- お役立ち記事
- Techniques for manufacturing thin-walled parts and suppressing cracks that design department leaders in the precision machinery industry should know.
Techniques for manufacturing thin-walled parts and suppressing cracks that design department leaders in the precision machinery industry should know.
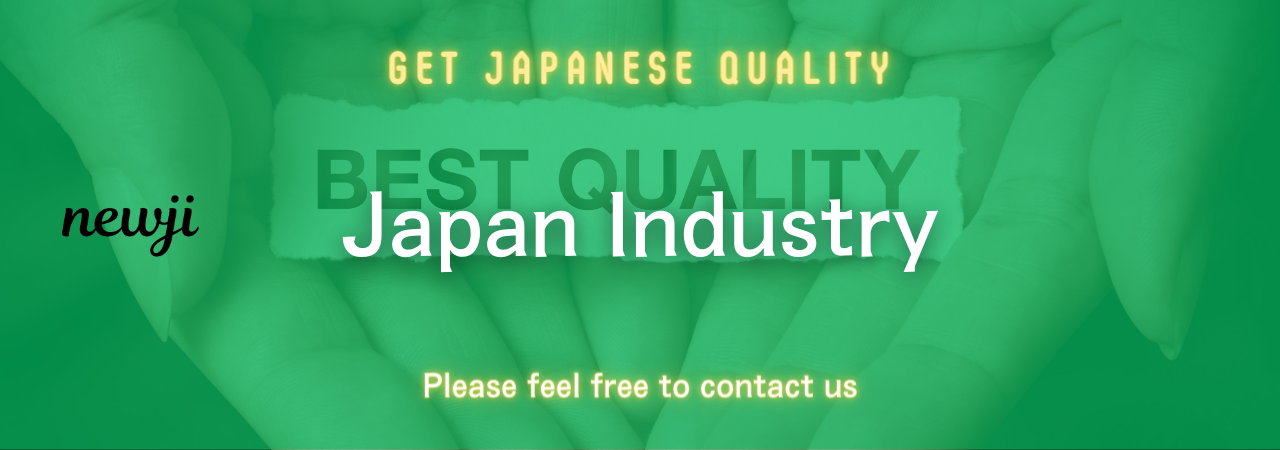
目次
Introduction to Thin-Walled Parts Manufacturing
In the world of precision machinery, the manufacturing of thin-walled parts is a highly sought-after skill.
These delicate components are integral in various applications, from aerospace to consumer electronics.
However, producing them without inducing cracks or defects requires refined techniques and understanding.
Design department leaders must be well-versed in these techniques to ensure high-quality outputs and optimize production efficiency.
Understanding Thin-Wall Manufacturing
Thin-walled parts refer to components with walls substantially thinner compared to their overall size.
The challenge lies in their delicate structure which is prone to warping, cracking, and deformation if not handled correctly.
Because of their lightweight nature, they are vital in industries where reducing weight is crucial, such as in aeronautics and automotive design.
Materials Selection
Choosing the right material is the cornerstone of manufacturing robust thin-walled parts.
Materials such as aluminum, titanium, and certain polymers are favored due to their lightweight yet strong properties.
Additionally, composite materials are gaining traction due to their customizability in terms of strength and weight distribution.
It’s essential for design leaders to collaborate with materials engineers to select the most appropriate material for the intended application’s requirements.
Design Considerations for Thin-Walled Parts
The design phase is critical in ensuring the manufacturability and durability of thin-walled parts.
Here are some design considerations that can help minimize defects:
Uniform Wall Thickness
Maintaining a consistent wall thickness can prevent stress concentrations, which are common sources of cracks.
Varying thicknesses can lead to differences in liquid cooling rates during casting, causing warping or stress.
Incorporate Support Structures
In processes like 3D printing, including support structures during design can help maintain the integrity of thin walls during the manufacturing process.
They can be easily removed post-production, ensuring the part retains its intended shape and properties.
Optimized Geometries
Geometries should be simplified where possible to avoid unnecessary complexities that could act as stress risers.
Fillets should replace sharp corners to distribute stress more evenly across the part.
Manufacturing Techniques for Thin-Walled Parts
To achieve success in manufacturing thin-walled parts, specific techniques must be adhered to, each providing unique advantages.
Casting
Casting is a cost-effective method but requires precision and control over factors like mold design and cooling rates.
Using advanced simulation tools can predict the outcomes of casting thin-walled parts, allowing engineers to remedy potential issues before actual production.
Injection Molding
This method is often used for polymers, providing high levels of accuracy and repeatability.
Key factors here are the temperature, pressure, and timing, which must be meticulously controlled to avoid defects.
3D Printing and Additive Manufacturing
These technologies have revolutionized the production of thin-walled parts by allowing complex geometries without additional cost.
Additive manufacturing offers significant flexibility in design and material usage but requires thorough understanding of layer adhesion methods.
Suppressing Cracks in Thin-Walled Parts
Avoiding cracks is paramount in thin-walled part production.
Here’s how design leaders can minimize this risk:
Implementing Stress Relief Protocols
After manufacturing, components may need thermal or mechanical stress-relief treatments to stabilize and prevent cracking.
Processes such as annealing help in reducing stresses that have built up during manufacturing.
Quality Control and Inspections
Regular quality checks and non-destructive testing methods should be integrated throughout the production process.
Techniques like X-ray or ultrasonic inspections can detect subsurface cracks that are not visible on the surface.
Simulation and Modeling
Prior to actual production, simulations offer insights into potential structural weaknesses.
By using software for finite element analysis, manufacturers can predict where stresses and cracks might occur, allowing for preemptive design modifications.
Conclusion
Manufacturing thin-walled parts demands a precise blend of material expertise, design acumen, and production excellence.
By employing thoughtful design strategies, leveraging advanced manufacturing technologies, and implementing rigorous quality control measures, design department leaders can significantly enhance the integrity and performance of thin-walled components.
The knowledge and application of these techniques not only lead to better products but also place companies ahead in the competitive market of precision machinery.
By continuously updating skills and embracing technological advancements, precision machinery experts can continue to meet and exceed the high demands of modern industries.
資料ダウンロード
QCD調達購買管理クラウド「newji」は、調達購買部門で必要なQCD管理全てを備えた、現場特化型兼クラウド型の今世紀最高の購買管理システムとなります。
ユーザー登録
調達購買業務の効率化だけでなく、システムを導入することで、コスト削減や製品・資材のステータス可視化のほか、属人化していた購買情報の共有化による内部不正防止や統制にも役立ちます。
NEWJI DX
製造業に特化したデジタルトランスフォーメーション(DX)の実現を目指す請負開発型のコンサルティングサービスです。AI、iPaaS、および先端の技術を駆使して、製造プロセスの効率化、業務効率化、チームワーク強化、コスト削減、品質向上を実現します。このサービスは、製造業の課題を深く理解し、それに対する最適なデジタルソリューションを提供することで、企業が持続的な成長とイノベーションを達成できるようサポートします。
オンライン講座
製造業、主に購買・調達部門にお勤めの方々に向けた情報を配信しております。
新任の方やベテランの方、管理職を対象とした幅広いコンテンツをご用意しております。
お問い合わせ
コストダウンが利益に直結する術だと理解していても、なかなか前に進めることができない状況。そんな時は、newjiのコストダウン自動化機能で大きく利益貢献しよう!
(Β版非公開)