- お役立ち記事
- For managers of equipment management departments in the plastic molding industry! How to introduce pokayoke technology to eliminate human error
For managers of equipment management departments in the plastic molding industry! How to introduce pokayoke technology to eliminate human error
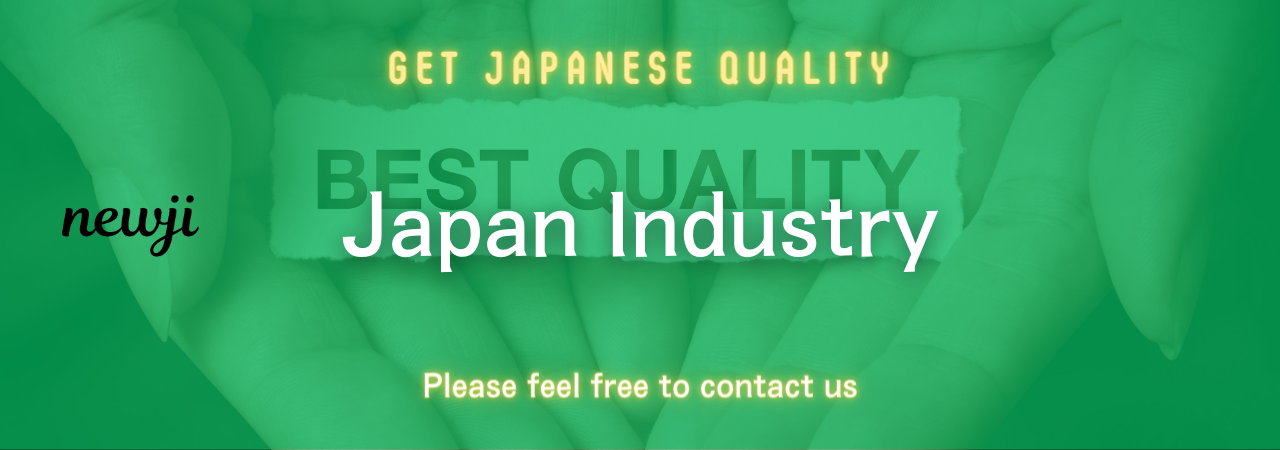
目次
Understanding Pokayoke Technology
Pokayoke, a Japanese term meaning “mistake-proofing,” is a simple yet effective approach to preventing human errors in manufacturing processes.
Originally introduced by Shigeo Shingo in the Toyota Production System, pokayoke aims to design products and systems in a way that makes it nearly impossible for mistakes to occur.
In the plastic molding industry, where precision and accuracy are crucial, integrating pokayoke technology can significantly enhance operational efficiency and product quality.
For equipment management departments, understanding this concept is the first step towards successful implementation.
By adopting pokayoke technology, managers can reduce production defects, lower costs, and improve safety, ultimately leading to a better work environment and higher customer satisfaction.
The Importance of Human Error Reduction
Human errors are inevitable, especially in complex industrial processes.
In the plastic molding industry, such errors can result in significant financial losses and compromised product quality.
For managers in equipment management departments, it is essential to implement strategies that minimize these errors.
Human errors can occur at various stages of the production process, including design, assembly, and quality control.
Pokayoke technology addresses these issues by focusing on the root causes of errors and implementing preventative measures.
This approach not only saves time and resources but also helps build a culture of quality and accountability within the organization.
Identifying Areas for Pokayoke Implementation
Before introducing pokayoke technology, managers must first identify areas within their operations that are most prone to errors.
This process involves analyzing production data, observing workflows, and consulting with employees to gain insights into potential problem areas.
Common issues in the plastic molding industry include material handling errors, incorrect machine settings, and improper part assembly.
By pinpointing these areas, managers can develop targeted pokayoke solutions to mitigate risks.
Material Handling
Incorrect material handling is a frequent source of errors in plastic molding.
Implementing pokayoke devices, such as color-coded bins or RFID tags, can ensure that the right materials are used for each production run.
Machine Settings
Machines must be set correctly to produce high-quality products.
Incorporating sensors or programmable logic controllers (PLCs) that automatically adjust settings based on specific requirements can significantly reduce human oversight and errors.
Part Assembly
Assembly errors can be minimized by designing fixtures and jigs that only allow parts to be assembled in the correct orientation.
Visual aids and templates can also assist workers in assembling parts accurately.
Steps to Implement Pokayoke Technology
Integrating pokayoke technology into the plastic molding industry requires careful planning and execution.
Here are the key steps managers can follow to ensure a successful implementation:
1. Conduct a Thorough Analysis
Begin by conducting a comprehensive analysis of your current production processes.
Identify common error-prone tasks, review past incidents, and consult with employees for additional insights.
This will help you understand where pokayoke technology can bring the most benefits.
2. Develop Solutions
Once you’ve identified areas for improvement, brainstorm and develop simple, practical pokayoke solutions.
Focus on designing foolproof systems or devices that prevent errors from occurring.
Consider involving cross-functional teams in this process to gather diverse perspectives and ideas.
3. Educate and Train Employees
Educating and training employees is crucial to the successful adoption of pokayoke technology.
Provide comprehensive training sessions to ensure workers understand the new systems and processes.
Encourage open communication and feedback to address any concerns or issues they may have.
4. Implement and Monitor
Deploy your pokayoke solutions and monitor the results closely.
Collect data on error rates, production efficiency, and product quality to assess the impact of the technology.
Make adjustments and improvements as necessary to optimize performance.
5. Foster a Culture of Continuous Improvement
Promote a culture of continuous improvement by encouraging employees to identify and suggest further improvements.
Regularly review and refine your pokayoke strategies to stay ahead of potential challenges and maintain high-quality standards.
Benefits of Pokayoke in the Plastic Molding Industry
Implementing pokayoke technology offers numerous benefits for managers in the plastic molding industry.
By reducing human errors, companies can experience increased efficiency and productivity, as fewer resources are wasted on rework or defect management.
Enhanced product quality leads to higher customer satisfaction, resulting in repeat business and positive brand reputation.
Additionally, streamlined operations contribute to cost savings, as error-related expenses decrease over time.
Moreover, pokayoke solutions can improve workplace safety by minimizing the risk of accidents related to human errors.
Ultimately, these advantages make pokayoke integration a valuable investment for equipment management departments looking to optimize their processes and achieve long-term success.
By understanding pokayoke technology, identifying areas for implementation, and following a structured approach, managers can effectively eliminate human errors and achieve operational excellence.
資料ダウンロード
QCD調達購買管理クラウド「newji」は、調達購買部門で必要なQCD管理全てを備えた、現場特化型兼クラウド型の今世紀最高の購買管理システムとなります。
ユーザー登録
調達購買業務の効率化だけでなく、システムを導入することで、コスト削減や製品・資材のステータス可視化のほか、属人化していた購買情報の共有化による内部不正防止や統制にも役立ちます。
NEWJI DX
製造業に特化したデジタルトランスフォーメーション(DX)の実現を目指す請負開発型のコンサルティングサービスです。AI、iPaaS、および先端の技術を駆使して、製造プロセスの効率化、業務効率化、チームワーク強化、コスト削減、品質向上を実現します。このサービスは、製造業の課題を深く理解し、それに対する最適なデジタルソリューションを提供することで、企業が持続的な成長とイノベーションを達成できるようサポートします。
オンライン講座
製造業、主に購買・調達部門にお勤めの方々に向けた情報を配信しております。
新任の方やベテランの方、管理職を対象とした幅広いコンテンツをご用意しております。
お問い合わせ
コストダウンが利益に直結する術だと理解していても、なかなか前に進めることができない状況。そんな時は、newjiのコストダウン自動化機能で大きく利益貢献しよう!
(Β版非公開)