- お役立ち記事
- For production engineers in the chemical reaction tank stirring pin manufacturing industry! Design method that achieves both high efficiency and chemical resistance
For production engineers in the chemical reaction tank stirring pin manufacturing industry! Design method that achieves both high efficiency and chemical resistance
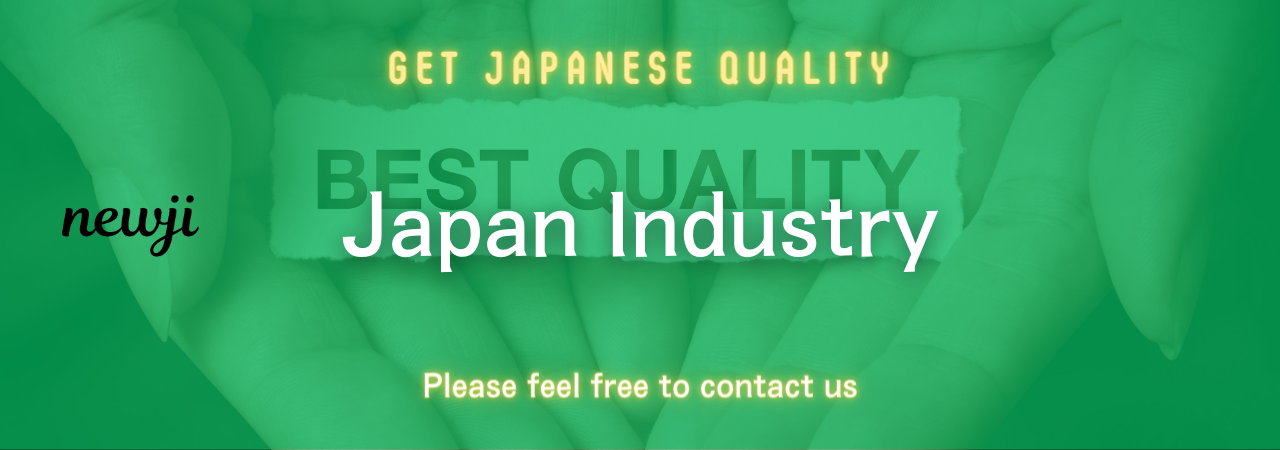
目次
Understanding the Basics of Stirring Pins for Chemical Reaction Tanks
In the chemical industry, production engineers play a crucial role in ensuring that chemical processes run smoothly and efficiently.
One essential component of this process is the stirring pin, used in chemical reaction tanks for mixing substances.
These pins not only need to be efficient in achieving the desired mix but must also resist the harsh chemicals they encounter.
To design stirring pins that excel in both efficiency and chemical resistance, engineers must take a comprehensive approach, factoring in materials, design structure, and operational conditions.
This article delves into these elements, offering insights and methods to help production engineers optimize their stirring pin designs.
Choosing the Right Materials
Selecting the appropriate material for stirring pins is critical to achieving chemical resistance.
The materials must withstand the corrosive nature of various chemicals without deteriorating, ensuring a long-lasting, safe, and hygienic operation.
Stainless Steel
Stainless steel is a popular choice due to its strength and exceptional resistance to corrosion and oxidation.
It’s ideal for tanks that process acids, alkalis, and other moderate to severely reactive chemicals.
Polymers and Plastics
For environments where metal contact might be unsuitable, certain advanced polymers offer excellent chemical resistance.
Materials like PTFE (Polytetrafluoroethylene) and PFA (Perfluoroalkoxy) are widely used because they resist degradation even with aggressive chemicals.
Coated Metals
In some cases, metals with specialized coatings may offer the best compromise between strength and resistance.
Coatings like epoxy or ceramic can enhance a metal’s durability and longevity in harsh environments.
Design Considerations for Efficiency
Efficiency in stirring pins can significantly impact the overall performance of chemical reactions, affecting reaction times, product yield, and energy consumption.
Aerodynamic and Hydrodynamic Shapes
The shape of the stirring pins influences the mixing process.
Streamlining the shape can reduce drag, thus improving the fluid movement within the tank.
Pin shapes should be carefully designed to facilitate optimal mixing and minimize resistance.
Length and Positioning
The length of the stirring pins must be tailored to the tank’s dimensions and the density of the chemicals.
Longer pins may be necessary for larger tanks to ensure effective mixing.
Accurate positioning within the tank is also crucial to ensure uniform mixing.
Speed of Rotation
The speed at which the pins rotate is a vital factor in mixing efficiency.
Production engineers must balance speed to optimize energy consumption and minimize wear on the pins, taking into account the viscosity of the chemicals.
Addressing Operational Conditions
It’s essential to consider the operational environment, as the conditions within chemical reaction tanks can vary widely.
Temperature and Pressure
Materials and designs must be resilient enough to withstand the fluctuating temperatures and pressures encountered in reactions.
This is especially true for exothermic or endothermic processes that may cause rapid changes in the tank’s environment.
pH Levels
Particular attention should be given to the pH levels of the chemicals involved.
Some materials may work well under neutral conditions but degrade rapidly under acidic or basic conditions.
Maintenance and Safety
Incorporating maintenance and safety into the design process extends the lifespan of stirring pins and ensures the safety of operations.
Ease of Maintenance
Designs should facilitate easy inspection, cleaning, and replacement of parts.
Detachable pins and smooth surfaces can simplify maintenance tasks, reducing downtime.
Safety Considerations
Ensuring that stirring pins do not contaminate the process or become a danger within the system is a priority.
Regular checks and material assessments help mitigate risks associated with component failure or contamination.
Innovations and Trends
Innovation continues to advance stirring pin technology, with new materials and designs constantly under development.
Smart Materials
Advances in material science, such as self-healing or nano-coated surfaces, offer promising developments for improving chemical resistance and durability.
3D Printing and Customization
3D printing technology allows for customized stirring pin designs tailored to specific processes.
This can lead to significant improvements in efficiency and cost-effectiveness.
Conclusion
Designing stirring pins for chemical reaction tanks requires a deep understanding of both chemical resistance and efficiency.
By choosing the right materials, optimizing design elements, considering operational conditions, and integrating maintenance and safety features, production engineers can significantly enhance their chemical mixing processes.
Staying abreast of technological advancements will further position engineers to implement state-of-the-art solutions, maintaining high operational standards and achieving exemplary outcomes in chemical production.
資料ダウンロード
QCD調達購買管理クラウド「newji」は、調達購買部門で必要なQCD管理全てを備えた、現場特化型兼クラウド型の今世紀最高の購買管理システムとなります。
ユーザー登録
調達購買業務の効率化だけでなく、システムを導入することで、コスト削減や製品・資材のステータス可視化のほか、属人化していた購買情報の共有化による内部不正防止や統制にも役立ちます。
NEWJI DX
製造業に特化したデジタルトランスフォーメーション(DX)の実現を目指す請負開発型のコンサルティングサービスです。AI、iPaaS、および先端の技術を駆使して、製造プロセスの効率化、業務効率化、チームワーク強化、コスト削減、品質向上を実現します。このサービスは、製造業の課題を深く理解し、それに対する最適なデジタルソリューションを提供することで、企業が持続的な成長とイノベーションを達成できるようサポートします。
オンライン講座
製造業、主に購買・調達部門にお勤めの方々に向けた情報を配信しております。
新任の方やベテランの方、管理職を対象とした幅広いコンテンツをご用意しております。
お問い合わせ
コストダウンが利益に直結する術だと理解していても、なかなか前に進めることができない状況。そんな時は、newjiのコストダウン自動化機能で大きく利益貢献しよう!
(Β版非公開)