- お役立ち記事
- For managers of design departments in electronic equipment manufacturing industries! Flip-chip technology implementation and thermal management points
For managers of design departments in electronic equipment manufacturing industries! Flip-chip technology implementation and thermal management points
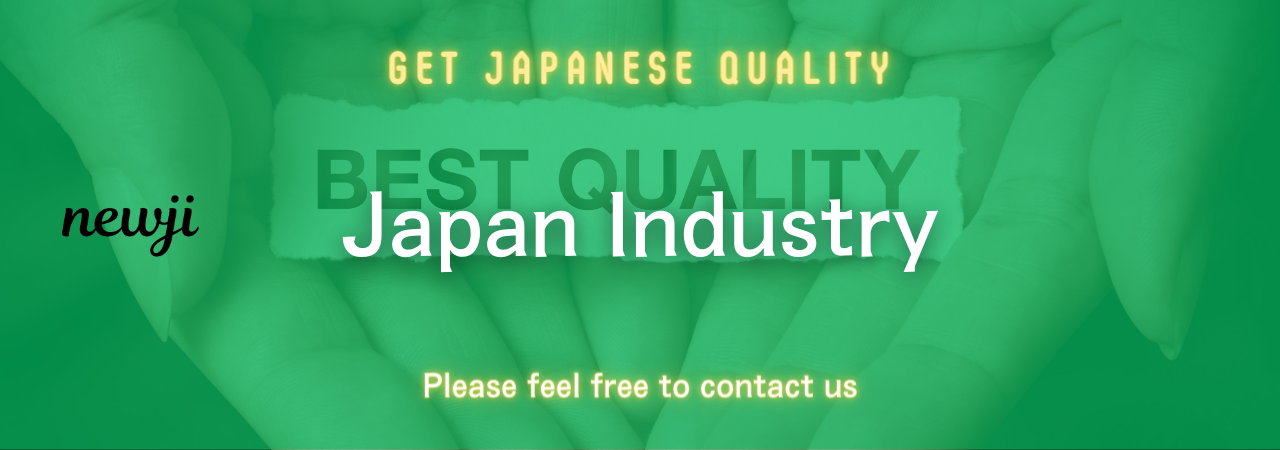
目次
Understanding Flip-Chip Technology
Flip-chip technology is an advanced method for connecting semiconductor devices to external circuitry.
Unlike traditional assembly techniques, this method involves placing the chip face down, hence the name “flip-chip.”
This process allows for shorter, more efficient connections between the chip and the substrate.
In the context of electronic equipment manufacturing, flip-chip technology provides several advantages.
It offers improved performance, higher frequencies, and reduced power consumption.
The compact nature of this approach also contributes to the miniaturization of electronic components, which is crucial in the ever-evolving world of technology.
For design managers in the electronic equipment industry, successfully implementing flip-chip technology can be a game-changer.
It empowers them to create products that are not only efficient but also competitive in terms of performance.
Key Steps in Implementing Flip-Chip Technology
Implementing flip-chip technology in your design department involves several critical steps.
These steps are crucial for ensuring that the process is effective and that the final product meets the desired standards.
1. Design and Simulation
Before physical implementation, it’s essential to carry out comprehensive design and simulation.
This step involves using CAD tools to model and simulate the flip-chip assembly.
Through simulation, potential issues can be identified and rectified early in the design phase.
This not only saves time but also reduces costs associated with redesigning and prototyping.
2. Selection of Materials
Choosing the right materials is paramount in implementing flip-chip technology.
Materials like the solder bumps, substrate, and underfill play vital roles in the reliability and performance of the final product.
Therefore, it is important to conduct thorough research and testing to ensure that the materials used can withstand thermal and mechanical stresses.
3. Bumping Process
The bumping process involves depositing solder or other conductive materials onto the chip’s pads.
It’s a critical step as it establishes the connection between the chip and the substrate.
Smooth and reliable solder bumps are essential for the electrical and mechanical integrity of the device.
4. Assembly and Bonding
Once the bumping process is complete, the chip is flipped and aligned onto the substrate.
Bonding techniques, such as thermocompression or ultrasonic bonding, are then used to ensure a secure connection.
Precision during this step is crucial to achieving a high-quality and functional electronic component.
5. Testing and Quality Assurance
Finally, rigorous testing must be conducted to ensure that the flip-chip assembly operates as intended.
Quality assurance processes, such as thermal cycling and mechanical stress testing, help validate the device’s performance under various conditions.
Thermal Management in Flip-Chip Technology
Thermal management is a key concern when dealing with flip-chip technology.
As electronic devices become smaller and more powerful, effectively dissipating heat becomes increasingly important.
Failure to manage thermal performance can lead to issues such as device malfunction, reduced lifespan, and compromised safety.
1. Heat Sink Design
One effective method of managing thermal performance is through the design of efficient heat sinks.
Heat sinks help dissipate heat away from the chip, maintaining the temperature within safe operating limits.
Designers must consider factors such as material selection and geometry to optimize heat sink efficacy.
2. Advanced Materials
In recent years, advanced materials with high thermal conductivity have been explored for use in flip-chip modules.
Materials like copper and aluminum are often used due to their excellent heat dissipation properties.
Incorporating these materials into your design can significantly enhance the thermal management of electronic devices.
3. Thermal Interface Materials (TIMs)
Thermal interface materials are placed between the chip and the heat sink to improve thermal conductivity.
These materials help reduce the thermal resistance at the interface, enabling more efficient heat transfer.
Selecting the right TIM based on the application’s requirements is vital for optimal thermal management.
4. Simulation and Testing
To predict thermal performance, simulation tools can be employed during the design phase.
These tools allow designers to model heat flow and identify potential thermal bottlenecks.
Subsequent testing, under real-world conditions, verifies the effectiveness of thermal management strategies.
Conclusion
For managers of design departments in the electronic equipment manufacturing industry, harnessing flip-chip technology and mastering thermal management principles are essential for success.
By following the key implementation steps and focusing on efficient thermal management, you can produce high-performance, reliable, and competitive electronic components.
Stay ahead in the rapidly evolving field of electronics by implementing these advanced technologies in your design processes.
資料ダウンロード
QCD調達購買管理クラウド「newji」は、調達購買部門で必要なQCD管理全てを備えた、現場特化型兼クラウド型の今世紀最高の購買管理システムとなります。
ユーザー登録
調達購買業務の効率化だけでなく、システムを導入することで、コスト削減や製品・資材のステータス可視化のほか、属人化していた購買情報の共有化による内部不正防止や統制にも役立ちます。
NEWJI DX
製造業に特化したデジタルトランスフォーメーション(DX)の実現を目指す請負開発型のコンサルティングサービスです。AI、iPaaS、および先端の技術を駆使して、製造プロセスの効率化、業務効率化、チームワーク強化、コスト削減、品質向上を実現します。このサービスは、製造業の課題を深く理解し、それに対する最適なデジタルソリューションを提供することで、企業が持続的な成長とイノベーションを達成できるようサポートします。
オンライン講座
製造業、主に購買・調達部門にお勤めの方々に向けた情報を配信しております。
新任の方やベテランの方、管理職を対象とした幅広いコンテンツをご用意しております。
お問い合わせ
コストダウンが利益に直結する術だと理解していても、なかなか前に進めることができない状況。そんな時は、newjiのコストダウン自動化機能で大きく利益貢献しよう!
(Β版非公開)