- お役立ち記事
- For quality control department leaders! An effective approach to quality control using seven QC tools
For quality control department leaders! An effective approach to quality control using seven QC tools
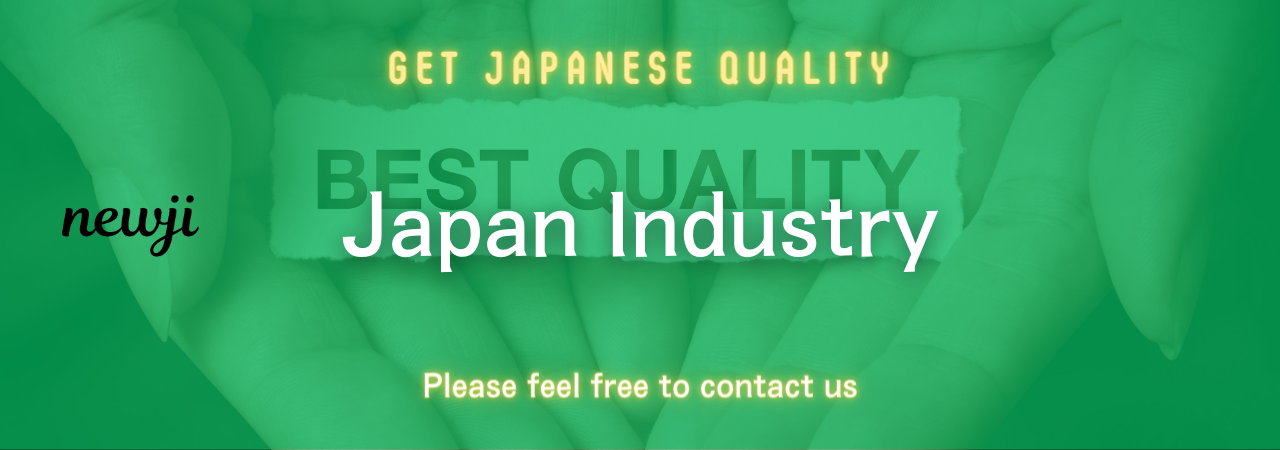
目次
Introduction to Quality Control and the Seven QC Tools
In today’s competitive market, quality control is crucial for any organization aiming for success and customer satisfaction.
Quality control ensures that products and services meet the required standards and specifications.
As leaders in the quality control department, it is your responsibility to implement effective strategies that ensure consistency and reliability.
One proven approach is the use of the seven QC tools.
These tools are fundamental techniques used to improve processes and resolve quality-related issues.
Understanding the Importance of Quality Control
Quality control is essential in maintaining customer trust and loyalty.
When products meet high standards, customers are more likely to continue using them and recommend them to others.
Moreover, effective quality control minimizes errors, reduces waste, and saves costs associated with product recalls and defects.
By implementing the seven QC tools, leaders can identify areas for improvement and make informed decisions to enhance quality.
The Seven QC Tools Explained
The seven QC tools are a set of problem-solving instruments that aid in quality management.
These tools are simple yet powerful methods that help in data collection, analysis, and decision-making.
Let’s delve into each one of them:
1. Check Sheets
Check sheets are used for data collection and analysis.
They provide a structured way to gather and record data effectively.
By using check sheets, quality control professionals can identify patterns, trends, and common issues in the production process.
They are useful for monitoring defect occurrences, everyday operations, and process stability.
2. Pareto Charts
Pareto charts are graphical representations that highlight the most significant factors in a data set.
Based on the Pareto principle or the 80/20 rule, these charts help identify the vital few causes that lead to the majority of problems.
Using Pareto charts allows leaders to prioritize issues and allocate resources efficiently for maximum impact.
3. Cause and Effect Diagrams
Also known as fishbone or Ishikawa diagrams, cause and effect diagrams help in identifying the root causes of a problem.
By visually mapping out potential causes, quality control teams can analyze different factors contributing to a defect or failure.
This tool encourages brainstorming and helps in pinpointing areas for corrective actions.
4. Control Charts
Control charts are used to monitor process performance over time.
They help in identifying variations in processes, whether they are due to common causes or special causes.
By using control charts, quality control leaders can distinguish between normal process fluctuations and outliers that signify problems, enabling timely interventions.
5. Histograms
Histograms are bar graphs that display the distribution of data points across different intervals.
They provide insights into the frequency, shape, and spread of data, allowing for an easy-to-understand visual comparison.
Histograms are valuable for understanding process variations and identifying possible deviations from desired outcomes.
6. Scatter Diagrams
Scatter diagrams visually represent the relationship between two variables.
They help in identifying potential correlations and patterns in data.
By analyzing scatter diagrams, quality control professionals can determine whether changes in one variable might affect another, aiding in process optimization and improvement.
7. Flowcharts
Flowcharts depict the steps in a process through diagrams, making complex workflows easier to understand.
They help in identifying unnecessary steps, bottlenecks, or opportunities for streamlining operations.
Flowcharts facilitate communication among team members and enhance process clarity and efficiency.
Implementing the Seven QC Tools
To effectively implement these tools in your quality control processes, you should follow a structured approach:
Step 1: Training and Development
Begin by training your team on how to use each of these tools effectively.
Organize workshops or seminars to educate them on the applications and benefits of each tool.
Providing hands-on experiences helps build confidence and encourages active participation in the quality control process.
Step 2: Data Collection and Analysis
Encourage your team to gather relevant data using the appropriate QC tools.
Ensure the data is accurate and representative of your processes.
Analyze the data collected to understand the current state of quality within your organization.
Step 3: Problem Identification and Prioritization
Utilize tools like Pareto charts and cause and effect diagrams to identify key issues affecting quality.
Prioritize these problems based on their potential impact on production and customer satisfaction.
Step 4: Implement Solutions and Monitor Progress
Develop actionable solutions based on your analysis and implement changes to improve quality.
Use control charts and flowcharts to monitor the outcomes and ensure ongoing process stability.
Regularly evaluate the effectiveness of implemented solutions and make adjustments as needed.
Step 5: Continuous Improvement
Quality control is an ongoing process.
Continuously seek opportunities for improvement by revisiting the seven QC tools.
Foster a culture of continuous improvement within your team and encourage them to suggest innovative ideas for enhancing quality.
Conclusion
By mastering the seven QC tools, quality control department leaders can effectively address issues, streamline processes, and ensure high-quality products and services.
These tools provide a structured approach to data collection, analysis, and problem-solving.
When implemented correctly, they contribute to organizational success, customer satisfaction, and competitiveness in the market.
As quality control leaders, leveraging these tools empowers you to make informed decisions and drive continuous improvement in your operations.
資料ダウンロード
QCD調達購買管理クラウド「newji」は、調達購買部門で必要なQCD管理全てを備えた、現場特化型兼クラウド型の今世紀最高の購買管理システムとなります。
ユーザー登録
調達購買業務の効率化だけでなく、システムを導入することで、コスト削減や製品・資材のステータス可視化のほか、属人化していた購買情報の共有化による内部不正防止や統制にも役立ちます。
NEWJI DX
製造業に特化したデジタルトランスフォーメーション(DX)の実現を目指す請負開発型のコンサルティングサービスです。AI、iPaaS、および先端の技術を駆使して、製造プロセスの効率化、業務効率化、チームワーク強化、コスト削減、品質向上を実現します。このサービスは、製造業の課題を深く理解し、それに対する最適なデジタルソリューションを提供することで、企業が持続的な成長とイノベーションを達成できるようサポートします。
オンライン講座
製造業、主に購買・調達部門にお勤めの方々に向けた情報を配信しております。
新任の方やベテランの方、管理職を対象とした幅広いコンテンツをご用意しております。
お問い合わせ
コストダウンが利益に直結する術だと理解していても、なかなか前に進めることができない状況。そんな時は、newjiのコストダウン自動化機能で大きく利益貢献しよう!
(Β版非公開)