- お役立ち記事
- Basics of equipment maintenance using reliability engineering that new leaders of equipment technology departments in the pharmaceutical manufacturing industry should know
Basics of equipment maintenance using reliability engineering that new leaders of equipment technology departments in the pharmaceutical manufacturing industry should know
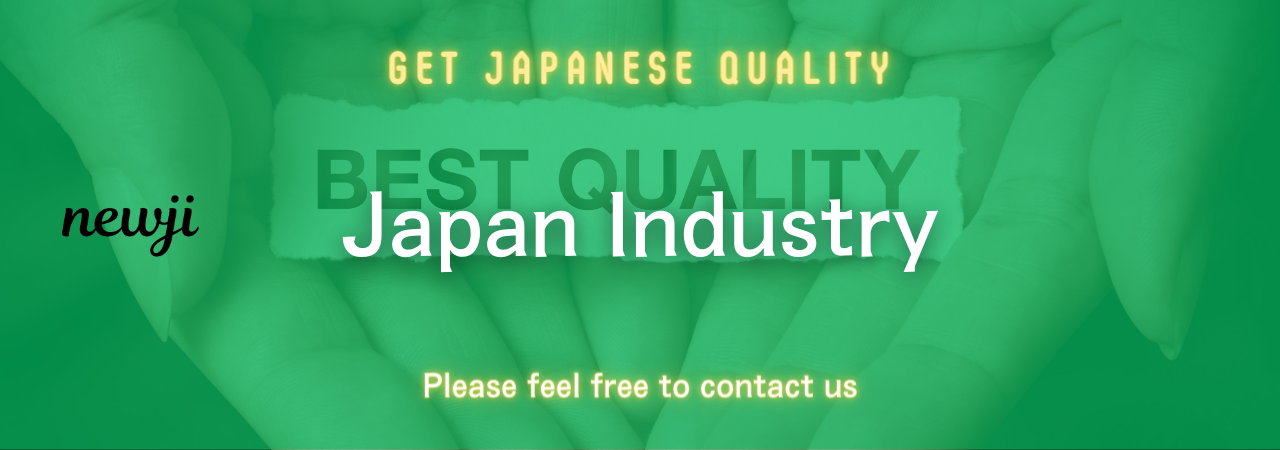
目次
Understanding Equipment Maintenance and Reliability Engineering
Equipment maintenance is crucial in ensuring the smooth operation of pharmaceutical manufacturing processes.
Without regular maintenance, equipment can fail, leading to costly downtime and potentially impacting product quality.
New leaders in equipment technology departments need to grasp the fundamentals of equipment maintenance and how reliability engineering plays a central role in this area.
Reliability engineering focuses on ensuring that equipment performs its intended function without failure for a specified period, enhancing efficiency and reducing costs.
The Importance of Equipment Maintenance in Pharmaceutical Manufacturing
In the pharmaceutical manufacturing industry, equipment reliability is vital to maintaining high standards of product consistency and safety.
Any equipment failure can lead to production delays, financial losses, and, in worst-case scenarios, significant public health risks.
Therefore, ensuring equipment reliability must be a top priority for all manufacturing facilities.
By understanding and implementing effective maintenance strategies, new leaders can help safeguard their organization’s reputation and ensure compliance with regulatory requirements.
Types of Maintenance Strategies
There are several maintenance strategies that equipment technology leaders should be aware of to optimize equipment performance and reliability:
1. Preventive Maintenance
Preventive maintenance involves scheduled inspections and servicing of equipment to prevent unexpected failures.
This strategy is proactive, with maintenance tasks planned and performed at regular intervals.
Preventive maintenance can include cleaning, lubrication, replacement of parts, and calibration.
The goal is to address potential issues before they become critical problems, thereby minimizing equipment downtime.
2. Predictive Maintenance
Predictive maintenance leverages condition-monitoring tools and technologies to assess the real-time condition of equipment.
This approach uses data analysis to predict when equipment failure might occur, allowing maintenance to be performed just in time.
By analyzing patterns and trends, predictive maintenance helps extend equipment life, optimize performance, and reduce costs associated with unnecessary preventive maintenance activities.
3. Reactive Maintenance
Reactive maintenance, also known as “run-to-failure” maintenance, occurs when repairs are made after equipment has already failed.
While sometimes unavoidable, relying solely on reactive maintenance is typically more expensive and disruptive, leading to higher repair costs and increased downtime.
However, reactive maintenance can still be a part of a comprehensive maintenance strategy for non-critical equipment with minimal impact when failed.
Integrating Reliability Engineering in Equipment Maintenance
Reliability engineering is a discipline that applies engineering principles and practices to improve the reliability and accuracy of equipment.
By integrating reliability engineering concepts into maintenance strategies, leaders can enhance equipment performance, increase uptime, and optimize resource allocation.
Key Reliability Engineering Concepts
1. Failure Modes and Effects Analysis (FMEA)
FMEA is a systematic approach used to identify and evaluate potential failure modes of equipment and their impact on production.
By analyzing failure modes, their causes, and effects, maintenance teams can develop strategies to mitigate risks and prioritize maintenance tasks effectively.
FMEA helps focus resources on the most critical areas, improving overall equipment reliability.
2. Root Cause Analysis (RCA)
Root cause analysis is a problem-solving method used to identify the underlying causes of equipment failures.
Instead of addressing the symptoms, RCA aims to find and eliminate the root cause to prevent recurrence.
This approach is essential for reducing chronic equipment issues and establishing long-term solutions to improve equipment reliability.
3. Reliability-Centered Maintenance (RCM)
RCM is a structured approach to determining the maintenance requirements of equipment in its operational context.
It involves assessing equipment functions, failure modes, and effects to develop tailored maintenance strategies based on their criticality.
RCM aims to balance the cost of maintenance with the level of reliability required, ensuring efficient resource deployment.
Implementing a Proactive Maintenance Culture
Adopting a proactive maintenance culture is essential for achieving long-term reliability and operational excellence in pharmaceutical manufacturing.
Here are some steps new leaders can take to foster such a culture within their departments:
1. Encourage Continuous Learning
Provide ongoing training and development opportunities for maintenance teams to stay up to date with the latest technologies, tools, and techniques.
Encourage the sharing of best practices and the pursuit of certifications in reliability engineering and maintenance management.
2. Promote Cross-Functional Collaboration
Foster collaboration between maintenance teams, operations, and engineering departments to enhance communication and problem-solving capabilities.
A cross-functional approach helps identify root causes more effectively and implement comprehensive solutions.
3. Leverage Technology
Utilize advanced technologies, such as the Industrial Internet of Things (IIoT), data analytics, and machine learning, to improve maintenance processes and equipment monitoring.
These tools can provide valuable insights and support predictive maintenance initiatives.
Conclusion
Understanding the basics of equipment maintenance and reliability engineering is crucial for new leaders in pharmaceutical manufacturing.
By integrating reliability engineering principles and fostering a proactive maintenance culture, leaders can enhance equipment performance, reduce downtime, and ensure compliance with industry standards.
Ultimately, this proactive approach will contribute to the overall success of the organization by maintaining high-quality production and safeguarding public health.
資料ダウンロード
QCD調達購買管理クラウド「newji」は、調達購買部門で必要なQCD管理全てを備えた、現場特化型兼クラウド型の今世紀最高の購買管理システムとなります。
ユーザー登録
調達購買業務の効率化だけでなく、システムを導入することで、コスト削減や製品・資材のステータス可視化のほか、属人化していた購買情報の共有化による内部不正防止や統制にも役立ちます。
NEWJI DX
製造業に特化したデジタルトランスフォーメーション(DX)の実現を目指す請負開発型のコンサルティングサービスです。AI、iPaaS、および先端の技術を駆使して、製造プロセスの効率化、業務効率化、チームワーク強化、コスト削減、品質向上を実現します。このサービスは、製造業の課題を深く理解し、それに対する最適なデジタルソリューションを提供することで、企業が持続的な成長とイノベーションを達成できるようサポートします。
オンライン講座
製造業、主に購買・調達部門にお勤めの方々に向けた情報を配信しております。
新任の方やベテランの方、管理職を対象とした幅広いコンテンツをご用意しております。
お問い合わせ
コストダウンが利益に直結する術だと理解していても、なかなか前に進めることができない状況。そんな時は、newjiのコストダウン自動化機能で大きく利益貢献しよう!
(Β版非公開)