- お役立ち記事
- Key points for increasing efficiency and regular maintenance of heat exchangers that equipment managers in the chemical manufacturing industry should know
月間76,176名の
製造業ご担当者様が閲覧しています*
*2025年3月31日現在のGoogle Analyticsのデータより
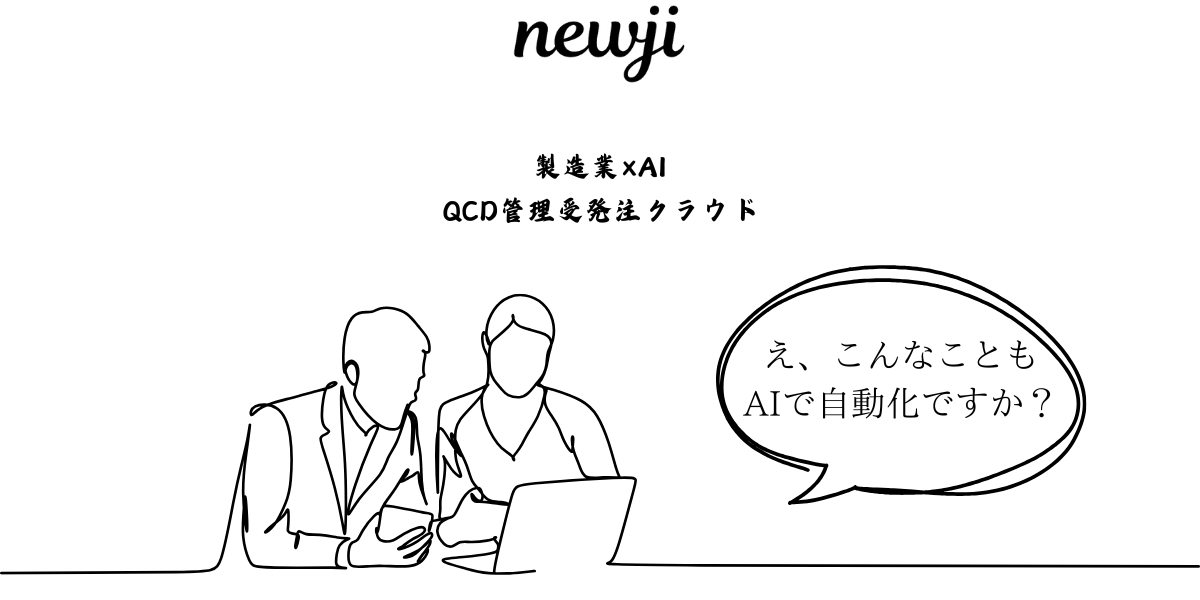
Key points for increasing efficiency and regular maintenance of heat exchangers that equipment managers in the chemical manufacturing industry should know
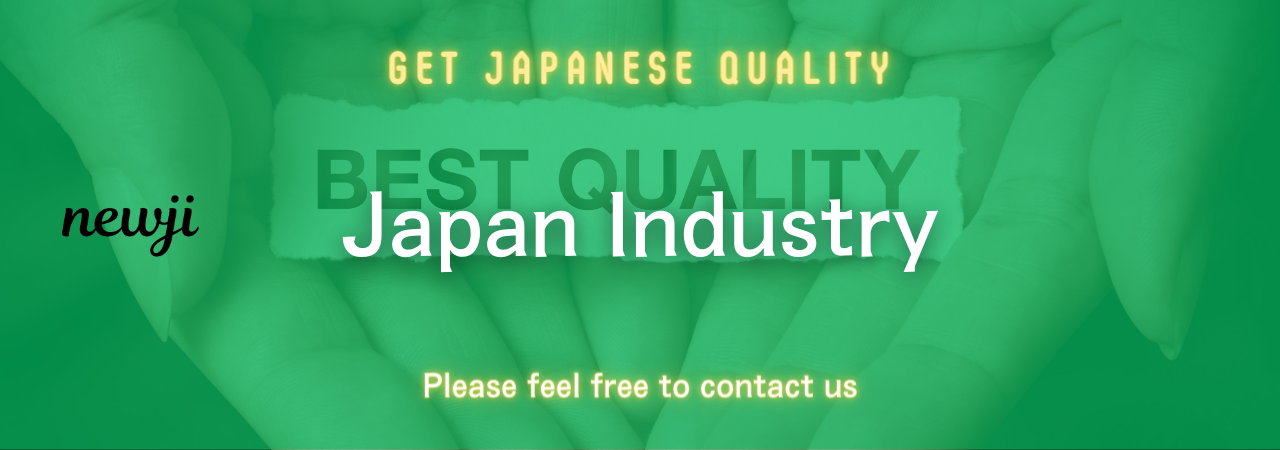
目次
Understanding Heat Exchangers in Chemical Manufacturing
Heat exchangers are crucial components in the chemical manufacturing industry, playing a significant role in energy conservation and productivity enhancement.
They transfer heat between two or more fluids without mixing them, ensuring optimal temperature control in various processes.
By efficiently managing heat exchangers, equipment managers can substantially improve the operational efficiency of their plants.
However, to achieve this, it’s essential to understand how these devices work and how to maintain them properly.
Types of Heat Exchangers
There are several types of heat exchangers used in the chemical industry, including:
1. **Shell and Tube Heat Exchangers** – These consist of tubes housed within a shell, where one fluid flows through the tubes, and another fluid flows around them.
They are versatile and suitable for high-pressure applications.
2. **Plate Heat Exchangers** – Comprised of corrugated plates, they allow fluid flow between plates, offering a large surface area for efficient heat transfer.
They are compact and ideal for liquids with similar viscosities.
3. **Air-Cooled Heat Exchangers** – This type uses air to cool fluids, eliminating the need for water, thus conserving resources and reducing operational costs.
4. **Double Pipe Heat Exchangers** – Consists of two coaxial pipes where one fluid flows in the annular space, and the other flows in the inner pipe.
They are simple and cost-effective for small-scale applications.
Understanding these types allows equipment managers to choose the appropriate exchanger based on specific process requirements, optimizing efficiency.
Importance of Regular Maintenance
Regular maintenance is vital for maintaining the performance and longevity of heat exchangers.
Neglecting maintenance can lead to reduced efficiency, increased energy consumption, and unexpected shutdowns due to equipment failure.
When a heat exchanger operates optimally, it leads to better temperature control, which is crucial for maintaining product quality and safety within the plant.
Therefore, equipment managers must implement a consistent maintenance routine.
Common Maintenance Activities
1. **Inspection** – Regular visual inspections help detect signs of wear and tear, leaks, or corrosion that could affect performance.
2. **Cleaning** – Fouling can significantly reduce heat exchanger efficiency.
Periodic cleaning, either mechanically or chemically, helps maintain optimal heat transfer rates.
3. **Monitoring** – Consistently monitor temperature and pressure differentials across the exchanger.
Sudden changes may indicate blockages or leaks needing immediate attention.
4. **Servicing** – Replacing worn gaskets, seals, or other components can prevent leaks and ensure efficient operation.
5. **Calibration** – Ensure sensors and monitors are calibrated to provide accurate data, essential for maintaining target processing conditions.
Strategies for Increasing Efficiency
In addition to regular maintenance, several strategies can enhance the efficiency of heat exchangers.
Optimize Operating Conditions
Every chemical process has specific temperature and pressure requirements.
Ensuring that heat exchangers operate within these parameters prevents energy wastage and improves performance.
Monitoring and adjusting flow rates can also impact efficiency.
Balancing the flow of fluids ensures maximum heat transfer occurs at the desired rate.
Upgrade to Modern Technology
Advancements in heat exchanger technology can also drive efficiency.
Modern designs often offer better heat transfer coefficients and require less maintenance.
Considering a switch to plate heat exchangers can significantly improve efficiency in processes where compatible.
Their compact design and higher heat transfer surface area make them a suitable choice for various applications.
Implement Energy Recovery Systems
Utilizing waste heat recovery systems can further enhance energy efficiency.
Reclaiming heat that would otherwise be lost and repurposing it within the plant reduces energy costs and can improve the overall sustainability of operations.
Developing a detailed energy analysis can help determine where energy recovery can be most effective, guiding further improvements.
Conclusion
Understanding the types of heat exchangers and the significance of regular maintenance is critical for equipment managers in the chemical manufacturing industry.
By implementing routine inspections, employing strategic cleaning and monitoring practices, and considering technological upgrades, managers can ensure the efficient and reliable operation of heat exchangers.
Optimizing these systems not only improves process efficiency, but also leads to significant energy and cost savings.
An efficient heat exchanger contributes to the overall success and sustainability of chemical manufacturing operations, ensuring the industry maintains high productivity and environmental responsibility standards.
資料ダウンロード
QCD管理受発注クラウド「newji」は、受発注部門で必要なQCD管理全てを備えた、現場特化型兼クラウド型の今世紀最高の受発注管理システムとなります。
ユーザー登録
受発注業務の効率化だけでなく、システムを導入することで、コスト削減や製品・資材のステータス可視化のほか、属人化していた受発注情報の共有化による内部不正防止や統制にも役立ちます。
NEWJI DX
製造業に特化したデジタルトランスフォーメーション(DX)の実現を目指す請負開発型のコンサルティングサービスです。AI、iPaaS、および先端の技術を駆使して、製造プロセスの効率化、業務効率化、チームワーク強化、コスト削減、品質向上を実現します。このサービスは、製造業の課題を深く理解し、それに対する最適なデジタルソリューションを提供することで、企業が持続的な成長とイノベーションを達成できるようサポートします。
製造業ニュース解説
製造業、主に購買・調達部門にお勤めの方々に向けた情報を配信しております。
新任の方やベテランの方、管理職を対象とした幅広いコンテンツをご用意しております。
お問い合わせ
コストダウンが利益に直結する術だと理解していても、なかなか前に進めることができない状況。そんな時は、newjiのコストダウン自動化機能で大きく利益貢献しよう!
(β版非公開)