- お役立ち記事
- For mid-level employees in the facility management department! Fundamentals of reliability engineering to maximize equipment availability
For mid-level employees in the facility management department! Fundamentals of reliability engineering to maximize equipment availability
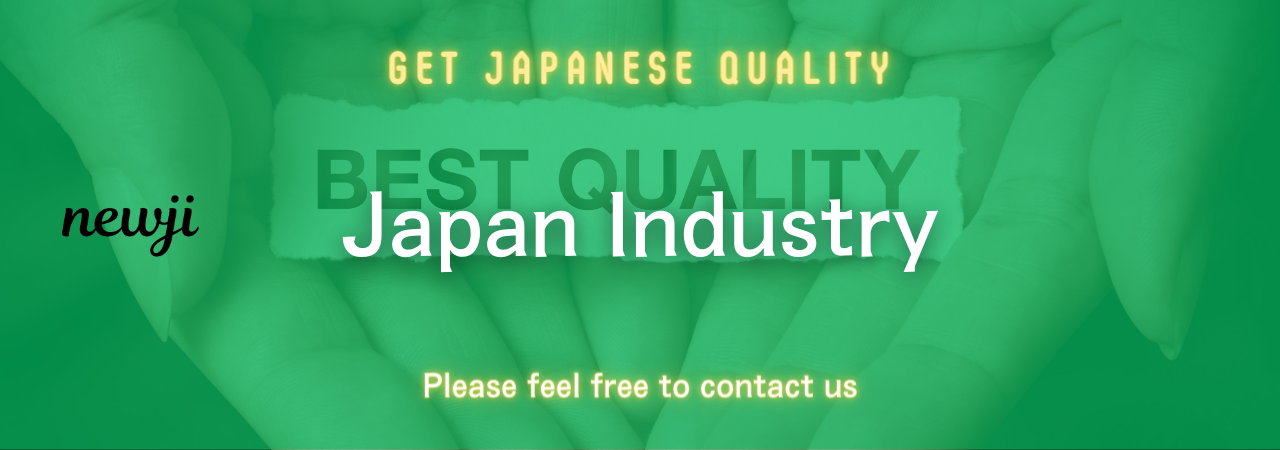
目次
Understanding Reliability Engineering
Reliability engineering is an essential discipline that focuses on ensuring that equipment and systems perform their intended functions without failure over a specified period.
For mid-level employees in the facility management department, having a grasp of reliability engineering fundamentals is crucial to maximizing equipment availability and optimizing maintenance strategies.
Reliability engineering involves various techniques and methodologies aimed at improving the reliability of systems.
It encompasses the design, analysis, and maintenance of systems to minimize the likelihood of failure.
By understanding the principles of reliability engineering, facility managers can make informed decisions about equipment maintenance and improve overall operational efficiency.
The Role of Reliability in Facility Management
In facility management, reliability is a key factor that influences the performance and longevity of equipment.
High reliability in equipment ensures minimal downtime, reduces maintenance costs, and improves safety.
Facility managers must prioritize equipment reliability to achieve these objectives.
Reliability engineering helps identify potential failure modes and vulnerabilities in equipment.
By analyzing historical data and conducting reliability assessments, facility managers can predict failure patterns and implement preventive measures.
This proactive approach minimizes unexpected breakdowns and extends the life of equipment.
Key Concepts in Reliability Engineering
To effectively apply reliability engineering principles in facility management, it is important to understand some key concepts:
1. **Reliability Function**: This mathematical representation describes the probability that a system or component will function successfully without failure for a specific period.
2. **Failure Rate**: This measures the frequency at which a component or system fails over a given time.
A lower failure rate indicates higher reliability.
3. **Mean Time to Failure (MTTF)**: MTTF is the average time that a non-repairable system or component is expected to operate before it fails.
For repairable systems, Mean Time Between Failures (MTBF) is used.
4. **Availability**: Availability is the degree to which a system is operational and accessible when needed for use.
It is closely linked to reliability and is a key performance indicator in facility management.
5. **Reliability Block Diagrams (RBDs)**: RBDs are graphical representations used to model the reliability of complex systems.
They help visualize and analyze how different components contribute to the overall system reliability.
Benefits of Implementing Reliability Engineering
Implementing reliability engineering in facility management offers numerous benefits:
1. **Enhanced Equipment Performance**: By monitoring and analyzing reliability metrics, facility managers can optimize maintenance schedules and improve equipment performance.
2. **Cost Savings**: Proactive maintenance strategies reduce the risk of failures and minimize repair costs.
Reliability engineering helps in identifying cost-effective solutions to extend equipment life.
3. **Improved Safety**: Reliable systems are less prone to accidents and malfunctions, ensuring a safer environment for workers and users of the facility.
4. **Increased Operational Efficiency**: With high equipment availability, facilities can operate more efficiently, meeting demands without interruptions.
5. **Data-Driven Decision Making**: Reliability engineering relies on data analysis, empowering facility managers with actionable insights to make informed decisions.
Steps to Implement Reliability Engineering in Facility Management
To effectively implement reliability engineering within a facility management context, consider the following steps:
1. Collect and Analyze Data
Gather historical data on equipment performance, maintenance records, and failure incidents.
Use this data to identify trends, recurring issues, and potential failure points.
Advanced analytics tools can aid in this process, providing insights that are vital for determining reliability improvements.
2. Conduct Reliability Assessments
Perform reliability assessments to evaluate the current state of equipment and identify vulnerabilities.
Techniques like Failure Modes, Effects, and Criticality Analysis (FMECA) and Fault Tree Analysis (FTA) can be implemented to determine the likelihood and impact of failures.
3. Develop a Preventive Maintenance Plan
Based on the analysis, create a preventive maintenance plan that addresses the identified failure modes.
This plan should include regular inspections, tests, and replacements before equipment reaches critical failure stages.
4. Implement Predictive Maintenance Techniques
Leverage predictive maintenance techniques using real-time data and condition monitoring technologies.
This approach allows for the early detection of anomalies, enabling timely interventions to prevent equipment failures.
5. Train Staff and Foster a Reliability Culture
Educate facility management teams and staff on the importance of reliability engineering.
Invest in training programs that equip employees with the skills to perform reliability assessments and maintenance tasks effectively.
Promote a culture that values equipment reliability as a key component of operational excellence.
Conclusion
For mid-level employees in the facility management department, understanding and applying reliability engineering principles can significantly impact equipment availability and performance.
By incorporating reliability assessments, proactive maintenance, and data-driven decision-making into their practices, facility managers can ensure their facilities operate smoothly and efficiently.
Embracing reliability engineering helps create resilient systems that can withstand challenges, ultimately leading to cost savings, improved safety, and heightened operational success.
With the fundamentals of reliability engineering in hand, facility managers can confidently navigate the complexities of managing essential equipment and infrastructure.
資料ダウンロード
QCD調達購買管理クラウド「newji」は、調達購買部門で必要なQCD管理全てを備えた、現場特化型兼クラウド型の今世紀最高の購買管理システムとなります。
ユーザー登録
調達購買業務の効率化だけでなく、システムを導入することで、コスト削減や製品・資材のステータス可視化のほか、属人化していた購買情報の共有化による内部不正防止や統制にも役立ちます。
NEWJI DX
製造業に特化したデジタルトランスフォーメーション(DX)の実現を目指す請負開発型のコンサルティングサービスです。AI、iPaaS、および先端の技術を駆使して、製造プロセスの効率化、業務効率化、チームワーク強化、コスト削減、品質向上を実現します。このサービスは、製造業の課題を深く理解し、それに対する最適なデジタルソリューションを提供することで、企業が持続的な成長とイノベーションを達成できるようサポートします。
オンライン講座
製造業、主に購買・調達部門にお勤めの方々に向けた情報を配信しております。
新任の方やベテランの方、管理職を対象とした幅広いコンテンツをご用意しております。
お問い合わせ
コストダウンが利益に直結する術だと理解していても、なかなか前に進めることができない状況。そんな時は、newjiのコストダウン自動化機能で大きく利益貢献しよう!
(Β版非公開)