- お役立ち記事
- A must-see for project leaders in the design department! How to meet customer requirements using quality function deployment (QFD)
A must-see for project leaders in the design department! How to meet customer requirements using quality function deployment (QFD)
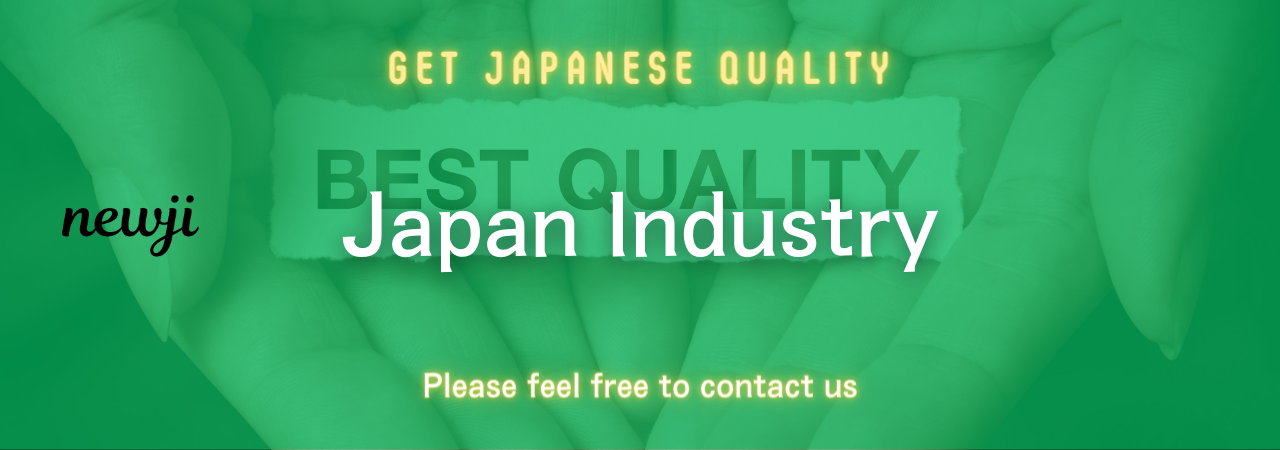
目次
Understanding Quality Function Deployment (QFD)
Quality Function Deployment, commonly known as QFD, is an essential tool for project leaders, particularly those in design departments, aiming to effectively meet customer requirements.
This methodology enables project teams to transform customer needs into specific engineering and technical requirements.
The goal is to ensure that the final product or service is in complete alignment with what the customer desires.
QFD focuses on listening to customer needs, translating them into design specifications, and distributing these specifications throughout the development cycle.
By doing so, it not only improves product quality but also enhances customer satisfaction and reduces the risk of costly changes later in the project.
The Importance of Understanding Customer Needs
Before diving into the mechanics of QFD, it’s crucial to emphasize the importance of understanding customer needs.
In the competitive world of product design and development, the market is saturated with options for consumers.
Therefore, identifying and meeting customer needs is a competitive advantage.
Project leaders must ensure they thoroughly understand the customer’s perspective to craft products or services that stand out.
Through surveys, feedback, interviews, and focus groups, teams can gather valuable insights that shape the project’s trajectory.
Integrating this customer feedback at the outset prevents miscommunications and ensures that the final deliverable truly addresses the intended requirements.
The Phases of Quality Function Deployment
QFD is organized into four primary phases, often visualized using a tool called the “House of Quality.”
These phases help project leaders systematically address customer requirements and translate them into actionable tasks.
1. Product Planning (House of Quality)
The first phase is the heart of the QFD process, where the focus is on understanding and prioritizing customer needs.
This involves creating a House of Quality matrix, a visual representation comparing customer wants against the company’s ability to fulfill those wants.
By doing this, project leaders can identify which product characteristics are most crucial to focus on.
2. Product Design
In this phase, the focus shifts to developing design specifications based on the prioritized customer needs identified in the first stage.
Project teams work on translating those needs into tangible design elements, such as size, features, and materials.
This integration ensures that the product design aligns perfectly with what the customer is looking for.
3. Process Planning
Once the design specifications are clear, the next step is to plan the manufacturing process.
This phase ensures that the production capabilities match the desired product specifications.
It involves detailing how the product will be manufactured and what processes and resources are necessary.
By aligning the process planning stage with customer needs, companies can eliminate inefficiencies and avoid defects.
4. Production Planning
The final phase involves setting up the controls and quality measures to ensure that the product meets all predefined specifications.
It includes setting standards for production, testing, and validation to ensure that the product not only meets but exceeds customer expectations.
Incorporating quality measures at this stage ensures that the final product aligns with the original designs and customer requirements.
Benefits of Using Quality Function Deployment
QFD offers numerous benefits to project leaders and design departments.
By using QFD, companies can ensure that their products are more closely aligned with customer needs.
This alignment usually leads to increased customer satisfaction and loyalty.
QFD also helps in prioritizing efforts and resources, leading to more efficient project execution.
It minimizes misunderstandings and misalignments during the product development cycle, which translates to shorter development times and reduced costs.
This structured approach to quality and design ensures that the end product not only meets but often exceeds customer expectations, providing a competitive advantage in the marketplace.
Challenges and Limitations
Like any methodology, QFD has its challenges and limitations.
Implementing QFD effectively requires a deep understanding of both customer needs and technical specifications, which can be resource-intensive.
Moreover, if the initial information or customer feedback is not accurate, the entire process can be derailed.
This method also requires cross-functional collaboration which can be difficult to coordinate, especially in larger organizations with complex structures.
Despite these challenges, with proper training and commitment, these obstacles can be overcome to maximize the benefits of QFD.
Implementing QFD in Your Projects
To successfully implement QFD, project leaders should start by assembling a cross-functional team.
This team should include members from various departments such as design, engineering, and marketing.
Training the team on the principles of QFD and familiarizing them with tools like the House of Quality is crucial.
The data collected from customer interactions must be comprehensive and accurate, serving as the foundation for the QFD process.
By effectively managing this process, and maintaining a clear focus on the customer throughout, project leaders can successfully meet and exceed customer requirements using QFD.
In today’s competitive market, utilizing methodologies like QFD can be the differentiator that sets a company apart, ensuring robust product design and development that is both customer-focused and quality-driven.
資料ダウンロード
QCD調達購買管理クラウド「newji」は、調達購買部門で必要なQCD管理全てを備えた、現場特化型兼クラウド型の今世紀最高の購買管理システムとなります。
ユーザー登録
調達購買業務の効率化だけでなく、システムを導入することで、コスト削減や製品・資材のステータス可視化のほか、属人化していた購買情報の共有化による内部不正防止や統制にも役立ちます。
NEWJI DX
製造業に特化したデジタルトランスフォーメーション(DX)の実現を目指す請負開発型のコンサルティングサービスです。AI、iPaaS、および先端の技術を駆使して、製造プロセスの効率化、業務効率化、チームワーク強化、コスト削減、品質向上を実現します。このサービスは、製造業の課題を深く理解し、それに対する最適なデジタルソリューションを提供することで、企業が持続的な成長とイノベーションを達成できるようサポートします。
オンライン講座
製造業、主に購買・調達部門にお勤めの方々に向けた情報を配信しております。
新任の方やベテランの方、管理職を対象とした幅広いコンテンツをご用意しております。
お問い合わせ
コストダウンが利益に直結する術だと理解していても、なかなか前に進めることができない状況。そんな時は、newjiのコストダウン自動化機能で大きく利益貢献しよう!
(Β版非公開)