- お役立ち記事
- Cutting and deburring of CFRP parts that new employees in the production technology department of the aircraft parts manufacturing industry should know.
Cutting and deburring of CFRP parts that new employees in the production technology department of the aircraft parts manufacturing industry should know.
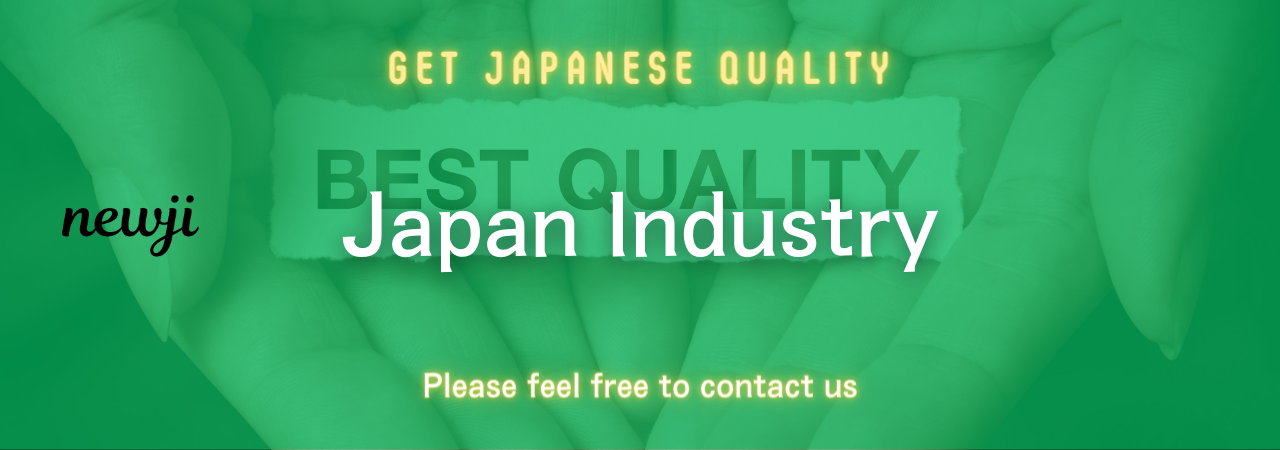
目次
Understanding CFRP and Its Use in the Aerospace Industry
CFRP, or Carbon Fiber Reinforced Polymer, is a composite material widely used in the aerospace industry.
Combining carbon fiber with a polymer matrix, CFRP offers high strength-to-weight ratios, which is crucial for aircraft parts where reducing weight while maintaining strength and durability is essential.
New employees in the production technology department need to understand that CFRP parts contribute significantly to fuel efficiency and overall performance of aircraft.
As a result, CFRP is a popular choice for constructing aircraft components such as wings, fuselages, and other critical structures.
The Importance of Cutting and Deburring CFRP Parts
When manufacturing CFRP parts, precise cutting and deburring are vital steps in the production process.
These processes ensure that the parts meet strict industry standards and performance criteria.
For new employees, it’s important to recognize that improper cutting can lead to defects or compromises in the structural integrity of the parts.
Deburring is equally important as it removes unwanted material residues and sharp edges that can affect the assembly of components.
Removing burrs also prevents potential injuries or damage and ensures that parts fit together seamlessly in the final product.
Techniques for Cutting CFRP Parts
Various techniques exist for cutting CFRP parts, each offering unique advantages and challenges.
Here are some common methods:
Water Jet Cutting
Water jet cutting involves using a high-pressure stream of water mixed with abrasive substances to slice through CFRP.
This method is known for its precision and ability to cut intricate shapes without causing thermal damage, a risk with other cutting techniques.
However, operators should be aware of potential delamination risks if the pressure settings are not correctly adjusted.
Laser Cutting
Laser cutting employs high-energy beams to cut materials, offering excellent precision and speed.
While suitable for thinner CFRP pieces, laser cutting may cause thermal damage or charred edges, compromising the quality of thicker components.
As new employees, understanding how to calibrate equipment and manage thermal impacts is essential for successful laser cutting applications.
Milling
CNC milling machines use rotating tools to remove material, providing accuracy and repeatability needed for complex part geometries.
Operators must consider tool wear and feed rates to avoid creating heat and vibrations that can damage the CFRP material.
Knowing how to optimize milling parameters is crucial for ensuring smooth and precise cuts.
Router Cutting
Router cutting is versatile and cost-effective, particularly useful for prototypes or small production runs.
It involves using a handheld or machine-driven router equipped with a specific cutting tool designed for CFRP.
New employees should familiarize themselves with the variety of router bits available and choose the right one based on the material thickness and design requirements.
Understanding Deburring Techniques for CFRP
Deburring is essential for producing smooth, safe, and functional aircraft components.
Different methods are available for deburring CFRP parts, and knowing which to use can greatly impact the success of the process.
Manual Deburring
Manual deburring uses hand tools to remove excess materials and smooth edges.
It’s a simple approach suitable for small or intricate components but can be labor-intensive and less precise than automated methods.
For manual deburring, it’s important for new employees to receive proper training to ensure consistency and quality.
Mechanical Deburring
Mechanical deburring uses specialized machinery to remove burrs rapidly and efficiently.
This method is well-suited for standardized parts produced in large quantities.
Operators must be aware of machine settings and tools used to prevent over-polishing or under-processing of CFRP surfaces.
Vibratory Deburring
Vibratory deburring involves placing parts into a vibrating container filled with abrasive media.
The vibrations cause the media to rub against the parts, effectively polishing and smoothing them.
This method is advantageous for handling large batches of parts and is less labor-intensive than other processes.
Understanding media selection and vibration settings is essential for achieving desired surface qualities.
Chemical Deburring
Chemical deburring uses specific solutions to dissolve burrs chemically.
While it offers precision and is gentle on the material, it’s more commonly used in small-scale operations as chemical handling can pose safety risks.
New employees should be trained on safety protocols and environmental considerations when employing chemical deburring.
Ensuring Safety and Precision in the Production Process
Success in cutting and deburring CFRP parts demands attention to safety and precision.
New employees should prioritize wearing appropriate personal protective equipment (PPE) during operations.
Also, maintaining the settings of cutting and deburring equipment and ensuring tools remain sharp and free of damage are indispensable.
Production environments should remain clean and organized, minimizing risks to workers and maximizing the reliability of final products.
Additionally, adhering to regular inspections and quality checks to detect deviations early ensures parts meet industry standards.
Conclusion
For new employees in the aircraft parts manufacturing industry, mastering the cutting and deburring of CFRP parts is paramount.
With a deep understanding of the various techniques, the benefits and limitations of each, and a commitment to quality and safety, they can significantly contribute to their team’s success.
As the aerospace industry continues to evolve, the importance of proficiency in handling CFRP components will only grow, paving the way for more efficient and innovative aircraft designs.
資料ダウンロード
QCD調達購買管理クラウド「newji」は、調達購買部門で必要なQCD管理全てを備えた、現場特化型兼クラウド型の今世紀最高の購買管理システムとなります。
ユーザー登録
調達購買業務の効率化だけでなく、システムを導入することで、コスト削減や製品・資材のステータス可視化のほか、属人化していた購買情報の共有化による内部不正防止や統制にも役立ちます。
NEWJI DX
製造業に特化したデジタルトランスフォーメーション(DX)の実現を目指す請負開発型のコンサルティングサービスです。AI、iPaaS、および先端の技術を駆使して、製造プロセスの効率化、業務効率化、チームワーク強化、コスト削減、品質向上を実現します。このサービスは、製造業の課題を深く理解し、それに対する最適なデジタルソリューションを提供することで、企業が持続的な成長とイノベーションを達成できるようサポートします。
オンライン講座
製造業、主に購買・調達部門にお勤めの方々に向けた情報を配信しております。
新任の方やベテランの方、管理職を対象とした幅広いコンテンツをご用意しております。
お問い合わせ
コストダウンが利益に直結する術だと理解していても、なかなか前に進めることができない状況。そんな時は、newjiのコストダウン自動化機能で大きく利益貢献しよう!
(Β版非公開)