- お役立ち記事
- A must-see for design department managers in the plastic molding industry! Guidelines for increasing part strength with insert molding
A must-see for design department managers in the plastic molding industry! Guidelines for increasing part strength with insert molding
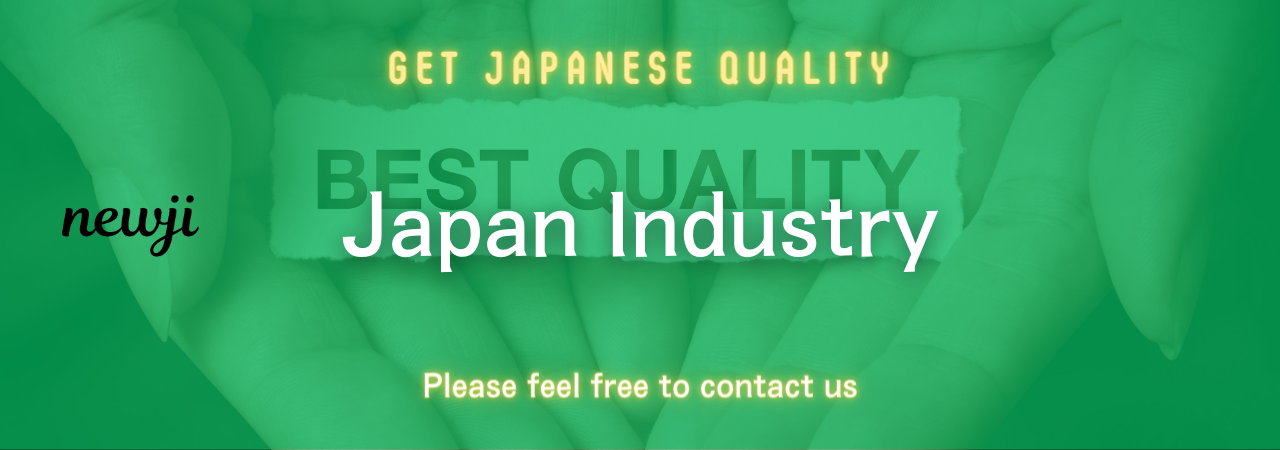
目次
Understanding Insert Molding
Insert molding is a game-changer in the plastic molding industry, offering a way to enhance part strength while maintaining flexibility in design.
This process involves inserting a metal or another material into a mold and then injecting plastic over it to form a single cohesive piece.
The result is a part with superior strength due to the combination of materials, making it a perfect choice for various applications across industries.
The Benefits of Insert Molding
Insert molding provides numerous advantages, particularly in terms of part strength and durability.
The combination of different materials can result in parts that withstand more stress and wear than their conventional plastic counterparts.
This is particularly beneficial in industries where safety, reliability, and longevity are paramount, such as automotive components, medical devices, and electrical housings.
Not only does insert molding increase strength, but it also allows for complex designs that would otherwise be impossible or too costly to produce with traditional methods.
By incorporating different materials into the initial design, engineers can tackle complex requirements without adding unnecessary weight or sacrificing performance.
Cost-Effectiveness and Efficiency
While initially, insert molding might seem more costly due to the integration of additional materials, it often proves cost-effective in the long run.
The enhanced durability and reduced failure rates mean fewer parts need replacing, saving both time and money.
Additionally, insert molding often reduces the need for secondary operations as complex assemblies can be completed in a single step.
Insert molding also contributes to faster production times.
Because this method eliminates the need for additional assembly processes, production lines can operate more efficiently, reducing lead times and getting products to market faster.
Guidelines for Increasing Part Strength with Insert Molding
For design department managers in the plastic molding industry, increasing part strength needs a strategic approach.
Here are some guidelines to help you achieve optimal results with insert molding:
Select the Right Materials
Choosing the right materials for both the insert and the plastic is critical in achieving the desired part strength.
Consider the mechanical, thermal, and environmental properties of the materials in relation to the intended use of the product.
Metal inserts such as stainless steel or brass can add significant tensile strength, while ceramic or other composites might be used for their thermal resistance properties.
Optimize Design for Molding
The design should facilitate a seamless union between the insert and the molded plastic.
This includes accommodating for any shrinkage that the plastic might undergo upon cooling, which can impact the integrity of the bond.
Make sure to design the insert with features such as knurled surfaces or holes to improve adhesion with the plastic.
Test Thoroughly
Conduct comprehensive testing before full-scale production to ensure the bond strength between materials meets performance standards.
This might include tensile tests, fatigue tests, and environmental testing to assess how the part will perform under various conditions.
Testing not only verifies the immediate strength but can also predict long-term performance.
Utilize Advanced Simulation Software
Use advanced simulation tools to predict the flow of plastic around the insert, checking for potential issues such as air pockets, inadequate filling, or excessive stress.
Simulation software can help identify problem areas early in the design phase, enabling you to make necessary adjustments before production.
Challenges and Solutions
While insert molding offers many benefits, it comes with its set of challenges.
It requires precision and careful planning to avoid common pitfalls such as misalignment or inadequate bonding.
Potential Challenges
One of the main challenges is ensuring proper alignment of the insert within the mold.
Misalignment can lead to uneven material distribution and weakened structures.
Another potential issue is the insulation effect, where the insert prevents the plastic from cooling uniformly, leading to warping or weakening.
Addressing Challenges
To address these challenges, use fixtures or guides to ensure precise placement of the insert within the mold.
Consider using heated molds to facilitate uniform cooling and bonding, or adjust the material composition to better manage the cooling process.
Future of Insert Molding in Design
The future of insert molding in the plastic molding industry looks promising, with continued advancements in materials and molding technology.
As manufacturers look for ways to innovate and improve product performance, insert molding stands out as a key method.
Its ability to combine multiple materials into one durable part opens possibilities for new designs and functions that push beyond traditional limits.
With the continued investment in research and development, the plastic molding industry can expect even more efficient and robust solutions from insert molding.
These advancements will likely lead to more lightweight materials with equal or greater strength, further enhancing the competitiveness of products in various markets.
By understanding the principles and best practices of insert molding, design department managers can leverage this technique to revolutionize their manufacturing processes and products.
By focusing on the nuances of material selection, design optimization, and thorough testing, they can ensure their products meet the highest standards of strength and quality.
資料ダウンロード
QCD調達購買管理クラウド「newji」は、調達購買部門で必要なQCD管理全てを備えた、現場特化型兼クラウド型の今世紀最高の購買管理システムとなります。
ユーザー登録
調達購買業務の効率化だけでなく、システムを導入することで、コスト削減や製品・資材のステータス可視化のほか、属人化していた購買情報の共有化による内部不正防止や統制にも役立ちます。
NEWJI DX
製造業に特化したデジタルトランスフォーメーション(DX)の実現を目指す請負開発型のコンサルティングサービスです。AI、iPaaS、および先端の技術を駆使して、製造プロセスの効率化、業務効率化、チームワーク強化、コスト削減、品質向上を実現します。このサービスは、製造業の課題を深く理解し、それに対する最適なデジタルソリューションを提供することで、企業が持続的な成長とイノベーションを達成できるようサポートします。
オンライン講座
製造業、主に購買・調達部門にお勤めの方々に向けた情報を配信しております。
新任の方やベテランの方、管理職を対象とした幅広いコンテンツをご用意しております。
お問い合わせ
コストダウンが利益に直結する術だと理解していても、なかなか前に進めることができない状況。そんな時は、newjiのコストダウン自動化機能で大きく利益貢献しよう!
(Β版非公開)