- お役立ち記事
- A must-see for design department leaders in the precision machinery industry! Optimal selection of hob cutter and method for improving gear machining accuracy
A must-see for design department leaders in the precision machinery industry! Optimal selection of hob cutter and method for improving gear machining accuracy
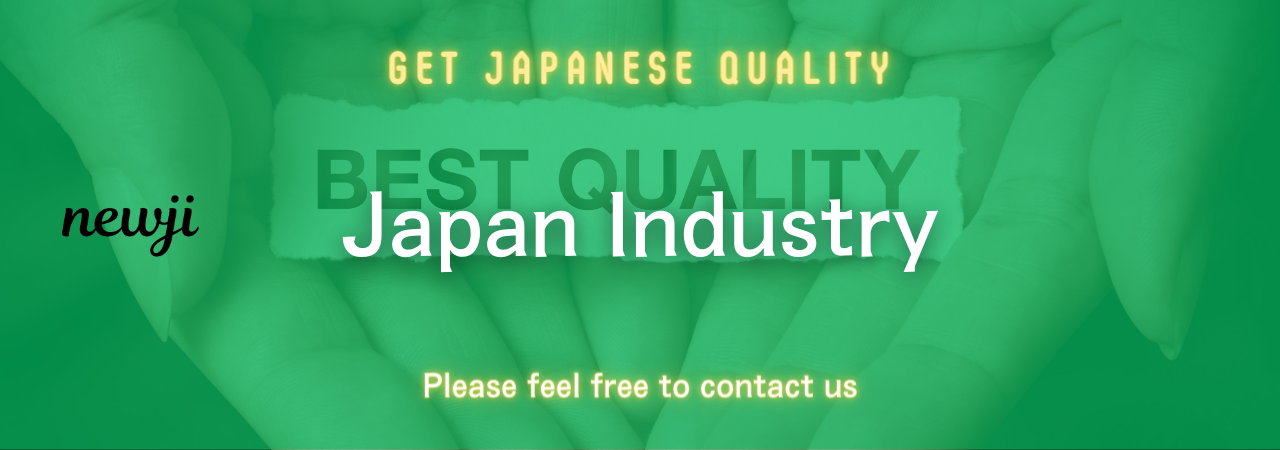
目次
Understanding Hob Cutters
Hob cutters are essential tools in the precision machinery industry, especially when it comes to gear manufacturing.
These tools are designed to cut gears with high precision, ensuring the gears function smoothly and efficiently.
A hob cutter is a cylindrical tool that has helical cutting teeth.
The tool rotates as it cuts the gear blank, gradually forming the desired gear shape.
In the precision machinery industry, the correct selection and utilization of hob cutters are crucial for achieving high-quality gear machining.
This ensures that the gears possess the necessary accuracy and durability.
For department leaders in the precision machinery industry, understanding the nuances of hob cutters is vital for improving production processes and product quality.
Selecting the Optimal Hob Cutter
Choosing the right hob cutter is a critical decision that impacts the final quality of the gears produced.
Several factors must be considered when selecting a hob cutter for a particular application.
Material of the Cutter
The material of the hob cutter plays a significant role in its performance.
High-speed steel (HSS) and carbide are the most common materials used for hob cutters.
HSS cutters are versatile, providing good performance for a variety of gear cutting tasks.
Carbide cutters, although more expensive, offer superior wear resistance and can handle harder workpieces.
Coating of the Hob Cutter
To enhance the lifespan of hob cutters, various coatings are applied.
TiN (Titanium Nitride) and AlTiN (Aluminium Titanium Nitride) are coatings that improve wear resistance and reduce friction.
Coated hob cutters can maintain their sharpness longer, leading to better precision in gear machining.
Profile and Size
The profile and size of the hob cutter should match the specific requirements of the gear being produced.
The cutter must be compatible with the gear’s dimensions and the machining equipment.
Custom hob cutters may be necessary for specialized gear designs, ensuring precision in the machining process.
Improving Gear Machining Accuracy
Achieving high accuracy in gear machining is crucial in the precision machinery industry.
Accuracy ensures that gears perform optimally and have a longer service life.
Here are some strategies to improve gear machining accuracy.
Regular Maintenance
Regular maintenance of hob cutters is essential for sustaining their performance.
Checking for wear and damage allows timely replacements, preventing inaccurate cuts.
Sharpening hob cutters when necessary helps maintain their cutting precision.
Correct Setup and Alignment
Proper setup and alignment of hob cutters and the workpiece are crucial for accurate gear machining.
Any misalignment can lead to errors in gear dimensions and overall performance.
Ensuring that the cutter is correctly aligned with the gear blank minimizes deviations and enhances the precision of the cut.
Advanced Machining Techniques
Incorporating advanced machining techniques such as CNC (Computer Numerical Control) can significantly improve gear machining accuracy.
CNC machines offer precise control over cutting processes, reducing human errors and improving consistency.
Updating conventional machining setups to CNC systems can yield higher quality gears.
Monitoring and Quality Control
Quality control is a vital component in the gear manufacturing process.
Implementing robust monitoring systems to assess gear quality during and after machining helps in maintaining high standards.
Use of Inspection Tools
Utilizing inspection tools such as gear measurement machines and high-precision calipers helps in identifying defects early.
This allows for timely corrections in the machining process, ensuring consistent gear accuracy.
Feedback and Adjustments
Implementing a feedback loop from the inspection phase to the machining process can enhance accuracy.
Adjusting machining parameters based on feedback from quality assessments helps fine-tune the process, reducing inaccuracies.
Conclusion
For leaders in the precision machinery industry, optimizing the use of hob cutters is imperative for achieving superior gear machining accuracy.
Selecting the right hob cutters considering materials, coatings, and sizes is the first step towards effective gear production.
Incorporating advanced machining techniques, regular maintenance, and stringent quality control can significantly elevate the quality of gears produced.
By understanding and implementing these strategies, department leaders can enhance productivity and ensure high precision in gear manufacturing.
資料ダウンロード
QCD調達購買管理クラウド「newji」は、調達購買部門で必要なQCD管理全てを備えた、現場特化型兼クラウド型の今世紀最高の購買管理システムとなります。
ユーザー登録
調達購買業務の効率化だけでなく、システムを導入することで、コスト削減や製品・資材のステータス可視化のほか、属人化していた購買情報の共有化による内部不正防止や統制にも役立ちます。
NEWJI DX
製造業に特化したデジタルトランスフォーメーション(DX)の実現を目指す請負開発型のコンサルティングサービスです。AI、iPaaS、および先端の技術を駆使して、製造プロセスの効率化、業務効率化、チームワーク強化、コスト削減、品質向上を実現します。このサービスは、製造業の課題を深く理解し、それに対する最適なデジタルソリューションを提供することで、企業が持続的な成長とイノベーションを達成できるようサポートします。
オンライン講座
製造業、主に購買・調達部門にお勤めの方々に向けた情報を配信しております。
新任の方やベテランの方、管理職を対象とした幅広いコンテンツをご用意しております。
お問い合わせ
コストダウンが利益に直結する術だと理解していても、なかなか前に進めることができない状況。そんな時は、newjiのコストダウン自動化機能で大きく利益貢献しよう!
(Β版非公開)