- お役立ち記事
- A must-see for design department managers in the auto parts manufacturing industry! Weight reduction design strategy using magnesium alloy
A must-see for design department managers in the auto parts manufacturing industry! Weight reduction design strategy using magnesium alloy
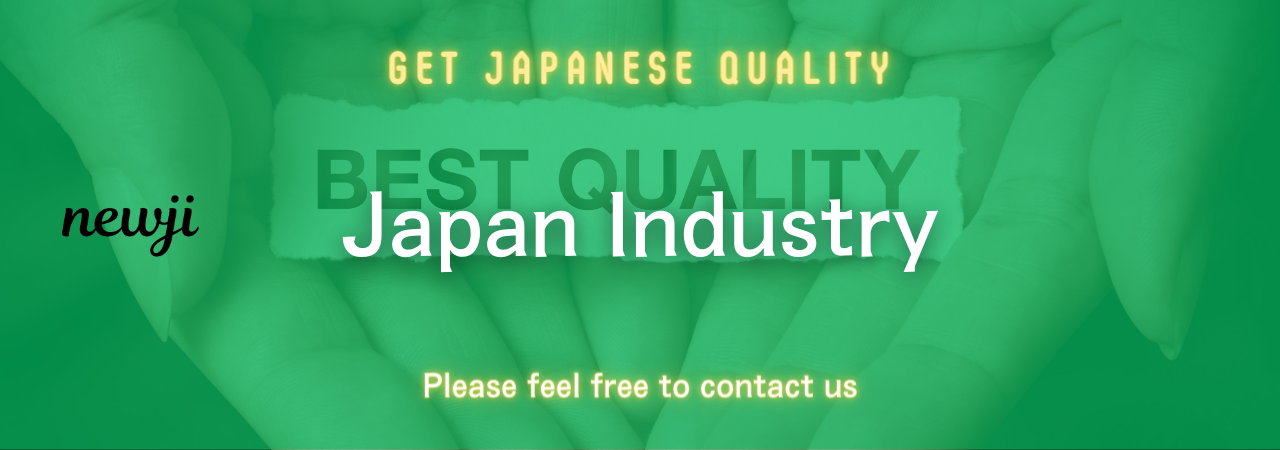
目次
Understanding the Importance of Weight Reduction in Auto Parts
In the bustling world of auto parts manufacturing, the push towards innovation has never been more intense.
Design department managers are constantly seeking strategies to make vehicles more efficient, environmentally friendly, and cost-effective.
One of the critical areas of focus is weight reduction.
Lighter vehicles consume less fuel, contribute less to greenhouse gas emissions, and offer improved overall vehicle performance.
Thus, a weight reduction strategy is not just a trend; it is a necessity for the future of the automotive industry.
The Role of Magnesium Alloy in Auto Manufacturing
Magnesium alloys have emerged as a promising solution in the quest for lightweight automotive parts.
These alloys offer a combination of light weight, structural strength, and versatility, making them an ideal choice for producing automobile components.
Magnesium is the lightest structural metal, and its alloys are significantly lighter than traditional aluminum alloys, while still providing similar strength.
This makes it an excellent candidate for parts requiring both durability and reduced weight.
Advantages of Using Magnesium Alloys
Magnesium alloys offer several benefits that make them attractive to the auto industry.
Firstly, they are incredibly light, which translates directly to lighter vehicles.
By reducing the overall weight of a vehicle, manufacturers can improve fuel efficiency and reduce carbon emissions.
Secondly, magnesium alloys possess excellent machinability, which allows for high precision in component production.
This enhances the ability to create complex designs without compromising quality.
Furthermore, despite their lightweight nature, magnesium alloys provide the necessary strength and rigidity needed to meet safety standards.
Improved Fuel Efficiency and Performance
Weight reduction directly impacts fuel efficiency.
For every 10% reduction in vehicle weight, there is a potential improvement of 5-7% in fuel efficiency.
This is a significant advantage as car manufacturers strive to meet stricter fuel economy regulations.
Moreover, lighter vehicles generally exhibit better acceleration, braking, and handling performance, which can enhance the driving experience.
Environmental Impact
Reducing the weight of a vehicle also has a positive environmental impact.
Lighter vehicles require less energy to move, which means they can operate on less fuel or electricity, thus reducing their carbon footprint.
Using magnesium alloys aligns with the industry’s movement towards sustainable manufacturing processes.
Additionally, magnesium is abundant and can be recycled, further supporting sustainability goals.
Challenges in Implementing Magnesium Alloy Parts
While the benefits of magnesium alloys are clear, there are challenges to overcome before they can be widely adopted in the automotive industry.
One of the primary concerns is the cost.
Magnesium alloys are generally more expensive than traditional materials, which can increase the overall production cost of vehicles.
Furthermore, magnesium is more susceptible to corrosion compared to aluminum and steel.
This requires additional considerations in the design and manufacturing process to ensure longevity and safety.
Solutions and Technological Advancements
Advancements in coating technologies can mitigate corrosion issues.
Using protective coatings or anodizing processes can extend the life of magnesium alloy components and maintain their structural integrity.
Furthermore, ongoing research in metallurgy is striving to develop new formulations of magnesium alloys that offer improved resistance to environmental factors at a lower cost.
Cost-Effectiveness Over Time
Despite the initial higher costs, the long-term savings achieved through improved fuel efficiency and lower emissions can offset the investment in magnesium alloy parts.
Additionally, as production technologies advance and economies of scale are realized, the cost of manufacturing with magnesium alloys is expected to decrease.
Strategies for Successful Implementation
For design department managers aiming to integrate magnesium alloys into their weight reduction strategy, it is crucial to approach the transition methodically.
Begin with a thorough cost-benefit analysis to understand the impact of magnesium alloy parts on the overall vehicle cost and performance.
Engage with material scientists and engineers to identify the most suitable magnesium alloys for specific applications and develop appropriate design parameters to enhance part durability.
Collaboration and Innovation
Collaboration between departments is essential to innovating with magnesium alloys.
Cross-functional teams can provide insights into the design and manufacturing processes from different perspectives, ensuring a holistic approach to implementation.
Additionally, partnerships with external suppliers and research institutions can bring fresh ideas and access to cutting-edge technologies.
Continuous Testing and Optimization
Testing is critical to ensuring the reliability and safety of magnesium alloy components.
Utilize simulation tools to predict performance under various conditions and make necessary adjustments.
Continuously monitor the performance of magnesium alloy parts in real-world applications to identify areas for improvement.
Conclusion
Weight reduction in automotive manufacturing is a strategic priority that is here to stay.
Magnesium alloys present a brilliant opportunity for design department managers in the industry to achieve this goal while enhancing vehicle performance and sustainability.
Despite challenges such as cost and corrosion, ongoing advancements in technology and collaborative efforts can pave the way for successful integration.
By embracing magnesium alloys, manufacturers can stay ahead in the competitive automotive market and contribute to a sustainable future.
資料ダウンロード
QCD調達購買管理クラウド「newji」は、調達購買部門で必要なQCD管理全てを備えた、現場特化型兼クラウド型の今世紀最高の購買管理システムとなります。
ユーザー登録
調達購買業務の効率化だけでなく、システムを導入することで、コスト削減や製品・資材のステータス可視化のほか、属人化していた購買情報の共有化による内部不正防止や統制にも役立ちます。
NEWJI DX
製造業に特化したデジタルトランスフォーメーション(DX)の実現を目指す請負開発型のコンサルティングサービスです。AI、iPaaS、および先端の技術を駆使して、製造プロセスの効率化、業務効率化、チームワーク強化、コスト削減、品質向上を実現します。このサービスは、製造業の課題を深く理解し、それに対する最適なデジタルソリューションを提供することで、企業が持続的な成長とイノベーションを達成できるようサポートします。
オンライン講座
製造業、主に購買・調達部門にお勤めの方々に向けた情報を配信しております。
新任の方やベテランの方、管理職を対象とした幅広いコンテンツをご用意しております。
お問い合わせ
コストダウンが利益に直結する術だと理解していても、なかなか前に進めることができない状況。そんな時は、newjiのコストダウン自動化機能で大きく利益貢献しよう!
(Β版非公開)