- お役立ち記事
- How to effectively implement TQM and improve quality that quality assurance department managers should know
How to effectively implement TQM and improve quality that quality assurance department managers should know
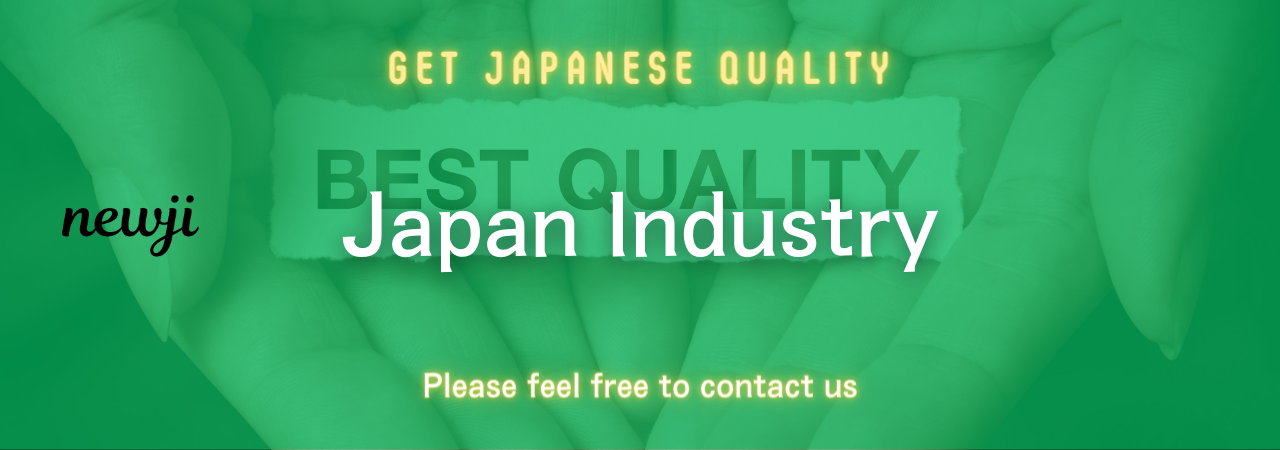
目次
Understanding TQM: Total Quality Management
Total Quality Management, or TQM, is a comprehensive approach to improving the performance of an organization by focusing on customer satisfaction, process optimization, and continual improvement.
TQM emphasizes the integration of all organizational functions, including marketing, finance, design, engineering, and production, to achieve customer satisfaction.
This approach ensures that quality becomes the responsibility of every employee.
For quality assurance department managers, implementing TQM effectively means embedding quality into the organization’s structure and culture.
It’s more than just a set of standards; it involves a holistic approach to building a quality-oriented mindset across the company.
The Core Principles of TQM
To successfully implement TQM, it’s important to understand its core principles.
These principles guide the adoption and application of quality improvement processes.
1. Customer Focus
Every organization that adopts TQM needs to prioritize its customers.
Understanding customer needs and expectations is crucial.
This means not only meeting customer requirements but exceeding them.
Feedback mechanisms should be well-established to grasp the voice of the customer and apply it to the improvement strategies.
2. Total Employee Involvement
Employees at all levels are the backbone of TQM.
Their full involvement enables their abilities to be used for the organization’s benefit.
Empowering employees through training, sharing knowledge, and involving them in decision-making processes facilitates their dedication to quality improvements.
3. Process-Centered Approach
A fundamental part of TQM is focusing on process thinking.
Organizations should consider processes as a set of activities that turn inputs into outputs.
By optimizing these processes, quality can be enhanced throughout the entire company.
Routine process evaluations and analyses play a crucial role in identifying areas for improvement.
4. Integrated System
An integrated system aligns all processes across the organization with its strategic objectives.
This system-oriented approach ensures that quality is consistent and aligned across all departments and functions.
Integration typically requires collaboration and breaking down silos within the company.
5. Continual Improvement
TQM is an ongoing journey where the focus is on continual improvement.
Organizations must strive for incremental improvement in their processes, products, or services.
This could be facilitated through methodologies like Kaizen, Lean, or Six Sigma, which focus on decreasing waste and increasing efficiency.
6. Fact-Based Decision Making
Decisions related to quality enhancements should rely on data, not assumptions.
By analyzing data accurately, organizations can understand trends, identify areas of concern, and track improvements.
Quality assurance managers should cultivate a culture where data-driven decisions are the norm.
7. Communication
Effective communication is the foundation of TQM.
Clear communication of strategies, methods, and planned improvements ensures that everyone in the organization is aligned with the common goals.
It’s also important for relaying progress and for motivating employees to contribute.
Steps to Implement TQM Effectively
Implementing TQM requires structured steps and consistent effort.
Here are the strategies that quality assurance department managers can employ to enhance quality successfully:
1. Getting Top Management Commitment
For TQM to be successfully implemented, it requires commitment from the top.
Quality should be a priority that is led by example from the executives, who must foster an environment conducive to quality improvement.
2. Developing a Clear Vision and Mission
Organizations must create a clear vision that underscores the importance of quality.
This vision should be communicated regularly and integrated into the company’s mission.
3. Conducting Training and Development Programs
Training is essential to build competency in quality management techniques.
Conducting workshops and training not only equips employees with the necessary skills but also reinforces the importance of quality.
4. Creating Cross-Functional Teams
Forming cross-functional teams encourages collaboration among departments.
These teams can tackle quality issues, leverage varied expertise, and implement solutions effectively.
5. Establishing a Systematic Measurement and Feedback System
A systematic approach to measure quality improvements is crucial.
Setting up reliable metrics and key performance indicators (KPIs) helps in assessing the progress of TQM initiatives.
6. Encouraging Simple Problem-Solving Tools
Tools such as the Plan-Do-Check-Act (PDCA) cycle, root cause analysis, and cause-and-effect diagrams are simple yet effective in tackling quality issues.
Managers should encourage the usage of these tools across the organization.
7. Fostering a Change-Embracing Culture
For TQM to be ingrained, there should be a culture that embraces change.
This involves breaking down resistance and empowering employees to take risks and innovate.
Overcoming Challenges in TQM Implementation
Implementing TQM can encounter barriers, and understanding these challenges helps in devising effective countermeasures.
Resistance to Change
Employees may resist changes proposed by TQM because it demands altering the current ways of working.
Open communication, training, and support are crucial to overcoming this resistance.
Ineffective Communication
Poor communication can derail TQM efforts.
Ensuring transparent and consistent communication helps keep all stakeholders informed and aligned.
Lack of Resources
Sometimes, inadequate resources such as time, budget, or personnel can hinder TQM implementation.
Proper planning and prioritization are essential to allocate resources effectively.
Conclusion
Total Quality Management is a robust framework that, when implemented effectively, can lead to superior product quality, increased customer satisfaction, and holistic improvement within organizations.
Quality assurance department managers hold a critical role in advocating and steering TQM adoption.
By embedding quality into every process and empowering employees, organizations can achieve sustainable improvements and operational excellence.
資料ダウンロード
QCD調達購買管理クラウド「newji」は、調達購買部門で必要なQCD管理全てを備えた、現場特化型兼クラウド型の今世紀最高の購買管理システムとなります。
ユーザー登録
調達購買業務の効率化だけでなく、システムを導入することで、コスト削減や製品・資材のステータス可視化のほか、属人化していた購買情報の共有化による内部不正防止や統制にも役立ちます。
NEWJI DX
製造業に特化したデジタルトランスフォーメーション(DX)の実現を目指す請負開発型のコンサルティングサービスです。AI、iPaaS、および先端の技術を駆使して、製造プロセスの効率化、業務効率化、チームワーク強化、コスト削減、品質向上を実現します。このサービスは、製造業の課題を深く理解し、それに対する最適なデジタルソリューションを提供することで、企業が持続的な成長とイノベーションを達成できるようサポートします。
オンライン講座
製造業、主に購買・調達部門にお勤めの方々に向けた情報を配信しております。
新任の方やベテランの方、管理職を対象とした幅広いコンテンツをご用意しております。
お問い合わせ
コストダウンが利益に直結する術だと理解していても、なかなか前に進めることができない状況。そんな時は、newjiのコストダウン自動化機能で大きく利益貢献しよう!
(Β版非公開)