- お役立ち記事
- A must-see for production operation department managers! How to maximize on-site efficiency with LEAN production methods
A must-see for production operation department managers! How to maximize on-site efficiency with LEAN production methods
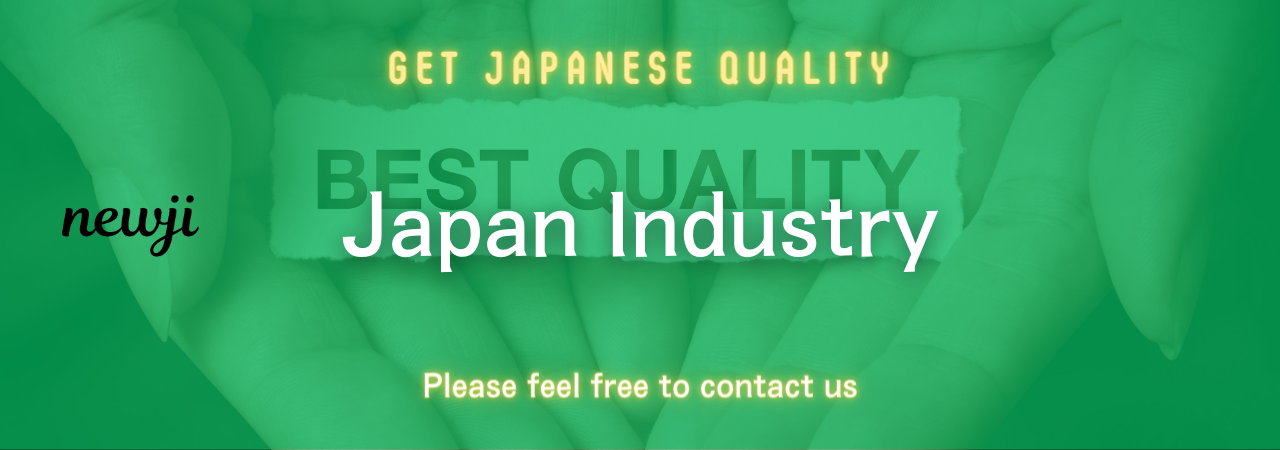
目次
Understanding LEAN Production Methods
LEAN production is a methodology aimed at minimizing waste without sacrificing productivity.
This approach focuses on enhancing overall efficiency by eliminating non-value-adding activities, thus maximizing the value from the customer’s standpoint.
Originating from the Toyota Production System, LEAN principles have been widely adopted across various industries to streamline operations and improve efficiency on the production floor.
The Core Principles of LEAN Production
To better understand how LEAN production can enhance on-site efficiency, it is important to grasp its core principles.
LEAN is built on five main principles: Value, Value Stream, Flow, Pull, and Perfection.
1. **Value**: This principle revolves around identifying what the customer considers valuable and ensuring that everything aligns with providing that value.
2. **Value Stream**: It involves mapping out all the steps involved in the production process to distinguish between value-adding and non-value-adding activities.
3. **Flow**: Maintaining a streamlined process with minimal interruptions is crucial. The goal is to ensure a smooth progression of tasks from one stage to the next.
4. **Pull**: Demand-driven production is essential. Instead of forecasting production needs, the focus is on producing based on current demands, allowing more flexible response times.
5. **Perfection**: Continuous improvement is a key aspect of LEAN, with a focus on always finding ways to refine processes and eliminate waste.
The Importance of LEAN in Enhancing Efficiency
Production operation department managers play a pivotal role in boosting efficiency on-site.
By integrating LEAN methods, managers can achieve numerous benefits:
– **Waste Reduction**: LEAN helps in identifying and eliminating waste in various forms, such as overproduction, waiting times, inefficient transport, excessive motion, over-processing, excess inventory, and defects.
– **Cost Savings**: By reducing waste, resources are better allocated, leading to significant cost savings. Lean operations lead to better utilization of man-hours, materials, and machinery.
– **Improved Quality**: LEAN focuses on producing products that match customer expectations and quality standards right from the start, reducing reworks and defects.
Implementing LEAN in the Production Floor
The journey of implementing LEAN involves several deliberate steps:
1. Conduct a Value Stream Mapping
Value stream mapping is crucial for visualizing the production process.
It helps in identifying areas needing improvement by distinguishing between steps that add value and those that don’t.
Mapping the current state provides a baseline from which enhancements are made.
2. Identify and Eliminate Waste
Once mapping is complete, the next step is identifying and tackling waste.
A thorough analysis pinpoints areas where resources can be better managed.
By focusing on eliminating these inefficiencies, production managers can significantly enhance production flow and reduce costs.
3. Create a Culture of Continuous Improvement
Building a culture that encourages continuous improvement is essential.
Managers should adopt a mindset of seeking perfection by constantly reassessing and optimizing processes.
Introducing tools like Kaizen or ‘5 Whys’ problem-solving techniques can facilitate this culture of ongoing enhancement.
4. Train and Empower Employees
Employees are instrumental to the success of LEAN implementation.
Training is essential for equipping them with necessary skills and mindsets.
Empowering employees fosters ownership, accountability, and a proactive approach toward process improvements.
5. Implement Pull Systems
Adopting a ‘pull’ system based on real-time demand rather than projections is vital.
This approach minimizes waste and ensures resources are used only when necessary.
Techniques like just-in-time production can be beneficial in maintaining a pull-focused operation.
Challenges in Implementing LEAN and How to Overcome Them
Though LEAN production methods offer many advantages, their implementation can encounter challenges:
– **Resistance to Change**: Employees and managers might resist changing existing workflows. Overcoming this requires effective communication, clear demonstration of benefits, and involving employees in the process.
– **Inadequate Training**: Without thorough training, employees may not fully grasp LEAN principles. Comprehensive training programs must be established to ensure everyone is well-versed in necessary methodologies.
– **Short-Term Focus**: Focusing solely on short-term gains can hinder the full potential of LEAN. It is important to maintain a long-term perspective and commit to continuous improvement over time.
– **Resource Allocation**: Implementing LEAN involves dedicating resources that may initially disrupt production. Proper planning and phased implementation can help mitigate these disruptions.
The Future of LEAN Production in the Manufacturing Industry
As industries evolve, LEAN production methods continue to adapt and offer new dimensions of efficiency.
By integrating digital technologies, such as IoT and data analytics, companies are enhancing the reach and precision of LEAN processes.
Manufacturers are increasingly leveraging digital tools to monitor performance in real-time, further streamlining operations and maximizing output.
Additionally, the emphasis on sustainability and environmental responsibility aligns seamlessly with LEAN’s commitment to waste reduction.
By achieving sustainable practices, companies position themselves as industry leaders in eco-friendly production techniques.
Conclusion
For managers in the production operation department, understanding and implementing LEAN production methods can lead to significant benefits.
With an emphasis on value creation, waste reduction, and continuous improvement, LEAN offers a robust pathway to enhancing on-site efficiency.
By addressing challenges and embracing the future of LEAN and its integration with digital solutions, companies can drive productivity and remain competitive in today’s dynamic market.
資料ダウンロード
QCD調達購買管理クラウド「newji」は、調達購買部門で必要なQCD管理全てを備えた、現場特化型兼クラウド型の今世紀最高の購買管理システムとなります。
ユーザー登録
調達購買業務の効率化だけでなく、システムを導入することで、コスト削減や製品・資材のステータス可視化のほか、属人化していた購買情報の共有化による内部不正防止や統制にも役立ちます。
NEWJI DX
製造業に特化したデジタルトランスフォーメーション(DX)の実現を目指す請負開発型のコンサルティングサービスです。AI、iPaaS、および先端の技術を駆使して、製造プロセスの効率化、業務効率化、チームワーク強化、コスト削減、品質向上を実現します。このサービスは、製造業の課題を深く理解し、それに対する最適なデジタルソリューションを提供することで、企業が持続的な成長とイノベーションを達成できるようサポートします。
オンライン講座
製造業、主に購買・調達部門にお勤めの方々に向けた情報を配信しております。
新任の方やベテランの方、管理職を対象とした幅広いコンテンツをご用意しております。
お問い合わせ
コストダウンが利益に直結する術だと理解していても、なかなか前に進めることができない状況。そんな時は、newjiのコストダウン自動化機能で大きく利益貢献しよう!
(Β版非公開)