- お役立ち記事
- For operators in the machining industry! How to set cutting conditions to improve accuracy in skiving machining
For operators in the machining industry! How to set cutting conditions to improve accuracy in skiving machining
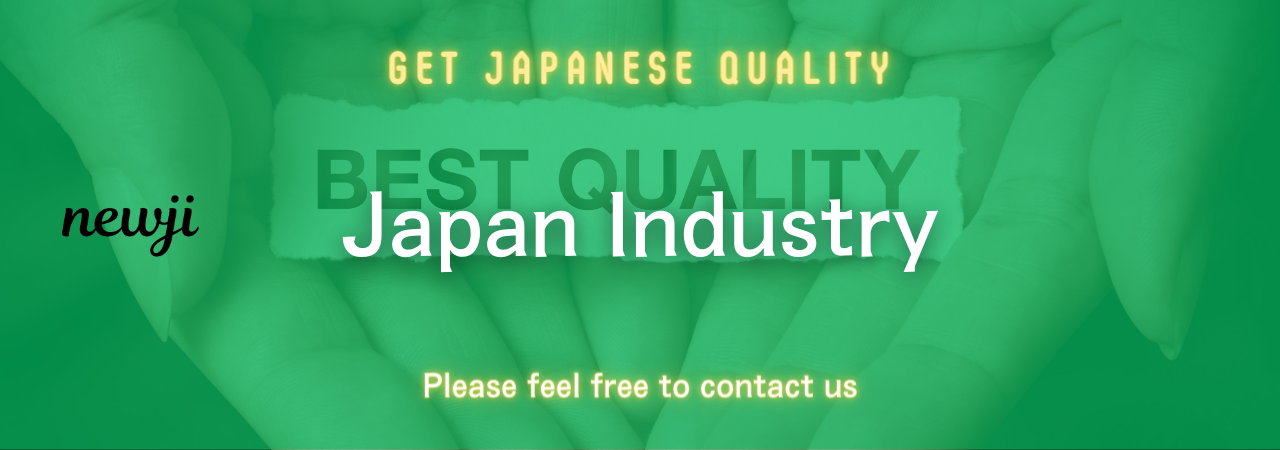
Skiving machining is a critical process in the machining industry known for its precision in creating smooth finishes and complex geometries in metal components.
For operators looking to enhance accuracy and efficiency, understanding how to set the right cutting conditions is paramount.
Below, we explore key factors to consider for optimal skiving performance.
目次
Understanding Skiving Machining
Skiving machining involves cutting a thin layer of material from the surface of a workpiece to achieve high-precision finishes.
This process is commonly used for manufacturing gears, splines, and other close-tolerance components.
The accuracy of skiving is fundamental to ensuring the quality and performance of the final product.
Before diving into setting cutting conditions, it is crucial to understand the principles of skiving.
Importance of Cutting Conditions
Cutting conditions refer to the combination of speed, feed rate, depth of cut, and tooling parameters applied during machining.
Setting these correctly is essential for optimizing the skiving process.
Inadequate settings can lead to poor surface finishes, tool wear, and even damage to the workpiece.
Conversely, precise control over these parameters can enhance accuracy and extend tool life.
Factors Affecting Skiving Process Accuracy
Several factors influence the accuracy and efficiency of skiving machining.
Here are some key considerations:
Material Properties
The material of the workpiece plays a significant role in determining cutting conditions.
Different materials react differently to cutting forces.
For example, harder materials may require slower cutting speeds and specific tooling to prevent excessive wear.
On the other hand, softer materials might allow for higher speeds but require careful management to avoid overheating and distortion.
Tool Selection
Choosing the right tool is crucial for skiving operations.
The tool’s geometry, material, and coating affect its performance and lifespan.
Carbide and high-speed steel tools are commonly used in skiving for their durability and ability to withstand high temperatures.
Additionally, tools with specific coatings, such as titanium nitride (TiN), improve wear resistance and reduce friction.
Cutting Speed
Cutting speed, measured in surface feet per minute (SFM) or meters per minute (MPM), dictates how fast the tool moves across the surface of the workpiece.
The optimal cutting speed is determined by the material and dimensions of both the workpiece and the tool.
It is essential to set the correct speed to balance between tool life and machining time, avoiding both excessive wear and inefficient production cycles.
Feed Rate
The feed rate is the speed at which the tool advances into the workpiece, typically measured in inches per minute (IPM) or millimeters per minute (MM/min).
A higher feed rate can increase machining efficiency but may compromise surface quality if not properly controlled.
Careful calibration of the feed rate ensures a precise cut without inducing vibrations or tool deflection.
Depth of Cut
The depth of cut refers to how deeply the tool penetrates the surface of the workpiece during each pass.
Adjusting the depth of cut is crucial for managing tool load and ensuring a smooth finish.
An excessively deep cut can cause tool breakage or overheating, while too shallow may require additional passes, increasing production time.
Coolant and Lubrication
The use of coolants and lubricants plays a vital role in skiving machining.
They help in maintaining tool temperature, reducing friction, and flushing away chips.
Selecting the right type of coolant and its application method can significantly enhance surface quality and tool life.
Setting Optimal Cutting Conditions
Setting the right cutting conditions involves a balanced approach to all the factors mentioned above.
Here’s a structured method to optimize your skiving operations:
Analyze Workpiece Material
Begin by understanding the properties of the workpiece material.
Gather data on its hardness, tensile strength, and thermal conductivity.
Precision machining often requires customization of conditions based on these material characteristics.
Select Appropriate Tools
Choose tools that are designed for skiving the material you’re working with.
Consider the tool geometry, material, and coating to ensure it can handle the conditions effectively.
Calculate Cutting Speed
Use material and tool data to determine the appropriate cutting speed.
Refer to manufacturer recommendations and industry standards for guidance.
Adjust as necessary based on trial runs and observation.
Determine Feed Rate and Depth of Cut
Assess the ideal feed rate by considering the tool and workpiece combination.
Start with conservative settings and gradually increase them while monitoring the quality of the cut.
Set the depth of cut to a level that the tool can manage without experiencing overloading.
Utilize Coolants Effectively
Apply coolants and lubricants to maintain the temperature and reduce the risk of thermal expansion or tool wear.
Ensure the delivery system is optimal for complete coverage of the cutting area.
Monitoring and Adjustments
Operators must continuously monitor the skiving process and be willing to make necessary adjustments.
Regular inspection of the finished workpiece, tool wear, and overall machine performance is essential.
Use digital tools and software for real-time data analysis to optimize further and refine cutting conditions.
By carefully setting and continuously adjusting the cutting conditions, operators in the machining industry can significantly improve the accuracy and efficiency of skiving operations.
Remaining informed on advancements in tool technology and machining strategies is crucial to maintaining a competitive edge.
Ensure ongoing training for operators to stay updated on the latest techniques and innovations in skiving machining.
資料ダウンロード
QCD調達購買管理クラウド「newji」は、調達購買部門で必要なQCD管理全てを備えた、現場特化型兼クラウド型の今世紀最高の購買管理システムとなります。
ユーザー登録
調達購買業務の効率化だけでなく、システムを導入することで、コスト削減や製品・資材のステータス可視化のほか、属人化していた購買情報の共有化による内部不正防止や統制にも役立ちます。
NEWJI DX
製造業に特化したデジタルトランスフォーメーション(DX)の実現を目指す請負開発型のコンサルティングサービスです。AI、iPaaS、および先端の技術を駆使して、製造プロセスの効率化、業務効率化、チームワーク強化、コスト削減、品質向上を実現します。このサービスは、製造業の課題を深く理解し、それに対する最適なデジタルソリューションを提供することで、企業が持続的な成長とイノベーションを達成できるようサポートします。
オンライン講座
製造業、主に購買・調達部門にお勤めの方々に向けた情報を配信しております。
新任の方やベテランの方、管理職を対象とした幅広いコンテンツをご用意しております。
お問い合わせ
コストダウンが利益に直結する術だと理解していても、なかなか前に進めることができない状況。そんな時は、newjiのコストダウン自動化機能で大きく利益貢献しよう!
(Β版非公開)