- お役立ち記事
- Evaluation of manufacturing processes using process capability index (Cpk) that should be practiced by quality control departments
月間77,185名の
製造業ご担当者様が閲覧しています*
*2025年2月28日現在のGoogle Analyticsのデータより
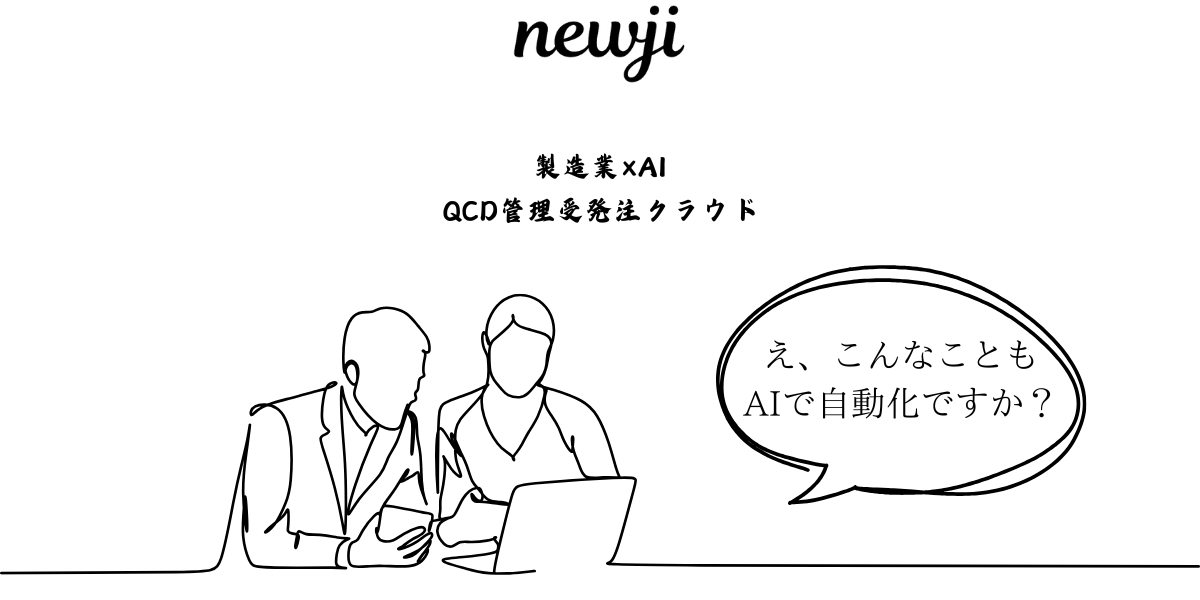
Evaluation of manufacturing processes using process capability index (Cpk) that should be practiced by quality control departments
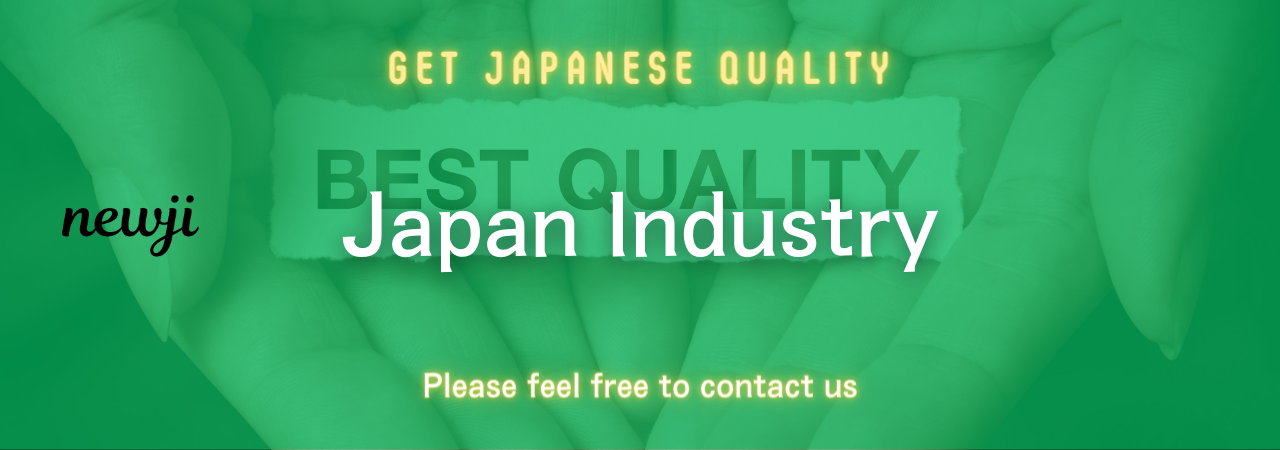
Understanding the Process Capability Index (Cpk)
The Process Capability Index, commonly known as Cpk, is a vital statistical tool used in the field of quality control.
Cpk is designed to quantify how well a manufacturing process can produce output within specified limits.
In simple terms, Cpk measures the ability of a process to produce items that meet quality standards consistently.
When a manufacturing process is evaluated, it’s essential to determine how much natural variation exists and whether the process can consistently produce products within specification limits.
That’s where Cpk comes into play.
It provides an objective measure to evaluate this capability.
Why Cpk Matters in Quality Control
For quality control departments, Cpk serves as an indicator of process performance.
It helps them assess if a process is statistically sufficient to meet design specifications set by engineers.
If the Cpk value is low, it means that the process might produce a higher percentage of products out of specification, risking customer satisfaction and increasing production waste.
A high Cpk value, typically above 1.33, indicates that the process is well-centred and capable, producing fewer defects.
Achieving a high Cpk demonstrates excellent quality control, leading to enhanced customer trust and optimized operational costs.
How to Calculate Cpk
To calculate Cpk, you’ll need three key pieces of information:
– The sample mean (average) of the process data
– The standard deviation of the process data
– The upper and lower specification limits
The Cpk formula is:
\[
Cpk = \min \left(\frac{\text{USL} – \mu}{3\sigma}, \frac{\mu – \text{LSL}}{3\sigma} \right)
\]
Where:
– USL = Upper Specification Limit
– LSL = Lower Specification Limit
– \( \mu \) = Mean of the process data
– \( \sigma \) = Standard deviation
This formula assesses how far the mean of the process is from the nearest specification limit, scaled by the process standard deviation.
It reflects not only how tight the process is (standard deviation) but also whether it’s centred between the specification limits.
Steps to Implement Cpk in Quality Control
Step 1: Collect Data
Collect a sufficient sample size from the process to provide an accurate reflection of its performance.
Ensure the data is representative of typical process operation and conditions.
Step 2: Determine Specification Limits
Clearly define the upper and lower specification limits.
These limits are often set by design engineers and dictate the range within which the product must fall to meet quality standards.
Step 3: Calculate Mean and Standard Deviation
Compute the mean and standard deviation of your collected data.
These values will provide insight into your process’s central tendency and variation.
Step 4: Apply the Cpk Formula
Use the Cpk formula to determine your process’s capability.
A Cpk value greater than 1.33 is typically viewed as capable, while a value below indicates areas for improvement.
Step 5: Continuous Monitoring
After establishing the Cpk, continue to monitor process performance periodically.
Quality control is about continuous improvement, so consistent data tracking helps catch variations and maintain process capability.
Advantages of Using Cpk
Adopting Cpk provides numerous benefits:
– **Improved Quality Control**: Cpk allows organizations to quantify process effectiveness, focus on areas needing improvement, and maintain high-quality production standards.
– **Enhanced Customer Satisfaction**: By producing within specification limits consistently, companies ensure the delivery of reliable products, boosting customer satisfaction.
– **Reduced Production Costs**: A capable process generally results in less waste and rework, thereby reducing operational costs.
– **Risk Management**: Cpk helps identify process variability and potential quality issues before they result in defects, safeguarding against product recalls and brand damage.
Limitations of Cpk
While Cpk is a powerful tool, it has some limitations:
– **Assumption of Normal Distribution**: Cpk assumes a normal distribution of data, which may not always be the case in real-world scenarios.
– **Sensitivity to Specification Limits**: If the specification limits are set too loosely, Cpk might suggest a process is capable when it may not meet real-world performance needs.
– **Single-Dimensional Perspective**: Cpk provides insight into a process at a single point in time, lacking a comprehensive view over time.
Conclusion: Cpk as a Catalyst for Quality Improvement
In the realm of manufacturing, the Process Capability Index (Cpk) is an invaluable metric that helps evaluate a process’s ability to meet rigorous quality standards.
Both powerful and insightful, Cpk empowers quality control departments to visualize process efficiency and promote higher standards.
By regularly applying Cpk analysis, organizations not only refine operational processes but also deliver superior products that uphold their brand’s reputation.
The practice of calculating and improving Cpk is a cornerstone for any quality-driven organization aiming for excellence and customer delight.
資料ダウンロード
QCD管理受発注クラウド「newji」は、受発注部門で必要なQCD管理全てを備えた、現場特化型兼クラウド型の今世紀最高の受発注管理システムとなります。
ユーザー登録
受発注業務の効率化だけでなく、システムを導入することで、コスト削減や製品・資材のステータス可視化のほか、属人化していた受発注情報の共有化による内部不正防止や統制にも役立ちます。
NEWJI DX
製造業に特化したデジタルトランスフォーメーション(DX)の実現を目指す請負開発型のコンサルティングサービスです。AI、iPaaS、および先端の技術を駆使して、製造プロセスの効率化、業務効率化、チームワーク強化、コスト削減、品質向上を実現します。このサービスは、製造業の課題を深く理解し、それに対する最適なデジタルソリューションを提供することで、企業が持続的な成長とイノベーションを達成できるようサポートします。
製造業ニュース解説
製造業、主に購買・調達部門にお勤めの方々に向けた情報を配信しております。
新任の方やベテランの方、管理職を対象とした幅広いコンテンツをご用意しております。
お問い合わせ
コストダウンが利益に直結する術だと理解していても、なかなか前に進めることができない状況。そんな時は、newjiのコストダウン自動化機能で大きく利益貢献しよう!
(β版非公開)