- お役立ち記事
- For leaders of quality assurance departments in the aircraft parts manufacturing industry! Improving the accuracy of non-destructive testing using eddy current testing
For leaders of quality assurance departments in the aircraft parts manufacturing industry! Improving the accuracy of non-destructive testing using eddy current testing
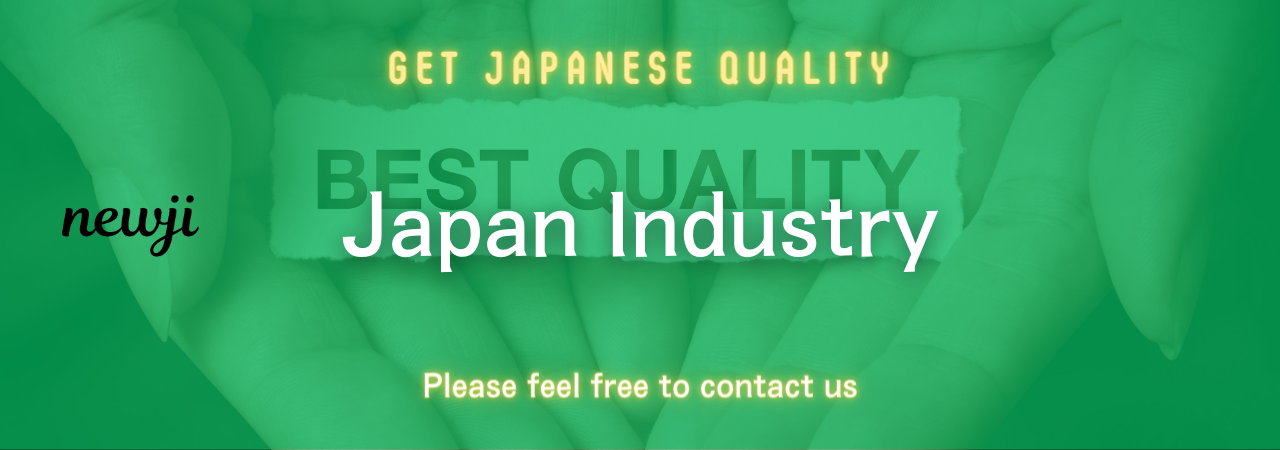
目次
Understanding Eddy Current Testing
Eddy current testing (ECT) is a popular non-destructive testing (NDT) technique used across various industries, including the aircraft parts manufacturing sector.
It involves inducing electromagnetic fields into conductive materials and examining the response.
This method allows for the detection of surface and sub-surface defects without causing any damage to the parts being tested.
For quality assurance leaders in the aircraft manufacturing industry, ensuring the accuracy of testing methods is paramount.
With materials in aircraft designed to withstand extreme conditions, detecting any imperfections early can prevent future failures and liabilities.
Eddy current testing offers a reliable and efficient means to achieve this.
Why Use Eddy Current Testing?
Eddy current testing is particularly suited for inspecting non-ferrous metals found in aircraft components, such as aluminum and titanium.
These materials are often used due to their lightweight and strong properties.
ECT is highly sensitive to surface flaws and can detect minute cracks, corrosion, and changes in conductivity or permeability—all critical aspects in maintaining the safety and integrity of aircraft parts.
Another advantage of eddy current testing is its ability to provide immediate feedback.
This means that evaluations can be performed on-site, reducing the time needed for inspection and minimizing disruptions to production schedules.
Additionally, ECT does not require any consumables, making it an environmentally friendly choice compared to other NDT methods.
Enhancing Accuracy in Eddy Current Testing
Accuracy is imperative in NDT, particularly in critical industries like aerospace.
Improving accuracy in eddy current testing involves focusing on several key areas: equipment quality, operator expertise, and testing protocols.
Choosing the Right Equipment
The performance of eddy current testing largely depends on the technology and quality of the equipment used.
High-quality eddy current instruments offer greater sensitivity and resolution, allowing for more precise detection of defects.
It’s essential to select equipment that fits the specific needs of the parts being tested.
Calibration is another critical aspect of equipment performance.
Regular calibration checks should be part of the maintenance routine to ensure instruments provide consistent readings.
Using the latest software updates can also enhance the capabilities of ECT equipment, offering better data analysis and storage options.
Training Skilled Personnel
The effectiveness of eddy current testing is greatly influenced by the operator’s skill level.
Investing in comprehensive training programs for technicians can improve their ability to interpret signals accurately and make informed decisions based on the results.
Training should cover both theoretical knowledge and practical applications, including understanding the principles of eddy current testing and hands-on experience with various testing scenarios.
Building expertise in signal analysis and defect identification is crucial for enhancing the accuracy of inspections.
Implementing Robust Testing Protocols
Developing and following standardized testing protocols ensures consistency and reliability in eddy current testing.
These protocols should include detailed procedures for equipment setup, calibration, inspection coverage, and documentation of findings.
Standards such as ASTM and ISO provide guidelines for conducting eddy current testing and can serve as a basis for internal protocols.
Regular audits and reviews of testing processes can help identify areas for improvement and ensure compliance with industry standards.
Integrating Eddy Current Testing in Quality Assurance
Incorporating eddy current testing into the quality assurance framework involves creating a structured approach that aligns with the overall goals of safety and efficiency in aircraft manufacturing.
Streamlining Inspection Processes
Integrating eddy current testing into the production line streamlines the inspection process, making it more efficient.
By identifying defects early in the manufacturing process, costly rework or scrap can be minimized, leading to significant cost savings.
Eddy current testing can be combined with other NDT methods, such as ultrasonic testing, to provide a comprehensive assessment of the component’s integrity.
By doing this, quality assurance leaders can make informed decisions and take corrective actions as necessary.
Data Management and Analysis
Effective data management is essential for tracking the performance of eddy current testing.
Implementing systems that allow for the storage and analysis of test data can provide valuable insights into trends and patterns, helping to predict future issues.
Advanced software solutions can assist in the analysis of eddy current test results, providing a clearer understanding of defect characteristics and their potential impact on the component’s performance.
This information can be used to refine testing techniques and improve overall quality assurance practices.
Continual Improvement and Innovation
Quality assurance departments should foster a culture of continual improvement, leveraging eddy current testing as a tool for innovation.
Regularly reviewing and updating testing processes, along with exploring new technologies or methodologies, ensures that the testing regime remains cutting-edge.
Engaging with industry forums, attending workshops, and collaborating with other stakeholders in the field can provide new perspectives and opportunities for improvement.
By embracing these opportunities, quality assurance leaders can contribute to the ongoing advancement of eddy current testing techniques.
In summary, enhancing the accuracy of non-destructive testing through eddy current techniques is vital for maintaining safety and reliability in aircraft parts manufacturing.
By investing in high-quality equipment, training skilled personnel, implementing robust protocols, and embracing continual improvement, quality assurance leaders can significantly enhance their testing capabilities.
資料ダウンロード
QCD調達購買管理クラウド「newji」は、調達購買部門で必要なQCD管理全てを備えた、現場特化型兼クラウド型の今世紀最高の購買管理システムとなります。
ユーザー登録
調達購買業務の効率化だけでなく、システムを導入することで、コスト削減や製品・資材のステータス可視化のほか、属人化していた購買情報の共有化による内部不正防止や統制にも役立ちます。
NEWJI DX
製造業に特化したデジタルトランスフォーメーション(DX)の実現を目指す請負開発型のコンサルティングサービスです。AI、iPaaS、および先端の技術を駆使して、製造プロセスの効率化、業務効率化、チームワーク強化、コスト削減、品質向上を実現します。このサービスは、製造業の課題を深く理解し、それに対する最適なデジタルソリューションを提供することで、企業が持続的な成長とイノベーションを達成できるようサポートします。
オンライン講座
製造業、主に購買・調達部門にお勤めの方々に向けた情報を配信しております。
新任の方やベテランの方、管理職を対象とした幅広いコンテンツをご用意しております。
お問い合わせ
コストダウンが利益に直結する術だと理解していても、なかなか前に進めることができない状況。そんな時は、newjiのコストダウン自動化機能で大きく利益貢献しよう!
(Β版非公開)