- お役立ち記事
- Integration of BTO (build to order) and production planning that the supply chain department should address
Integration of BTO (build to order) and production planning that the supply chain department should address
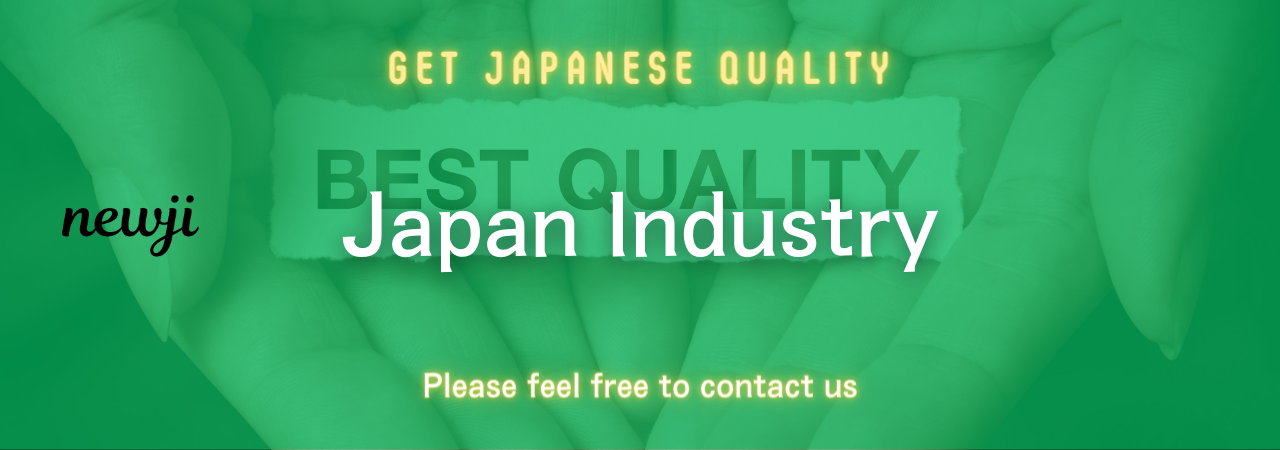
目次
Understanding BTO and Production Planning
In the realm of manufacturing and supply chain management, BTO (Build to Order) and production planning are pivotal concepts that often work hand in hand to ensure efficiency and customer satisfaction.
BTO refers to the process where products are manufactured only after an order is received, allowing for customization according to customer specifications.
Production planning, on the other hand, is a detailed roadmap of how the production process will unfold to meet those orders, ensuring the optimal use of resources and time.
To maximize the benefits of both these processes, it is essential for the supply chain department to integrate BTO with effective production planning.
The Importance of BTO
BTO has gained significant traction in recent years due to its ability to offer personalized products and reduction in inventory costs.
Unlike traditional production methods, where products are mass-produced based on forecasts, BTO ensures that items are only made when there is a confirmed demand.
This not only reduces the risk of excess inventory but also enhances customer satisfaction by delivering products tailored to individual needs.
Moreover, the BTO system allows companies to be more agile and responsive to market fluctuations and changing customer preferences.
With the global market becoming increasingly competitive, businesses that can swiftly adapt their production processes to meet specific customer demands gain a significant edge over their competitors.
Key Aspects of Production Planning
Production planning is essentially about making the right product, at the right time, in the right quantity.
This involves careful coordination of various activities such as procurement of raw materials, scheduling of production runs, allocation of resources, and ensuring quality control measures are in place.
The goal is to streamline operations to maximize efficiency while minimizing costs and delays.
Effective production planning requires a deep understanding of capacity constraints, lead times, and inventory levels.
It also necessitates robust communication and collaboration between different departments, such as procurement, manufacturing, and logistics.
By anticipating potential bottlenecks and proactively addressing them, production planners can ensure a smooth and efficient production process.
Integrating BTO and Production Planning
The integration of BTO and production planning is crucial for companies that want to capitalize on the advantages of both approaches.
This requires a holistic view of the entire supply chain, where information flows seamlessly across all levels of the organization.
Here are some strategies that companies can employ to integrate these two crucial processes:
1. Leverage Technology and Data Analytics
In today’s digital age, technology and data analytics play a crucial role in integrating BTO and production planning.
Advanced ERP (Enterprise Resource Planning) systems enable real-time data sharing between departments and provide valuable insights into customer orders, inventory levels, and production capabilities.
Using predictive analytics, companies can forecast demand patterns, identify potential risks, and make informed decisions regarding production schedules and inventory management.
This helps in aligning the BTO process with production planning, ensuring that resources are allocated efficiently to meet customer demands.
2. Foster Collaboration and Communication
For successful integration, it is imperative that all stakeholders within the organization are aligned and working towards a common goal.
Regular meetings and communication channels should be established to ensure that everyone is on the same page.
This includes not only the production and supply chain departments but also sales, marketing, and customer service teams.
By fostering a collaborative environment, companies can ensure that customer orders are accurately relayed to the production team, and any changes in demand are swiftly communicated.
3. Implement Flexible Manufacturing Systems
Flexibility in manufacturing processes is key to accommodating BTO demands while maintaining efficient production planning.
Companies should invest in flexible manufacturing systems that allow for quick reconfiguration of production lines to handle custom orders without significant downtime.
Automation and robotics can also enhance flexibility by enabling faster changeovers and reducing the reliance on manual interventions.
This ensures that production schedules can be quickly adapted to meet changing customer demands without compromising on quality or delivery timelines.
4. Develop a Robust Supply Chain Network
A robust supply chain network is essential for integrating BTO and production planning effectively.
This involves building strong relationships with suppliers to ensure a steady supply of raw materials and components needed for production.
Diversifying the supplier base can also mitigate risks associated with supply disruptions and lead to more competitive pricing.
Additionally, establishing partnerships with logistics providers can help in optimizing transportation routes and reducing delivery times, further aligning the BTO process with production planning.
Challenges and Solutions
Integrating BTO and production planning is not without its challenges.
One of the primary obstacles is the complexity of managing a high level of customization, which can lead to difficulties in standardizing production processes.
Moreover, with shorter production runs, there is a greater risk of errors, which can impact quality and customer satisfaction.
To address these challenges, companies can invest in training programs to upskill their workforce and improve process standardization.
Implementing quality control measures and continuous improvement practices can also help in maintaining high standards and reducing the likelihood of errors.
Furthermore, companies should focus on building a culture of resilience and agility, encouraging employees to embrace change and adapt to new processes and technologies.
By cultivating a forward-thinking mindset, organizations can overcome challenges and succeed in integrating BTO and production planning.
Conclusion
The integration of BTO and production planning is a strategic imperative for supply chain departments aiming to provide high-quality, customized products efficiently.
By leveraging technology, fostering collaboration, implementing flexible manufacturing systems, and developing a robust supply chain network, companies can effectively align these two processes.
While challenges may arise, addressing them through proactive measures such as training and quality control can ensure success.
Ultimately, the seamless integration of BTO and production planning enhances operational efficiency, reduces costs, and maximizes customer satisfaction, providing businesses with a competitive edge in today’s dynamic market.
資料ダウンロード
QCD調達購買管理クラウド「newji」は、調達購買部門で必要なQCD管理全てを備えた、現場特化型兼クラウド型の今世紀最高の購買管理システムとなります。
ユーザー登録
調達購買業務の効率化だけでなく、システムを導入することで、コスト削減や製品・資材のステータス可視化のほか、属人化していた購買情報の共有化による内部不正防止や統制にも役立ちます。
NEWJI DX
製造業に特化したデジタルトランスフォーメーション(DX)の実現を目指す請負開発型のコンサルティングサービスです。AI、iPaaS、および先端の技術を駆使して、製造プロセスの効率化、業務効率化、チームワーク強化、コスト削減、品質向上を実現します。このサービスは、製造業の課題を深く理解し、それに対する最適なデジタルソリューションを提供することで、企業が持続的な成長とイノベーションを達成できるようサポートします。
オンライン講座
製造業、主に購買・調達部門にお勤めの方々に向けた情報を配信しております。
新任の方やベテランの方、管理職を対象とした幅広いコンテンツをご用意しております。
お問い合わせ
コストダウンが利益に直結する術だと理解していても、なかなか前に進めることができない状況。そんな時は、newjiのコストダウン自動化機能で大きく利益貢献しよう!
(Β版非公開)