- お役立ち記事
- For managers of quality assurance departments in the plastic molding industry! Cooling management method to suppress shrinkage of molded products
For managers of quality assurance departments in the plastic molding industry! Cooling management method to suppress shrinkage of molded products
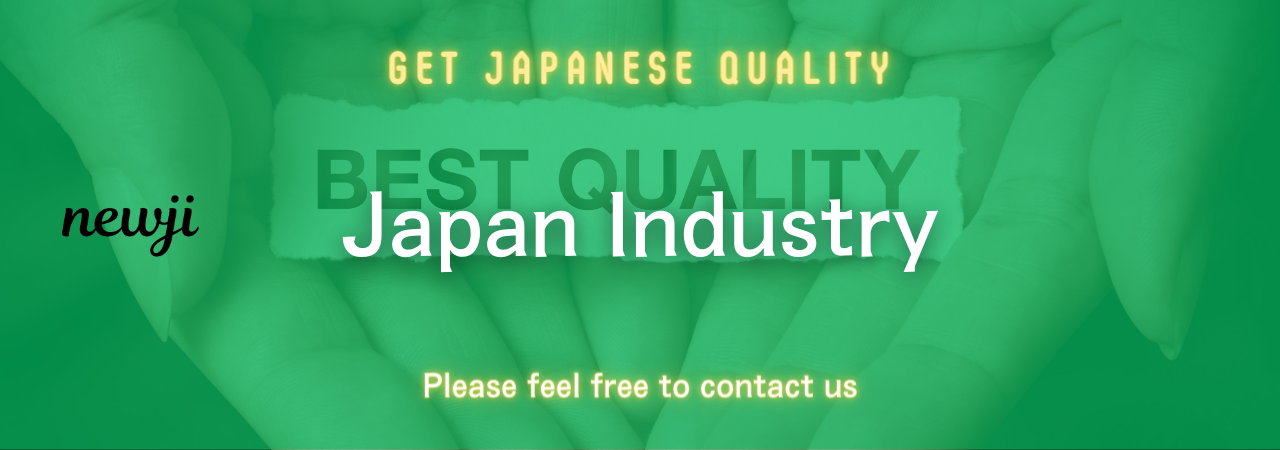
目次
Understanding the Importance of Cooling in Plastic Molding
Plastic molding is a precise process that involves several crucial stages, one of which is cooling.
While often overlooked, cooling plays a significant role in the quality of the final molded product.
For managers in the quality assurance departments of the plastic molding industry, ensuring that cooling is accurately managed can be a game-changer.
Improper cooling can lead to defects such as shrinkage, which can affect the structural integrity and appearance of the plastic product.
What is Shrinkage in Molded Products?
Shrinkage in plastic molded products is a common issue that’s caused by the cooling and solidification process.
As the plastic cools and hardens inside the mold, it contracts.
Depending on the type of plastic used and the conditions under which it cools, this contraction can cause visible warping or internal stress, leading to undesirable distortion or weakening of the product.
The Impact of Shrinkage
Shrinkage not only affects the functionality of the product but also its aesthetic appeal.
For products that require tight dimensional tolerances, such as automotive parts or consumer electronics, shrinkage can lead to assembly issues or operational failures.
Understanding and controlling shrinkage is vital to maintain product quality and reduce costly defects and recalls.
Factors Affecting Cooling and Shrinkage
Several factors influence how plastic cools and shrinks, which include:
1. Material Properties
Different polymers have varying properties that affect their cooling rates and shrinkage patterns.
For example, crystalline polymers like polyethylene tend to shrink more than amorphous polymers like polystyrene.
Selecting the appropriate material for your product is crucial to managing shrinkage.
2. Mold Design
The design of the mold plays a pivotal role in cooling efficiency.
Molds with uniform wall thickness tend to cool evenly, reducing the chances of differential shrinkage.
Incorporating proper cooling channels in the mold design is essential for uniform cooling.
3. Cooling Time and Temperature
The duration for which the plastic is allowed to cool can significantly impact shrinkage.
Longer cooling times can lead to better dimensional stability but may increase cycle times.
Conversely, inadequate cooling can cause excessive shrinkage.
Finding the balance between cycle time and cooling effectiveness is crucial.
4. Injection Pressure and Speed
Higher injection pressures and speeds can compress the polymer more, affecting how it cools and shrinks.
Adjusting these parameters can help manage shrinkage, but must be done carefully to avoid introducing other defects.
Strategies for Effective Cooling Management
To suppress shrinkage and improve product quality, consider these cooling management strategies:
Optimizing Mold Design
Designing molds with balanced cooling channels can help achieve uniform cooling rates.
Use computational fluid dynamics (CFD) software to simulate and optimize cooling performance.
Consider the use of conformal cooling channels, which follow the shape of the mold cavity, enhancing uniform cooling.
Material Selection and Testing
Select materials with lower shrinkage potential and test them under different cooling conditions.
Utilize rheological and shrinkage testing data to predict and prevent potential issues before mass production.
Cooling Time Adjustment
Analyze the cooling curve specific to each material and adjust the cooling time accordingly.
Use real-time monitoring systems to track temperatures in critical areas of the mold.
Fine-tuning the cooling time based on trial runs can lead to significant improvements in product quality.
Advanced Process Control Systems
Invest in advanced control systems that allow for precise monitoring and regulation of the molding process.
Implement sensors and feedback loops in the cooling system to maintain consistent cooling performance.
This can reduce human error and ensure repeatable cooling conditions.
Training and Education for Quality Assurance Teams
Educating quality assurance teams on the intricacies of cooling and its impact on shrinkage is vital.
Regular training sessions can keep teams updated on the latest methodologies and technologies in cooling management.
Empower your team with the knowledge to troubleshoot issues related to cooling and shrinkage effectively.
Conclusion
Effective cooling management is a critical component in producing high-quality plastic molded products.
By understanding the factors that contribute to shrinkage and employing strategic cooling solutions, managers in the quality assurance departments can significantly reduce defects.
Investing in technology, design optimization, and team education paves the way for improved product reliability and customer satisfaction.
With a focused approach, shrinkage can be minimized, enhancing the overall success of the plastic molding process.
資料ダウンロード
QCD調達購買管理クラウド「newji」は、調達購買部門で必要なQCD管理全てを備えた、現場特化型兼クラウド型の今世紀最高の購買管理システムとなります。
ユーザー登録
調達購買業務の効率化だけでなく、システムを導入することで、コスト削減や製品・資材のステータス可視化のほか、属人化していた購買情報の共有化による内部不正防止や統制にも役立ちます。
NEWJI DX
製造業に特化したデジタルトランスフォーメーション(DX)の実現を目指す請負開発型のコンサルティングサービスです。AI、iPaaS、および先端の技術を駆使して、製造プロセスの効率化、業務効率化、チームワーク強化、コスト削減、品質向上を実現します。このサービスは、製造業の課題を深く理解し、それに対する最適なデジタルソリューションを提供することで、企業が持続的な成長とイノベーションを達成できるようサポートします。
オンライン講座
製造業、主に購買・調達部門にお勤めの方々に向けた情報を配信しております。
新任の方やベテランの方、管理職を対象とした幅広いコンテンツをご用意しております。
お問い合わせ
コストダウンが利益に直結する術だと理解していても、なかなか前に進めることができない状況。そんな時は、newjiのコストダウン自動化機能で大きく利益貢献しよう!
(Β版非公開)