderstandings and delays in negotiations.
Rigidity in Processes
Strict adherence to standards can sometimes lead to rigidity, making it difficult to adapt quickly to changes.
While consistency is beneficial, excessive rigidity may hinder innovation and responsiveness to emerging market trends.
Balancing standardization with flexibility is crucial for sustained competitiveness.
Supplier Negotiation Techniques
Building Trust and Long-Term Relationships
Japanese manufacturers focus on building trust with suppliers through consistent and transparent interactions.
Long-term relationships are prioritized over short-term gains, fostering a collaborative environment.
Trust-based relationships facilitate smoother negotiations and more favorable terms.
Transparent Communication
Clear and honest communication is essential in negotiations.
Japanese companies ensure that expectations, requirements, and concerns are openly addressed.
Transparency minimizes misunderstandings and promotes mutually beneficial agreements.
Collaborative Problem Solving
During negotiations, Japanese manufacturers adopt a collaborative approach to resolving issues.
By working together with suppliers to find solutions, both parties can achieve optimal outcomes.
This method strengthens partnerships and ensures that both sides are invested in the success of the relationship.
Market Conditions Affecting Japanese Manufacturers
Global Competition
Japanese manufacturers operate in a highly competitive global market.
To maintain their edge, they continuously innovate and improve processes to offer superior products.
Staying ahead of competitors requires ongoing investment in research and development.
Technological Advancements
Rapid technological changes influence manufacturing practices and standards.
Japanese companies must adopt new technologies to remain compliant and competitive.
Embracing innovations such as automation and digitalization enhances efficiency and product quality.
Economic Factors
Economic fluctuations can impact manufacturing operations and compliance costs.
Exchange rate variations, inflation, and shifts in consumer demand require manufacturers to adjust strategies.
Economic resilience and adaptability are essential for maintaining compliance and market position.
Best Practices for Achieving Compliance
Adopting Advanced Technologies
Implementing the latest technologies can streamline processes and ensure adherence to global standards.
Automation, data analytics, and smart manufacturing tools enhance accuracy and efficiency.
Staying technologically current is vital for compliance and competitiveness.
Investing in Workforce Training
A well-trained workforce is crucial for maintaining high standards.
Continuous training programs ensure that employees are knowledgeable about the latest practices and standards.
Investing in human resources leads to better quality control and operational excellence.
Continuous Monitoring and Improvement
Ongoing monitoring of processes and performance is essential to maintain compliance.
Regular audits and assessments help identify areas for improvement.
A commitment to continuous improvement ensures sustained adherence to global standards.
Case Studies of Japanese Manufacturing Success
Toyota
Toyota exemplifies excellence in complying with global standards through its Toyota Production System (TPS).
Emphasizing lean manufacturing and continuous improvement, Toyota sets industry benchmarks for quality and efficiency.
Its focus on innovation and sustainability has solidified its position as a global automotive leader.
Sony
Sony has established itself as a pioneer in electronics by adhering to stringent global standards.
Its commitment to quality and innovation has produced iconic products known worldwide.
Sony’s strategic sourcing and robust supplier relationships contribute to its manufacturing success.
Panasonic
Panasonic’s dedication to sustainable manufacturing practices aligns with global environmental standards.
By integrating energy-efficient technologies and eco-friendly materials, Panasonic meets regulatory requirements and consumer expectations.
Its comprehensive quality management systems ensure product reliability and customer satisfaction.
Future Trends in Japanese Manufacturing Compliance
Industry 4.0 Integration
The fourth industrial revolution, or Industry 4.0, involves the integration of digital technologies into manufacturing.
Japanese manufacturers are adopting advanced robotics, artificial intelligence, and the Internet of Things (IoT) to enhance productivity and compliance.
Industry 4.0 facilitates smarter manufacturing processes and real-time monitoring of standards adherence.
Sustainable Manufacturing
Sustainability is becoming increasingly important in global manufacturing standards.
Japanese companies are investing in green technologies and sustainable practices to reduce their environmental impact.
Sustainable manufacturing not only ensures compliance but also meets the growing demand for eco-friendly products.
Global Standard Synchronization
As global standards evolve, Japanese manufacturers must continuously align their practices with international requirements.
Harmonizing standards across different regions facilitates smoother global operations and reduces compliance complexities.
Staying informed about changes in global standards is essential for maintaining competitiveness.
Conclusion
Japanese manufacturing excels in compliance with global standards through a steadfast commitment to quality, efficiency, and continuous improvement.
By embracing philosophies like Kaizen and lean manufacturing, fostering strong supplier relationships, and adopting advanced technologies, Japanese companies maintain their competitive edge.
While challenges such as high initial investments and cultural barriers exist, the advantages of compliance—ranging from high reliability to a robust global reputation—are substantial.
As the industry evolves with trends like Industry 4.0 and sustainable practices, Japanese manufacturers are well-positioned to continue their leadership in the global market.
Their dedication to best practices and adaptability ensures ongoing success in meeting and exceeding global standards.
資料ダウンロード
QCD調達購買管理クラウド「newji」は、調達購買部門で必要なQCD管理全てを備えた、現場特化型兼クラウド型の今世紀最高の購買管理システムとなります。
ユーザー登録
調達購買業務の効率化だけでなく、システムを導入することで、コスト削減や製品・資材のステータス可視化のほか、属人化していた購買情報の共有化による内部不正防止や統制にも役立ちます。
NEWJI DX
製造業に特化したデジタルトランスフォーメーション(DX)の実現を目指す請負開発型のコンサルティングサービスです。AI、iPaaS、および先端の技術を駆使して、製造プロセスの効率化、業務効率化、チームワーク強化、コスト削減、品質向上を実現します。このサービスは、製造業の課題を深く理解し、それに対する最適なデジタルソリューションを提供することで、企業が持続的な成長とイノベーションを達成できるようサポートします。
オンライン講座
製造業、主に購買・調達部門にお勤めの方々に向けた情報を配信しております。
新任の方やベテランの方、管理職を対象とした幅広いコンテンツをご用意しております。
お問い合わせ
コストダウンが利益に直結する術だと理解していても、なかなか前に進めることができない状況。そんな時は、newjiのコストダウン自動化機能で大きく利益貢献しよう!
(Β版非公開)