- お役立ち記事
- For quality control leaders in the semiconductor industry! Void countermeasures and rework technology for high-density substrates
For quality control leaders in the semiconductor industry! Void countermeasures and rework technology for high-density substrates
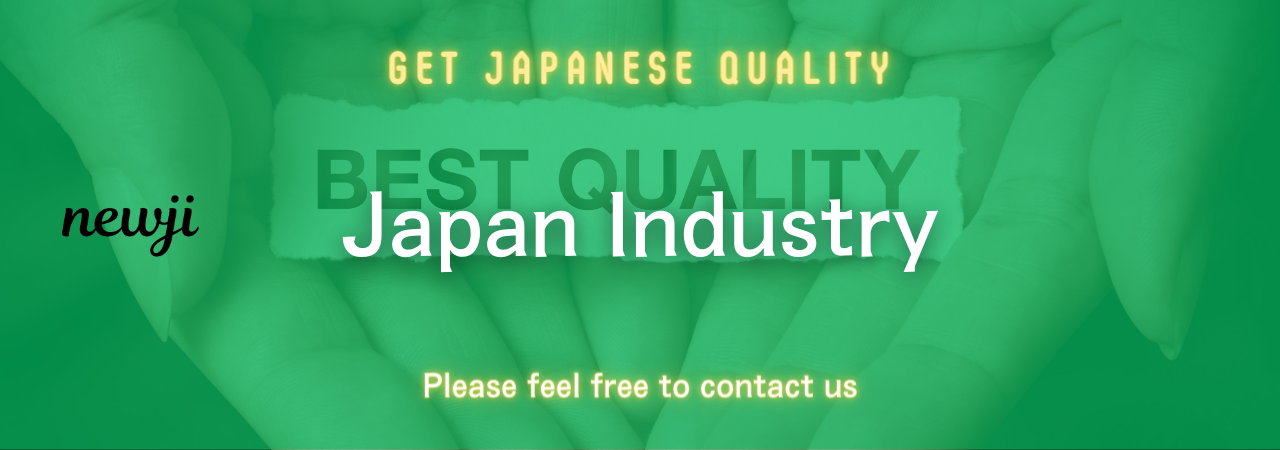
目次
Understanding Voids in High-Density Substrates
In the semiconductor industry, maintaining quality control is an essential task for leaders who are responsible for overseeing the production process of microelectronic components.
One of the significant challenges encountered is the presence of voids in high-density substrates.
These voids can lead to defects, compromising the performance and reliability of semiconductors.
Hence, understanding how voids form and developing effective countermeasures is crucial.
Voids are essentially tiny air pockets or gaps that occur within the substrate during the manufacturing process.
They can result from various factors, such as improper soldering, gas entrapment, or thermal expansion mismatches.
Left unchecked, these voids can cause circuit failure, leading to costly reworks or replacements.
Causes of Voids in Semiconductor Manufacturing
To effectively counteract voids, it is important to first understand their causes.
Several factors contribute to the formation of voids in high-density substrates:
1. Soldering Issues
Soldering is a critical process in semiconductor manufacturing where components are affixed to the substrate.
Improper soldering, either due to insufficient heat or incorrect pressure, can lead to void formation.
2. Flux Residues
Flux is used in the soldering process to clean and prepare surfaces for bonding.
If not adequately cleaned, flux residues can cause voids by trapping gases beneath the soldered joint.
3. Thermal Expansion
Differences in thermal expansion coefficients between materials can lead to void formation.
When components expand or contract at varying rates due to temperature changes, it can create gaps.
4. Material Contamination
Contaminants such as dust, dirt, or oils can disrupt the substrate’s surface, preventing a proper bond during soldering, which contributes to void formation.
Strategies for Addressing Voids
Implementing void countermeasures is critical for quality control in the semiconductor industry.
The following strategies can help mitigate void-related issues:
1. Improved Soldering Techniques
Utilizing advanced soldering methods such as dynamic solder reflow or vapor phase soldering can significantly reduce void formation.
These techniques ensure consistent heat application and pressure, leading to better solder joints.
2. Flux and Cleaning Improvements
Employing higher quality flux and ensuring thorough cleaning of surfaces before and after soldering can help reduce flux residues and, consequently, voids.
3. Thermal Management
Controlling the production environment to minimize drastic temperature changes can prevent void formation due to thermal expansion.
Using materials with compatible thermal expansion coefficients also helps.
4. Material Handling Best Practices
Ensuring a clean production environment and handling materials with care can prevent contamination, thus minimizing void formation.
Rework Technologies for High-Density Substrates
Despite best efforts, voids may still occur, making it essential to have reliable rework technologies in place.
Rework involves repairing defective parts without affecting the overall device functionality.
1. Desoldering and Resoldering
Desoldering with precision tools allows for the removal of faulty components or substrates.
The area can then be cleaned and prepared for resoldering new components, eliminating voids in the process.
2. Using Reflow Ovens
Controlled heating in a reflow oven can remedy solder joints with minor voids.
The heat allows the solder to re-melt, potentially reducing or eliminating voids.
3. Advanced Imaging Techniques
Using imaging tools such as X-ray or ultrasonic scanning helps identify voids that are not visible to the naked eye.
Having accurate data ensures targeted rework efforts.
4. Patch Repair
In cases where voids are detected in non-critical areas, patch repair may be a viable option.
Using conductive material to fill voids restores functionality without extensive rework.
Future Outlook: Technologies and Innovations
As the semiconductor industry continues to advance, new technologies and innovations are emerging to tackle void issues more effectively.
Research and development in materials science are leading to the creation of novel materials with excellent bonding properties and reduced liabilities for void formation.
Automation in manufacturing processes, including robotic soldering and real-time error detection systems, paves the way for higher precision and control over substrate quality.
Furthermore, the integration of artificial intelligence (AI) to predict and prevent voids before they occur marks a significant step towards enhancing semiconductor reliability.
In conclusion, void countermeasures and rework technologies for high-density substrates remain a pivotal focus for quality control leaders in the semiconductor industry.
By understanding the causes of voids and employing effective strategies and technologies, it is possible to improve product quality and performance, ensuring the advancement of semiconductor technology into the future.
資料ダウンロード
QCD調達購買管理クラウド「newji」は、調達購買部門で必要なQCD管理全てを備えた、現場特化型兼クラウド型の今世紀最高の購買管理システムとなります。
ユーザー登録
調達購買業務の効率化だけでなく、システムを導入することで、コスト削減や製品・資材のステータス可視化のほか、属人化していた購買情報の共有化による内部不正防止や統制にも役立ちます。
NEWJI DX
製造業に特化したデジタルトランスフォーメーション(DX)の実現を目指す請負開発型のコンサルティングサービスです。AI、iPaaS、および先端の技術を駆使して、製造プロセスの効率化、業務効率化、チームワーク強化、コスト削減、品質向上を実現します。このサービスは、製造業の課題を深く理解し、それに対する最適なデジタルソリューションを提供することで、企業が持続的な成長とイノベーションを達成できるようサポートします。
オンライン講座
製造業、主に購買・調達部門にお勤めの方々に向けた情報を配信しております。
新任の方やベテランの方、管理職を対象とした幅広いコンテンツをご用意しております。
お問い合わせ
コストダウンが利益に直結する術だと理解していても、なかなか前に進めることができない状況。そんな時は、newjiのコストダウン自動化機能で大きく利益貢献しよう!
(Β版非公開)