- お役立ち記事
- Transforming Japanese Manufacturing: The Pivotal Role of Sputtering Process OEM Technologies
Transforming Japanese Manufacturing: The Pivotal Role of Sputtering Process OEM Technologies
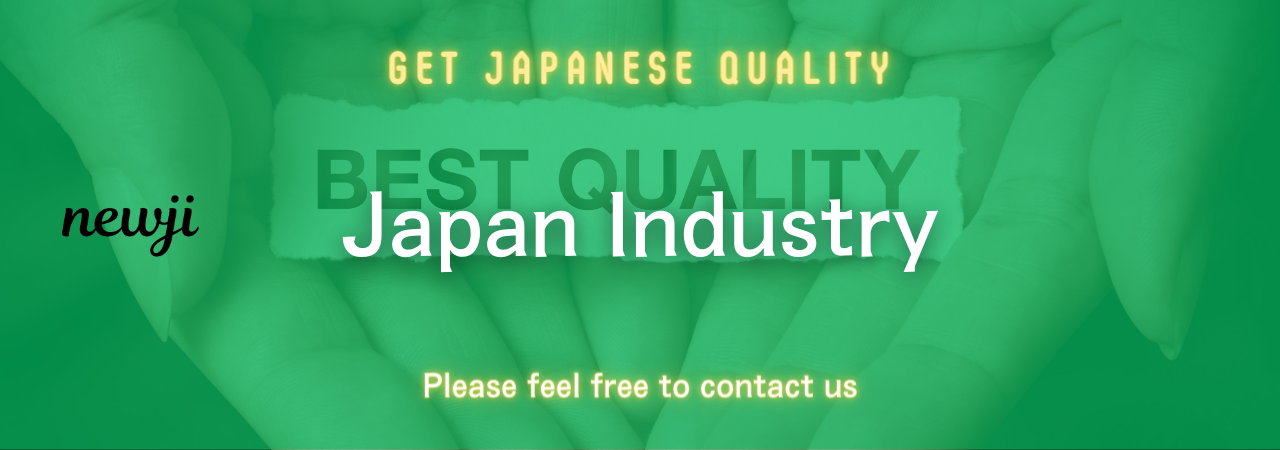
目次
Introduction
The manufacturing landscape is continually evolving, driven by advancements in technology and shifts in global market dynamics. Among the pivotal technologies shaping this transformation is the sputtering process. Originating from Japan, sputtering process OEM (Original Equipment Manufacturer) technologies have become a cornerstone in various industries, from electronics to automotive manufacturing. This article delves into the transformative role of Japanese sputtering process OEM technologies, exploring their benefits, challenges, procurement strategies, and best practices from a procurement and purchasing perspective.
Understanding the Sputtering Process
Sputtering is a physical vapor deposition (PVD) technique used to deposit thin films of material onto substrates. This process is essential in manufacturing components with precise material compositions and coatings, such as semiconductors, solar panels, and display screens. Japanese OEM technologies in sputtering have gained global recognition for their precision, efficiency, and reliability.
How Sputtering Works
In the sputtering process, ions are accelerated towards a target material, causing atoms to be ejected and deposited onto a substrate. This method allows for the creation of uniform and high-quality thin films, critical for various high-tech applications. Japanese manufacturers have perfected this technology, ensuring minimal defects and high consistency across production batches.
Types of Sputtering Techniques
There are several sputtering techniques, including DC sputtering, RF sputtering, and magnetron sputtering. Each method offers distinct advantages depending on the material and application requirements. Japanese OEMs excel in providing versatile sputtering solutions tailored to specific industry needs, enhancing the adaptability of manufacturing processes.
Advantages of Japanese Sputtering OEM Technologies
Japanese sputtering OEM technologies offer numerous benefits that make them highly sought after in the global market. These advantages stem from Japan’s emphasis on quality, innovation, and efficiency in manufacturing.
High Precision and Quality
Japanese manufacturers are renowned for their meticulous attention to detail. Sputtering equipment from Japanese OEMs ensures high precision in thin film deposition, resulting in superior product quality. This precision is crucial for industries where even minor defects can lead to significant performance issues.
Advanced Technological Innovations
Japan invests heavily in research and development, leading to continuous innovations in sputtering technologies. Features such as real-time monitoring, automation, and integration with other manufacturing systems are standard in Japanese OEM sputtering equipment. These innovations enhance production efficiency and reduce the likelihood of errors.
Reliability and Longevity
Japanese OEMs prioritize the durability of their equipment. Sputtering machines are built to withstand high operational demands, offering long service lives with minimal downtime. This reliability translates to lower maintenance costs and increased productivity for manufacturers.
Customization and Flexibility
Japanese manufacturers offer customizable sputtering solutions to meet the unique requirements of different industries. This flexibility allows companies to optimize their production processes and achieve specific performance goals, providing a competitive edge in the market.
Disadvantages of Japanese Sputtering OEM Technologies
While Japanese sputtering OEM technologies offer substantial benefits, there are also challenges associated with their procurement and implementation.
Higher Initial Costs
Japanese sputtering equipment often comes with a higher price tag compared to alternatives from other regions. The advanced features and superior quality contribute to the higher initial investment. For some companies, especially startups or those with tight budgets, this can be a significant barrier.
Complexity of Technology
The sophisticated nature of Japanese sputtering technologies can pose implementation challenges. Companies may require extensive training and technical support to operate and maintain the equipment effectively. This complexity can lead to longer setup times and increased dependency on the manufacturer for support.
Supply Chain Dependencies
Relying on Japanese OEMs for sputtering equipment means dependence on their supply chains. Any disruptions, whether due to geopolitical issues, natural disasters, or logistical challenges, can impact the timely delivery of equipment and parts, potentially halting production processes.
Limited Availability of Local Support
For companies located outside Japan, accessing local support and spare parts can be challenging. While Japanese OEMs often have global service networks, response times may be longer compared to local suppliers, affecting maintenance and repair timelines.
Procurement and Purchasing Strategies
Effective procurement and purchasing strategies are vital to maximizing the benefits of Japanese sputtering OEM technologies while mitigating potential drawbacks. This section explores strategies to optimize procurement processes.
Thorough Needs Assessment
Before initiating the procurement process, companies must conduct a comprehensive needs assessment. Understanding specific production requirements, desired features, and long-term goals helps in selecting the most suitable sputtering equipment. This assessment ensures that the investment aligns with the company’s strategic objectives.
Supplier Evaluation and Selection
Evaluating potential Japanese OEM suppliers is crucial. Factors to consider include the supplier’s reputation, quality certifications, technological capabilities, and customer support services. Visiting supplier facilities and requesting demonstrations can provide deeper insights into their operational standards and product performance.
Cost-Benefit Analysis
Conducting a cost-benefit analysis helps in understanding the overall value proposition of the sputtering equipment. While Japanese OEMs may have higher upfront costs, the long-term benefits such as durability, efficiency, and reduced maintenance can offset the initial investment. This analysis aids in making informed purchasing decisions.
Negotiating Payment Terms
Negotiating favorable payment terms with Japanese OEMs can alleviate financial strain. Options such as installment payments, extended credit periods, or discounts for bulk purchases can make the investment more manageable. Clear communication and a solid understanding of the financial implications are essential during negotiations.
Supplier Negotiation Techniques
Effective negotiation with Japanese suppliers is key to securing favorable terms and building long-term partnerships. The following techniques can enhance negotiation outcomes.
Building Strong Relationships
In Japanese business culture, relationships and trust are paramount. Investing time in building a strong rapport with suppliers can lead to more favorable negotiation outcomes. Regular communication, respect for cultural norms, and demonstrating commitment to a long-term partnership foster mutual trust.
Understanding Cultural Nuances
Being aware of Japanese business etiquette and cultural practices is essential. Practices such as bowing, the exchange of business cards with both hands, and a formal communication style can facilitate smoother negotiations. Showing respect for these nuances can positively influence supplier relationships.
Leveraging Long-Term Commitments
Japanese suppliers value long-term commitments. Highlighting the potential for ongoing business and future orders can provide leverage during negotiations. Suppliers are more likely to offer favorable terms to partners who demonstrate a willingness to engage in sustained collaboration.
Clarifying Technical Requirements
Clearly articulating technical requirements and expectations ensures that both parties are aligned. Detailed specifications, performance standards, and quality benchmarks reduce the risk of misunderstandings and ensure that the delivered equipment meets the company’s needs.
Negotiating After-Sales Support
After-sales support is a critical aspect of procurement. Negotiating comprehensive support services, including installation, training, maintenance, and rapid response to issues, enhances the value of the equipment. Ensuring robust after-sales support can minimize downtime and operational disruptions.
Market Conditions in Sputtering OEM Technologies
Understanding the current market conditions is essential for making informed procurement decisions. This section examines the trends and factors influencing the sputtering OEM market.
Global Demand and Supply Dynamics
The demand for sputtering technologies is driven by advancements in electronics, renewable energy, and automotive industries. As global demand continues to rise, Japanese OEMs are expanding their production capacities to meet the needs. However, supply chain disruptions can affect the availability and pricing of sputtering equipment.
Technological Advancements
Continuous technological advancements are shaping the sputtering OEM market. Innovations such as higher deposition rates, improved uniformity, and enhanced automation are increasing the efficiency and capabilities of sputtering equipment. Staying abreast of these advancements is crucial for procurement professionals.
Competitive Landscape
The sputtering OEM market is competitive, with Japanese manufacturers holding a significant share. Other regions, including Europe and the United States, also have strong OEM suppliers. Evaluating the competitive landscape helps in negotiating better deals and understanding the unique strengths of Japanese suppliers.
Regulatory and Environmental Factors
Regulatory standards and environmental considerations influence the sputtering OEM market. Japanese manufacturers often prioritize eco-friendly technologies and compliance with international standards, making their equipment attractive to companies focused on sustainability.
Economic Conditions
Global economic conditions, including exchange rates and trade policies, impact the procurement of Japanese sputtering equipment. Fluctuations in currency values can affect the cost, while trade agreements and tariffs influence the overall feasibility of procurement from Japan.
Best Practices in Procuring from Japanese Suppliers
Adhering to best practices ensures successful procurement outcomes when dealing with Japanese sputtering OEM suppliers. The following practices are recommended for procurement professionals.
Comprehensive Supplier Research
Conducting thorough research on potential suppliers is foundational. This includes evaluating their market reputation, financial stability, technological expertise, and track record in delivering quality products. Comprehensive research minimizes the risk of engaging with unreliable suppliers.
Clear Communication Channels
Establishing clear and effective communication channels with suppliers is essential. Regular updates, transparent discussions about expectations and challenges, and prompt responses to inquiries facilitate smooth procurement processes.
Setting Realistic Timelines
Setting and adhering to realistic timelines ensures that procurement schedules are met without undue pressure. Collaborating with suppliers to establish feasible delivery and implementation schedules helps in managing expectations and avoiding delays.
Quality Assurance and Inspection
Implementing stringent quality assurance measures and conducting inspections upon delivery ensure that the sputtering equipment meets the required standards. Collaborating with suppliers on quality benchmarks and inspection protocols maintains consistency and reliability in the procurement process.
Risk Management Strategies
Developing risk management strategies helps in mitigating potential procurement risks. Identifying potential challenges, such as supply chain disruptions or technological failures, and establishing contingency plans ensures readiness to handle unforeseen issues.
Continuous Improvement and Feedback
Engaging in continuous improvement processes and providing feedback to suppliers promotes ongoing enhancements in equipment quality and service. Establishing a feedback loop fosters a collaborative relationship focused on mutual growth and innovation.
Case Studies: Successful Procurement from Japanese OEMs
Examining real-world examples provides valuable insights into effective procurement strategies from Japanese suppliers.
Case Study 1: Electronics Manufacturer Enhances Production Efficiency
A leading electronics manufacturer sought to upgrade its production line with advanced sputtering equipment. After a thorough needs assessment, the company partnered with a Japanese OEM renowned for its innovative sputtering technologies. Through effective negotiation and clear communication, the manufacturer secured favorable payment terms and comprehensive after-sales support. The new sputtering equipment significantly improved production efficiency, reduced defect rates, and enhanced product quality, resulting in increased market competitiveness.
Case Study 2: Automotive Supplier Implements Sustainable Manufacturing Practices
An automotive parts supplier aimed to incorporate sustainable practices into its manufacturing processes. Collaborating with a Japanese OEM, the company procured sputtering equipment featuring eco-friendly technologies and energy-efficient operations. The partnership not only enabled the supplier to meet environmental standards but also lowered operational costs through reduced energy consumption. This strategic procurement strengthened the company’s commitment to sustainability and attracted environmentally conscious clients.
Case Study 3: Renewable Energy Firm Scales Production with Customized Solutions
A renewable energy firm focused on solar panel manufacturing required customized sputtering solutions to scale production. By engaging a Japanese OEM with expertise in tailored sputtering technologies, the firm obtained equipment designed to meet specific deposition requirements. The customized solutions facilitated the mass production of high-efficiency solar panels, enabling the firm to expand its market presence and meet growing demand.
Future Trends in Sputtering OEM Technologies
The sputtering OEM landscape is poised for further evolution, driven by technological advancements and changing market demands. Understanding these trends helps in strategic procurement planning.
Integration with Industry 4.0
Industry 4.0 emphasizes the integration of digital technologies into manufacturing processes. Japanese sputtering OEMs are increasingly incorporating smart features, such as IoT connectivity, real-time data analytics, and automation, into their equipment. This integration enhances operational efficiency, predictive maintenance, and data-driven decision-making.
Advancements in Material Science
Ongoing advancements in material science are expanding the capabilities of sputtering technologies. Japanese OEMs are developing equipment capable of depositing a wider range of materials with improved properties, catering to emerging applications in nanotechnology, biotechnology, and advanced electronics.
Enhanced Sustainability Measures
Sustainability remains a key focus in manufacturing. Japanese sputtering OEMs are innovating to create more environmentally friendly equipment, reducing energy consumption, minimizing waste, and utilizing recyclable materials. These advancements align with global sustainability goals and regulatory requirements.
Customization and Flexibility
The demand for customized manufacturing solutions is rising. Japanese OEMs are enhancing the flexibility of their sputtering equipment to accommodate diverse production needs. This trend supports companies in achieving tailored production processes and adapting to rapidly changing market demands.
Collaboration and Partnerships
Collaborative efforts between Japanese OEMs and international manufacturers are increasing. These partnerships facilitate knowledge transfer, co-development of technologies, and joint ventures, fostering innovation and expanding market reach for both parties.
Conclusion
Japanese sputtering process OEM technologies play a pivotal role in transforming manufacturing across various industries. Their high precision, advanced innovations, and reliability offer substantial advantages to manufacturers seeking to enhance production quality and efficiency. However, navigating the challenges associated with higher costs, technological complexity, and supply chain dependencies requires strategic procurement and purchasing approaches. By adopting best practices, effective negotiation techniques, and staying informed about market conditions and future trends, companies can successfully leverage Japanese sputtering OEM technologies to achieve their manufacturing goals and maintain a competitive edge in the global market.
資料ダウンロード
QCD調達購買管理クラウド「newji」は、調達購買部門で必要なQCD管理全てを備えた、現場特化型兼クラウド型の今世紀最高の購買管理システムとなります。
ユーザー登録
調達購買業務の効率化だけでなく、システムを導入することで、コスト削減や製品・資材のステータス可視化のほか、属人化していた購買情報の共有化による内部不正防止や統制にも役立ちます。
NEWJI DX
製造業に特化したデジタルトランスフォーメーション(DX)の実現を目指す請負開発型のコンサルティングサービスです。AI、iPaaS、および先端の技術を駆使して、製造プロセスの効率化、業務効率化、チームワーク強化、コスト削減、品質向上を実現します。このサービスは、製造業の課題を深く理解し、それに対する最適なデジタルソリューションを提供することで、企業が持続的な成長とイノベーションを達成できるようサポートします。
オンライン講座
製造業、主に購買・調達部門にお勤めの方々に向けた情報を配信しております。
新任の方やベテランの方、管理職を対象とした幅広いコンテンツをご用意しております。
お問い合わせ
コストダウンが利益に直結する術だと理解していても、なかなか前に進めることができない状況。そんな時は、newjiのコストダウン自動化機能で大きく利益貢献しよう!
(Β版非公開)