- お役立ち記事
- For production engineers in the precision machinery industry! How to realize machining of high hardness materials with tools coated with PVD
For production engineers in the precision machinery industry! How to realize machining of high hardness materials with tools coated with PVD
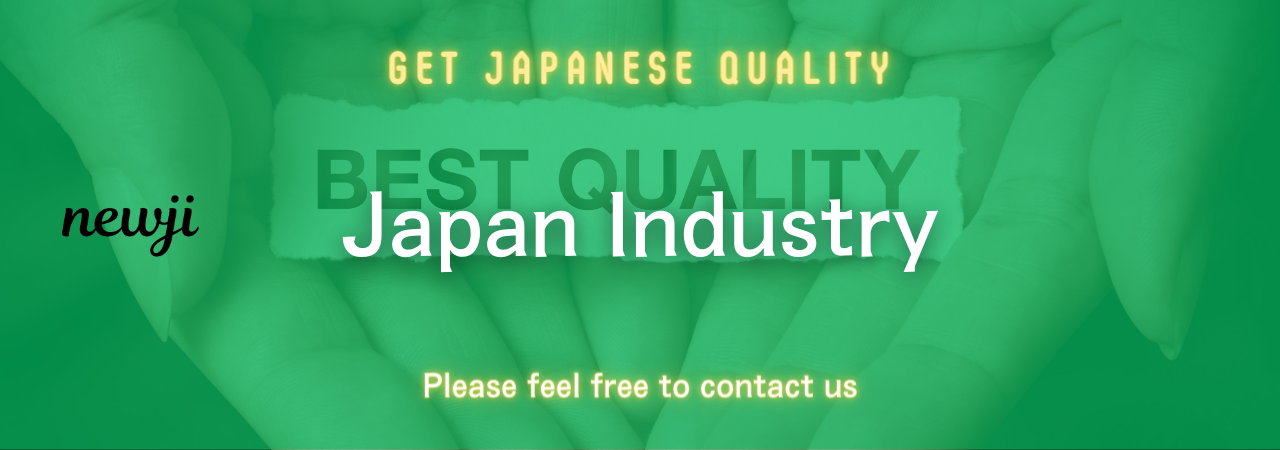
目次
Introduction to High Hardness Material Machining
Machining materials with high hardness can often pose significant challenges in the precision machinery industry.
These materials, while offering exceptional durability and strength, can also be difficult to work with using standard techniques.
However, advancements in tool coatings, specifically Physical Vapor Deposition (PVD), have made the machining of these tough materials more efficient and cost-effective.
In this article, we will explore how production engineers can leverage PVD-coated tools to optimize the machining process of high hardness materials.
Understanding Physical Vapor Deposition (PVD)
Before delving into the applications of PVD in machining, it’s important to understand what Physical Vapor Deposition entails.
PVD is a coating process that involves the condensation of vaporized material onto a surface to form a thin film.
This method is frequently employed to enhance the hardness, resistance, and lifespan of cutting tools.
By applying a PVD coating, tools gain a high degree of precision and are able to perform reliably under extreme conditions.
Advantages of PVD-Coated Tools
PVD-coated tools bring a host of advantages to the machining of high hardness materials.
Firstly, the coating provides enhanced wear resistance, allowing tools to maintain sharpness and effectiveness over longer periods.
This results in fewer tool changes and prolonged tool life, thus reducing downtime and improving production efficiency.
Another benefit is the improved thermal stability offered by PVD coatings.
When machining tough materials, high temperatures can lead to tool damage or failure.
However, PVD coatings can withstand higher temperatures, thereby protecting the tool and ensuring consistent performance during cutting operations.
Additionally, the reduced friction offered by PVD coatings can significantly decrease the tool’s operational temperature.
This not only prolongs the lifespan of the tool but also improves the quality of the finished product by reducing imperfections caused by excess heat.
Increased Cutting Speed
PVD-coated tools allow for increased cutting speeds due to their enhanced performance characteristics.
Higher cutting speeds mean faster production times, which is crucial in competitive manufacturing environments.
This increased efficiency does not come at the cost of precision, as PVD coatings enable tools to maintain tight tolerances and produce high-quality outputs.
Surface Finish Improvements
The surface finish of a machined part is critical, especially in precise applications.
PVD coatings contribute to producing smoother surface finishes due to their ability to minimize tool wear and maintain cutting-edge sharpness.
This is particularly beneficial when working with high hardness materials, where achieving a fine finish can be challenging.
Choosing the Right PVD-Coated Tool
Selecting the appropriate PVD-coated tool is crucial to maximizing the benefits of working with high hardness materials.
When choosing these tools, production engineers must consider factors such as the type of material being machined, the specific requirements of the application, and the preferred machining strategy.
Material Compatibility
It’s important to ensure that the PVD coating is compatible with the material being machined.
Different coatings offer varying levels of hardness, heat resistance, and chemical stability, which must align with the characteristics of the material.
For instance, a titanium nitride (TiN) coating is suitable for softer metals, while a titanium aluminum nitride (TiAlN) coating might be better for harder alloys.
Application Requirements
Understanding the specific application requirements is essential to choosing the correct tool.
This includes the necessary tolerance levels, desired surface finish, and the scale of production.
Matching the tool’s capabilities with these requirements ensures optimal performance and cost-efficiency.
Machining Strategy
The chosen machining strategy will also influence the selection of PVD-coated tools.
High-speed machining may require different coatings compared to operations needing high precision or fine detailing.
It’s imperative to align the capabilities of the tool with the established machining approach.
Best Practices for Machining High Hardness Materials
To fully realize the potential of PVD-coated tools, production engineers should adhere to best practices when machining high hardness materials.
Tool Maintenance
Regular maintenance of tools is necessary to preserve their effectiveness.
Despite their durability, PVD-coated tools should be routinely inspected for wear and damage to avoid unforeseen failures during operations.
Optimizing Cutting Conditions
Setting optimal cutting conditions can significantly enhance the machining process.
Variables such as cutting speed, feed rate, and depth of cut should be adjusted to suit the material and the tool’s capabilities.
Properly calibrated machines can extend the tool’s life and improve the resulting product quality.
Continuous Monitoring and Adjustments
Throughout the machining process, continuous monitoring should be conducted to ensure accuracy and efficiency.
Any deviations from expected performance can indicate the need for adjustments in the machining parameters or maintenance intervals.
Conclusion
The use of PVD-coated tools represents a substantial advancement in the machining of high hardness materials within the precision machinery industry.
By leveraging these enhanced tools, production engineers can achieve greater efficiency, improved surface finishes, and lower operational costs.
Following best practices and carefully selecting the right tools based on material compatibility, application requirements, and machining strategy, engineers can fully exploit the benefits offered by PVD coatings.
The result is a more competitive and innovative manufacturing process that meets modern industry demands.
資料ダウンロード
QCD調達購買管理クラウド「newji」は、調達購買部門で必要なQCD管理全てを備えた、現場特化型兼クラウド型の今世紀最高の購買管理システムとなります。
ユーザー登録
調達購買業務の効率化だけでなく、システムを導入することで、コスト削減や製品・資材のステータス可視化のほか、属人化していた購買情報の共有化による内部不正防止や統制にも役立ちます。
NEWJI DX
製造業に特化したデジタルトランスフォーメーション(DX)の実現を目指す請負開発型のコンサルティングサービスです。AI、iPaaS、および先端の技術を駆使して、製造プロセスの効率化、業務効率化、チームワーク強化、コスト削減、品質向上を実現します。このサービスは、製造業の課題を深く理解し、それに対する最適なデジタルソリューションを提供することで、企業が持続的な成長とイノベーションを達成できるようサポートします。
オンライン講座
製造業、主に購買・調達部門にお勤めの方々に向けた情報を配信しております。
新任の方やベテランの方、管理職を対象とした幅広いコンテンツをご用意しております。
お問い合わせ
コストダウンが利益に直結する術だと理解していても、なかなか前に進めることができない状況。そんな時は、newjiのコストダウン自動化機能で大きく利益貢献しよう!
(Β版非公開)