- お役立ち記事
- For leaders of quality control departments in the aviation parts manufacturing industry! Improving the reliability of composite materials using non-destructive testing (NDT)
For leaders of quality control departments in the aviation parts manufacturing industry! Improving the reliability of composite materials using non-destructive testing (NDT)
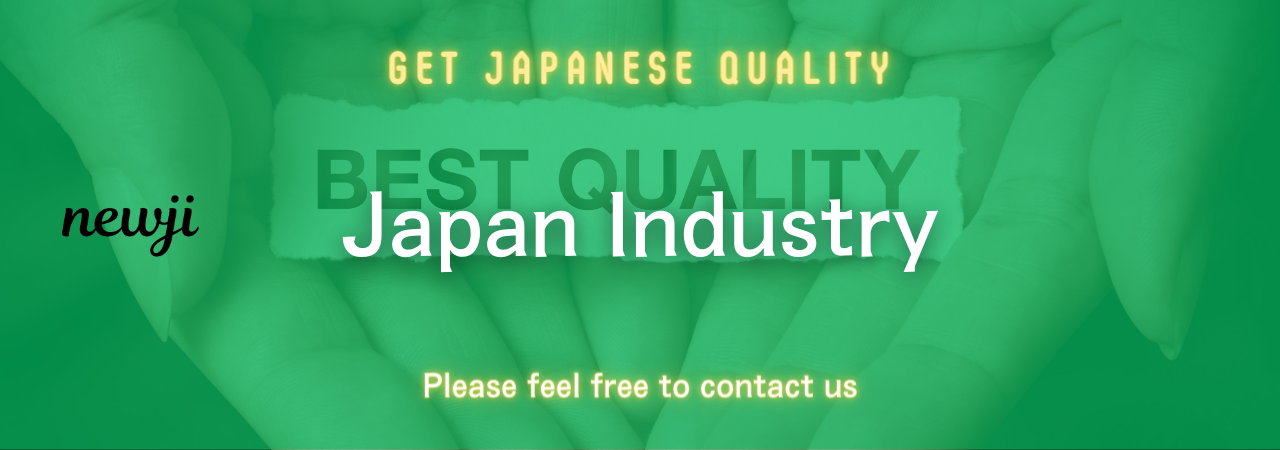
目次
Understanding the Importance of Non-Destructive Testing (NDT)
In the aviation parts manufacturing industry, ensuring the reliability and safety of composite materials is paramount.
With the growing use of composite materials, the challenge lies in maintaining strict quality controls to ensure these components meet rigorous safety standards.
Non-destructive testing (NDT) plays a crucial role in this process by allowing for the inspection of materials without causing damage.
This technique is essential for identifying internal defects, ensuring adherence to specifications, and maintaining compliance with regulatory guidelines.
NDT encompasses a variety of techniques such as ultrasonic testing, radiographic testing, and eddy current testing, among others.
These methods offer a comprehensive solution for quality control leaders striving to enhance the reliability of composite materials in aviation.
The Role of Composite Materials in Aviation
Composite materials have become increasingly important in the aviation industry due to their superior lightness, strength, and resistance to environmental stressors.
They are used in various aircraft components, including wings, fuselages, and interior parts, offering significant weight reduction and improved fuel efficiency.
However, the complex nature of these materials presents challenges for quality control teams tasked with ensuring their reliability.
Because of these complexities, advanced testing methods like NDT become indispensable.
NDT allows manufacturers to detect flaws that are not visible to the naked eye, such as delaminations, voids, or inclusions that could compromise the structural integrity of aircraft parts.
Benefits of Implementing NDT in Quality Control
Implementing non-destructive testing in quality control processes offers numerous advantages.
Firstly, it enhances safety by ensuring that only components meeting the highest standards are used in aircraft construction.
By identifying potential failures before they manifest, NDT helps prevent catastrophic events.
Secondly, NDT contributes to cost-efficiency.
Detecting defects early in the manufacturing process can significantly reduce the expenses associated with repairs or part replacements after production.
Moreover, NDT supports regulatory compliance by providing documented evidence that parts meet or exceed industry standards.
This is particularly important in aviation, where regulations are stringent, and certification requires demonstrable adherence to specific guidelines.
Improved Reliability and Performance
One of the key benefits of NDT is its ability to significantly improve the reliability and performance of composite materials.
By using advanced testing techniques, manufacturers can ensure the structural integrity of components under various conditions.
This not only extends the lifespan of the parts but also enhances their performance, contributing to the overall efficiency of the aircraft.
Minimized Downtime
NDT enables quick and effective inspection of parts without the need for downtime in production lines.
This fast turnaround is crucial for maintaining productivity and meeting tight delivery schedules.
Unlike destructive testing methods, NDT allows for ongoing inspections, ensuring quality without halting operations.
Enhanced Customer Confidence
Consistent use of NDT builds trust with customers by demonstrating a commitment to quality and safety.
Aviation manufacturers can showcase their dedication to producing reliable and high-performing components, thereby strengthening client relationships and securing future contracts.
Diverse NDT Methods
There are several NDT methods available, each suited to different types of inspections and materials.
Multiple techniques can be employed, depending on the specific needs of the quality control department.
Here’s a closer look at some of these methods:
Ultrasonic Testing
Ultrasonic testing uses high-frequency sound waves to detect internal flaws in materials.
This method is highly effective for assessing the integrity of composite layers and locating defects such as delaminations or voids.
It is a versatile technique widely used in the aerospace industry due to its accuracy and efficiency.
Radiographic Testing
Radiographic testing involves the use of X-rays or gamma rays to examine the interior structure of a component.
This technique is useful for detecting subsurface defects and is often used for complex assemblies and parts in which dimensional accuracy is critical.
The resulting images provide a clear representation of the internal state of the material, allowing for detailed analysis.
Eddy Current Testing
Eddy current testing is a method used for detecting surface and near-surface defects on conductive materials.
It involves inducing an electromagnetic field into the material and analyzing the resulting currents.
This technique is particularly beneficial for detecting cracks and corrosion on aircraft parts, ensuring that they remain in optimal condition.
Conclusion
For leaders in quality control departments within the aviation parts manufacturing industry, adopting non-destructive testing methods is vital for improving the reliability of composite materials.
NDT provides an effective solution for uncovering potential defects without damaging the components, ensuring that only the highest quality parts are used in aircraft production.
By embracing the diverse range of NDT techniques, quality control teams can enhance safety standards, reduce costs, and build confidence among stakeholders.
As the aviation industry continues to evolve, the role of non-destructive testing will only grow in importance.
Quality control leaders must stay informed about the latest advancements in NDT to maintain their competitive edge and ensure the ongoing success of their operations.
資料ダウンロード
QCD調達購買管理クラウド「newji」は、調達購買部門で必要なQCD管理全てを備えた、現場特化型兼クラウド型の今世紀最高の購買管理システムとなります。
ユーザー登録
調達購買業務の効率化だけでなく、システムを導入することで、コスト削減や製品・資材のステータス可視化のほか、属人化していた購買情報の共有化による内部不正防止や統制にも役立ちます。
NEWJI DX
製造業に特化したデジタルトランスフォーメーション(DX)の実現を目指す請負開発型のコンサルティングサービスです。AI、iPaaS、および先端の技術を駆使して、製造プロセスの効率化、業務効率化、チームワーク強化、コスト削減、品質向上を実現します。このサービスは、製造業の課題を深く理解し、それに対する最適なデジタルソリューションを提供することで、企業が持続的な成長とイノベーションを達成できるようサポートします。
オンライン講座
製造業、主に購買・調達部門にお勤めの方々に向けた情報を配信しております。
新任の方やベテランの方、管理職を対象とした幅広いコンテンツをご用意しております。
お問い合わせ
コストダウンが利益に直結する術だと理解していても、なかなか前に進めることができない状況。そんな時は、newjiのコストダウン自動化機能で大きく利益貢献しよう!
(Β版非公開)