- お役立ち記事
- A must-see for new employees in the quality assurance department of the medical device manufacturing industry! Building a traceability system based on ISO13485
A must-see for new employees in the quality assurance department of the medical device manufacturing industry! Building a traceability system based on ISO13485
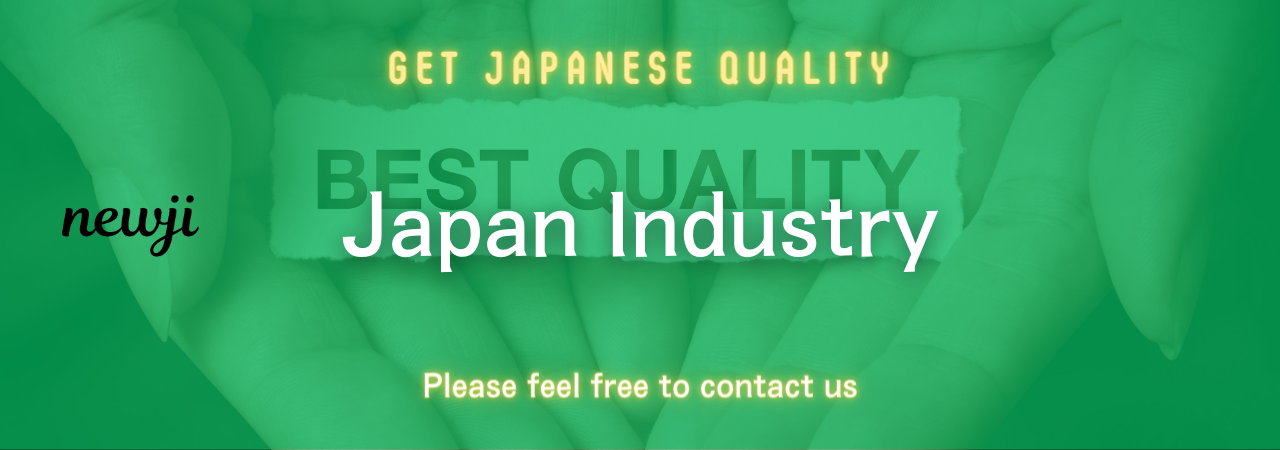
目次
Understanding ISO 13485 and Its Importance
ISO 13485 is an internationally recognized standard specifically for the quality management systems of companies in the medical device sector.
This standard ensures organizations meet regulatory requirements applicable to medical devices, from design to production and post-production processes.
For new employees in the quality assurance department of a medical device manufacturing company, understanding ISO 13485 is crucial.
This standard provides a framework for maintaining the quality and safety of medical devices, significantly impacting patient safety and satisfaction.
What Is a Traceability System?
Traceability in the context of medical device manufacturing refers to the capability to trace the history, application, or location of an item through recorded identification.
A robust traceability system allows companies to track a product throughout the manufacturing process, from raw materials to the end user.
Traceability is essential in ensuring the integrity of medical devices, enabling quick and effective responses when quality issues arise.
It is a critical component of compliance with ISO 13485, as it provides evidence of compliance throughout the product lifecycle.
Why New Employees Should Focus on Traceability
For new employees in quality assurance, understanding and participating in building a traceability system can enhance their ability to ensure product quality and compliance.
Traceability is not just a process; it forms the backbone of a comprehensive quality assurance system that meets ISO 13485 standards.
Focusing on traceability helps in:
1. Identifying the source of defects,
2. Ensuring that only approved materials are used,
3. Confirming that processes are followed in accordance with protocol,
4. Streamlining the process of responding to product recalls or audits.
Steps to Building a Traceability System
1. Understanding the Requirements
New employees should first understand the specific requirements of ISO 13485 related to traceability.
This includes knowing what documentation is necessary, the types of records that should be maintained, and how these records should be managed.
2. Implementing Effective Documentation
Strong documentation practices are key to building a traceability system.
Every stage of the manufacturing process should be documented carefully, including:
– The receipt of raw materials,
– In-process data,
– Final product testing,
– Delivery records.
New employees should be diligent in recording this information clearly and accurately.
3. Utilizing Technology
Modern traceability systems often rely on technology, such as barcodes, RFID, and digital recordkeeping systems.
New employees should familiarize themselves with these technologies and understand how they integrate into the traceability process.
Understanding how to use these technologies effectively will enhance their ability to maintain an accurate traceability system.
4. Training and Continuous Improvement
Training is crucial for all employees, but especially for those new to the field of quality assurance.
Participate in training programs that focus on ISO 13485, traceability, and quality management.
Additionally, new employees should be open to feedback and willing to contribute to continuous improvement efforts within the traceability system.
Quality systems should evolve with changes in technology and regulatory requirements.
Benefits of a Robust Traceability System
Building a strong traceability system offers several benefits, including:
– Improved product quality and safety,
– Enhanced ability to meet regulatory compliance,
– More efficient recall procedures,
– Better supply chain management,
– Increased customer trust and satisfaction.
A robust traceability system ensures that all products issued meet the company’s and ISO’s quality standards, ultimately safeguarding the health and safety of patients and end users.
Conclusion
For new employees in the medical device manufacturing industry, understanding and contributing to a traceability system aligned with ISO 13485 is vital.
This system ensures compliance with strict regulations, maintains high levels of product quality and safety, and supports overall business success.
As a new employee, grasping the intricacies of traceability not only enhances your ability to perform your role effectively but also contributes significantly to the broader objectives of maintaining excellence and upholding patient safety in the industry.
資料ダウンロード
QCD調達購買管理クラウド「newji」は、調達購買部門で必要なQCD管理全てを備えた、現場特化型兼クラウド型の今世紀最高の購買管理システムとなります。
ユーザー登録
調達購買業務の効率化だけでなく、システムを導入することで、コスト削減や製品・資材のステータス可視化のほか、属人化していた購買情報の共有化による内部不正防止や統制にも役立ちます。
NEWJI DX
製造業に特化したデジタルトランスフォーメーション(DX)の実現を目指す請負開発型のコンサルティングサービスです。AI、iPaaS、および先端の技術を駆使して、製造プロセスの効率化、業務効率化、チームワーク強化、コスト削減、品質向上を実現します。このサービスは、製造業の課題を深く理解し、それに対する最適なデジタルソリューションを提供することで、企業が持続的な成長とイノベーションを達成できるようサポートします。
オンライン講座
製造業、主に購買・調達部門にお勤めの方々に向けた情報を配信しております。
新任の方やベテランの方、管理職を対象とした幅広いコンテンツをご用意しております。
お問い合わせ
コストダウンが利益に直結する術だと理解していても、なかなか前に進めることができない状況。そんな時は、newjiのコストダウン自動化機能で大きく利益貢献しよう!
(Β版非公開)