- お役立ち記事
- For leaders in quality assurance departments in the coating industry! Enhancing coating film quality using cross-cut testing
For leaders in quality assurance departments in the coating industry! Enhancing coating film quality using cross-cut testing
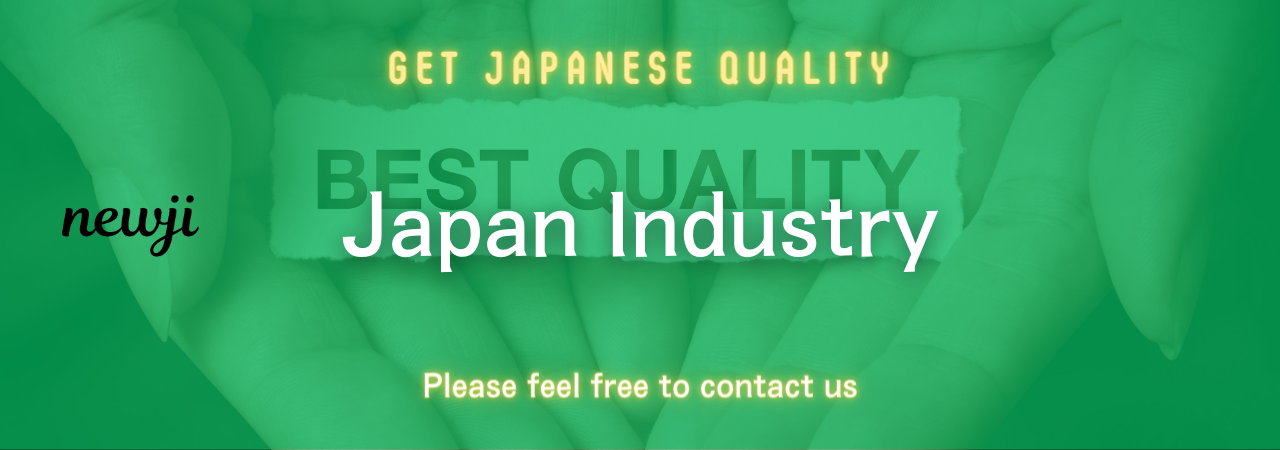
目次
Understanding Coating Film Quality
In the coating industry, maintaining high-quality standards is paramount for ensuring customer satisfaction and product durability.
Coatings provide not just aesthetic enhancements but also protection against environmental factors such as corrosion and weathering.
Ensuring the robustness and longevity of these coatings is a major responsibility of quality assurance departments.
One effective method for assessing coating film quality is the cross-cut test.
What is Cross-Cut Testing?
Cross-cut testing, also known as adhesion testing, is a simple and effective method to evaluate the adhesion strength of a coating film to substrates.
This test involves making cuts in the coating film to form a grid pattern, then assessing how much of the coating peels off.
It provides a clear visual and quantitative measure of a coating’s adhesion quality.
This method is a standardized test widely used due to its reliability and direct insights into the coating’s performance.
The Importance of Cross-Cut Testing
Cross-cut testing is crucial for several reasons.
Firstly, it helps identify potential adhesion issues that may lead to premature coating failure, impacting the product’s lifespan and performance.
By detecting weaknesses early, adjustments can be made to the formulation or application process, enhancing the overall quality of the coating.
Secondly, the results from a cross-cut test provide feedback for continuous improvement.
Quality assurance teams can use this data to refine their processes, ensuring coatings consistently meet the required standards.
Moreover, it helps in confirming compliance with industry regulations and standards, which is essential for maintaining a strong reputation and avoiding potential legal issues.
The Process of Cross-Cut Testing
Performing a cross-cut test involves several detailed steps to ensure accuracy and reliability of results.
Preparation of the Sample
The first step in cross-cut testing is preparing the sample.
It is essential to select a representative sample that closely resembles the actual application.
This ensures that the test results are applicable to real-world conditions.
The substrate should be clean and free from contaminants to avoid skewed results.
Executing the Cross-Cut
Using a specialized cross-cut tool, a series of cuts are made through the coating down to the substrate.
These cuts form a grid pattern, often with six to eleven parallel lines intersected by another set of lines.
The number of squares and width between cuts can vary depending on the standard being followed, such as ASTM D3359 or ISO 2409.
Assessment of Results
After making the cross-cuts, a standardized tape is applied over the grid and then quickly removed.
The amount of coating adhering to the tape determines the adhesion classification.
A visual inspection is conducted, and the coating’s adhesion is rated based on the amount of flaking and detachment from the substrate.
Results are categorized into classes, with Class 0 indicating perfect adhesion and Class 5 indicating poor adhesion.
Enhancing Coating Quality with Cross-Cut Testing
Quality assurance teams can leverage cross-cut test results to enhance coating film quality significantly.
Identifying Adhesion Problems
Cross-cut testing is key in identifying adhesion problems that could affect the performance of the final product.
Knowing the exact point of failure allows teams to adjust variables such as surface preparation, coating formulation, or curing conditions to improve adhesion.
Optimizing Coating Formulations
By understanding which coatings adhere better, manufacturers can refine their formulations for better performance.
This could involve experimenting with different binders, pigments, or additives to find the optimal combination for strong adhesion.
Improving Surface Preparation Techniques
Surface preparation is critical for coating adhesion.
Cross-cut testing can reveal whether issues arise from poor surface cleaning or treatment.
By improving preparation techniques such as blasting, priming, or etching, adhesion can be enhanced significantly.
Examining Application Methods
The method of application has a substantial impact on coating adhesion.
Cross-cut results can indicate if changes in application techniques, such as spray pattern, pressure, or angle, might improve adhesion.
This ensures uniform coverage and reduces the risk of defects.
Conclusion
In a competitive coating industry, ensuring high-quality standards is essential for maintaining customer trust and product reliability.
Cross-cut testing stands out as a valuable tool for quality assurance departments.
Not only does it provide critical insights into adhesion properties, but it also supports continuous improvement efforts.
By incorporating cross-cut testing into regular quality checks, coating manufacturers can enhance film quality, assure compliance with standards, and ultimately deliver superior products to their customers.
For leaders in the quality assurance departments, embracing this testing method can be the difference between meeting industry standards and setting new benchmarks for excellence.
資料ダウンロード
QCD調達購買管理クラウド「newji」は、調達購買部門で必要なQCD管理全てを備えた、現場特化型兼クラウド型の今世紀最高の購買管理システムとなります。
ユーザー登録
調達購買業務の効率化だけでなく、システムを導入することで、コスト削減や製品・資材のステータス可視化のほか、属人化していた購買情報の共有化による内部不正防止や統制にも役立ちます。
NEWJI DX
製造業に特化したデジタルトランスフォーメーション(DX)の実現を目指す請負開発型のコンサルティングサービスです。AI、iPaaS、および先端の技術を駆使して、製造プロセスの効率化、業務効率化、チームワーク強化、コスト削減、品質向上を実現します。このサービスは、製造業の課題を深く理解し、それに対する最適なデジタルソリューションを提供することで、企業が持続的な成長とイノベーションを達成できるようサポートします。
オンライン講座
製造業、主に購買・調達部門にお勤めの方々に向けた情報を配信しております。
新任の方やベテランの方、管理職を対象とした幅広いコンテンツをご用意しております。
お問い合わせ
コストダウンが利益に直結する術だと理解していても、なかなか前に進めることができない状況。そんな時は、newjiのコストダウン自動化機能で大きく利益貢献しよう!
(Β版非公開)