- お役立ち記事
- A must-see for managers of research and development departments in the medical device manufacturing industry! Success stories of material characterization and product development
A must-see for managers of research and development departments in the medical device manufacturing industry! Success stories of material characterization and product development
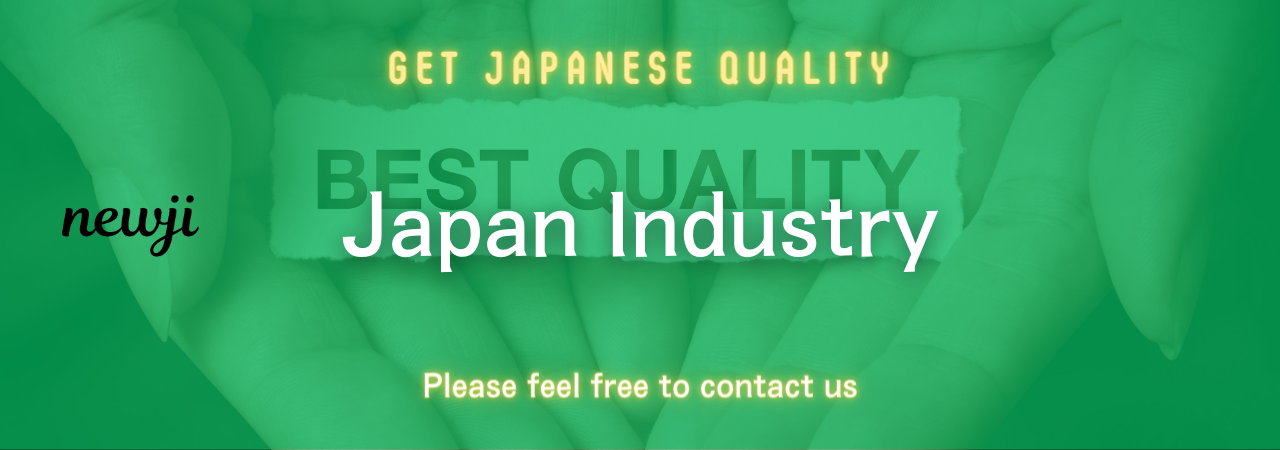
目次
Introduction to Material Characterization in Medical Device Manufacturing
In the fast-paced world of medical device manufacturing, innovation is key to staying competitive.
One of the critical aspects of innovation in this field is material characterization.
Material characterization involves understanding the properties and behaviors of materials used in medical devices.
This process is essential for ensuring the safety, reliability, and effectiveness of medical products.
For managers in research and development departments, mastering material characterization can lead to significant breakthroughs in product development.
The Importance of Material Characterization
Material characterization is the backbone of the medical device manufacturing industry.
It involves the analysis and assessment of materials’ physical, chemical, mechanical, and biological properties.
This knowledge allows manufacturers to select appropriate materials for specific applications, ensuring product performance and patient safety.
In the medical device sector, where products often enter direct contact with human bodies, choosing the right material is crucial.
Materials used must meet stringent regulatory standards and should perform consistently under various conditions.
Therefore, understanding material properties through characterization is not just beneficial but mandatory for compliance and success.
Techniques in Material Characterization
There are several advanced techniques used in material characterization.
Each technique offers insights into different aspects of the materials used in medical devices.
One common technique is spectroscopy, which includes methods such as infrared (IR) and nuclear magnetic resonance (NMR) spectroscopy.
These methods help determine the chemical structure and composition of materials.
Microscopy techniques, such as scanning electron microscopy (SEM) and transmission electron microscopy (TEM), provide a detailed look at a material’s surface topography and microstructure.
Mechanical testing, including tensile testing and hardness testing, assesses a material’s strength, flexibility, and durability.
Such evaluations are vital for devices that experience stress or load during their use.
Thermal analysis, including differential scanning calorimetry (DSC) and thermogravimetric analysis (TGA), investigates a material’s stability and behavior at different temperatures.
This is especially important for devices exposed to a range of temperatures during sterilization or usage.
Lastly, biocompatibility testing ensures that materials are safe for interaction with biological systems, which is crucial for implants and other in-body devices.
Success Stories in Product Development
Several success stories illustrate the role of material characterization in advancing the medical device manufacturing industry.
For instance, the development of biodegradable stents has been a game-changer in cardiovascular treatments.
By thoroughly characterizing biodegradable polymers, researchers were able to create stents that gradually dissolve within the body after serving their purpose, reducing the need for additional surgeries.
Effective material characterization ensured that these polymers were safe and reliable for clinical use.
In another instance, the advancement of orthopedic implants benefited significantly from material characterization.
Titanium and its alloys were extensively studied for their mechanical properties and biocompatibility.
This characterization led to the development of implants that were both strong and well-tolerated by patients’ bodies, reducing the risk of rejection or infection.
The development of smart medical devices, such as wearables that monitor patient vitals in real-time, also owes its success to material characterization.
Innovative materials have been identified that are flexible, conductive, and safe for prolonged skin contact, making these devices both practical and comfortable for users.
Challenges and Solutions
Despite its benefits, material characterization is not without challenges.
One significant challenge is the time and cost associated with the comprehensive analysis of new materials.
Additionally, keeping up with evolving technologies and regulatory standards demands continuous learning and adaptation.
However, solutions are emerging.
Utilizing computer simulations and digital twins can speed up the process, allowing for faster iteration and testing of material properties.
Collaborative efforts within the industry, including partnerships with academic institutions and material suppliers, can also enhance access to cutting-edge techniques and expertise.
These collaborations can help spread the costs and risks associated with material development and characterization.
The Role of R&D Managers
For managers in research and development departments, understanding and implementing material characterization strategies is crucial.
R&D managers should foster an environment that encourages innovation and experimentation with new materials.
Investing in training and resources to equip their teams with the latest technologies in material characterization is essential.
They should also stay informed about the latest developments in materials science and regulatory changes that impact material usage.
By prioritizing material characterization, R&D managers can lead their teams to develop safer, more effective, and innovative medical devices.
This proactive approach not only supports product development but also enhances the company’s reputation as an industry leader in innovation.
Conclusion
Material characterization is undeniably a cornerstone of successful product development in the medical device manufacturing industry.
From ensuring compliance to fostering innovation, the role of material characterization is multifaceted and indispensable.
By leveraging appropriate techniques and addressing challenges head-on, managers in R&D departments can drive significant advancements and success in their product lines.
Ultimately, the focus on material characterization will lead to safer, more effective medical devices that improve patient outcomes, securing a competitive edge in the market.
資料ダウンロード
QCD調達購買管理クラウド「newji」は、調達購買部門で必要なQCD管理全てを備えた、現場特化型兼クラウド型の今世紀最高の購買管理システムとなります。
ユーザー登録
調達購買業務の効率化だけでなく、システムを導入することで、コスト削減や製品・資材のステータス可視化のほか、属人化していた購買情報の共有化による内部不正防止や統制にも役立ちます。
NEWJI DX
製造業に特化したデジタルトランスフォーメーション(DX)の実現を目指す請負開発型のコンサルティングサービスです。AI、iPaaS、および先端の技術を駆使して、製造プロセスの効率化、業務効率化、チームワーク強化、コスト削減、品質向上を実現します。このサービスは、製造業の課題を深く理解し、それに対する最適なデジタルソリューションを提供することで、企業が持続的な成長とイノベーションを達成できるようサポートします。
オンライン講座
製造業、主に購買・調達部門にお勤めの方々に向けた情報を配信しております。
新任の方やベテランの方、管理職を対象とした幅広いコンテンツをご用意しております。
お問い合わせ
コストダウンが利益に直結する術だと理解していても、なかなか前に進めることができない状況。そんな時は、newjiのコストダウン自動化機能で大きく利益貢献しよう!
(Β版非公開)