- お役立ち記事
- Roller preventive maintenance and abnormality detection methods that new leaders of equipment maintenance departments in the steel industry should know
Roller preventive maintenance and abnormality detection methods that new leaders of equipment maintenance departments in the steel industry should know
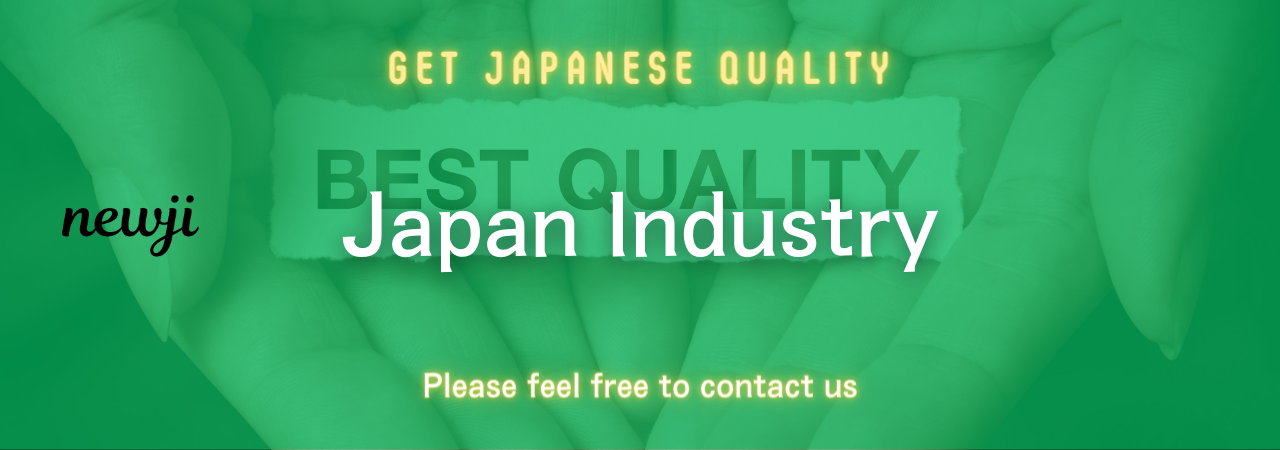
目次
Introduction to Roller Maintenance in the Steel Industry
In the steel industry, ensuring the optimal functioning of rollers is crucial for maintaining smooth operations and prolonging the lifespan of equipment.
As a newly appointed leader in an equipment maintenance department, it is essential to understand preventive maintenance and abnormality detection methods for rollers.
This knowledge will not only help in preventing unexpected breakdowns but will also enhance overall productivity and safety.
The Importance of Preventive Maintenance
Preventive maintenance is a proactive approach to ensure equipment, such as rollers, operates efficiently and reliably.
By regularly inspecting and servicing the equipment, you can identify potential issues before they lead to severe problems or failures.
One of the primary benefits of preventive maintenance is cost savings.
It is much less expensive to conduct regular maintenance checks than to deal with sudden equipment failures, which can result in costly repairs and downtime.
Moreover, preventive maintenance ensures the safety of workers.
Well-maintained equipment reduces the risk of accidents, providing a secure working environment.
Key Components of Roller Preventive Maintenance
Effective roller preventive maintenance involves several critical components:
1. **Regular Inspections**: Conduct thorough inspections to check for signs of wear and tear, misalignments, or unusual noises.
2. **Lubrication**: Ensure that rollers are properly lubricated to minimize friction and wear.
The type of lubricant used should be appropriate for the working conditions and roller materials.
3. **Cleaning**: Regularly clean the rollers to prevent the buildup of dirt, dust, and debris that can affect performance and lead to premature wear.
4. **Calibration and Alignment**: Check the alignment and calibration of rollers.
Misaligned rollers can cause uneven wear and operational inefficiencies.
5. **Replacement of Worn Parts**: Replace worn-out parts before they cause significant damage or lead to equipment failure.
Abnormality Detection in Rollers
Detecting abnormalities promptly is crucial in preventing further damage to the rollers and ensuring continuous operations.
Several methods can be employed to detect abnormalities:
Visual Inspections
Regular visual inspections can reveal signs of wear, damage, or misalignment that might indicate potential issues.
It’s important to train maintenance personnel to recognize these signs and know what corrective actions to take.
Vibration Analysis
Vibration analysis is a reliable technique used to detect irregularities in roller operations.
By using sensors to monitor vibration levels, you can identify changes that might indicate mechanical problems, such as unbalanced rollers or bearing issues.
Temperature Monitoring
Monitoring the temperature of rollers can provide insights into their operational health.
Unexpected temperature changes might signal potential issues such as overheating or excessive friction.
Sound Analysis
Unusual noises can be an early warning sign of roller abnormalities.
Sound analysis involves using acoustic sensors to detect deviations from normal operating sounds, helping to identify issues before they lead to significant problems.
Implementing a Maintenance Schedule
For effective roller maintenance, implementing a well-planned maintenance schedule is crucial.
A maintenance schedule should include the frequency of inspections, lubrication, cleaning, and parts replacement.
It should be designed based on manufacturer recommendations and operational conditions.
Regular training for maintenance staff ensures they are capable of performing the tasks effectively and staying updated on the latest methods and technologies.
Utilizing Technology for Roller Maintenance
Incorporating technology into roller maintenance efforts can significantly enhance efficiency and accuracy.
Predictive Maintenance Tools
Predictive maintenance tools use data analytics and machine learning to predict when equipment might fail.
By analyzing historical data, these tools can indicate when maintenance should be performed, reducing the risk of unplanned downtime.
Digital Twins
Digital twin technology creates a virtual model of the rollers, allowing for real-time monitoring and analysis.
This technology provides insights into performance and potential issues, facilitating timely maintenance interventions.
Conclusion
Understanding and implementing effective roller preventive maintenance and abnormality detection methods is essential for new leaders in the steel industry.
By adopting a proactive approach, you can ensure the smooth operation of equipment, reduce costs, enhance safety, and promote a culture of reliability and efficiency.
As you step into your leadership role, remember that regular maintenance and modern technologies are your allies in maintaining robust and dependable steel production processes.
資料ダウンロード
QCD調達購買管理クラウド「newji」は、調達購買部門で必要なQCD管理全てを備えた、現場特化型兼クラウド型の今世紀最高の購買管理システムとなります。
ユーザー登録
調達購買業務の効率化だけでなく、システムを導入することで、コスト削減や製品・資材のステータス可視化のほか、属人化していた購買情報の共有化による内部不正防止や統制にも役立ちます。
NEWJI DX
製造業に特化したデジタルトランスフォーメーション(DX)の実現を目指す請負開発型のコンサルティングサービスです。AI、iPaaS、および先端の技術を駆使して、製造プロセスの効率化、業務効率化、チームワーク強化、コスト削減、品質向上を実現します。このサービスは、製造業の課題を深く理解し、それに対する最適なデジタルソリューションを提供することで、企業が持続的な成長とイノベーションを達成できるようサポートします。
オンライン講座
製造業、主に購買・調達部門にお勤めの方々に向けた情報を配信しております。
新任の方やベテランの方、管理職を対象とした幅広いコンテンツをご用意しております。
お問い合わせ
コストダウンが利益に直結する術だと理解していても、なかなか前に進めることができない状況。そんな時は、newjiのコストダウン自動化機能で大きく利益貢献しよう!
(Β版非公開)