- お役立ち記事
- For operators in the machining industry! A practical guide to adjusting the cutting edge for high-precision gear machining on hobbing machines
For operators in the machining industry! A practical guide to adjusting the cutting edge for high-precision gear machining on hobbing machines
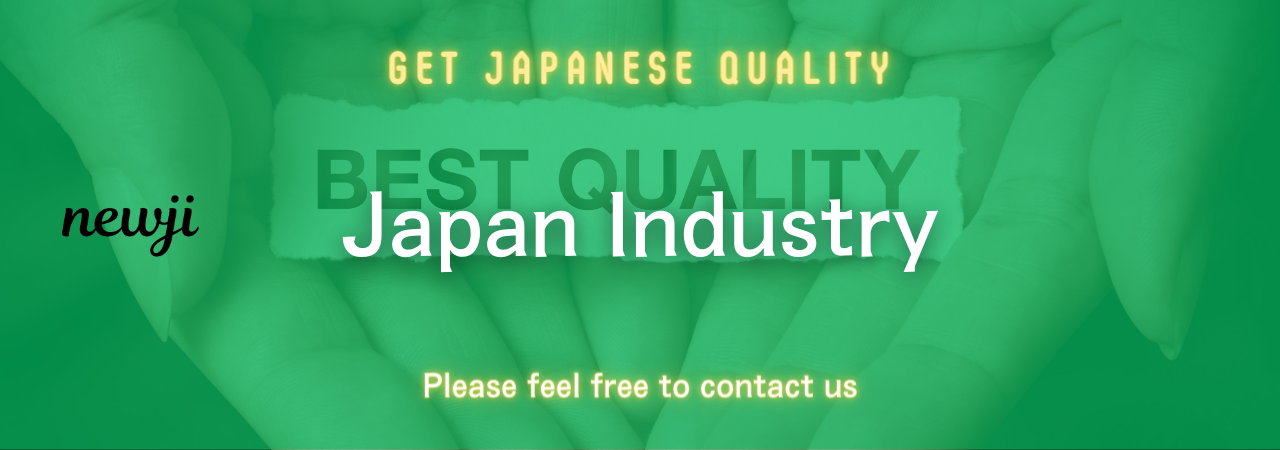
目次
Understanding the Basics of Gear Hobbing
Gear hobbing is a machining process that involves the cutting of gears and splines, using a specialized cutting tool known as a hob.
It’s a highly efficient and precise method used in creating complex gear structures found in various industries, from automotive to aerospace.
The success of gear hobbing largely depends on several factors, with the cutting edge of the hob playing a pivotal role.
The Importance of the Cutting Edge
The cutting edge of the hob is where the metal meets the tool.
It directly influences the quality of the gear machined.
A sharp, well-maintained cutting edge ensures high precision, smooth surface finishes, and longer tool life.
On the contrary, a dull or damaged cutting edge can lead to inaccuracies, poor surface quality, and increased tool wear.
Preparing for High-Precision Machining
Achieving high-precision gear machining on hobbing machines requires thorough preparation.
This not only involves setting up the hobbing machine correctly but also understanding the material you are working with.
Each material type, whether it’s steel, brass, or aluminum, behaves differently under machining conditions.
Therefore, selecting the appropriate hob material and geometry is essential.
Selecting the Right Hob
Choosing the correct hob for your machining process is crucial.
Hobs come in various designs and materials, such as high-speed steel (HSS) and carbide.
While carbide hobs offer longer life and higher cutting speeds, HSS hobs are more economical and can handle a wider range of materials.
Furthermore, the hob’s geometry—its tooth count, pressure angle, and helix angle—must be optimized for the specific gear design you are working on.
Proper Machine Setup
A properly set up hobbing machine is integral to achieving precision.
Ensure that the hob is mounted securely and aligned correctly with the gear blank.
The machine’s spindle speed and feed rate must be calibrated to suit the hob’s material and geometry, as well as the gear’s requirements.
Attention to these details will reduce vibration, minimize tool deflection, and ultimately improve gear precision.
Adjusting the Cutting Edge
Fine-tuning the cutting edge is a critical step in achieving high-precision gear machining.
This involves meticulous sharpening and profiling of the hob.
Sharpening Techniques
Sharpening the hob involves grinding its cutting edges to restore sharpness and maintain the correct profile.
Regular inspection of the hob is necessary to determine the need for sharpening.
A dull hob should be sharpened promptly to prevent damage to the workpiece and ensure a clean cut.
The grinding process should be precise, maintaining the original geometry of the hob to ensure consistent performance.
Maintaining Profile Integrity
Maintaining the correct profile on the cutting edge is essential for gear quality.
Any deviation in the profile could lead to inaccuracies in the gear shape.
Use precision grinding equipment and regularly check the hob against manufacturer specifications to ensure the profile remains intact.
Monitoring and Maintenance
Once the hob is properly adjusted, ongoing monitoring and maintenance are necessary to sustain precision.
Regular Inspections
Regularly inspect the hob for signs of wear and improper cutting.
Checking after each production run or during machine downtimes can help identify potential issues before they affect production.
Look for signs of uneven wear, chipping, or rounding on the cutting edges.
Replacing or Reconditioning Hobs
Even with regular maintenance, hobs will eventually require replacement or reconditioning.
Know the limits of your hob’s lifespan and plan for timely replacement to avoid compromising gear quality.
When reconditioning hobs, send them to a certified service provider to ensure they are returned to factory specifications.
Quality Assurance in Gear Production
Quality control is a vital component of high-precision gear machining.
Employ advanced measurement tools and techniques to verify each gear meets design specifications.
Using Precision Measurement Tools
Utilize tools such as gear measurement machines, profilometers, and coordinate measuring machines (CMM) to ensure dimensional accuracy.
Regular calibration of these tools is essential for reliable results.
Documenting and Analyzing Results
Document gear measurements and analyze these results to identify trends or patterns.
This data can provide valuable insights into your machining process and indicate areas for improvement.
Conclusion
High-precision gear machining on hobbing machines demands meticulous attention to detail, starting with the cutting edge.
By selecting suitable hobs, correctly setting up machines, and maintaining cutting edge integrity, machinists can achieve superior gear quality.
Combined with regular maintenance and robust quality control practices, these efforts will lead to consistent and reliable gear production.
Understanding and applying these principles is key for any operator looking to excel in the machining industry.
資料ダウンロード
QCD調達購買管理クラウド「newji」は、調達購買部門で必要なQCD管理全てを備えた、現場特化型兼クラウド型の今世紀最高の購買管理システムとなります。
ユーザー登録
調達購買業務の効率化だけでなく、システムを導入することで、コスト削減や製品・資材のステータス可視化のほか、属人化していた購買情報の共有化による内部不正防止や統制にも役立ちます。
NEWJI DX
製造業に特化したデジタルトランスフォーメーション(DX)の実現を目指す請負開発型のコンサルティングサービスです。AI、iPaaS、および先端の技術を駆使して、製造プロセスの効率化、業務効率化、チームワーク強化、コスト削減、品質向上を実現します。このサービスは、製造業の課題を深く理解し、それに対する最適なデジタルソリューションを提供することで、企業が持続的な成長とイノベーションを達成できるようサポートします。
オンライン講座
製造業、主に購買・調達部門にお勤めの方々に向けた情報を配信しております。
新任の方やベテランの方、管理職を対象とした幅広いコンテンツをご用意しております。
お問い合わせ
コストダウンが利益に直結する術だと理解していても、なかなか前に進めることができない状況。そんな時は、newjiのコストダウン自動化機能で大きく利益貢献しよう!
(Β版非公開)