- お役立ち記事
- Unlocking Efficiency: ABC Analysis in Japanese Manufacturing Strategy
Unlocking Efficiency: ABC Analysis in Japanese Manufacturing Strategy
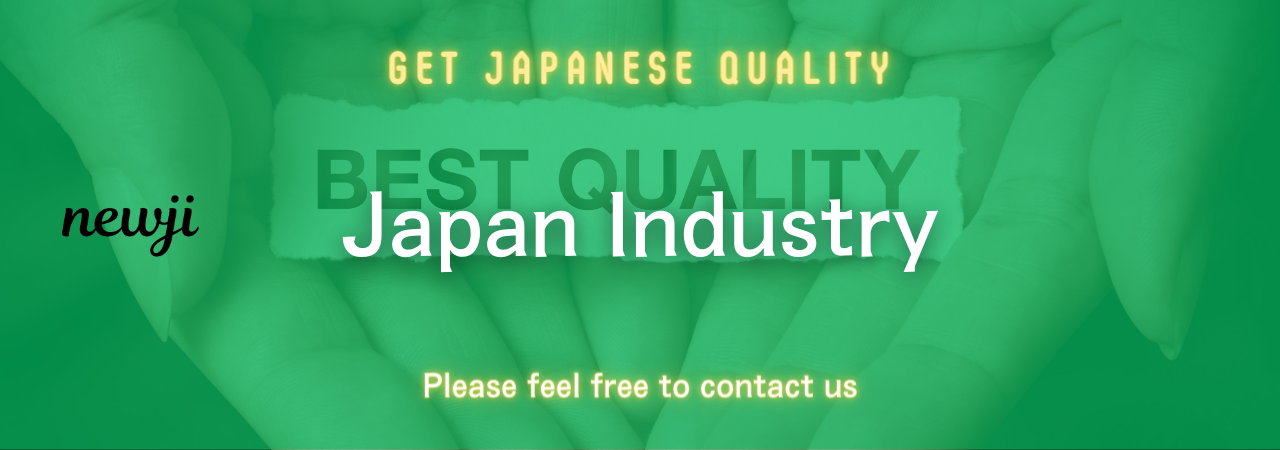
目次
Introduction to ABC Analysis in Japanese Manufacturing
ABC Analysis is a pivotal inventory management technique that categorizes inventory into three classes: A, B, and C. This method allows manufacturing companies to prioritize their inventory management efforts, focusing on the most critical items that significantly impact the business. In Japanese manufacturing, where efficiency and precision are paramount, ABC Analysis plays a crucial role in streamlining operations, optimizing procurement processes, and enhancing overall productivity.
The Fundamentals of ABC Analysis
ABC Analysis operates on the Pareto Principle, also known as the 80/20 rule, which suggests that approximately 80% of the effects come from 20% of the causes. Applied to inventory management, this means that a small percentage of inventory items often account for a large portion of the company’s value or usage.
Class A Items
Class A items are the most valuable and critical to the business. They typically represent a small percentage of the total inventory but account for a significant portion of the inventory value—often around 70-80%. These items require tight control, frequent reviews, and accurate forecasting to prevent stockouts and ensure smooth production processes.
Class B Items
Class B items are of moderate value and importance. They usually make up a larger percentage of inventory than Class A items but account for a smaller portion of the total value, around 15-25%. These items require regular monitoring and periodic review to maintain optimal inventory levels without overstocking.
Class C Items
Class C items are the least valuable and least critical to the business operations. They represent the largest percentage of inventory items but contribute minimally to the overall inventory value, typically around 5-10%. These items require minimal control and less frequent reviews, allowing companies to manage them with simpler inventory strategies.
Implementing ABC Analysis in Japanese Manufacturing
Japanese manufacturing is renowned for its emphasis on efficiency, quality, and continuous improvement. Implementing ABC Analysis within this context involves several strategic steps to align inventory management with these core principles.
Data Collection and Inventory Classification
The first step is to gather detailed data on all inventory items, including their usage rates, consumption value, and criticality to production. This data forms the basis for classifying items into A, B, and C categories. In Japanese manufacturing, this process is often supported by advanced inventory management systems that ensure accuracy and real-time tracking.
Prioritizing Inventory Management Efforts
Once items are classified, resources can be allocated more effectively. Class A items, being the most critical, receive the highest attention in terms of inventory control, demand forecasting, and supplier relationships. B and C items are managed with proportionate levels of oversight, ensuring that efforts are focused where they are most needed.
Continuous Monitoring and Adjustment
ABC Analysis is not a one-time task but requires ongoing monitoring and adjustments. In the dynamic environment of Japanese manufacturing, changes in production processes, market demand, and supplier performance necessitate regular reviews and reclassification of inventory items to maintain alignment with business goals.
Advantages of ABC Analysis in Procurement and Purchasing
Implementing ABC Analysis offers several benefits, particularly in the areas of procurement and purchasing within Japanese manufacturing contexts.
Optimized Inventory Levels
By identifying the most valuable items, companies can maintain optimal inventory levels, reducing carrying costs and minimizing the risk of stockouts. This is essential for maintaining the flow of production without unnecessary financial burdens.
Improved Supplier Relationships
With a clear understanding of which items are most critical, procurement teams can prioritize supplier relationships and negotiate better terms for Class A items. This focus leads to more reliable supply chains and enhances the overall quality of materials received.
Enhanced Forecasting and Planning
ABC Analysis aids in more accurate demand forecasting and production planning. By concentrating on high-impact items, companies can better anticipate market needs and adjust their procurement strategies accordingly, leading to increased responsiveness and competitiveness.
Cost Savings
Efficient inventory management through ABC Analysis reduces excess inventory and associated costs. By avoiding overstocking of low-value items and ensuring adequate supply of high-value items, companies can achieve significant cost savings and improve their bottom line.
Disadvantages and Challenges of ABC Analysis
While ABC Analysis offers numerous benefits, it also presents certain challenges that companies must address to ensure successful implementation.
Initial Data Intensive
ABC Analysis requires comprehensive and accurate data collection, which can be time-consuming and resource-intensive. Inaccurate or incomplete data can lead to misclassification of inventory items, undermining the effectiveness of the analysis.
Dynamic Market Conditions
In rapidly changing markets, the significance of inventory items may shift quickly. This requires frequent reclassification and updates to the ABC categories, which can be challenging to manage and keep up-to-date.
Overemphasis on Cost
Focusing primarily on the monetary value of items may lead to neglecting other important factors, such as lead times, supplier reliability, and product criticality. A balanced approach is necessary to ensure that all aspects of inventory management are considered.
Implementation Complexity
Integrating ABC Analysis into existing inventory management systems and processes can be complex, especially in large organizations with diverse product lines. Proper training and change management strategies are essential to overcome this complexity.
Supplier Negotiation Techniques Using ABC Analysis
ABC Analysis provides a strategic foundation for effective supplier negotiation, particularly in Japanese manufacturing, where supplier relationships are integral to success.
Prioritizing Key Suppliers
For Class A items, it is vital to identify and prioritize key suppliers who can consistently meet quality and delivery standards. Building strong, collaborative relationships with these suppliers ensures reliability and fosters mutual growth.
Volume Commitments and Discounts
Leveraging the high volume and value of Class A items, companies can negotiate better pricing, volume discounts, and favorable payment terms. This not only reduces procurement costs but also secures a steady supply of critical materials.
Performance-Based Agreements
Implementing performance-based agreements with suppliers ensures that Class A items meet predefined quality and delivery benchmarks. These agreements create accountability and drive continuous improvement in supplier performance.
Risk Mitigation Strategies
For high-value items, it is essential to develop risk mitigation strategies, such as dual sourcing or maintaining safety stock levels. Negotiating terms that allow for flexibility in the event of supply disruptions enhances resilience in the supply chain.
Market Conditions and ABC Analysis
Understanding market conditions is crucial for effectively applying ABC Analysis in procurement and purchasing strategies.
Demand Fluctuations
Market demand can vary due to factors such as economic conditions, technological advancements, and consumer preferences. ABC Analysis helps companies adapt to these fluctuations by highlighting which inventory items need more agile management.
Supplier Market Dynamics
The availability and pricing of suppliers can change based on competition, geopolitical factors, and resource availability. ABC Analysis provides insights into which suppliers are critical for Class A items, allowing companies to navigate market dynamics more effectively.
Global Supply Chain Considerations
In a globalized market, supply chain disruptions can have significant impacts. ABC Analysis enables companies to identify and prioritize critical suppliers, facilitating quicker responses to global supply chain challenges.
Best Practices for ABC Analysis in Japanese Manufacturing
To maximize the benefits of ABC Analysis, Japanese manufacturing companies should adhere to best practices that align with their operational excellence standards.
Integrate ABC Analysis with Lean Manufacturing
Combining ABC Analysis with lean manufacturing principles can enhance efficiency by eliminating waste, optimizing inventory levels, and ensuring that resources are focused on high-impact areas.
Leverage Technology and Automation
Utilizing advanced inventory management systems and automation tools supports accurate data collection, real-time tracking, and efficient reclassification of inventory items. Technology integration is key to maintaining the precision and responsiveness required in Japanese manufacturing.
Continuous Improvement and Review
Adopting a Kaizen mindset—continuous improvement—is essential for ABC Analysis. Regularly reviewing and updating inventory classifications ensures that the analysis remains relevant and effective in changing market conditions.
Collaborate Across Departments
Effective ABC Analysis requires collaboration between procurement, production, finance, and other departments. Cross-functional teams ensure that all aspects of inventory management are considered and that strategies are aligned with overall business objectives.
Training and Development
Investing in training for staff involved in inventory management ensures that they understand the principles of ABC Analysis and can effectively implement and utilize the technique. Skilled personnel are critical for the success of any inventory management strategy.
Case Study: ABC Analysis in a Japanese Automotive Manufacturer
To illustrate the practical application of ABC Analysis, consider a leading Japanese automotive manufacturer that implemented this technique to enhance its procurement and inventory management processes.
Challenge
The company faced issues with excess inventory of low-value components and frequent stockouts of critical high-value parts, leading to production delays and increased costs.
Solution
By conducting a comprehensive ABC Analysis, the company categorized its inventory into Class A, B, and C items based on their value and impact on production. Class A items were identified as critical engine components, while Class C items included various fasteners and non-critical parts.
Implementation
The company restructured its procurement strategy to focus on tight control and strategic supplier partnerships for Class A items. For Class C items, the procurement process was streamlined to reduce overhead and inventory carrying costs.
Results
The implementation of ABC Analysis led to a 20% reduction in inventory carrying costs and a 15% decrease in stockout incidents. Production efficiency improved, and the company achieved better alignment between inventory levels and actual demand.
Conclusion
ABC Analysis is a powerful tool in the arsenal of Japanese manufacturing strategies, offering significant benefits in procurement, inventory management, and overall operational efficiency. By categorizing inventory into A, B, and C classes, companies can prioritize their efforts, optimize resources, and foster strong supplier relationships. While challenges exist in implementation and maintaining accuracy, adherence to best practices and a commitment to continuous improvement can ensure that ABC Analysis delivers substantial value. In the competitive landscape of global manufacturing, leveraging ABC Analysis can unlock efficiencies that drive success and sustain growth.
資料ダウンロード
QCD調達購買管理クラウド「newji」は、調達購買部門で必要なQCD管理全てを備えた、現場特化型兼クラウド型の今世紀最高の購買管理システムとなります。
ユーザー登録
調達購買業務の効率化だけでなく、システムを導入することで、コスト削減や製品・資材のステータス可視化のほか、属人化していた購買情報の共有化による内部不正防止や統制にも役立ちます。
NEWJI DX
製造業に特化したデジタルトランスフォーメーション(DX)の実現を目指す請負開発型のコンサルティングサービスです。AI、iPaaS、および先端の技術を駆使して、製造プロセスの効率化、業務効率化、チームワーク強化、コスト削減、品質向上を実現します。このサービスは、製造業の課題を深く理解し、それに対する最適なデジタルソリューションを提供することで、企業が持続的な成長とイノベーションを達成できるようサポートします。
オンライン講座
製造業、主に購買・調達部門にお勤めの方々に向けた情報を配信しております。
新任の方やベテランの方、管理職を対象とした幅広いコンテンツをご用意しております。
お問い合わせ
コストダウンが利益に直結する術だと理解していても、なかなか前に進めることができない状況。そんな時は、newjiのコストダウン自動化機能で大きく利益貢献しよう!
(Β版非公開)