- お役立ち記事
- Strategies for lightweight design using CAE that should be addressed by design department leaders in the automotive industry
Strategies for lightweight design using CAE that should be addressed by design department leaders in the automotive industry
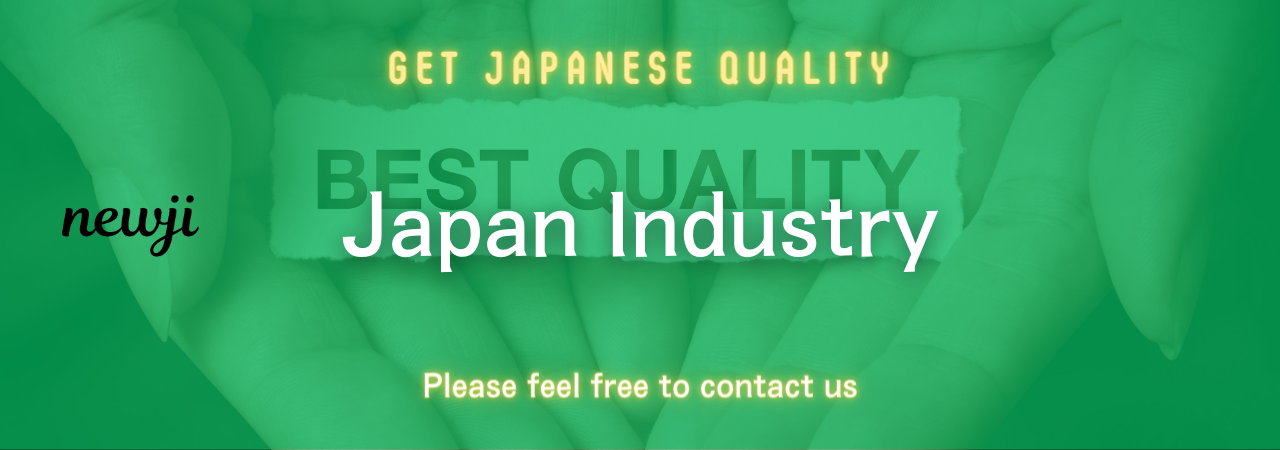
目次
Understanding the Importance of Lightweight Design in the Automotive Industry
In today’s automotive industry, the push for efficiency, sustainability, and performance is stronger than ever.
Cars are not just about speed or style anymore; they need to meet stringent environmental regulations, provide better fuel efficiency, and enhance driving dynamics.
One of the most effective ways to achieve these goals is through lightweight design.
By reducing the weight of vehicles, manufacturers can improve fuel efficiency, reduce emissions, and even enhance vehicle safety.
For design department leaders in the automotive industry, adopting strategies for lightweight design using Computer-Aided Engineering (CAE) is essential.
The Role of CAE in Lightweight Design
Computer-Aided Engineering plays a crucial role in the development of lightweight automotive designs.
Through CAE tools, engineers can simulate, analyze, and optimize designs, ensuring that vehicles meet all necessary performance criteria while reducing weight.
CAE allows for the exploration of different materials and design alternatives without the need for physical prototypes, saving both time and cost.
Incorporating CAE into the design process enables a more iterative and efficient design workflow.
Designers can test different scenarios, modify materials, and adjust geometries in a virtual environment, which leads to more innovative and creative solutions.
For design department leaders, understanding how to leverage CAE is fundamental to driving successful lightweight initiatives.
Optimizing Material Choices
One of the key strategies for achieving lightweight automotive design is optimizing material choices.
Using materials like aluminum, high-strength steel, and advanced composites can significantly reduce the weight of a vehicle while maintaining structural integrity.
CAE software allows engineers to test various material combinations and predict how they will perform under different conditions.
The advantage here is that design leaders can evaluate the trade-offs between cost, weight, and performance.
By integrating insights from CAE analysis, teams can select materials that meet the specific requirements of each component, resulting in a balanced and effective lightweight design.
Structural Optimization for Weight Reduction
Structural optimization is another crucial aspect where CAE stands out.
Through techniques like topology optimization, engineers can find the best material distribution within a given design space to minimize weight and maintain stiffness and strength.
CAE tools enable design departments to identify areas where material can be removed without compromising safety or functionality.
For design department leaders, encouraging the use of structural optimization methods can lead to innovative designs that are not only lighter but also offer improved performance.
This proactive approach helps ensure that weight reduction does not come at the expense of quality or safety.
Integrating Multidisciplinary Design Optimization (MDO)
Multidisciplinary Design Optimization is an advanced CAE strategy that simultaneously considers various engineering disciplines such as aerodynamics, structural integrity, and acoustics.
By using MDO in the design process, engineers can achieve a holistic approach to lightweight design.
This ensures that all aspects of the vehicle’s performance are optimized together rather than individually.
For design leaders, promoting MDO within the design team can foster collaboration and innovation.
When different disciplines work together from the outset of the design phase, the end product is more likely to meet all performance targets while maintaining a reduced weight profile.
Overcoming Challenges in Lightweight Design
While the benefits of lightweight design are numerous, the challenges cannot be overlooked.
Some common obstacles include cost implications of advanced materials, potential compromises on noise, vibration, and harshness (NVH), and meeting crash safety standards.
CAE tools can be incredibly valuable in overcoming these challenges by providing detailed simulations and early prediction of potential issues.
Balancing Cost and Performance
Advanced lightweight materials can be more expensive than traditional options.
Design department leaders need to balance cost with the performance benefits of these materials.
Through CAE, teams can simulate and analyze cost-effective alternatives and understand where using premium materials makes the most sense financially and performance-wise.
Addressing NVH Concerns
Reducing weight sometimes leads to increased NVH, which can negatively impact the driving experience.
CAE simulations can predict NVH levels early in the design process, enabling teams to address potential issues proactively.
By understanding the NVH implications of different design choices, engineers can implement solutions that mitigate negative effects while continuing to focus on weight reduction.
Ensuring Safety Compliance
Safety is non-negotiable in automotive design, and crashworthiness cannot be compromised for the sake of weight savings.
CAE allows for comprehensive crash simulations that help ensure that lighter vehicles can still perform well in safety tests.
This helps design departments develop designs that are both lightweight and safe, meeting all necessary regulatory standards.
Implementing CAE-Driven Strategies
Design department leaders must play a pivotal role in implementing CAE-driven lightweight design strategies.
They need to foster a culture of innovation and continuous learning within their teams to ensure sustainable success.
Leaders can achieve this by providing access to the latest CAE tools, encouraging cross-disciplinary collaboration, and investing in training and development for their staff.
Moreover, by setting clear objectives aligned with the organization’s overall goals, leaders can guide their teams strategically.
This alignment ensures that every lightweight initiative undertaken through CAE contributes meaningfully to the company’s vision and enhances product competitiveness in the market.
The Future of Lightweight Design with CAE
As technology continues to evolve, the capabilities of CAE will only expand.
Future advancements in simulation accuracy, real-time data processing, and even AI-driven design insights promise to revolutionize how lightweight automotive designs are developed.
For leaders in the design department, staying abreast of these technological trends is critical.
By embracing CAE-driven strategies today, automotive industry leaders can ensure that their teams are prepared for future challenges and opportunities in vehicle design.
This forward-thinking approach not only enhances product performance and sustainability but also positions manufacturers as innovators in a highly competitive industry.
資料ダウンロード
QCD調達購買管理クラウド「newji」は、調達購買部門で必要なQCD管理全てを備えた、現場特化型兼クラウド型の今世紀最高の購買管理システムとなります。
ユーザー登録
調達購買業務の効率化だけでなく、システムを導入することで、コスト削減や製品・資材のステータス可視化のほか、属人化していた購買情報の共有化による内部不正防止や統制にも役立ちます。
NEWJI DX
製造業に特化したデジタルトランスフォーメーション(DX)の実現を目指す請負開発型のコンサルティングサービスです。AI、iPaaS、および先端の技術を駆使して、製造プロセスの効率化、業務効率化、チームワーク強化、コスト削減、品質向上を実現します。このサービスは、製造業の課題を深く理解し、それに対する最適なデジタルソリューションを提供することで、企業が持続的な成長とイノベーションを達成できるようサポートします。
オンライン講座
製造業、主に購買・調達部門にお勤めの方々に向けた情報を配信しております。
新任の方やベテランの方、管理職を対象とした幅広いコンテンツをご用意しております。
お問い合わせ
コストダウンが利益に直結する術だと理解していても、なかなか前に進めることができない状況。そんな時は、newjiのコストダウン自動化機能で大きく利益貢献しよう!
(Β版非公開)