- お役立ち記事
- For leaders of design departments in the chemical manufacturing industry! How to improve design accuracy with CAE and simulation technology
For leaders of design departments in the chemical manufacturing industry! How to improve design accuracy with CAE and simulation technology
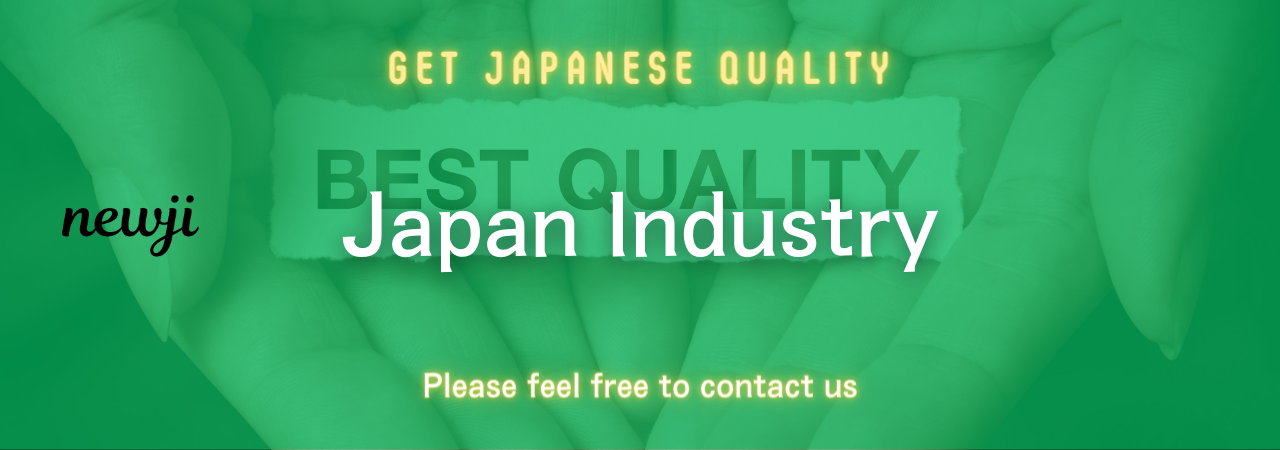
目次
Understanding CAE and Simulation Technology
In today’s fast-paced chemical manufacturing industry, the role of design departments is more crucial than ever.
With increasing demands for precision and efficiency, leaders in this field must leverage modern tools like Computer-Aided Engineering (CAE) and simulation technologies to enhance design accuracy.
But what exactly are CAE and simulation technologies, and how can they improve design processes?
CAE refers to the use of computer software to simulate the performance of a product under various conditions.
This technology allows engineers to analyze the effects of different physical forces, materials, and environments on their designs.
By incorporating CAE into the design process, designers can anticipate potential issues and make necessary adjustments before the actual production begins.
This not only saves time and resources but also enhances the overall quality and reliability of the final product.
Simulation technology, on the other hand, enables the virtual modeling and analysis of chemical processes and reactions.
It provides a realistic representation of how substances interact under various conditions.
This technology is particularly valuable in the chemical manufacturing industry, where understanding complex reactions and processes is crucial for ensuring safety and efficiency.
Benefits of Using CAE and Simulation in Chemical Design
Integrating CAE and simulation technology into the design processes of chemical manufacturing offers numerous advantages.
One of the primary benefits is improved accuracy and efficiency in design.
By simulating the impacts of different variables, teams can refine their designs to meet precise specifications before any physical prototypes are created.
This reduces the need for costly and time-consuming trial-and-error experimentation.
Moreover, CAE and simulation technologies help identify potential design flaws early in the process.
By doing so, design departments can avoid costly recalls and ensure products meet safety standards from the outset.
The ability to predict and rectify design issues before they occur is invaluable, especially in an industry where safety is paramount.
Additionally, utilizing these technologies can significantly reduce the time to market.
As simulations provide rapid feedback on design iterations, teams can make informed decisions quickly, streamlining the development process.
This agility not only cuts down the development timeline but also provides a competitive edge in a market where speed and innovation are key drivers of success.
Implementing CAE and Simulation Technology
To effectively implement CAE and simulation technology, design leaders in the chemical manufacturing industry must first invest in the right tools and software.
Choosing the appropriate software depends on the specific needs of your department and the type of products being developed.
Some popular software packages for CAE and simulation include ANSYS, COMSOL Multiphysics, and Autodesk Simulation.
Once the software is selected, it is crucial to ensure that your team is adequately trained to use these tools effectively.
This might involve organizing training sessions or workshops to help team members get acquainted with the technology.
Investing in skill development not only enhances the capability of the team but also maximizes the return on investment from the technology itself.
Furthermore, it’s important to foster a collaborative environment where team members feel encouraged to share insights and findings from simulation results.
Open communication and teamwork can lead to more innovative solutions and improved design outcomes.
Maintaining Accuracy and Reliability
While CAE and simulation technologies provide powerful tools for enhancing design accuracy, it’s important to maintain vigilance in ensuring that simulations remain reliable and accurate.
To do this, always validate simulation results with experimental or real-world data.
This triangulation can help verify the accuracy of the simulations and improve credibility in decision-making.
Additionally, continuously update simulation models based on the latest data and technological advancements.
Staying current with the latest developments ensures that your team’s simulations accurately reflect real-world conditions.
Overcoming Challenges in Chemical Design
Despite their benefits, implementing CAE and simulation technologies does come with challenges.
One of the major obstacles is the initial cost of acquiring the software and training staff.
However, when weighed against the potential savings from reduced prototypes and faster time-to-market, these investments often justify themselves over time.
Another challenge is ensuring the integration of these technologies within existing workflows.
Design leaders must carefully plan the implementation process to minimize disruptions.
This might involve phased rollouts or pilot programs to gradually incorporate these tools into everyday practices.
Furthermore, there may be resistance to change within teams accustomed to traditional methods.
To overcome this, it’s vital to demonstrate the tangible benefits and improvements achieved through CAE and simulation technology.
Sharing case studies and success stories can help build confidence and support from team members.
The Future of Design in Chemical Manufacturing
As technology continues to advance, the future of design in chemical manufacturing looks promising.
CAE and simulation technologies are becoming more sophisticated, offering even higher levels of precision and capability.
For design leaders, staying informed about emerging technological trends and advancements is imperative.
These advancements will likely expand the scope of what’s possible in chemical design, opening new opportunities for innovation and efficiency.
Design departments that embrace CAE and simulation technologies will be well-equipped to navigate the evolving landscape of chemical manufacturing, ensuring they remain at the forefront of the industry.
By leveraging these powerful tools, design leaders can not only improve design accuracy but also drive overall success and sustainability in their organizations.
With careful implementation and a commitment to continuous improvement, the potential for CAE and simulation technologies in the chemical manufacturing industry is vast and transformative.
資料ダウンロード
QCD調達購買管理クラウド「newji」は、調達購買部門で必要なQCD管理全てを備えた、現場特化型兼クラウド型の今世紀最高の購買管理システムとなります。
ユーザー登録
調達購買業務の効率化だけでなく、システムを導入することで、コスト削減や製品・資材のステータス可視化のほか、属人化していた購買情報の共有化による内部不正防止や統制にも役立ちます。
NEWJI DX
製造業に特化したデジタルトランスフォーメーション(DX)の実現を目指す請負開発型のコンサルティングサービスです。AI、iPaaS、および先端の技術を駆使して、製造プロセスの効率化、業務効率化、チームワーク強化、コスト削減、品質向上を実現します。このサービスは、製造業の課題を深く理解し、それに対する最適なデジタルソリューションを提供することで、企業が持続的な成長とイノベーションを達成できるようサポートします。
オンライン講座
製造業、主に購買・調達部門にお勤めの方々に向けた情報を配信しております。
新任の方やベテランの方、管理職を対象とした幅広いコンテンツをご用意しております。
お問い合わせ
コストダウンが利益に直結する術だと理解していても、なかなか前に進めることができない状況。そんな時は、newjiのコストダウン自動化機能で大きく利益貢献しよう!
(Β版非公開)